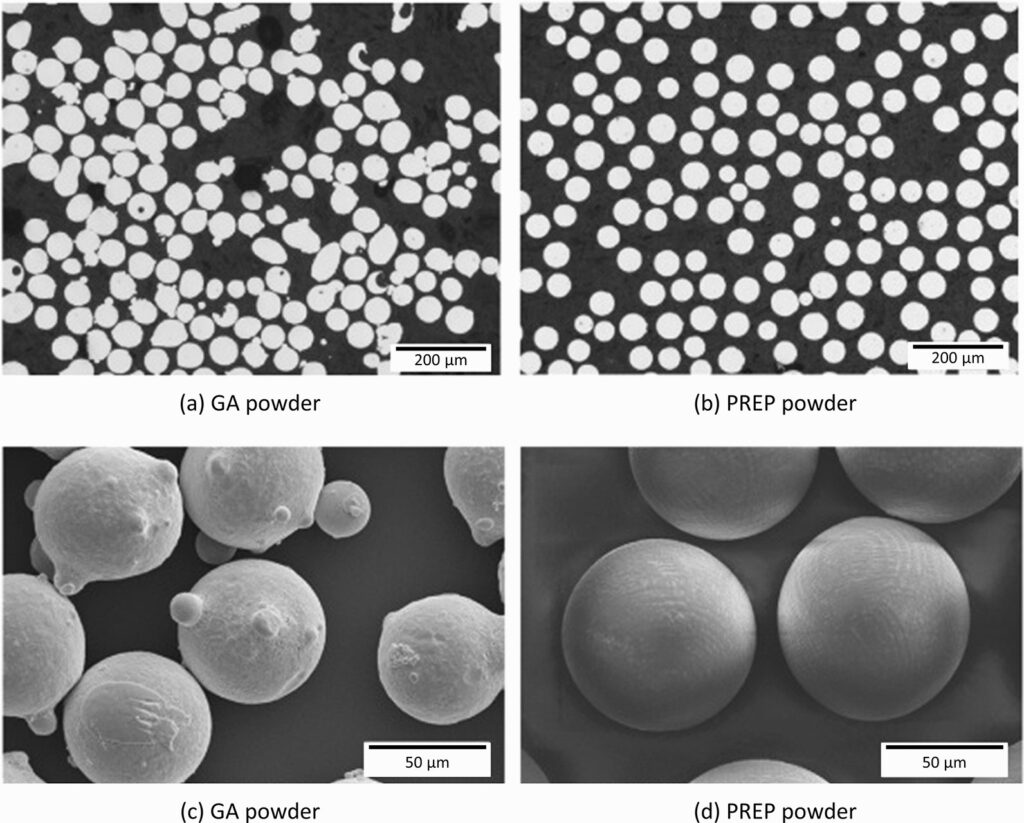
CuNi36In5 Spherical Copper-Based Spray Powder: The Perfect Choice for Longevity and Performance
Low MOQ
Provide low minimum order quantity to meet different needs.
OEM & ODM
Provide customized products and design services to meet unique customer needs.
Adequate Stock
Ensure fast order processing and provide reliable and efficient service.
Customer Satisfaction
Provide high quality products with customer satisfaction at the core.
share this article
Table of Contents
When it comes to advanced materials for surface coating, CuNi36In5 Spherical Copper-Based Spray Powder stands out as a versatile and high-performance choice. Whether you’re involved in aerospace, automotive, or energy production, this copper-based alloy delivers exceptional properties that can enhance the durability, wear resistance, and performance of critical components.
In this comprehensive guide, we’ll dive deep into the world of CuNi36In5. We’ll cover everything from its composition and properties to its applications, specifications, and pricing. If you’re a materials engineer, product designer, or someone curious about cutting-edge technologies, this article will provide the detailed insights you need to make informed decisions.
