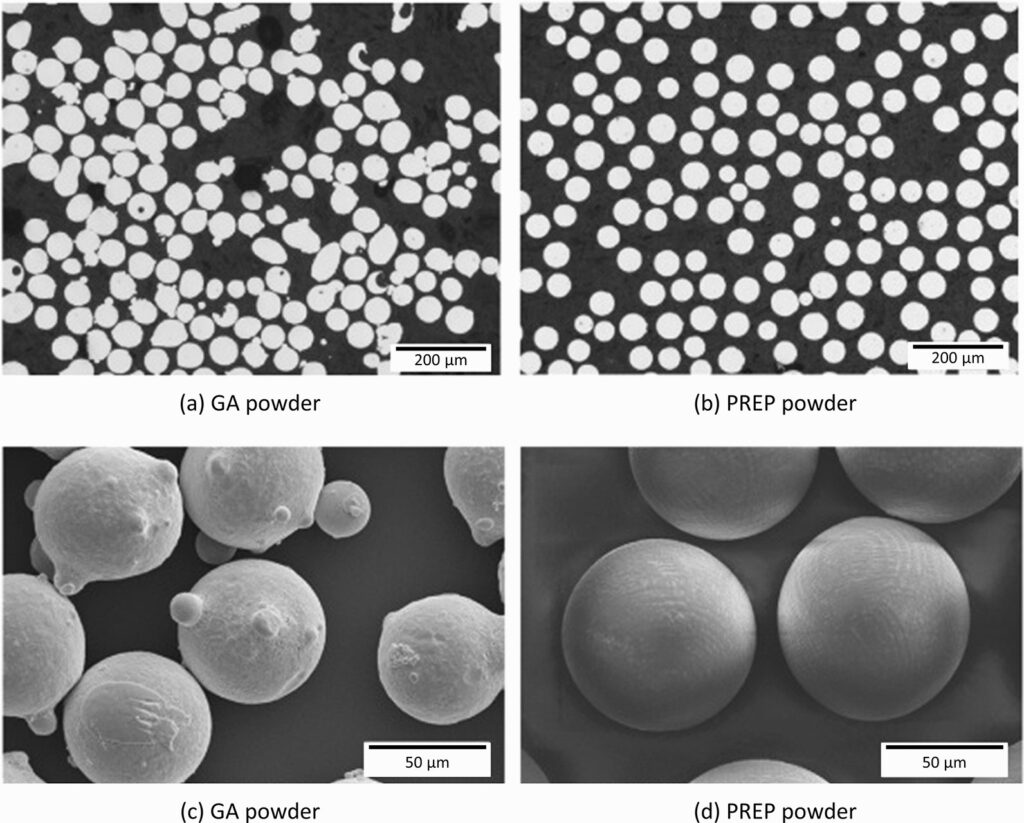
Electrolytic Tungsten Carbide: Why This Material Outperforms the Rest
Low MOQ
Provide low minimum order quantity to meet different needs.
OEM & ODM
Provide customized products and design services to meet unique customer needs.
Adequate Stock
Ensure fast order processing and provide reliable and efficient service.
Customer Satisfaction
Provide high quality products with customer satisfaction at the core.
share this article
Table of Contents
Electrolytic tungsten carbide is one of the most innovative materials in the world of engineering and manufacturing. Known for its incredible hardness, wear resistance, and versatility, it plays a critical role in applications ranging from cutting tools to industrial machinery. But what exactly is electrolytic tungsten carbide, and why is it so vital in today’s high-tech industries?
In this guide, we’ll dive deep into the world of electrolytic tungsten carbide, covering everything from its production process to its applications, pricing, and industry standards. Whether you’re an engineer looking to understand the material’s technical specs or a manufacturer considering it for your next project, this comprehensive guide has you covered.
Overview
Electrolytic tungsten carbide is a form of tungsten carbide produced via an electrolytic process, which sets it apart from traditional methods. This process results in a material with exceptional purity and enhanced performance characteristics, making it ideal for high-precision applications. The material consists of tungsten and carbon, usually in a ratio of 94:6 or 93:7. The electrolytic production method ensures a higher level of control over the material’s composition, leading to consistent quality and superior properties.
Why Choose Electrolytic Tungsten Carbide?
Why is electrolytic tungsten carbide different from the regular stuff? Well, imagine you’re building a high-performance car. You need the best engine, the best tires, and the best materials. Similarly, when you’re developing high-end tools or components, you need materials that can go the extra mile. With electrolytic tungsten carbide, you get a material that not only meets the standard requirements for hardness and durability but exceeds them in terms of purity and performance.
Composition and Properties
The unique production process of electrolytic tungsten carbide gives it several distinct properties that make it stand out from traditional tungsten carbide. Let’s break down its composition and key characteristics.
