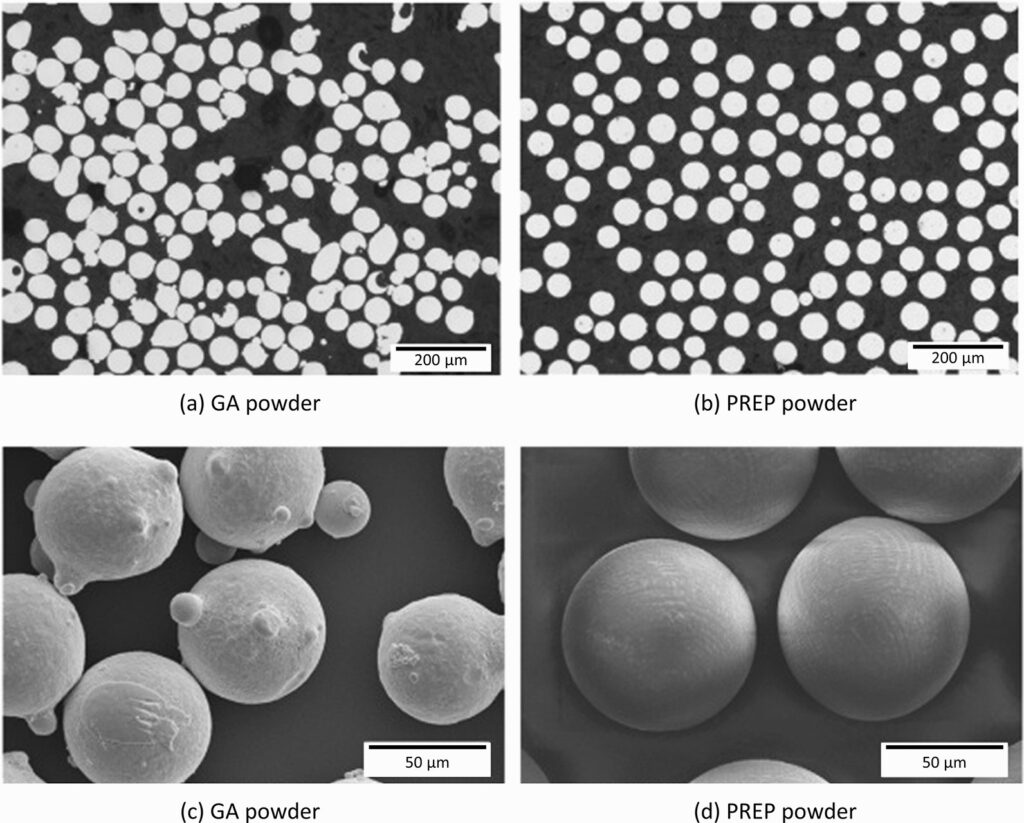
CM247LC Spherical Nickel-Based Alloy Powder: The Superior Material for High-Stress Applications
Low MOQ
Provide low minimum order quantity to meet different needs.
OEM & ODM
Provide customized products and design services to meet unique customer needs.
Adequate Stock
Ensure fast order processing and provide reliable and efficient service.
Customer Satisfaction
Provide high quality products with customer satisfaction at the core.
share this article
Table of Contents
When we talk about high-performance materials, especially those used in extreme environments, CM247LC Spherical Nickel-Based Alloy Powder stands out as a top contender. Whether you’re looking to create components for aerospace engines, turbines, or industrial gas turbines, this alloy offers an exceptional combination of strength, corrosion resistance, and high-temperature capability. But what makes this material so special, and why is it becoming a go-to option for industries that demand top-tier performance?
In this comprehensive guide, we’ll delve into the composition, properties, applications, and specifications of CM247LC Spherical Nickel-Based Alloy Powder. We’ll also cover its pricing, suppliers, and advantages and limitations. Finally, we’ll wrap it up with a FAQ section to address some common questions about this powerful material.
So, whether you’re a manufacturer, an engineer, or simply someone interested in innovative metallic materials, this guide will provide you with everything you need to know about CM247LC.
Overview of CM247LC Spherical Nickel-Based Alloy Powder
Let’s start with the basics. CM247LC is a nickel-based superalloy that is specially engineered to withstand extreme temperatures while maintaining excellent mechanical properties. Its ability to retain strength, creep resistance, and corrosion resistance at high temperatures makes it ideal for aerospace, power generation, and industrial applications.
The “LC” in CM247LC stands for “low carbon,” which means this alloy has reduced carbon content compared to other nickel alloys. This modification improves its weldability, ductility, and machinability—making it easier to work with while retaining its superior performance characteristics.
Composition and Key Properties of CM247LC Spherical Nickel-Based Alloy Powder
What exactly is in CM247LC that makes it so capable of withstanding extreme conditions? The magic lies in its complex composition of elements, each contributing to its unique properties.
