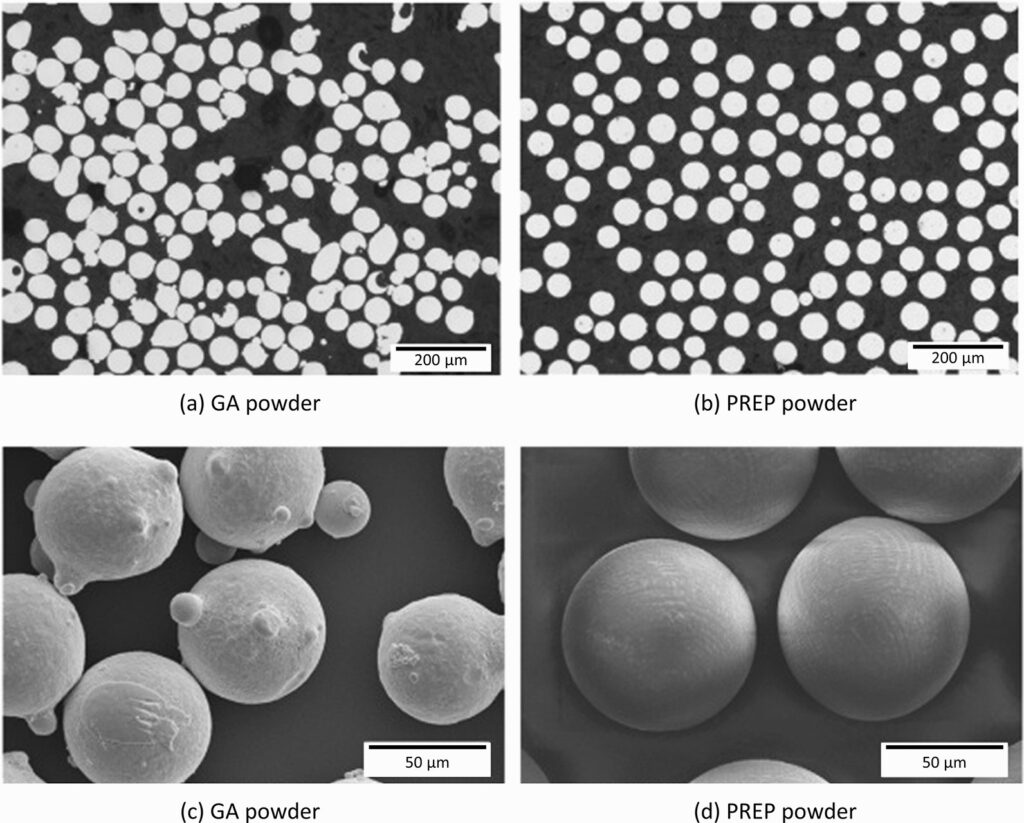
CoCrW Powder: Unlocking the Strength and Versatility of Cobalt-Chromium-Tungsten Alloy
Low MOQ
Provide low minimum order quantity to meet different needs.
OEM & ODM
Provide customized products and design services to meet unique customer needs.
Adequate Stock
Ensure fast order processing and provide reliable and efficient service.
Customer Satisfaction
Provide high quality products with customer satisfaction at the core.
share this article
Table of Contents
When it comes to materials that can withstand extreme conditions, CoCrW powder is in a league of its own. This alloy powder, made up of cobalt (Co), chromium (Cr), and tungsten (W), is known for its superior wear resistance, corrosion resistance, and high-temperature stability. These unique properties make CoCrW powder indispensable in industries like aerospace, automotive, medical, and industrial tooling. Whether you’re developing cutting-edge technology or working on advanced manufacturing projects, CoCrW powder might just be the solution you’ve been looking for.
In this guide, we’ll dive deep into the composition, properties, applications, and pricing of CoCrW powder. We’ll also explore its advantages and limitations, giving you a comprehensive understanding of why this material is so valuable in various sectors. Ready to find out more? Let’s get started!
What is CoCrW Powder?
CoCrW powder is a high-performance alloy primarily composed of cobalt, chromium, and tungsten. The unique combination of these elements provides exceptional mechanical and chemical properties, making it ideal for applications where strength, wear resistance, and heat resistance are crucial.
In simpler terms, CoCrW powder is like the superhero of metal alloys. Cobalt gives it toughness and the ability to retain its strength at high temperatures. Chromium adds excellent corrosion resistance, while tungsten takes the wear resistance to the next level, making this alloy perfect for machinery, cutting tools, and even medical implants.