Overview of CuNi36In5 Spherical Copper-Based Spray Powder
CuNi36In5 is a copper-nickel alloy enhanced with indium and used primarily in thermal spray coating applications. The addition of 36% nickel (Ni) and 5% indium (In) to the copper base results in a material with improved corrosion resistance, thermal stability, and bonding strength. The spherical powder form is ideal for spray coating, ensuring uniform deposition and excellent adhesion to a wide range of surfaces.
This material is often used in gas turbine components, marine equipment, and electrical connectors, where its unique combination of properties is required to withstand extreme environments. The spherical shape of the particles allows for superior flowability, making it well-suited for plasma spraying, HVOF (High-Velocity Oxygen Fuel), and other thermal spray technologies.
Key Features of CuNi36In5 Spherical Copper-Based Spray Powder
- High Bond Strength: Excellent adhesion to base materials, ensuring long-lasting coatings.
- Corrosion Resistance: Superior performance in marine environments and industries exposed to saltwater or corrosive chemicals.
- Thermal Conductivity: Great heat transfer properties, making it ideal for thermal management applications.
- Wear Resistance: Enhanced durability under abrasive and erosive conditions.
- Spherical Particle Shape: Ensures smooth application and uniform coating in thermal spray processes.
Composition, Properties, and Characteristics of CuNi36In5 Spherical Copper-Based Spray Powder
The performance of CuNi36In5 Spherical Copper-Based Spray Powder is tied directly to its precise composition and material properties. Understanding the role of each element helps explain why this alloy performs so well in harsh environments.
Composition of CuNi36In5 Spherical Copper-Based Spray Powder
Element | Percentage (% by weight) | Role in the Alloy |
---|---|---|
Copper (Cu) | Balance (~59%) | Provides high thermal conductivity and excellent corrosion resistance. |
Nickel (Ni) | 36% | Enhances strength, corrosion resistance, and wear resistance. |
Indium (In) | 5% | Improves solderability, thermal stability, and provides a lubricating effect. |
Key Properties of CuNi36In5 Spherical Copper-Based Spray Powder
Property | Description |
---|---|
Density | Approximately 8.9 g/cm³, offering good mass for thermal spray applications. |
Tensile Strength | High tensile strength, contributing to durability and resistance to stress. |
Thermal Conductivity | Excellent heat transfer capabilities, ideal for thermal management coatings. |
Corrosion Resistance | Outstanding resistance to oxidation and corrosion in marine and chemical environments. |
Wear Resistance | High resistance to abrasion and erosion, making it suitable for high-wear applications. |
Melting Point | Approximately 1200°C, ensuring the powder can withstand high-temperature environments. |
Electrical Conductivity | Good electrical conductivity, making it useful for electrical connectors and conductive coatings. |
Flowability | The spherical shape ensures high flowability, critical for consistent spray coating performance. |
How Properties Translate to Performance
Think of CuNi36In5 as the “Swiss Army Knife” of spray powders. Its thermal conductivity ensures that it performs well in heat-sensitive applications, while its corrosion resistance makes it invaluable in marine or chemical environments where other materials might fail. The spherical shape of the powder ensures that it applies smoothly, allowing for even coatings that extend the lifespan of critical components.
Applications of CuNi36In5 Spherical Copper-Based Spray Powder
CuNi36In5 is a go-to material for a wide range of industries, thanks to its remarkable versatility. From aerospace to marine engineering, this alloy plays a crucial role in protecting and enhancing surfaces. Below, we’ll examine some common applications and why this alloy is so effective in each case.
Common Applications of CuNi36In5 Spherical Copper-Based Spray Powder
Industry | Applications |
---|---|
Aerospace | Gas turbine engines, heat exchangers, and thermal management systems. |
Marine | Propellers, hull coatings, and offshore drilling equipment. |
Automotive | Exhaust systems, heat shields, and brake components. |
Energy | Turbine blades, boiler tubes, and heat exchangers. |
Electrical | Electrical connectors, conductive coatings, and grounding systems. |
Industrial Machinery | Pump components, valves, and seals exposed to abrasive conditions. |
Why CuNi36In5 is Ideal for These Applications
Imagine you’re designing a turbine blade for a gas engine. You need a material that can handle extreme heat, resist corrosion, and maintain structural integrity under stress. CuNi36In5 excels in these conditions, offering the thermal stability and wear resistance that other materials simply can’t match.
