electron beam melting 3d printing
Table of Contents
Overview
electron beam melting 3d printing is an additive manufacturing technology that uses an electron beam as energy source to selectively melt and fuse metallic powder particles layer-by-layer to fabricate complex 3D parts.
Compared to other metal 3D printing methods, EBM offers distinct advantages like excellent mechanical properties, high build rates, vacuum processing benefits, and suitability for reactive materials. However, the high equipment cost and limited material options have confined EBM usage to demanding applications in aerospace, medical, and automotive sectors.
This comprehensive guide covers EBM technology, process, materials, applications, system manufacturers, costs, advantages/limitations, and other FAQs to help manufacturers evaluate if EBM is the right metal AM solution for their needs.
How Electron Beam Melting 3D Printing Works
EBM printing involves the following key steps:
3D Model Preparation
- CAD model optimized for EBM – wall thicknesses, supports, orientation etc.
File Conversion to .STL
- CAD geometry converted to triangular facets .STL file
Machine Setup
- Build parameters input – speed, power, focus offset etc.
- Material loaded, parameters adjusted based on powder properties
Powder Raking
- Powder uniformly raked over build platform in controlled layers
Electron Beam Melting
- Focused electron beam selectively melts powder to build each layer
- Vacuum environment prevents oxidation
Lowering of Platform
- After a layer is melted, platform indexed down by layer thickness
- Fresh layer of powder spread over previous layer
Removal from Machine
- Excess powder removed from built parts
- Support structures detached
- Post-processing done if needed
The layer-by-layer building process enables intricate, optimized geometries with excellent properties.
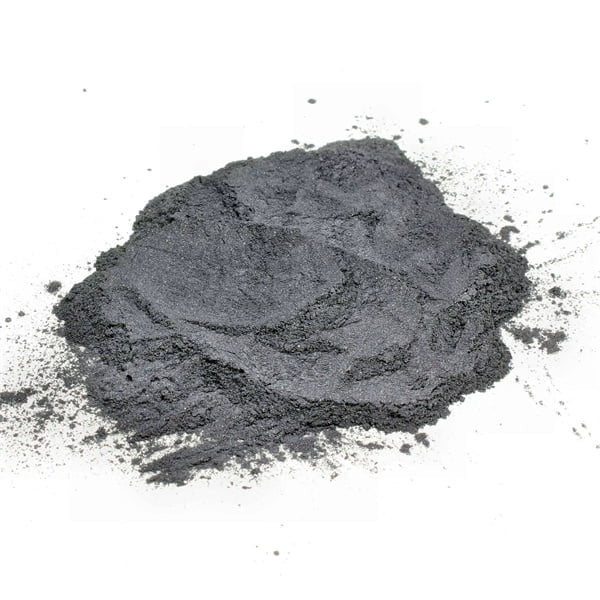
Materials for EBM 3D Printing
EBM is compatible with a range of metal alloys:
Material | Key Properties | Applications |
---|---|---|
Titanium alloys | High strength, low weight ratio | Aerospace, medical implants |
Nickel superalloys | Heat and corrosion resistance | Turbine blades, rocket nozzles |
Cobalt-chrome | Biocompatibility, high hardness | Dental implants, medical devices |
Tool steels | Excellent wear resistance | Cutting tools, molds, dies |
Stainless steels | Corrosion resistance, high ductility | Pumps, valves, vessels |
Both standard and custom alloys optimized for EBM can be printed. Parameter tuning is required for new materials to achieve desired properties.
EBM Machine Suppliers
The major EBM equipment manufacturers include:
Supplier | Key Machine Models | Build Envelope |
---|---|---|
Arcam EBM (GE Additive) | Arcam A2X, Q10plus, Spectra H, Spectra L | 254 x 254 x 380 mm |
Velo3D | Sapphire | 250 x 250 x 300 mm |
Raycham | EBAM 300 | 300 x 300 x 300 mm |
Sciaky | EBAM 110 | 1100 x 1100 x 900 mm |
JEOL | JEM-ARM300F | 300 x 300 x 300 mm |
Arcam EBM pioneered commercial EBM systems. Other providers have entered more recently, expanding material and size capabilities.