Composition and Properties
Understanding the composition is key to appreciating its unique properties. Each element in the alloy plays a significant role in determining its overall performance.
Composition and Key Properties
Element | Percentage (%) | Role in the Alloy |
---|---|---|
Cobalt (Co) | 50-70% | Provides the base, contributing to high-temperature strength, toughness, and thermal stability. |
Chromium (Cr) | 20-30% | Enhances corrosion resistance and oxidation resistance, particularly in harsh environments like marine, chemical, or high-temperature settings. |
Tungsten (W) | 5-12% | Increases hardness, wear resistance, and the ability to withstand high temperatures, making it ideal for cutting tools and mechanical components. |
Carbon (C) | ≤ 1% | Improves hardness by forming carbides that enhance wear resistance. |
Nickel (Ni) | ≤ 1% | Sometimes added to improve toughness and corrosion resistance, depending on the application. |
Mechanical and Physical Properties
Property | Description |
---|---|
Density | 8.3–9.1 g/cm³ |
Melting Point | 1,300-1,450°C |
Tensile Strength | 900-1,400 MPa (depends on heat treatment and specific formulation) |
Hardness | 40-60 HRC (Rockwell Hardness) depending on tungsten content and heat treatment. |
Elastic Modulus | 200-220 GPa |
Corrosion Resistance | Excellent, especially in saline, acidic, and high-temperature environments. |
Wear Resistance | Superior wear resistance, making it ideal for components that experience constant mechanical stress. |
Thermal Stability | Maintains strength and wear resistance even at elevated temperatures, ideal for high-heat applications. |
Biocompatibility | Safe for use in medical implants and prosthetics. |
Why CoCrW Powder? The Key Characteristics
Let’s break down why it is such a sought-after material and what makes it stand out compared to other alloys like stainless steel or titanium.
1. Unmatched Wear Resistance with Tungsten
Tungsten is one of the hardest elements available, and its presence in CoCrW powder significantly enhances the material’s ability to resist wear and abrasion. This characteristic is particularly important for cutting tools, machinery, and turbine blades—all of which experience high levels of friction during use.
2. Incredible High-Temperature Strength
Many alloys lose their mechanical strength when exposed to high temperatures, but not CoCrW. Thanks to the cobalt base and the addition of tungsten, this alloy retains its hardness and durability even when subjected to extreme heat. This makes it a perfect fit for jet engines, exhaust systems, and other high-heat environments.
3. Exceptional Corrosion Resistance
Thanks to chromium, CoCrW powder is highly resistant to corrosion, particularly in saline or acidic environments. This makes it ideal for marine applications, chemical processing, and even medical implants, where exposure to bodily fluids makes corrosion resistance essential.
4. Biocompatibility for Medical Use
CoCrW powder is also biocompatible, meaning it can be safely used inside the human body. This is why it’s frequently used for orthopedic implants, dental prosthetics, and surgical tools. The combination of strength, corrosion resistance, and biocompatibility makes CoCrW powder a top choice for medical device manufacturers.
Applications
The versatility of CoCrW powder means it’s used in a wide range of industries. Below are some of the most common applications where this alloy truly shines.
Industry | Application |
---|---|
Aerospace | Turbine blades, jet engine components, exhaust systems, high-temperature structural parts. |
Medical | Orthopedic implants (hip and knee replacements), dental prosthetics, surgical tools. |
Automotive | High-performance engine components, exhaust valves, and parts exposed to high wear and heat. |
Industrial Tooling | Cutting tools, dies, and wear-resistant equipment used in manufacturing. |
Marine | Propellers, pumps, and other components exposed to saltwater and corrosive environments. |
Chemical Processing | Valves, pumps, and components exposed to corrosive chemicals and high temperatures. |
As you can see, CoCrW powder’s ability to withstand extreme wear, corrosion, and heat makes it a go-to material for industries that demand high performance and longevity.
Specifications, Sizes, Grades, and Standards
When working with CoCrW powder, it’s important to understand the different specifications, sizes, and grades available, depending on the application.
Specification | Details |
---|---|
Particle Size | Typically ranges from 15 to 45 microns for additive manufacturing and powder metallurgy. |
ASTM Standards | ASTM F75 (for medical implants), ASTM F1537 (for surgical applications). |
ISO Standards | ISO 5832-12 (for medical-grade CoCrW alloys), ISO 22674 (for dental applications). |
UNS Number | UNS R31539 (Unified Numbering System standard for CoCrW alloys). |
Grain Size | Powder grain size can be fine-tuned for specific manufacturing processes, such as 3D printing or sintering. |
These specifications ensure that CoCrW powder meets the high standards required for industries like medical devices, aerospace, and automotive.
