the Application of DMLS in Aerospace
Table of Contents
Imagine crafting intricate aircraft parts with unparalleled design freedom, slashing weight while boosting performance – that’s the magic of Direct Metal Laser Sintering (DMLS) in the aerospace industry. This revolutionary 3D printing technology is rapidly transforming how we design, manufacture, and utilize components in airplanes, satellites, and beyond. Buckle up, as we delve into the fascinating world of DMLS in aerospace, exploring its applications, the specific metal powders it utilizes, and the exciting future it promises.
DMLS: A 3D Printing Powerhouse for Aerospace
DMLS, also known as Direct Metal Laser Melting (DMLS®), is an additive manufacturing process that uses a high-powered laser to selectively melt metal powder particles layer by layer, building a 3D object from a computer-aided design (CAD) model. Unlike traditional subtractive manufacturing techniques like machining, DMLS creates parts from the ground up, offering a treasure trove of benefits for aerospace applications:
- Unmatched Design Freedom: DMLS breaks free from the limitations of conventional methods. Imagine internal lattice structures for weight reduction, complex cooling channels for improved engine efficiency, or parts with previously impossible geometries – DMLS makes it all possible.
- Lightweighting Prowess: Every gram counts in aerospace. DMLS allows engineers to design intricate, lightweight components that significantly reduce overall aircraft weight, translating to increased fuel efficiency and longer flight ranges.
- Rapid Prototyping and Iteration: The ability to fabricate complex parts quickly and directly from CAD models allows for swift prototyping and design iteration. This expedites the development process and reduces time-to-market for new aerospace technologies.
- Reduced Waste and Material Savings: DMLS utilizes only the necessary metal powder, minimizing waste compared to traditional methods that generate significant scrap material. This translates to cost savings and a more environmentally friendly manufacturing process.
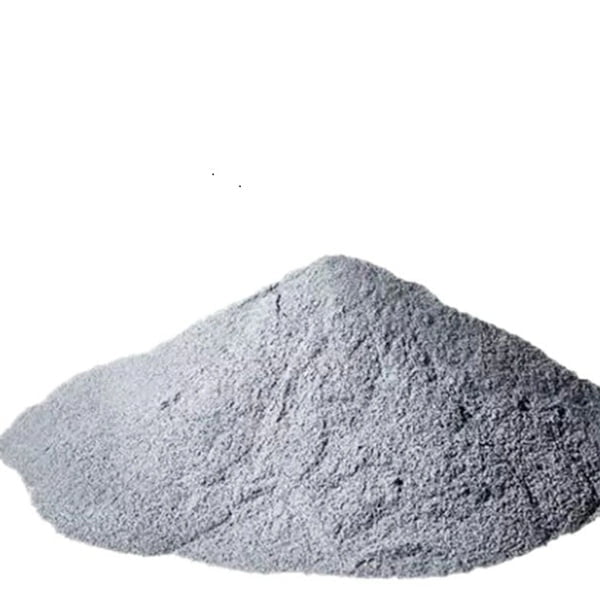
DMLS in Action: A Showcase of Applications
DMLS isn’t just theoretical; it’s revolutionizing aerospace in real-world applications:
- Aircraft Engines: Complex engine components like combustors, fuel injectors, and lightweight turbine blades with intricate internal cooling channels are being increasingly produced with DMLS, leading to improved fuel efficiency and engine performance.
- Airframe Structures: DMLS is enabling the creation of lightweight, high-strength airframe components like brackets, ribs, and fittings, contributing to overall weight reduction and enhanced aircraft performance.
- Satellites and Spacecraft: The ability to create intricate parts with high strength-to-weight ratios makes DMLS ideal for satellite structures, deployable mechanisms, and even propulsion components, paving the way for lighter, more efficient spacecraft.
- Unmanned Aerial Vehicles (UAVs): DMLS is perfectly suited for the rapid prototyping and production of lightweight, customized components for UAVs, fostering innovation in the rapidly growing drone industry.