Specifications
Typical EBM system specifications:
Parameter | Specification |
---|---|
Beam power | Up to 12 kW |
Accelerating voltage | 60 kV |
Beam current | Up to 40 mA |
Beam size | 200 μm minimum |
Scan speed | Up to 8000 m/s |
Focus offset | Automatic, settable 0-5 mm |
Vacuum | 5 x 10-4 mbar |
Layer thickness | 50-200 μm |
Maximum build size | 1100 x 1100 x 900 mm |
Repeatability | ± 0.2% of build height |
Higher power and finer focus provides sharper melt pools and better feature resolution. Larger build envelopes facilitate batch production.
EBM Design Principles
Key EBM part design principles:
- Minimize unsupported surfaces to prevent distortion
- Use self-supporting angles above 45° to avoid supports
- Design internal channels for unmelted powder removal
- Account for ~20% shrinkage compared to final part dimensions
- Include texturing to improve powder flow into intricate areas
- Position parts for uniform heating and efficient packing
- Design structures to minimize trapped powder
- Keep overhangs above 30° to prevent dripping
- Use conformal lattice supports when needed
EBM design freedom allows consolidating assemblies into optimized, lightweight monolithic parts.
Applications of EBM
EBM is ideal for:
Aerospace and automotive:
- Turbine blades, fuel injectors, structural frames, intricate enclosures
Medical:
- Orthopedic implants, prosthetics, surgical tools requiring biocompatibility
Industrial:
- Lightweight robotics components, fluid handling parts subjected to corrosion
Defense:
- Durable, customized components like cooling channels and mounts
R&D:
- Novel alloys, metal matrix composites, and lattice structures
EBM’s combination of design freedom, engineering properties and manufacturing economics make it the process of choice for critical applications.
Cost Analysis
EBM system and part production cost depend on:
Machine Purchase
- ~$800,000 for medium-sized production machines
- Multi-million investment for large systems
Material Cost
- Powder can range from $100-500/kg
- Some alloys like Ti64 command premium pricing
Operation Cost
- Average machine cost ~$50-150/hour
- Labor for pre/post processing
Part Size
- Larger parts require more material and build time
- Small parts can be nested for efficiency
Post-processing
- Heat treatment, CNC, finishing increase costs
Total Cost Per Part
- Small parts ~ $20-$50 per cubic inch
- Large parts ~$5-$15 per cubic inch
Higher utilization via batch production and nesting lowers cost per part.
Process Control and Optimization
Critical process parameters to control:
- Power – Influences melt pool size, penetration, build rate
- Speed – Impacts resolution, surface finish, deposit shapes
- Focus offset – Controls beam shape, penetration, defects
- Layer thickness – Determines Z-axis resolution, build time
- Hatch spacing – Adjust to achieve required density, prevent balling
- Scanning strategy – Unidirectional, island, contour patterns affectresidual stresses and distortion
- Preheat – Improves powder sintering, reduces cracking and warpage
Design of Experiments combined with melt pool studies and microstructural characterization inform parameter selection to achieve desired properties.
Post-Processing
Typical EBM post-processing steps:
- Removal – Depowdering to detach parts from build plate
- Support removal – Cutting off support structures if needed
- Stress relieving – Heat treatment to prevent cracking
- Surface finishing – Machining, grinding, polishing to improve finish
- Hot isostatic pressing – Applies heat and pressure to close residual pores and improve density
- Inspection – Confirming dimensions, material composition, defects
Minimizing supports and post-processing is a key consideration during EBM part design.
Qualification and Certification
EBM parts destined for regulated industries require:
- Testing to applicable standards like ASTM F2924, ASTM F3001 etc.
- Extensive metrological inspection for critical dimensions and surface quality
- Material composition analysis through chemical analysis, microstructure characterization
- Mechanical property evaluation like tensile, fatigue, fracture toughness testing
- Non-destructive inspection using X-ray tomography, liquid penetrant testing etc.
- Documentation of full traceability for powder, build parameters, post-processing etc.
- Formal part qualification and certification by relevant bodies
Following established protocols and standards ensures parts meet the stringent quality demands.
