Electron Beam Melting Machines
Table of Contents
Overview of electron beam melting machine
Electron beam melting (EBM) is an additive manufacturing technology used to fuse metal powders into fully dense parts layer-by-layer using a high power electron beam under vacuum conditions. EBM machines offer unmatched build speeds and mechanical properties unachievable with other metal 3D printing methods.
Key attributes of EBM technology include:
Table 1: Overview of Electron Beam Melting Technology
Attribute | Description |
---|---|
Heat Source | High intensity electron beam |
Environment | High vacuum |
Feedstock | Metal powder bed |
Beam Control | Electromagnetic lenses and coils |
Build Mode | Layer-by-layer metal powder fusion |
Applications | Aerospace, medical, automotive, tooling |
By leveraging precise beam focusing and rapid scanning, EBM fuses conductive materials like titanium, nickel alloys, tool steels, and refractory metals into fully dense components with superior properties exceeded only by wrought products.
The controlled vacuum environment prevents contamination while the intelligent energy delivery and high preheat temperatures minimize residual stresses leading to warp or cracks.
Understanding these core principles helps illustrate why EBM delivers exceptional mechanical performance tailor-made for the most demanding industry applications.
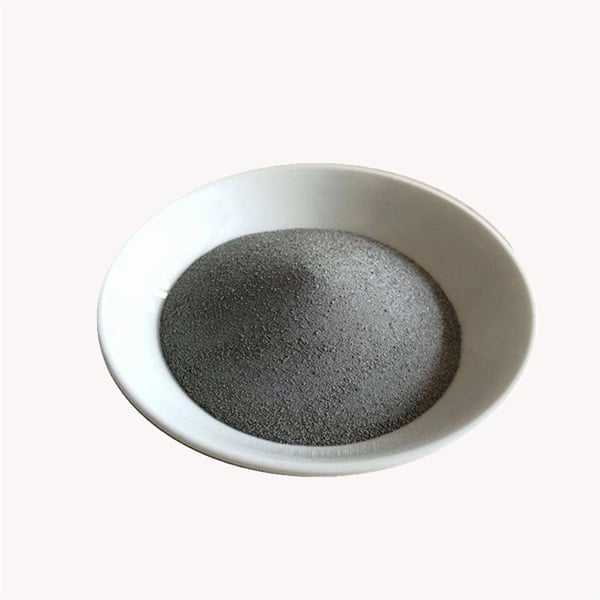
Types of Electron Beam Melting Systems
Feature | Description | Impact on System Use |
---|---|---|
Electron Gun Configuration | Electron beam melting systems utilize an electron gun to generate a high-energy beam that selectively melts metal powder. There are two main configurations for electron guns: * Sidewinder: The electron beam source is positioned horizontally alongside the build chamber. This design allows for a larger build chamber volume but may limit access for post-processing. * Top Gun: The electron beam source is situated directly above the build chamber. This configuration offers easier access for part removal and monitoring but may restrict the maximum build envelope. | The selection of gun configuration depends on the priority between build volume and accessibility. Sidewinders are ideal for high-throughput production of larger parts, while Top Guns are better suited for research and development applications where frequent part monitoring and manipulation are necessary. |
Beam Melting Mode | EBM systems can operate in two primary beam melting modes: * Raster Scan: The electron beam rapidly scans across the powder bed in a predetermined pattern, melting designated areas layer-by-layer. This method is efficient for simple geometries but can create stair-stepping artifacts on curved surfaces. * Vector Scan: The electron beam follows a defined vector path to melt the powder. This method offers greater control over melt pool geometry and surface finish, particularly for intricate features. However, vector scanning can be slower than raster scanning for simple geometries. | The choice between raster and vector scan modes depends on the desired balance between speed, resolution, and surface quality. Raster scanning is preferred for high-volume production of parts with basic geometries, while vector scanning is more suitable for complex parts demanding high accuracy and surface finish. |
Vacuum System Design | Electron beam melting necessitates a high vacuum environment (typically below 10^-4mbar) to prevent oxidation of the molten metal and ensure beam stability. There are two common vacuum system designs: * Diffusion Pump: This traditional design utilizes diffusion pumps to achieve the required vacuum level. Diffusion pumps are reliable and well-established but require routine maintenance and can be relatively slow to reach optimal vacuum levels. * Cryopumping: This newer technology employs cryopumps to capture gas molecules through extreme cooling. Cryopumps offer faster pump-down times and reduced maintenance needs compared to diffusion pumps. However, they have a higher initial investment cost and may require additional plumbing for liquid nitrogen supply. | The selection of vacuum system design hinges on factors like budget, maintenance requirements, and desired cycle times. Diffusion pumps are a cost-effective choice for established production environments, while cryopumping offers advantages for high-throughput applications or research settings prioritizing fast turnaround times. |