The Arsenal of Metal Powders
The success of DMLS hinges on the specific metal powders used. Here’s a glimpse into some of the top contenders, each with its unique properties:
Metal Powder | Description | Properties | Applications in Aerospace |
---|---|---|---|
Titanium Alloys (Ti-6Al-4V, Ti-6Al-4V ELI): | The workhorse of aerospace DMLS, offering excellent strength-to-weight ratio, high corrosion resistance, and biocompatibility (useful for spacecraft life support systems). | Excellent mechanical properties, good weldability, biocompatible. | Turbine blades, airframe components, spacecraft structures. |
Inconel 625: | A high-performance nickel-chromium superalloy known for its exceptional high-temperature strength and oxidation resistance. | Exceptional high-temperature performance, good corrosion resistance. | Engine combustors, hot section components, high-temperature aerospace applications. |
Aluminum Alloys (AlSi10Mg, Scalmalloy): | Offering a good balance of strength, weight, and printability, aluminum alloys are finding increasing use in aerospace DMLS, particularly for non-critical components. | Lightweight, good printability, some strength limitations. | Lightweight airframe components, housings, non-critical parts. |
Stainless Steel (316L): | A versatile and cost-effective option, offering good corrosion resistance and machinability. | Good corrosion resistance, machinability, moderate strength. | Housings, ducting, non-critical components requiring corrosion resistance. |
Cobalt Chrome (CoCr): | A biocompatible alloy with excellent wear resistance, making it a valuable option for certain aerospace applications. | High wear resistance, biocompatible, good strength. | Landing gear components, specific wear applications. |
Copper Alloys (CuNi) (Continued): | Offering high thermal and electrical conductivity, copper alloys are finding niche applications in aerospace for heat exchangers and electrical components. | conductivity, good electrical conductivity. | Heat exchangers, electrical components in spacecraft. |
Molybdenum (Mo): | A refractory metal known for its exceptional high-temperature strength and good thermal conductivity. | Excellent high-temperature performance, good thermal conductivity. | Refractory components for rocket engines, heat shields. |
Tantalum (Ta): | Another refractory metal with a very high melting point and excellent corrosion resistance. | Ultra-high melting point, good corrosion resistance. | Crucibles for molten metal handling, specific high-temperature applications. |
Nickel Alloys (Rene 41, Inconel 718): | A family of high-performance nickel alloys offering a combination of strength, high-temperature performance, and good oxidation resistance. | Excellent mechanical properties, good high-temperature performance. | Turbine blades, disks, and other high-temperature structural components in jet engines. |
Choosing the Right Metal Powder
Selecting the optimal metal powder for a DMLS application is akin to a matchmaker’s job – it requires careful consideration of various factors:
- Required Properties: The specific needs of the component dictate the powder choice. High-temperature engine parts necessitate powders like Inconel 625 or Rene 41, while lightweight airframe components might utilize aluminum alloys.
- Printability: Not all metal powders are created equal in terms of printability. Factors like particle size, shape, and flowability significantly impact the success of the DMLS process.
- Cost: Metal powders vary considerably in price. Titanium alloys are generally more expensive than stainless steel, for instance. A balance needs to be struck between cost and performance requirements.
Advantages and Limitations of DMLS
While DMLS boasts a treasure trove of advantages, it’s not without limitations:
Advantages:
- Unmatched Design Freedom: DMLS unlocks previously unimaginable design possibilities, fostering innovation and performance gains.
- Lightweighting: The ability to create intricate, lightweight structures translates to significant weight reduction in aerospace applications.
- Rapid Prototyping and Iteration: DMLS expedites the development process by enabling swift prototyping and design changes.
- Reduced Waste: DMLS minimizes material waste compared to traditional methods, promoting sustainability.
Limitations:
- Material Availability: The selection of readily available metal powders for DMLS is still evolving compared to traditional manufacturing materials.
- Surface Finish: DMLS parts can have a rougher surface finish compared to machined components, potentially requiring additional post-processing steps.
- Part Size Limitations: Current DMLS machines have limitations on the size of parts they can produce.
- Cost: While DMLS offers long-term benefits, the upfront cost of DMLS machines and metal powders can be higher than traditional methods for certain applications.
The Future of DMLS in Aerospace: Soaring to New Heights
The future of DMLS in aerospace is nothing short of exhilarating. As technology advances, we can expect:
- Development of New Metal Powders: The range of readily available metal powders specifically designed for DMLS applications will continue to expand, pushing the boundaries of what’s possible.
- Larger Build Volumes: DMLS machines with larger build envelopes will become more commonplace, enabling the creation of even bigger and more complex aerospace components.
- Improved Surface Finish: Advancements in DMLS technology will lead to smoother surface finishes, potentially reducing the need for extensive post-processing.
- Reduced Costs: As DMLS technology matures and adoption increases, the overall cost of DMLS machines and metal powders is likely to decrease, making it more accessible for a wider range of aerospace applications.
