Comparison between EBM and Binder Jetting
Table of Contents
The world of 3D printing continues to evolve at a breakneck pace, offering exciting possibilities for creating complex metal objects. But with so many technologies vying for attention, choosing the right one for your project can be a daunting task. Two prominent contenders in this arena are Electron Beam Melting (EBM) and Binder Jetting. Both boast impressive capabilities, but their inner workings and ideal applications differ significantly. So, buckle up as we delve into the intricate dance between EBM and Binder Jetting, dissecting their materials, printing processes, strengths, and weaknesses to help you pick the perfect match for your metallic masterpieces.
The Difference in Materials Between These Two Metal 3D Printing Technologies
Imagine building a house; the quality of your bricks determines the sturdiness of the final structure. Similarly, in metal 3D printing, the material selection plays a crucial role. Let’s explore the types of metal powders compatible with each technology:
EBM Compatible Metal Powders:
Metal Powder | Description |
---|---|
Titanium Alloys (Ti6Al4V, Gr23) | Renowned for their exceptional strength-to-weight ratio, biocompatibility, and high-temperature resistance, making them ideal for aerospace, medical implants, and high-performance components. |
Nickel Superalloys (Inconel 625, Inconel 718) | These champions boast unbeatable resistance to corrosion, oxidation, and high temperatures, perfect for jet engine parts, turbines, and demanding oil & gas applications. |
Cobalt Chrome (CoCrMo) | A biocompatible powerhouse, often used in medical implants like knee and hip replacements due to its excellent wear resistance and corrosion tolerance. |
Copper (Cu) | This highly conductive metal finds applications in heat exchangers, electrical components, and even artistic creations due to its unique reddish hue. |
Stainless Steel (316L) | A versatile and cost-effective option, offering a good balance of strength, corrosion resistance, and affordability for various industrial applications. |
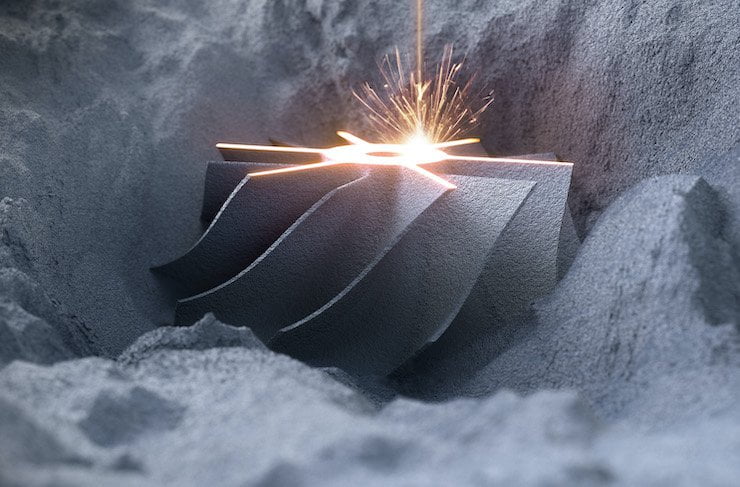
Binder Jetting Compatible Metal Powders:
Metal Powder | Description |
---|---|
Stainless Steel (17-4PH, 316L) | Similar to EBM, Binder Jetting utilizes various stainless steel grades, offering a blend of strength, corrosion resistance, and affordability for diverse applications. |
Tool Steel (H13, M2) | These steel powders are formulated for high wear resistance, making them suitable for creating molds, dies, and cutting tools. |
Copper (Cu) | Just like EBM, Binder Jetting can utilize copper powder, capitalizing on its excellent thermal and electrical conductivity for heat sinks and electrical components. |
Bronze (CuSn6) | An alloy of copper and tin, bronze offers a good balance of strength, wear resistance, and corrosion resistance, making it suitable for gears, bearings, and artistic prints. |
Inconel 625 | While less common than in EBM, Binder Jetting can also process Inconel 625 for applications requiring exceptional high-temperature performance. |
Key Points to Consider:
- EBM boasts a wider range of high-performance materials like titanium and nickel superalloys, catering to demanding applications.
