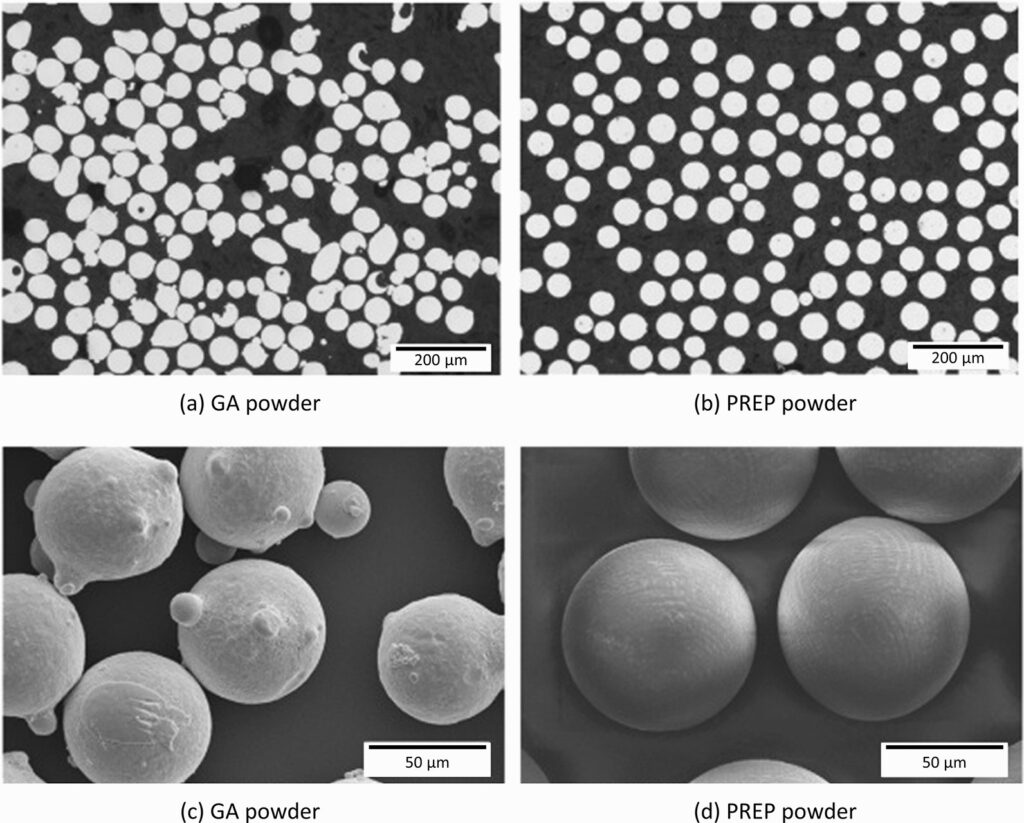
CuNi2SiCr Spherical Copper Alloy Powder: The Perfect Alloy for Maximum Durability and Conductivity
Low MOQ
Provide low minimum order quantity to meet different needs.
OEM & ODM
Provide customized products and design services to meet unique customer needs.
Adequate Stock
Ensure fast order processing and provide reliable and efficient service.
Customer Satisfaction
Provide high quality products with customer satisfaction at the core.
share this article
Table of Contents
When it comes to materials that offer a unique balance of strength, corrosion resistance, and electrical conductivity, CuNi2SiCr spherical copper alloy powder stands out as one of the most versatile and highly sought-after alloys in modern manufacturing. This exceptional alloy, composed primarily of copper, nickel, silicon, and chromium, finds its way into applications that demand both high performance and durability in extreme conditions. Whether you’re involved in aerospace, automotive, electronics, or additive manufacturing, CuNi2SiCr can offer you the best of both worlds.
In this comprehensive guide, we’ll explore everything you need to know about CuNi2SiCr spherical copper alloy powder. From its properties and applications to pricing and suppliers, this article will help you understand why this material is a popular choice and how it could be the optimal solution for your next high-tech project.
Overview of CuNi2SiCr Spherical Copper Alloy Powder
So, what exactly is CuNi2SiCr spherical copper alloy powder? The name tells you most of what you need to know about the alloy’s composition: it contains copper (Cu), nickel (Ni), silicon (Si), and chromium (Cr). However, the spherical shape of the powder particles is a key factor in its flowability, packing density, and uniformity, making it perfect for powder metallurgy and additive manufacturing processes.
The addition of nickel improves the material’s strength and corrosion resistance, while silicon enhances its hardness and thermal stability. Chromium, meanwhile, boosts wear resistance and prevents oxidation, making the alloy ideal for environments where extreme durability is a must.
Key Benefits of CuNi2SiCr Spherical Copper Alloy Powder:
- Excellent Electrical Conductivity: The copper base ensures good electrical performance.
- High Strength and Ductility: The alloy retains ductility while offering improved strength, thanks to nickel and silicon.