DMLS is not just a manufacturing technology; it’s a catalyst for innovation in aerospace. By unlocking design freedom, reducing weight, and expediting development cycles, DMLS is propelling us towards a future of lighter, more efficient, and high-performance aircraft, satellites, and spacecraft. The sky’s truly the limit for DMLS in aerospace!
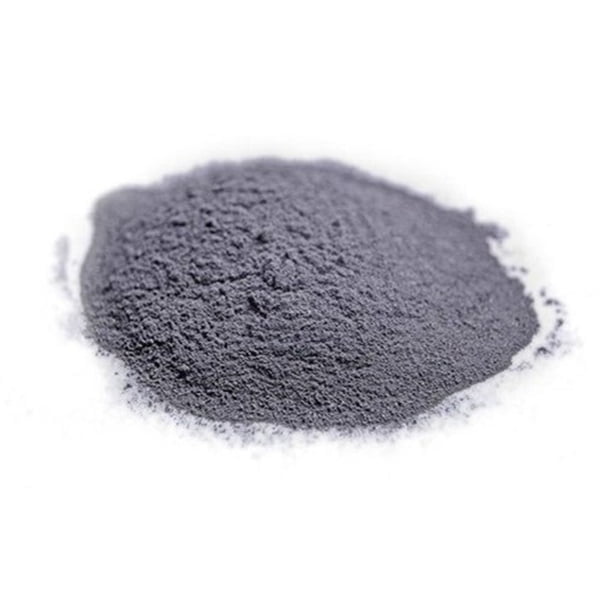
FAQ
Q: What are the advantages of using DMLS for aerospace applications?
A: DMLS offers numerous advantages, including unmatched design freedom, lightweighting capabilities, rapid prototyping, and reduced waste compared to traditional manufacturing methods.
Q: What are some of the limitations of DMLS?
A: Limitations include the current selection of readily available metal powders, potential surface finish challenges, part size limitations, and higher upfront costs compared to some traditional methods.
Q: What are some of the future trends for DMLS in aerospace?
A: The future of DMLS in aerospace is incredibly promising. We can expect advancements in several key areas:
Development of New Metal Powders: Metal powder manufacturers are constantly innovating, formulating new powders with superior properties specifically tailored for DMLS. This will expand the design possibilities even further, enabling the creation of components with even higher strength-to-weight ratios, improved high-temperature performance, and enhanced corrosion resistance. Imagine exotic alloys pushing the boundaries of what’s currently possible, revolutionizing engine performance and leading to the development of next-generation aerospace vehicles.
Larger Build Volumes: Current DMLS machines are limited in the size of parts they can produce. However, the future is brimming with larger build envelope machines. This will be a game-changer, allowing for the creation of entire airframe sections, large rocket engine components, and even complete satellite structures directly from a 3D printer. This opens doors for significant reductions in part count and assembly complexity, leading to lighter, more efficient spacecraft.
Improved Surface Finish: While DMLS parts offer exceptional functionality, their surface finish can be rougher compared to traditionally machined components. This can sometimes necessitate additional post-processing steps like polishing or machining. Advancements in DMLS technology, however, are leading to smoother surface finishes directly from the printing process. This will not only reduce post-processing needs but also potentially improve the performance of certain components by creating smoother airflow paths or reducing friction.
Reduced Costs: As DMLS technology matures and adoption increases, the overall cost of DMLS machines and metal powders is expected to decrease. This will make DMLS a more viable option for a wider range of aerospace applications, not just for high-end, performance-critical components. This democratization of DMLS has the potential to accelerate innovation across the entire aerospace industry.
In Conclusion
DMLS is not just a manufacturing technology; it’s a revolution in the making for the aerospace industry. By unlocking design freedom, reducing weight, expediting development cycles, and promoting sustainability, DMLS is propelling us towards a future of lighter, more efficient, and high-performance flying machines. As DMLS technology continues to evolve, the possibilities are truly limitless. The future of aerospace is undoubtedly shaped by DMLS, and the sky is truly not the limit – it’s just the beginning!
Share On
MET3DP Technology Co., LTD is a leading provider of additive manufacturing solutions headquartered in Qingdao, China. Our company specializes in 3D printing equipment and high-performance metal powders for industrial applications.
Inquiry to get best price and customized Solution for your business!
Related Articles
About Met3DP
Recent Update
Our Product
CONTACT US
Any questions? Send us message now! We’ll serve your request with a whole team after receiving your message.
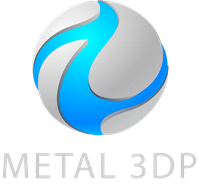
Metal Powders for 3D Printing and Additive Manufacturing