Characteristic | Description |
---|---|
Hardness | Extremely hard, typically around 9 on the Mohs scale, making it comparable to diamond in terms of hardness. |
Density | Electrolytic tungsten carbide has a density similar to other forms of tungsten carbide, approximately 15.6 g/cm³. |
Purity | The electrolytic production process allows for higher purity levels, usually over 99.9%, which enhances wear resistance and overall performance. |
Thermal Conductivity | The material has excellent thermal conductivity, which allows it to perform well in high-temperature environments, such as cutting or machining operations. |
Toughness | Despite its hardness, electrolytic tungsten carbide also exhibits good toughness, meaning it can withstand high-impact forces without cracking, making it ideal for heavy-duty tools. |
Wear Resistance | One of the most wear-resistant materials available, making it perfect for long-term use in abrasive environments. |
Corrosion Resistance | Enhanced corrosion resistance makes electrolytic tungsten carbide suitable for use in harsh chemical environments. |
Melting Point | Like other forms of tungsten carbide, it has a high melting point of around 2,870°C (5,198°F), allowing it to retain its properties at elevated temperatures. |
These properties make electrolytic tungsten carbide one of the most durable and versatile materials in industrial and high-tech applications. Its hardness, combined with toughness and corrosion resistance, provides a material that can withstand extreme wear and tear while maintaining performance.
Types
There are several types of electrolytic tungsten carbide, each designed for specific applications. These types vary slightly in composition and grain size, which can affect their performance. Here’s a breakdown of the most common types:
Type | Description |
---|---|
Fine-Grain Electrolytic Tungsten Carbide | With a grain size of less than 1 µm, fine-grain electrolytic tungsten carbide is used in precision tools where sharpness and cutting accuracy are critical. |
Coarse-Grain Electrolytic Tungsten Carbide | Grain sizes range from 1-10 µm, making it ideal for heavy-duty applications where toughness and impact resistance are more critical than sharpness. |
Cobalt-Bonded Electrolytic Tungsten Carbide | This type includes a small percentage of cobalt, improving toughness and resistance to cracking, especially in tools that experience high-impact forces. |
Nickel-Bonded Electrolytic Tungsten Carbide | Nickel is added instead of cobalt for applications that require superior corrosion resistance, such as in the oil and gas industry. |
Nano-Grain Electrolytic Tungsten Carbide | Features grain sizes smaller than 0.5 µm, providing extreme hardness and wear resistance, making it suitable for cutting-edge technologies like micro-tools and electronics. |
Each type of electrolytic tungsten carbide offers specific benefits and is tailored for different industrial needs. Whether you’re looking for extra sharpness in cutting tools or enhanced toughness in wear parts, there’s a type of electrolytic tungsten carbide for you.
Applications
Electrolytic tungsten carbide is used in a wide variety of industries, thanks to its superior hardness and wear resistance. Let’s take a look at some of its most common applications:
Application | Description |
---|---|
Cutting Tools | Electrolytic tungsten carbide is widely used in cutting tools such as drill bits, milling cutters, and saw blades, where high precision and wear resistance are essential. |
Mining and Drilling | In mining and drilling applications, electrolytic tungsten carbide is used in tools that face extreme wear and impact, such as rock drills and cutting tools. |
Aerospace Components | Its high-temperature stability makes electrolytic tungsten carbide ideal for aerospace components that must endure extreme conditions, like turbine blades and nozzles. |
Wear Parts | Bearings, bushings, and other parts that experience constant friction are often made from electrolytic tungsten carbide to extend their operational life. |
Metal Forming | Electrolytic tungsten carbide is used in dies and punches for forming metals, as it can resist deformation under high pressure and force. |
Medical Devices | High-purity electrolytic tungsten carbide is used in surgical tools where precision, durability, and biocompatibility are critical. |
Electronics | In the electronics industry, electrolytic tungsten carbide is used in micro-tools and other components where sharpness and hardness are essential. |
Defense and Military | Electrolytic tungsten carbide is used for armor-piercing ammunition and other military equipment that require materials capable of withstanding extreme forces. |
From cutting tools and aerospace components to military applications, electrolytic tungsten carbide proves to be a versatile and indispensable material for demanding environments.
Specifications, Sizes, Grades, and Industry Standards
When selecting electrolytic tungsten carbide, it’s crucial to understand the available specifications, grades, and industry standards. This ensures that the material you choose meets your specific needs for performance and durability.
Specification | Description |
---|---|
Grain Size | Grain sizes can range from nano-scale (<0.5 µm) to coarse (>10 µm), with finer grains offering higher sharpness and wear resistance. |
Purity Level | Typically ranges from 99.9% to 99.99%, depending on the application, with higher purity offering improved performance in critical applications. |
Toughness Rating | Measured in MPa·m½, toughness ratings for electrolytic tungsten carbide typically range from 8-12 MPa·m½, indicating resistance to cracking under stress. |
Hardness (HV) | Hardness is measured on the Vickers scale, with values typically ranging from 1600 to 2200 HV depending on grain size and application. |
ISO Standards | Electrolytic tungsten carbide often adheres to standards like ISO 9001 for quality management and ISO 4499 for cemented carbide properties. |
ASTM Standards | Standards such as ASTM B777 for tungsten and ASTM F288 for aerospace applications ensure consistency and quality in the material’s performance. |
Sintering Temperature | Sintering temperatures for electrolytic tungsten carbide typically exceed 1,300°C, depending on the specific grade and application. |
Understanding these specifications ensures that the material you choose will perform optimally in your specific application, whether you’re manufacturing cutting tools, medical devices, or aerospace components.