Composition of CM247LC Spherical Nickel-Based Alloy Powder
Element | Percentage Composition |
---|---|
Nickel (Ni) | 60-65% |
Chromium (Cr) | 8.0-9.5% |
Cobalt (Co) | 9.0-10.5% |
Aluminum (Al) | 5.2-5.9% |
Titanium (Ti) | 0.5-1.0% |
Molybdenum (Mo) | 0.5-1.0% |
Tungsten (W) | 9.0-10.5% |
Tantalum (Ta) | 2.8-3.3% |
Carbon (C) | 0.07% max |
Boron (B) | 0.015-0.025% |
Zirconium (Zr) | 0.03-0.08% |
Key Properties of CM247LC Spherical Nickel-Based Alloy Powder
The specific combination of elements in CM247LC results in a material with outstanding mechanical and thermal properties. Let’s break down the key characteristics:
Property | Value |
---|---|
Melting Point | 1335°C – 1370°C |
Density | 8.89 g/cm³ |
Tensile Strength (at room temp.) | ~1,000 MPa |
Yield Strength (at room temp.) | ~800 MPa |
Creep Resistance | Exceptional at temperatures up to 980°C |
Thermal Conductivity | 12 W/m·K |
Oxidation Resistance | Excellent, especially in high-temperature environments |
Hardness | 35-40 HRC |
Why These Properties Matter
- High-Temperature Strength: CM247LC retains its mechanical strength at temperatures up to 1,000°C, making it ideal for aerospace components or gas turbines that operate in extreme heat.
- Creep Resistance: Over time, materials can deform under high stress and temperature. CM247LC excels in resisting this deformation, known as “creep.”
- Oxidation Resistance: The alloy’s ability to resist oxidation at high temperatures is crucial for applications like jet engine parts, where exposure to oxygen-rich environments could otherwise degrade the material.
- Density and Weight: While CM247LC is dense, its high strength-to-weight ratio makes it a preferred choice for applications demanding lightweight durability.
Applications of CM247LC Spherical Nickel-Based Alloy Powder
Where is CM247LC used, and why is it the material of choice for so many demanding applications? The answer lies in its versatility and ability to perform under extreme conditions.
Common Applications by Industry
Industry | Applications |
---|---|
Aerospace | Turbine blades, jet engine components, exhaust nozzles |
Power Generation | Gas turbine blades, vanes, and combustion chambers |
Automotive | High-performance exhaust systems, turbocharger components |
Industrial Gas Turbines | High-temperature components for energy generation |
Additive Manufacturing | Spherical powder for 3D printing of high-performance parts |
Oil and Gas | Downhole tools, drilling components exposed to high pressure and temperature |
Aerospace: High-Temperature Precision in Jet Engines
CM247LC is widely used in the aerospace industry, particularly in jet engine components. The high-temperature resistance and mechanical strength of this alloy make it ideal for turbine blades, which must endure both extreme heat and mechanical stress without deforming. These blades are critical components that directly affect the performance and efficiency of jet engines.
Power Generation: Reliable Performance in Gas Turbines
In the power generation sector, CM247LC is commonly used in gas turbines. These turbines operate at extreme temperatures, and the material’s creep resistance ensures that components like turbine blades and vanes maintain their integrity over extended periods of use. This results in more reliable energy production and longer-lasting components.
Additive Manufacturing: A New Frontier for CM247LC
With the rise of additive manufacturing (3D printing), CM247LC Spherical Nickel-Based Alloy Powder has found new applications. The spherical powder form of the material is ideal for laser powder bed fusion and other metal 3D printing techniques, allowing for the creation of complex geometries with high precision. This is particularly useful for industries like aerospace and automotive, where weight reduction and performance optimization are critical.
Specifications, Sizes, and Standards for CM247LC Spherical Nickel-Based Alloy Powder
When selecting CM247LC Spherical Nickel-Based Alloy Powder, it’s essential to consider the particle size, purity, and conformance to industry standards. These factors ensure that the powder meets the specific requirements of your application.
Specifications and Sizes for CM247LC Powder
Specification | Details |
---|---|
Particle Size | 15-45 µm, 45-75 µm, 75-150 µm |
Purity | ≥ 99.0% |
Sphericity | > 0.95 |
Flow Rate | 25 – 30 s/50g |
Bulk Density | 4.5 – 5.0 g/cm³ |
ISO Standards | ISO 15156 (H2S environments), ASTM B835 |
Why Particle Size and Purity Matter
- Particle Size: The particle size of the powder affects its flowability, packing density, and suitability for additive manufacturing or coating applications. Finer particles (15-45 µm) are typically used for 3D printing, while larger particles (75-150 µm) are better suited for powder metallurgy.
- Purity: High-purity powders (≥ 99.0%) ensure consistent performance and reliability, particularly in high-stress or high-temperature environments.