- Corrosion and Wear Resistance: Chromium helps resist oxidation and wear, even in harsh environments.
- Thermal Stability: The addition of silicon ensures the alloy performs well in high-temperature applications.
- Ideal for Additive Manufacturing: The spherical powder shape enhances flowability and precision in 3D printing processes.
Composition, Properties, and Characteristics of CuNi2SiCr Spherical Copper Alloy Powder
The unique combination of copper, nickel, silicon, and chromium in CuNi2SiCr spherical copper alloy powder results in a material that balances strength, ductility, resistance, and conductivity. Below is a detailed table outlining the composition, properties, and characteristics of this alloy.
Composition and Properties of CuNi2SiCr Spherical Copper Alloy Powder
Parameter | Details |
---|---|
Composition | Copper (Cu): ~97%, Nickel (Ni): 2%, Silicon (Si): 0.6% – 1%, Chromium (Cr): 0.15% – 0.4% |
Density | 8.8 g/cm³ |
Tensile Strength | 450 – 600 MPa |
Electrical Conductivity | 40% – 60% IACS (International Annealed Copper Standard) |
Thermal Conductivity | 300 – 360 W/m·K |
Hardness | 150 – 190 HV (Vickers Hardness) |
Melting Point | 1,070°C to 1,080°C |
Corrosion Resistance | High, due to chromium content |
Wear Resistance | Excellent, suitable for high-stress applications |
Why CuNi2SiCr is a Standout Material
The synergy between nickel, silicon, and chromium significantly enhances the properties that pure copper lacks. Nickel boosts strength and corrosion resistance, while silicon and chromium improve hardness and thermal stability. This combination makes CuNi2SiCr a one-stop solution for applications that require durability, strength, and conductivity under challenging conditions.
Applications of CuNi2SiCr Spherical Copper Alloy Powder
Given its remarkable properties, CuNi2SiCr spherical copper alloy powder is widely used in industries that require high strength, wear resistance, and electrical conductivity. Whether you’re working in aerospace, automotive, electronics, or power generation, this alloy is likely to meet your needs.
Common Applications of CuNi2SiCr Spherical Copper Alloy Powder
Industry | Applications |
---|---|
Aerospace | Electrical connectors, heat sinks, and high-stress components |
Automotive | Engine components, electrical systems, and high-performance pistons |
Electronics | Relays, switches, and connectors requiring both conductivity and strength |
Additive Manufacturing | 3D-printed parts, heat exchangers, and tooling |
Power Generation | Generator components, transformers, and thermal management systems |
Marine | Corrosion-resistant components, shipboard electrical systems |
Why CuNi2SiCr is Ideal for Additive Manufacturing
The spherical shape of the powder particles makes CuNi2SiCr perfect for additive manufacturing processes like 3D printing. The powder’s high flowability ensures that each layer in the printing process is consistent, resulting in higher-quality parts with superior mechanical properties.
Specifications, Sizes, and Standards for CuNi2SiCr Spherical Copper Alloy Powder
When choosing CuNi2SiCr spherical copper alloy powder, it’s important to select the right particle size and grade to match your specific application. Additionally, ensuring that the powder complies with industry standards is crucial, especially in regulated fields like aerospace and automotive manufacturing.
Specifications and Standards for CuNi2SiCr Spherical Copper Alloy Powder
Specification | Details |
---|---|
Particle Size Range | Typically between 15-45 μm for additive manufacturing, 25-75 μm for powder metallurgy |
Purity | 99.5% or higher for most industrial applications |
Density (bulk) | 8.8 g/cm³ |
Standards | Meets ASTM B422 for copper-nickel-silicon alloys, ISO 9001 for quality management |
Packaging Options | Available in 1kg, 5kg, 10kg, and 25kg containers, with bulk orders available |
Why Adhering to Standards is Crucial
Meeting ASTM and ISO standards ensures that the CuNi2SiCr alloy powder you purchase will perform consistently and meet the necessary physical and mechanical properties. These standards are especially important in industries like aerospace, where even small variations can have significant consequences.
Suppliers and Pricing Details for CuNi2SiCr Spherical Copper Alloy Powder
The price of CuNi2SiCr spherical copper alloy powder can vary depending on factors such as particle size, purity, and the supplier’s reputation. Below, we’ve compiled a list of some of the leading suppliers, along with their pricing for different variants of CuNi2SiCr powder.