Suppliers and Pricing
The market for electrolytic tungsten carbide is diverse, with various suppliers offering different grades and sizes. Pricing varies based on factors such as purity, grain size, and order volume. Here’s a look at some of the major suppliers and pricing trends in the market.
Supplier | Country | Price Per Kg (USD) | Purity Levels Available | Notable Features |
---|---|---|---|---|
Global Tungsten & Powders Corp. | United States | $800 – $1,500 | 99.9% – 99.99% | Renowned supplier of high-purity electrolytic tungsten carbide for aerospace and medical applications. |
H.C. Starck Tungsten | Germany | $900 – $1,600 | 99.95% – 99.99% | Specializes in high-grade tungsten carbide powders for cutting tools and wear parts. |
Buffalo Tungsten | United States | $700 – $1,300 | 99.9% – 99.95% | Competitive pricing for large-scale industrial applications. |
Zhuzhou Cemented Carbide Group | China | $600 – $1,200 | 99.9% – 99.95% | Major supplier for mining and drilling industries. |
ALMT Corp | Japan | $850 – $1,400 | 99.99% | Focuses on high-purity carbide for precision tools and advanced electronic components. |
Pricing for electrolytic tungsten carbide can vary significantly depending on the supplier, the grade of material, and the volume of the order. It’s essential to request quotes from several suppliers to find the right balance of quality and cost for your specific needs.
Advantages and Limitations
Like any material, electrolytic tungsten carbide comes with its own set of advantages and limitations. Understanding both can help you make an informed decision about whether this material is right for your application.
Advantages | Limitations |
---|---|
Exceptional Hardness: Electrolytic tungsten carbide is one of the hardest materials, making it ideal for cutting tools and wear parts. | Cost: Electrolytic tungsten carbide is more expensive than standard tungsten carbide due to its purity and production process. |
High Wear Resistance: Its ability to resist wear and abrasion makes it suitable for long-term, high-stress applications. | Brittleness: Despite its toughness, it can still be brittle under extreme impact, especially in less ductile applications. |
Corrosion Resistance: High purity levels improve its resistance to corrosion in harsh chemical environments. | Machining Difficulty: Due to its hardness, machining electrolytic tungsten carbide requires specialized tools and techniques. |
Thermal Stability: Performs well in high-temperature environments, maintaining its properties under extreme heat. | Oxidation Risk: At very high temperatures, the material can oxidize if not properly protected, reducing its overall durability. |
While electrolytic tungsten carbide offers superior performance in terms of hardness, wear resistance, and corrosion resistance, it’s essential to consider its cost and machining difficulties when deciding if it’s the right material for your project.
Frequently Asked Questions (FAQ)
Let’s answer some of the most common questions people have about electrolytic tungsten carbide.
Question | Answer |
---|---|
What is it? | It’s a type of tungsten carbide produced via an electrolytic process, resulting in higher purity and enhanced performance characteristics. |
How is it different from regular tungsten carbide? | It is purer, with fewer impurities, which improves its wear resistance, hardness, and corrosion resistance. |
What is it used for? | It’s used in cutting tools, aerospace components, mining equipment, medical devices, and electronics, thanks to its hardness, toughness, and durability. |
How much does it cost? | Prices vary, typically ranging from $600 to $1,600 per kilogram, depending on purity, grain size, and supplier. |
Can it be machined? | Yes, but it requires specialized tools and techniques due to its extreme hardness, which makes conventional machining difficult. |
Is it resistant to corrosion? | Yes, it has excellent corrosion resistance, especially in high-purity forms, making it suitable for harsh chemical environments. |
Conclusion
It is a powerful, high-performance material that excels in demanding applications. Its hardness, wear resistance, and corrosion resistance make it ideal for industries like aerospace, mining, and manufacturing. However, it’s essential to weigh the benefits against the limitations, such as cost and machining difficulty, to determine if it’s the right material for your project.
As industries continue to push the boundaries of what’s possible, the role of materials like electrolytic tungsten carbide will only become more significant. Whether you’re developing cutting tools or aerospace components, this material offers the durability and performance needed to meet the most challenging requirements.
Get Latest Price
About Met3DP
Product Category
HOT SALE
CONTACT US
Any questions? Send us message now! We’ll serve your request with a whole team after receiving your message.
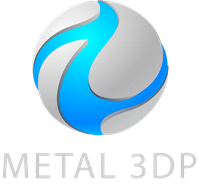
Metal Powders for 3D Printing and Additive Manufacturing