EBM Compared to Other Metal AM
EBM Advantages
- Excellent material properties from faster cooling
- High productivity and low cost per part
- Minimal support structures needed
- Unaffected by residual stresses and distortion
- Vacuum environment prevents oxidation
- Lower thermal gradients vs laser processes
Limitations
- Conductive materials only, limited material options currently
- More geometrical constraints than laser AM
- Rough surface finish often requires post machining
- Equipment cost is higher than laser systems
Implementing EBM Successfully
Keys to EBM adoption:
- Evaluate part application requirements versus EBM capabilities
- Assess expected machine utilization to determine ROI
- Account for post-processing time/cost during planning
- Partner with experienced service bureaus to minimize learning curve
- Leverage EBM design expertise to redesign parts for optimal manufacturability
- Graduate from prototyping to series production to maximize productivity
- Implement robust quality management and certification protocols
A holistic implementation approach enables companies to leverage EBM benefits and become production leaders.
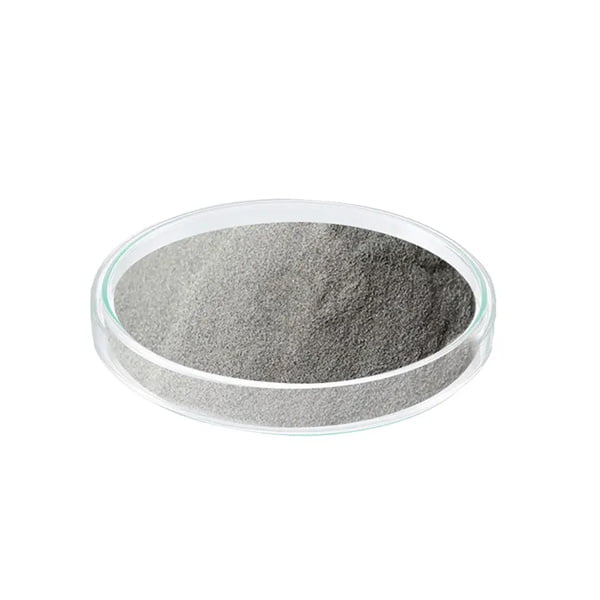
FAQs
What materials are used in EBM?
Titanium alloys, nickel superalloys, tool steels, cobalt-chrome, and stainless steels are common. Both standard and custom alloys optimized for EBM can be printed.
How does the cost of EBM compare to other metal AM processes?
EBM machines and powder feedstock are more expensive than laser-based AM systems. But higher build rates and productivity can offset this for production applications.
What are some key differences between EBM and selective laser melting?
Faster build rates, elevated temperature operation, and excellent material properties differentiate EBM, while limitations in surface finish and geometric freedom are the main tradeoffs.
What types of post-processing are typically required for EBM parts?
Support removal, stress relieving heat treatment, hot isostatic pressing, and surface finishing like CNC machining are common. Minimizing supports during design reduces post-processing.
What size parts can be built using EBM technology?
Small benchtop systems have build volumes under 100 mm cubed while large production systems can accommodate parts over a meter in size. Maximum size is expanding with newer large-format machines.
Conclusion
EBM’s unique rapid melting capabilities enable manufacturing intricate metal components with unmatched properties and productivity. While equipment costs and material options have restricted adoption so far, continued advances are opening up new applications across aerospace, medical, defense, automotive, and energy sectors. EBM’s future is bright as part quality and reliability continue to improve while metal powders become more available and affordable. Informed manufacturers who leverage EBM’s advantages while accounting for its limitations are poised to disrupt incumbents and become new leaders.
Share On
MET3DP Technology Co., LTD is a leading provider of additive manufacturing solutions headquartered in Qingdao, China. Our company specializes in 3D printing equipment and high-performance metal powders for industrial applications.
Inquiry to get best price and customized Solution for your business!
Related Articles
About Met3DP
Recent Update
Our Product
CONTACT US
Any questions? Send us message now! We’ll serve your request with a whole team after receiving your message.
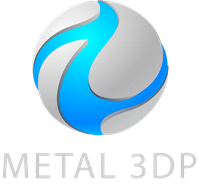
Metal Powders for 3D Printing and Additive Manufacturing
COMPANY
PRODUCT
cONTACT INFO
- Qingdao City, Shandong, China
- [email protected]
- [email protected]
- +86 19116340731