- Binder Jetting offers a broader selection of affordable materials like stainless steel and tool steel, making it cost-effective for specific projects.
- Both technologies can handle copper for its conductive properties, but EBM might offer finer powder control for intricate designs.
The Printing Process Showdown: EBM vs. Binder Jetting
Now that we’ve explored the building blocks, let’s witness the magic unfold! EBM and Binder Jetting take fundamentally different approaches to transforming metal powder into 3D marvels.
EBM – A High-Vacuum Waltz:
Imagine a ballet performed in a pristine, airless environment. That’s the essence of EBM. The process unfolds in a vacuum chamber to prevent oxidation of the metal powder. Here’s a breakdown of the steps:
- Powder Deposition: A thin layer of metal powder is spread evenly across the build platform.
- Electron Beam Dance: A powerful electron beam scans the layer, selectively melting the powder particles according to the digital design. The molten metal fuses together, creating a solid layer.
- Layer by Layer: This meticulous dance of powder deposition and electron beam melting repeats, building the object layer by layer until it’s complete.
Binder Jetting – A Liquid Symphony:
Think of a skilled artist meticulously painting a masterpiece. Binder Jetting employs a similar principle, but with a robotic twist. Here’s how it works:
- Powder Spreading: A thin layer of metal powder is spread evenly across the build platform using a blade or roller mechanism.
- Binder Inkjet Printing: A specialized inkjet head selectively deposits a liquid binder onto the powder bed, adhering the particles together according to the digital design. Unlike EBM, there’s no melting involved at this stage.
- Layer by Layer: Similar to EBM, this process of powder spreading and binder jetting repeats, building the object layer by layer.
Post-Processing: The Final Touches
Both EBM and Binder Jetting require additional steps after the printing process is complete. Here’s what happens:
- EBM: The printed object remains in the vacuum chamber, where it undergoes a cooling process to maintain its structural integrity. It might also require support structure removal and additional finishing procedures depending on the application.
- Binder Jetting: The printed object is removed from the build chamber and undergoes a debinding process to remove the binding agent. This can involve thermal or chemical debinding techniques. Finally, the object is sintered in a furnace, which involves heating it to a high temperature (but below the melting point) to fuse the metal particles together and achieve the desired strength and density.
Key Points to Consider:
- EBM offers a more controlled and precise melting process, leading to denser and higher-strength parts compared to Binder Jetting.
- Binder Jetting is generally faster than EBM due to the simpler, inkjet-based approach. However, the post-processing steps can add additional time to the overall process.
- EBM requires a vacuum chamber, making it a more complex and expensive technology compared to Binder Jetting.
The Accuracy of These Two Metal 3D Printing Technologies is Different
Just like a painter’s brushstroke determines the detail in a painting, the printing process significantly impacts the accuracy of the final 3D printed object. Here’s a breakdown of what to expect:
- EBM: Due to the precise nature of the electron beam melting process, EBM generally offers higher dimensional accuracy and finer surface finishes compared to Binder Jetting. This makes it ideal for applications requiring intricate details and tight tolerances.
- Binder Jetting: The resolution of the binder jetting process can be slightly lower than EBM, leading to potentially rougher surface finishes and slightly larger dimensional variations. However, advancements in technology are continuously improving the accuracy of Binder Jetting.
Key Points to Consider:
- For parts requiring exceptional detail and tight tolerances, EBM reigns supreme.
- Binder Jetting can still achieve good accuracy for many applications, particularly when part complexity is not a major concern. The cost-effectiveness of Binder Jetting might outweigh slight accuracy limitations for certain projects.
The Equipment for These Two Metal 3D Printing Technologies is Different
The hardware behind each technology plays a crucial role in its capabilities and limitations. Let’s delve into the equipment differences:
- EBM Systems: These are complex machines with high-powered electron beam guns, vacuum chambers, and sophisticated layer-by-layer control systems. The cost of EBM machines is typically higher due to their advanced technology.
- Binder Jetting Systems: These systems are generally less complex than EBM machines. They utilize inkjet printing technology and furnace integration for debinding and sintering. The cost of Binder Jetting machines can be lower compared to EBM.