Suppliers and Pricing
Pricing for CoCrW powder can vary depending on the supplier, purity, and particle size. Below is a table outlining some common suppliers and their typical pricing.
Supplier | Price Range (per kg) | Notes |
---|---|---|
Sandvik | $200 – $300 | High-quality CoCrW powder for medical and aerospace applications. |
Carpenter Technology | $250 – $350 | Specializes in premium-grade CoCrW powder for industrial, automotive, and medical use. |
ATI Metals | $220 – $330 | Known for high-performance alloys used in aerospace and automotive sectors. |
Oerlikon Metco | $210 – $320 | Offers a wide range of metal powders, including CoCrW tailored for additive manufacturing and sintering. |
Arcam/GE Additive | $230 – $340 | Specializes in metal powders for 3D printing, including CoCrW powder. |
Pricing may fluctuate based on order size, specific grade, and market conditions. Custom formulations or specialty powders may come with a higher price tag.
Advantages and Limitations
Like any material, CoCrW powder has its advantages and limitations. Let’s explore both sides to provide a balanced view of this material.
Advantages
Advantage | Why It Matters |
---|---|
Exceptional Wear Resistance: Thanks to tungsten, CoCrW powder offers superior wear resistance. | Ideal for components exposed to mechanical friction, such as cutting tools and turbine blades. |
High-Temperature Strength: Retains strength and hardness even at elevated temperatures. | Perfect for aerospace and automotive applications where high temperatures are common. |
Biocompatibility: Safe for use inside the human body. | Frequently used in medical implants, such as hip and knee replacements. |
Corrosion Resistance: Strong resistance to corrosive environments, including saltwater and acids. | Suitable for marine and chemical processing applications. |
Versatility in Additive Manufacturing: Well-suited for 3D printing and powder metallurgy. | Allows for the creation of complex, high-performance parts with precision. |
Limitations
Limitation | Why It’s a Challenge |
---|---|
High Cost: CoCrW powder is more expensive than other alloys like stainless steel or titanium. | May not be cost-effective for less demanding applications. |
Machinability: CoCrW can be difficult to machine, requiring specialized tools and techniques. | Increased difficulty in manufacturing may raise production costs. |
Heavier Than Alternatives: CoCrW can be heavier than lighter alloys like titanium. | Weight may be a limiting factor in aerospace or automotive applications where lighter materials are preferred. |
FAQs
Question | Answer |
---|---|
What is CoCrW powder used for? | CoCrW powder is used in aerospace, medical, automotive, and industrial tooling applications due to its wear resistance, corrosion resistance, and strength. |
How much does CoCrW powder cost? | Prices typically range from $200 to $350 per kilogram, depending on the supplier and specific application. |
Is CoCrW powder biocompatible? | Yes, CoCrW powder is highly biocompatible and is commonly used in medical implants such as hip and knee replacements. |
What are the primary elements in CoCrW powder? | The primary elements are cobalt, chromium, and tungsten, with small amounts of carbon and nickel. |
Can CoCrW powder be 3D printed? | Yes, CoCrW powder is frequently used in additive manufacturing, especially 3D printing for aerospace and medical applications. |
What industries use CoCrW powder? | CoCrW powder is used in industries such as aerospace, medical, automotive, industrial tooling, marine, and chemical processing. |
Is CoCrW powder magnetic? | CoCrW powder is typically non-magnetic, making it suitable for use in sensitive equipment like medical devices and aerospace components. |
Conclusion
In conclusion, it is a high-performance alloy that offers a unique combination of wear resistance, high-temperature strength, and corrosion resistance. Whether you’re designing medical implants, developing automotive components, or creating industrial tooling, the properties make it an ideal choice for demanding applications.
While the cost may be higher than some alternatives, the benefits of using CoCrW powder far outweigh the limitations in environments where strength, durability, and precision are critical factors. As additive manufacturing continues to grow, the demand for versatile materials like CoCrW powder will only increase.
Get Latest Price
About Met3DP
Product Category
HOT SALE
CONTACT US
Any questions? Send us message now! We’ll serve your request with a whole team after receiving your message.
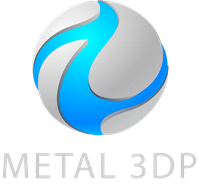
Metal Powders for 3D Printing and Additive Manufacturing