- Sphericity: A high degree of sphericity improves the flowability of the powder, making it easier to work with in metal additive manufacturing processes like laser powder bed fusion (LPBF).
Suppliers and Pricing for CM247LC Spherical Nickel-Based Alloy Powder
Finding the right supplier is critical when sourcing CM247LC Spherical Nickel-Based Alloy Powder. Factors like quality, purity, and pricing can vary significantly between suppliers. Below, we’ve outlined some of the key suppliers and their pricing details.
Suppliers and Pricing Information for CM247LC Powder
Supplier | Price Range (per kg) | Notes |
---|---|---|
Supplier A | $300 – $350 | Specializes in high-purity powder for additive manufacturing |
Supplier B | $320 – $370 | Offers a wide range of particle sizes and bulk pricing |
Supplier C | $310 – $360 | ISO-certified powder for aerospace applications |
Supplier D | $330 – $380 | Focuses on high-quality powders for 3D printing and metal injection molding |
Factors Affecting Pricing
- Particle Size: Finer powders, such as those used in additive manufacturing, generally cost more due to the additional processes required to achieve the desired particle size.
- Purity: Higher-purity powders are more expensive, as they have undergone more rigorous refinement processes to remove impurities that could negatively impact performance in critical applications.
- Bulk Orders: Many suppliers offer bulk discounts, which can significantly reduce the price per kilogram for large orders.
Advantages and Limitations of CM247LC Spherical Nickel-Based Alloy Powder
Like any material, CM247LC has its strengths and weaknesses. Understanding these can help you determine whether it’s the right material for your specific application.
Advantages of CM247LC Spherical Nickel-Based Alloy Powder
Advantage | Why It Matters |
---|---|
High-Temperature Strength | Retains mechanical strength at temperatures up to 1,000°C. |
Creep Resistance | Exceptional resistance to deformation over time under high stress and heat. |
Oxidation Resistance | Excellent performance in oxygen-rich, high-temperature environments. |
Spherical Shape | High sphericity improves flowability in additive manufacturing processes. |
Corrosion Resistance | Resists corrosion in harsh environments such as power generation and aerospace. |
Limitations of CM247LC Spherical Nickel-Based Alloy Powder
Limitation | Why It Matters |
---|---|
High Cost | More expensive than other alloys, especially in high-purity powder form. |
Machinability | Can be difficult to machine due to its hardness and strength. |
Limited Ductility | While strong at high temperatures, CM247LC has limited ductility compared to other nickel-based alloys. |
Frequently Asked Questions (FAQs) About CM247LC Spherical Nickel-Based Alloy Powder
To clear up any lingering questions, we’ve compiled some of the most frequently asked questions about CM247LC Spherical Nickel-Based Alloy Powder.
Question | Answer |
---|---|
What is CM247LC Spherical Nickel-Based Alloy Powder used for? | It is commonly used in aerospace, power generation, and industrial gas turbines where high-temperature resistance is critical. |
Why is CM247LC special? | Its unique composition allows it to maintain mechanical strength at extreme temperatures, making it ideal for turbine blades and jet engine components. |
Is CM247LC hard to machine? | Yes, due to its hardness and strength, CM247LC can be challenging to machine, but its performance in high-temperature environments makes it worth the effort. |
How much does CM247LC powder cost? | Prices typically range from $300 to $380 per kg, depending on factors like particle size and purity. |
Can CM247LC be used in 3D printing? | Absolutely! CM247LC Spherical Nickel-Based Alloy Powder is ideal for additive manufacturing due to its high sphericity and flowability. |
What industries benefit most from CM247LC powder? | Industries like aerospace, power generation, and automotive benefit from its high-temperature strength, creep resistance, and oxidation resistance. |
Conclusion
To sum it all up, CM247LC Spherical Nickel-Based Alloy Powder is a high-performance material that excels in extreme environments. Its unique combination of nickel, chromium, cobalt, and other elements gives it superior strength, creep resistance, and oxidation resistance, making it the go-to material for industries like aerospace, power generation, and automotive.
While CM247LC comes with a higher price tag and some challenges in machinability, its benefits far outweigh these limitations for applications that demand top-tier performance. Whether you’re manufacturing turbine blades, 3D printing high-strength parts, or looking for a material that can stand up to extreme temperatures, CM247LC delivers on all fronts.
Is CM247LC Spherical Nickel-Based Alloy Powder the right material for your next project? If temperature resistance, creep strength, and mechanical durability are your top priorities, then the answer is a resounding yes!
Get Latest Price
About Met3DP
Product Category
HOT SALE
CONTACT US
Any questions? Send us message now! We’ll serve your request with a whole team after receiving your message.
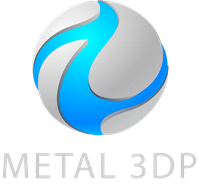
Metal Powders for 3D Printing and Additive Manufacturing