Key Points to Consider:
- The higher cost of EBM equipment translates to potentially higher printing costs per part compared to Binder Jetting.
- The simpler nature of Binder Jetting systems might make them more accessible to a wider range of users.
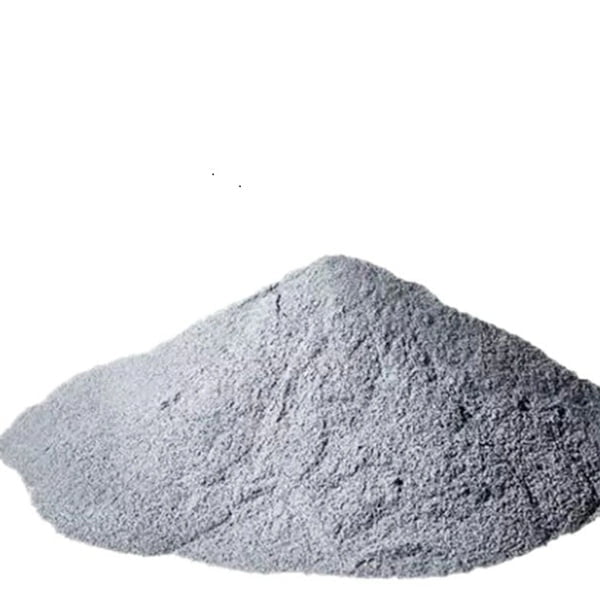
The Pros and Cons of EBM and Binder Jetting
Now that we’ve dissected the inner workings of each technology, let’s summarize their strengths and weaknesses to help you make an informed decision:
EBM
Pros:
- Excellent dimensional accuracy and surface finish
- High-density and strong parts
- Wide range of high-performance materials
- Ideal for complex geometries and intricate details
Cons:
- High cost of equipment and printing
- Limited material selection compared to Binder Jetting in some categories (e.g., affordable options)
- Slower printing speed compared to Binder Jetting
Binder Jetting
Pros:
- Faster printing speed
- More affordable equipment and printing costs
- Broader selection of materials, including cost-effective options
- Suitable for high-volume production runs
Cons:
- Slightly lower dimensional accuracy and surface finish compared to EBM
- Material properties might not be as high-performance as EBM for certain materials
- Post-processing steps add complexity
Choosing the Right Technology: A Balancing Act
Selecting the ideal metal 3D printing technology for your project hinges on a careful consideration of your priorities. Here’s a framework to guide your decision:
Prioritize high-performance parts with exceptional accuracy and detail: If your project demands top-notch mechanical properties, intricate features, and tight tolerances, EBM stands out as the champion. Applications like aerospace components, medical implants, and high-performance molds would greatly benefit from EBM’s strengths.
Cost is a major concern: For projects where affordability is paramount, Binder Jetting emerges as the more budget-friendly option. The lower equipment and printing costs, coupled with a wider selection of cost-effective materials, make Binder Jetting an attractive choice for prototypes, functional parts with moderate stress requirements, and applications where large volumes are needed.
Speed is of the essence: When time is a critical factor, Binder Jetting’s faster printing speed can be a game-changer. This technology is ideal for projects with tight deadlines or rapid prototyping needs.
Material selection is crucial: Consider the specific properties required for your project. If high-performance materials like titanium alloys or nickel superalloys are essential, EBM offers a wider range of options in that category. However, Binder Jetting provides a broader selection overall, including tool steels and bronzes, which might be suitable depending on the application.
Part complexity matters: EBM excels at creating intricate geometries with exceptional detail due to the precise nature of the electron beam melting process. If your design boasts complex features and tight internal channels, EBM might be the better choice. However, Binder Jetting can still handle moderately complex geometries for many applications.
Think about post-processing: While both technologies require additional steps after printing, EBM’s post-processing can be simpler due to the absence of a debinding stage. However, Binder Jetting’s debinding and sintering steps add complexity but can be a worthwhile trade-off for the potential cost savings.