Similarly, in the marine industry, this alloy’s ability to resist saltwater corrosion makes it a prime choice for propellers and hull coatings. It’s not just about protecting the surface; it’s about ensuring the longevity and performance of your equipment in some of the most challenging environments on Earth.
Specifications, Sizes, and Industry Standards for CuNi36In5 Spherical Copper-Based Spray Powder
When choosing a material for thermal spray applications, it’s crucial to select the right specifications. CuNi36In5 is available in a variety of particle sizes and conforms to industry standards, ensuring it meets the needs of different applications.
Common Specifications for CuNi36In5 Spherical Copper-Based Spray Powder
Specification | Description |
---|---|
Particle Size Distribution | Available in sizes ranging from 15-45 µm, 45-75 µm, and 75-150 µm. |
Purity | Typically 99.5% or higher, ensuring minimal contamination and maximum performance. |
Shape | Spherical, ensuring better flowability and consistency in thermal spray processes. |
Melting Point | Approximately 1200°C, ensuring performance in high-temperature environments. |
Surface Finish | Ensures smooth, uniform coatings with minimal roughness. |
Industry Standards | Complies with ISO 14919, AWS C2.25/C2.25M, and EN 15331 for thermal spraying. |
Why Specifications Matter
The right particle size can make or break a coating application. If you’re working with HVOF spraying, you might opt for a 45-75 µm particle size to ensure smooth application and a dense coating. On the other hand, if your project involves plasma spraying, a finer particle size like 15-45 µm may be ideal for achieving a high-quality surface finish.
Suppliers and Pricing for CuNi36In5 Spherical Copper-Based Spray Powder
Pricing for CuNi36In5 Spherical Copper-Based Spray Powder can vary based on factors like particle size, purity, and order volume. Below, we’ve gathered information on some of the most reputable suppliers and their price ranges.
Suppliers and Pricing for CuNi36In5 Spherical Copper-Based Spray Powder
Supplier | Country | Material | Price Range (per kg) |
---|---|---|---|
Praxair Surface Technologies | USA | CuNi36In5 Spherical Spray Powder | $250 – $400 |
Oerlikon Metco | Switzerland | High-Purity CuNi36In5 Powder | $280 – $450 |
H.C. Starck | Germany | CuNi36In5 for Thermal Spraying | $300 – $480 |
Höganäs AB | Sweden | Spherical Copper-Based Alloy Powder | $270 – $460 |
Tekna | Canada | CuNi36In5 Powder for Aerospace Applications | $290 – $500 |
Factors That Influence Pricing
Several factors can impact the pricing of CuNi36In5 Spherical Copper-Based Spray Powder:
- Particle Size: Finer particles are generally more expensive due to the increased precision required in their production.
- Purity: Higher purity levels, often demanded in aerospace or biomedical applications, come with a premium price tag.
- Order Volume: Large purchases often come with bulk discounts, lowering the overall cost per kilogram.
- Supplier Reputation: Established suppliers with a track record of quality control may charge higher prices, but the reliability often justifies the cost.
If your project requires high-purity powder for aerospace applications, you might consider purchasing from a supplier like Oerlikon Metco or Tekna, even though their prices may be on the higher end. The quality assurance and certifications these suppliers provide can make all the difference in critical, high-value applications.
Handling, Storage, and Safety Information for CuNi36In5 Spherical Copper-Based Spray Powder
Handling and storing CuNi36In5 requires attention to detail to ensure both safety and material integrity. Like all metal powders, it is essential to follow safety guidelines to prevent oxidation, contamination, or fire hazards.