Leading Suppliers and Pricing for CuNi2SiCr Spherical Copper Alloy Powder
Supplier | Product Description | Price (USD) | Comments |
---|---|---|---|
Höganäs AB | CuNi2SiCr, 15-45 μm, spherical powder | $180 – $300 per kg | High-purity powder for additive manufacturing. |
GKN Additive | CuNi2SiCr, 25-75 μm, spherical powder | $200 – $350 per kg | Aerospace-grade powder with excellent flowability. |
Valimet | CuNi2SiCr, 20-50 μm, spherical powder | $210 – $320 per kg | Ideal for powder metallurgy and metal injection molding. |
Advanced Powder Tech | CuNi2SiCr, 15-45 μm, spherical powder | $190 – $330 per kg | Premium powder for 3D printing and thermal applications. |
Factors Influencing CuNi2SiCr Powder Pricing
Several factors contribute to the variability in CuNi2SiCr spherical copper alloy powder pricing:
- Particle Size: Finer powders tend to be more expensive due to stricter production tolerances.
- Supplier Reputation: Established suppliers such as Höganäs AB and GKN Additive charge more for their high-quality, consistent products.
- Purity: Higher-purity powders are typically more expensive, especially for high-tech industries like aerospace and electronics.
Advantages and Limitations of CuNi2SiCr Spherical Copper Alloy Powder
While CuNi2SiCr spherical copper alloy powder offers numerous advantages, it’s important to understand both its strengths and limitations. Below, we’ll compare the pros and cons of this material to help you determine whether it’s the right choice for your project.
Advantages of CuNi2SiCr Spherical Copper Alloy Powder
Advantages | Details |
---|---|
High Strength and Ductility | Nickel and silicon enhance both the strength and ductility of the alloy, making it suitable for high-stress applications. |
Corrosion Resistance | Chromium provides excellent resistance to corrosion, especially in marine and industrial environments. |
Wear Resistance | The alloy is highly resistant to wear, thanks to the addition of chromium and silicon. |
Thermal Stability | Silicon ensures that the alloy retains its structural integrity at high temperatures. |
Electrical Conductivity | While slightly lower than pure copper, CuNi2SiCr still offers good electrical conductivity for use in electronic components. |
Limitations of CuNi2SiCr Spherical Copper Alloy Powder
Limitations | Details |
---|---|
Higher Cost | Compared to pure copper or other copper alloys, CuNi2SiCr is more expensive due to its added elements and the complexity of production. |
Lower Electrical Conductivity | The addition of nickel and silicon reduces the conductivity compared to pure copper, which may not be ideal for ultra-sensitive electronic applications. |
Complex Machinability | While machinable, CuNi2SiCr can be more difficult to process than softer copper alloys, requiring specialized tools and techniques. |
Is CuNi2SiCr Worth the Investment?
If you need a material that combines strength, corrosion resistance, and thermal stability with decent electrical conductivity, then CuNi2SiCr spherical copper alloy powder is absolutely worth the investment. However, if cost or maximizing conductivity is your primary concern, you might consider other alloys, such as pure copper or cheaper copper-nickel alloys.
FAQs About CuNi2SiCr Spherical Copper Alloy Powder
Question | Answer |
---|---|
What industries benefit most from CuNi2SiCr alloy powder? | Industries like aerospace, automotive, electronics, and marine benefit the most from its strength, corrosion resistance, and conductivity. |
How does CuNi2SiCr compare to pure copper powder? | CuNi2SiCr offers greater strength, wear resistance, and corrosion resistance but has slightly lower electrical conductivity compared to pure copper. |
What is the typical particle size for CuNi2SiCr powder in additive manufacturing? | The typical particle size for additive manufacturing is 15-45 μm, providing excellent flowability and precision. |
Can CuNi2SiCr alloy be used in high-temperature environments? | Yes, the alloy performs well in high-temperature environments, thanks to the addition of silicon, which enhances thermal stability. |
Is CuNi2SiCr powder suitable for 3D printing? | Absolutely! The spherical shape and good flowability make it ideal for 3D printing and other forms of additive manufacturing. |
Conclusion: Why CuNi2SiCr Spherical Copper Alloy Powder is a Must-Have for High-Performance Applications
In conclusion, CuNi2SiCr spherical copper alloy powder is the perfect solution for industries that demand a combination of strength, conductivity, and corrosion resistance. This alloy is designed to excel in challenging environments, making it a top choice for applications in aerospace, automotive, electronics, and marine industries.
While cost may be a consideration, the long-term benefits of using CuNi2SiCr—such as increased durability, wear resistance, and thermal stability—often outweigh the initial investment. Whether you’re manufacturing heat exchangers, electrical connectors, or 3D-printed parts, this alloy offers the versatility and performance needed for critical applications.
So, if you’re looking to take your manufacturing process to the next level, consider the advantages of CuNi2SiCr spherical copper alloy powder. With its superior properties, you’ll be investing in a material that is built to last and engineered for excellence.
Get Latest Price
About Met3DP
Product Category
HOT SALE
CONTACT US
Any questions? Send us message now! We’ll serve your request with a whole team after receiving your message.
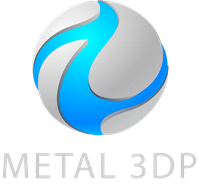
Metal Powders for 3D Printing and Additive Manufacturing