Custom Powders
Table of Contents
Imagine having the power to create a material exactly suited to your needs. Not just any material, but one where the very essence – its grain structure, composition, and properties – is meticulously designed. This is the realm of custom powders, a world where particles as tiny as specks of dust hold the key to groundbreaking innovation across countless industries.
In this comprehensive guide, we’ll delve deep into the fascinating world of custom powders. We’ll explore the different types, their unique properties, and the diverse applications that are pushing the boundaries of what’s possible. But before we dive in, let’s establish a foundational understanding.
What are Custom Powders?
Custom powders are finely-ground materials, meticulously engineered to possess specific characteristics. Unlike their off-the-shelf counterparts, these powders are tailored to meet the exact requirements of an application. This customization can involve:
- Composition: Precisely controlling the blend of elements to achieve desired properties like strength, conductivity, or melting point.
- Particle size and distribution: Manipulating the size and distribution of particles within the powder to influence factors like flowability, packing density, and reactivity.
- Morphology: Shaping the individual particles to achieve specific surface areas or enhance interaction with other materials.
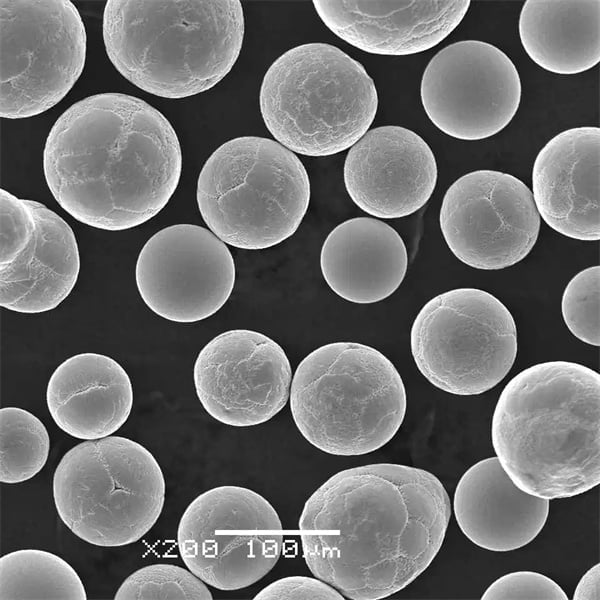
Why Use Custom Powders?
Think of custom powders as the building blocks of tomorrow’s advancements. By harnessing the power of precise engineering, they offer a multitude of advantages over traditional materials:
- Enhanced Performance: Custom powders can be designed to exhibit superior strength, conductivity, thermal resistance, or other performance-critical properties. Imagine lighter yet stronger components for aerospace applications, or more efficient heat exchangers for power plants.
- Unlocking New Applications: The tailored nature of custom powders allows them to be used in previously unimaginable applications. Imagine 3D printing intricate medical implants with biocompatible powders, or developing advanced battery technology with powders boasting exceptional energy density.
- Optimizing Processes: By controlling factors like flowability and packing density, custom powders can streamline manufacturing processes. This translates to reduced waste, improved efficiency, and ultimately, cost savings.
Exploring the Landscape of Custom Powders
The world of custom powders is a diverse one, encompassing a vast array of materials. Here are ten specific examples, each with its unique properties and applications:
1. Gas-Atomized Nickel Alloy Powders
- Composition: Primarily nickel, with controlled additions of chromium, aluminum, and titanium.
- Properties: Excellent high-temperature strength, oxidation resistance, and weldability.
- Applications: Turbine blades for jet engines, components for rocket engines, and parts for chemical processing equipment.
2. Spherical Titanium Powders
- Composition: Pure titanium or titanium alloys.
- Properties: High strength-to-weight ratio, excellent biocompatibility, and good corrosion resistance.
- Applications: Aerospace components, medical implants, and high-performance sporting goods.
3. Water-Atomized Stainless Steel Powders
- Composition: Various grades of stainless steel, with varying chromium and nickel content.
- Properties: Excellent corrosion resistance, good mechanical strength, and affordability.
- Applications: Food processing equipment, medical devices, and automotive components.
4. Aluminum Alloy Powders
- Composition: Aluminum blended with elements like silicon, copper, and magnesium.
- Properties: Lightweight, good formability, and high electrical conductivity (depending on alloy).
- Applications: Aerospace structures, heat sinks for electronics, and lightweight automotive components.
5. Inconel Powders
- Composition: Nickel-chromium superalloys with additions of elements like iron, molybdenum, and niobium.