Handling, Storage, and Safety Guidelines for CuNi36In5 Spherical Copper-Based Spray Powder
Aspect | Guidelines |
---|---|
Handling | Wear gloves, protective clothing, and use fume hoods to avoid inhalation. |
Storage | Store in a dry, cool environment, ideally in sealed containers to prevent moisture absorption. |
Fire and Explosion Risk | Fine metal powders can be combustible; ensure proper ventilation and avoid dust accumulation. |
Disposal | Follow local environmental regulations for the safe disposal of metal powders. |
Safety Equipment | Use masks and ensure proper ventilation to prevent inhalation of fine particles. |
Why Safety Matters with CuNi36In5
While CuNi36In5 is generally safe to handle, improper storage or exposure to moisture can lead to oxidation, compromising the quality of the powder. Additionally, the combustibility of fine metal powders means that proper ventilation and dust control are critical to avoid fire or explosion risks.
Comparing the Pros and Cons of CuNi36In5 Spherical Copper-Based Spray Powder
Like any material, CuNi36In5 has its advantages and limitations. Below, we’ll break down the pros and cons to help you determine if this spray powder is the right choice for your specific needs.
Advantages and Limitations of CuNi36In5 Spherical Copper-Based Spray Powder
Advantages | Limitations |
---|---|
Excellent Corrosion Resistance | Higher Cost compared to some other copper-based alloys. |
Good Thermal Conductivity | Limited Availability compared to more common spray powders. |
High Bond Strength | Combustible in fine powder form, requiring careful handling. |
Spherical Shape Ideal for Spray Coatings | More Expensive due to the spherical powder production process. |
Wear Resistance | Lower Electrical Conductivity compared to pure copper powders. |
Versatility Across Industries | Lower Melting Point compared to some other high-performance alloys. |
When the Advantages Outweigh the Limitations
For applications where corrosion resistance and thermal conductivity are critical, such as in marine or aerospace environments, the benefits of CuNi36In5 far outweigh its limitations. While it may come at a higher cost, its ability to protect expensive components from wear and corrosion ensures long-term savings by reducing the need for frequent maintenance or part replacements.
Frequently Asked Questions (FAQ) About CuNi36In5 Spherical Copper-Based Spray Powder
Question | Answer |
---|---|
What is CuNi36In5 Spherical Copper-Based Spray Powder used for? | It’s used in thermal spray coatings for industries like aerospace, marine, and automotive. |
Why is the spherical shape important? | The spherical shape ensures better flowability and uniform coating in thermal spray applications. |
How much does CuNi36In5 Spherical Copper-Based Spray Powder cost? | Prices range from $250 to $500 per kilogram, depending on supplier, particle size, and purity. |
Is CuNi36In5 corrosion resistant? | Yes, it offers excellent corrosion resistance, especially in marine and chemical processing environments. |
Can CuNi36In5 be used in high-temperature applications? | Yes, with a melting point of around 1200°C, it performs well in high-temperature environments. |
How is CuNi36In5 applied? | It’s typically applied using thermal spray techniques like HVOF and plasma spraying. |
Conclusion
CuNi36In5 Spherical Copper-Based Spray Powder is a high-performance material that combines corrosion resistance, thermal conductivity, and wear resistance, making it ideal for use in aerospace, marine, automotive, and energy industries. Its unique composition allows it to perform exceptionally well in harsh environments where other materials might fail.
By understanding its composition, properties, and applications, you can make informed decisions about incorporating CuNi36In5 into your next project. With trusted suppliers offering a range of particle sizes and specifications, you’ll be able to find the right product to meet your specific needs.
As technology continues to evolve, CuNi36In5 will remain a critical material for spray coating applications, ensuring that surfaces are protected and components last longer, even in the most challenging conditions.
Get Latest Price
About Met3DP
Product Category
HOT SALE
CONTACT US
Any questions? Send us message now! We’ll serve your request with a whole team after receiving your message.
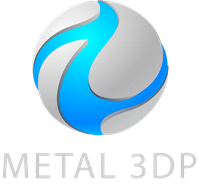
Metal Powders for 3D Printing and Additive Manufacturing