Examples in Action: Putting Theory into Practice
Let’s illustrate the decision-making process with real-world scenarios:
- Scenario 1: A Lightweight Aircraft Bracket
Imagine you’re designing a lightweight bracket for an aircraft wing. Strength, weight reduction, and intricate details for stress distribution are paramount. In this case, EBM’s ability to handle high-performance materials like titanium alloys (known for their exceptional strength-to-weight ratio) and produce parts with excellent accuracy would make it the ideal choice.
- Scenario 2: Rapid Prototyping of a Tool Insert
You’re developing a new prototype for a tool insert and require a quick turnaround. While the final insert might be machined from high-grade steel, Binder Jetting’s speed and affordability make it a perfect fit for creating a functional prototype for initial testing. The ability of Binder Jetting to handle tool steel powders allows for material properties relevant to the final application.
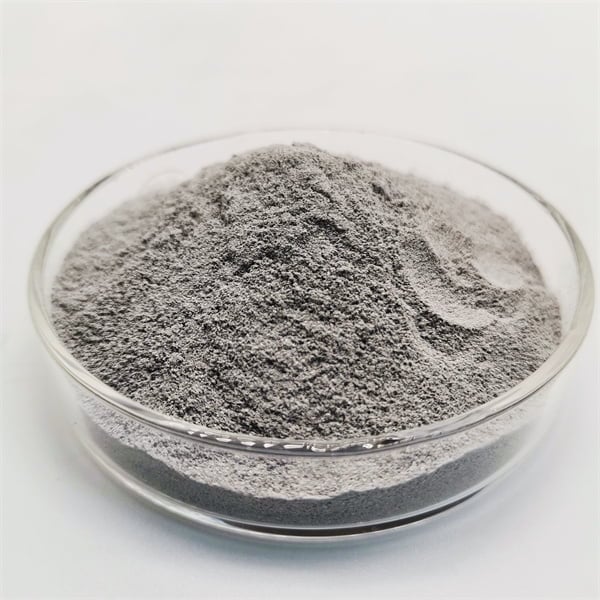
FAQ
Q: Which technology is environmentally friendly?
Both EBM and Binder Jetting can be environmentally friendly compared to traditional manufacturing techniques. EBM operates in a vacuum chamber, minimizing emissions and waste. Binder Jetting utilizes metal powder, and a significant portion of unused powder can often be recycled for future use, depending on the material and the specific system. However, the energy consumption for both processes should be considered.
Q: Can I print colorful parts with metal 3D printing?
While current metal 3D printing technologies don’t directly print multicolored parts, post-processing techniques like anodizing or plating can be used to achieve a desired color aesthetic on the printed metal.
Q: What are the safety considerations for metal 3D printing?
Metal 3D printing can involve working with fine metal powders, which can be hazardous if inhaled. Always consult the safety data sheet (SDS) for the specific metal powder you are using and follow the recommended safety precautions, which may include wearing appropriate personal protective equipment (PPE) such as gloves, respirator, and safety glasses. Additionally, EBM systems use high-powered electron beams, and proper training and safety protocols are essential when operating such equipment.
In Conclusion: Unveiling the Metal Marvels
EBM and Binder Jetting, though distinct in their approaches, represent powerful tools in the metal 3D printing landscape. By understanding their material capabilities, printing processes, strengths, and limitations, you can make an informed decision to unlock the potential of these metal marvels for your next project. Remember, the ideal technology hinges on your specific priorities – a balancing act between performance, budget, speed, and material requirements. So, unleash your creativity, embrace the possibilities of metal 3D printing, and transform your vision into a tangible masterpiece!
Share On
MET3DP Technology Co., LTD is a leading provider of additive manufacturing solutions headquartered in Qingdao, China. Our company specializes in 3D printing equipment and high-performance metal powders for industrial applications.
Inquiry to get best price and customized Solution for your business!
Related Articles
About Met3DP
Recent Update
Our Product
CONTACT US
Any questions? Send us message now! We’ll serve your request with a whole team after receiving your message.
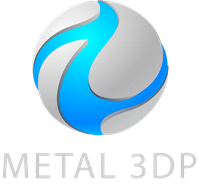
Metal Powders for 3D Printing and Additive Manufacturing