- Properties: Exceptional high-temperature strength, oxidation resistance, and creep resistance.
- Applications: Turbine blades for gas turbines, rocket engine components, and parts for extreme-environment applications.
6. Custom Copper Powders
- Composition: Pure copper or copper alloys with controlled levels of oxygen or other elements.
- Properties: High electrical and thermal conductivity, good machinability, and excellent recyclability.
- Applications: Electrical components, heat exchangers, and parts requiring high thermal management capabilities.
7. Biocompatible Polymer Powders
- Composition: Polymers like polylactic acid (PLA) or polyetheretherketone (PEEK) specifically designed for medical applications.
- Properties: Biocompatible, biodegradable (for PLA), and good mechanical strength.
- Applications: Medical implants, drug delivery devices, and tissue engineering scaffolds.
8. Custom Refractory Powders
- Composition: High-melting-point materials like carbides, nitrides, and oxides.
- Properties: Excellent thermal resistance, good chemical stability, and high wear resistance.
- Applications: Linings for furnaces and reactors, crucibles for metal melting, and components for high-temperature applications.
9. Magnetic Powders
- Composition: Iron-based alloys or rare earth elements engineered for specific magnetic properties.
- Properties: Tailored magnetic permeability, coercivity, and remanence depending on composition and processing.
- Applications: Transformers, electric motors, data storage devices, and magnetic sensors.
1 0. Diamond Powders
- Composition: Micron-sized diamond particles.
- Properties: Extreme hardness, high thermal conductivity, and excellent wear resistance.
- Applications: Cutting and grinding tools, polishing compounds, and wear-resistant coatings.
A Look at the Properties Landscape
The table below provides a more comprehensive overview of the properties associated with various custom powder types. This allows for a quick comparison and highlights the versatility achievable through custom engineering.
Property | Material Examples | Description |
---|---|---|
Strength | Gas-atomized Nickel Alloys, Spherical Titanium Powders | Ability to withstand high mechanical stress. |
High-Temperature Resistance | Inconel Powders, Custom Refractory Powders | Maintains structural integrity at elevated temperatures. |
Corrosion Resistance | Water-Atomized Stainless Steel Powders, Biocompatible Polymer Powders (specific types) | Resists degradation from environmental factors. |
Lightweight | Aluminum Alloy Powders | Low density for weight-critical applications. |
Electrical Conductivity | Custom Copper Powders | Efficient transmission of electrical current. |
Thermal Conductivity | Custom Copper Powders, Diamond Powders | Effective transfer of heat. |
Biocompatibility | Biocompatible Polymer Powders | Compatible with living tissue, crucial for medical implants. |
Flowability | Various (depending on engineering) | Ease with which powder flows, impacting processing efficiency. |
Packing Density | Various (depending on engineering) | How tightly particles pack together, influencing material properties. |
Custom Powders in Action: Unveiling Diverse Applications
The true power of custom powders lies in their ability to revolutionize various industries. Here’s a glimpse into some of the groundbreaking applications:
- Aerospace: Custom powders are instrumental in creating lighter, stronger components for aircraft and spacecraft. Imagine jet engine turbine blades made from gas-atomized nickel alloys or lightweight aluminum alloy components for next-generation space vehicles.
- Medical Technology: The biocompatible nature of custom powders paves the way for advanced medical implants. Imagine 3D-printed bone grafts using biocompatible polymer powders or intricate prosthetic limbs crafted from titanium powders.
- Electronics: Custom copper powders with precisely controlled properties enable the development of high-performance electrical components. Imagine more efficient heat sinks for electronic devices or next-generation batteries boasting exceptional energy density thanks to custom powders.
- Manufacturing: Custom powders streamline manufacturing processes by optimizing flowability and packing density. This translates to reduced waste, improved production efficiency, and ultimately, cost savings across various industries.
Advantages and Limitations of Custom Powders
While custom powders offer a plethora of advantages, it’s important to acknowledge the potential limitations:
Advantages:
- Tailored Performance: Precisely engineered properties for specific applications.
- Unlocking Innovation: Enables the development of groundbreaking products and technologies.
- Process Optimization: Streamlines manufacturing for efficiency and cost savings.
Limitations:
- Development Costs: Custom engineering can be expensive, especially for initial development stages.
- Production Complexity: Manufacturing custom powders may require specialized equipment and expertise.
- Limited Availability: Certain custom powders might have limited commercial availability.
Choosing the Right Custom Powder
Selecting the right custom powder involves carefully considering your specific needs and priorities. Here are some key factors to ponder:
- Desired Properties: Identify the critical properties your application demands (strength, conductivity, etc.).
- Cost Considerations: Weigh the development and production costs of custom powders against potential benefits.
- Availability: Ensure the chosen custom powder is readily available from reputable suppliers.
- Processing Compatibility: Consider if your existing manufacturing processes can accommodate the specific powder characteristics.
The Future of Custom Powders: A World of Possibilities
The future of custom powders is brimming with exciting possibilities. As research and development efforts continue, we can expect to see:
- Even More Tailored Properties: The ability to engineer powders with even more precise and exotic properties.
- Advanced Manufacturing Techniques: Development of new techniques for cost-effective and scalable production of custom powders.
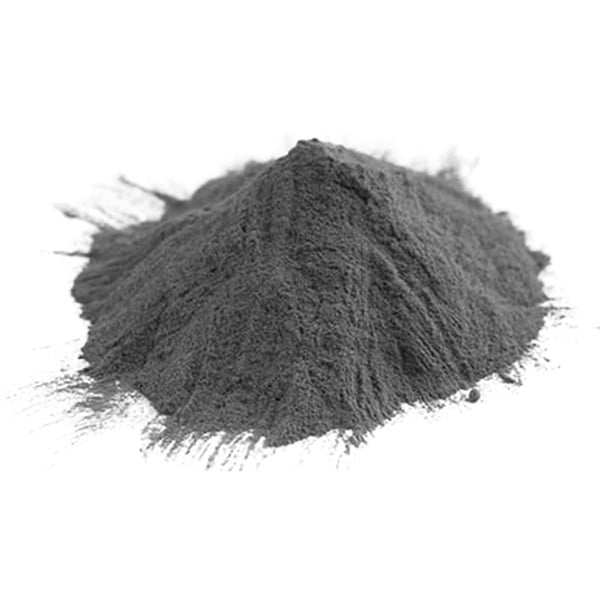
FAQ
Here are some of the most common questions regarding custom powders, presented in a clear and informative FAQ format:
Question | Answer |
---|---|
What are the size ranges of custom powders? | Custom powders can range in size from micrometers (millionths of a meter) to hundreds of micrometers. The specific size range is tailored to the desired application. For instance, powders for 3D printing typically fall within a specific range to ensure optimal flow and printability. |
How are custom powders manufactured? | There are various techniques for custom powder production, with some of the most common methods including gas atomization, water atomization, and mechanical grinding. Each method offers distinct advantages and is chosen based on the desired powder properties and material. |
Are custom powders safe to handle? | The safety of custom powders depends on the specific material composition. Some powders, like certain metal alloys, might require specific handling procedures due to potential health hazards. It’s crucial to consult safety data sheets (SDS) and follow recommended handling guidelines for each type of custom powder. |
How are custom powders priced? | The cost of custom powders can vary significantly depending on the material, complexity of engineering, and production volume. Generally, custom powders tend to be more expensive than off-the-shelf alternatives. However, the potential performance benefits and application-specific advantages can often justify the cost. |
Where can I find suppliers of custom powders? | Several reputable companies specialize in the production and supply of custom powders. Conducting online research or attending industry trade shows can help you connect with potential suppliers. When selecting a supplier, consider factors like their experience with your desired material, production capabilities, quality control standards, and customer service reputation. |
Conclusion
Custom powders represent a transformative force in the world of materials science and engineering. By harnessing the power of precise control, they unlock a vast spectrum of possibilities for innovation across countless industries. As technology continues to evolve, and our understanding of material behavior deepens, the potential of custom powders seems limitless. From crafting lighter, stronger components for space exploration to developing biocompatible implants that heal the human body, custom powders are poised to revolutionize the way we design, engineer, and interact with the world around us.
Share On
MET3DP Technology Co., LTD is a leading provider of additive manufacturing solutions headquartered in Qingdao, China. Our company specializes in 3D printing equipment and high-performance metal powders for industrial applications.
Inquiry to get best price and customized Solution for your business!
Related Articles
About Met3DP
Recent Update
Our Product
CONTACT US
Any questions? Send us message now! We’ll serve your request with a whole team after receiving your message.
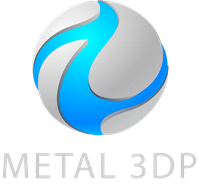
Metal Powders for 3D Printing and Additive Manufacturing
COMPANY
PRODUCT
cONTACT INFO
- Qingdao City, Shandong, China
- [email protected]
- [email protected]
- +86 19116340731