Powder Delivery System | The even distribution of metal powder across the build platform is critical for successful EBM builds. Two primary powder delivery systems are employed: * Blade Coating: A blade or rake spreads a thin layer of powder over the build platform after each melting cycle. Blade coating is a simple and reliable method but can cause inconsistencies in powder density due to variations in blade pressure and angle. * Recoil Spreading: A high-pressure gas stream disrupts the powder bed, causing the powder particles to recoil and deposit a fresh layer. Recoil spreading offers more uniform powder distribution compared to blade coating but requires careful optimization of gas pressure to avoid disturbing previously melted layers. | The powder delivery system selection impacts layer quality and repeatability. Blade coating is suitable for low-volume production or applications where powder density is less critical. Recoil spreading is preferred for high-precision parts demanding consistent powder distribution. |
Fundamentals of Electron Beam Melting Process
Stage | Description | Advantages | Considerations |
---|---|---|---|
Powder Preparation | Metal powders used in EBM are meticulously produced to ensure optimal flowability, particle size distribution, and chemical purity. Particle size plays a crucial role, as excessively fine powders can hinder layer spreading, while overly coarse powders can lead to balling and poor fusion. Strict control over oxygen, nitrogen, and other elements is essential to minimize porosity and achieve the desired mechanical properties. | * Consistent material properties throughout the build * Reduced risk of defects like porosity and cracking | * High upfront cost of high-quality metal powders * Need for specialized handling and storage due to potential reactivity |
Vacuum Chamber | Electron Beam Melting necessitates a high vacuum environment (typically between 10⁻⁴ and 10⁻⁹ Pa) to prevent oxidation and contamination of the molten metal. This is achieved by powerful vacuum pumps that extract air molecules from the chamber. The absence of oxygen allows for processing of reactive metals like titanium and tantalum. | * Minimizes interaction between molten metal and atmospheric gases * Enables production of high-density parts with excellent mechanical properties | * Complex and expensive vacuum pumping systems required * Additional considerations for moisture control to prevent spatter and inconsistencies |
Electron Beam Generation | At the heart of EBM lies an electron gun, which emits a focused beam of high-energy electrons. An electric field heats a filament (cathode), causing it to release electrons. These electrons are accelerated by a high voltage towards an anode and further concentrated by electromagnetic coils. The resulting beam boasts exceptional power density, capable of melting even refractory metals with high melting points. | * Precise control over melt pool size and depth * Deep penetration for complex geometries with internal features | * Requires high voltage and sophisticated beam control systems * Maintenance and calibration of the electron gun are crucial |
Powder Delivery and Spreading | A blade or roller mechanism meticulously spreads a thin layer of metal powder across the build platform. This layer thickness, typically ranging from 30 to 100 microns, is predetermined by the desired resolution and part geometry. | * Ensures uniform layer thickness for consistent material properties * Enables creation of intricate features | * Precise control of powder spreading mechanism is critical * Powder flowability and particle size distribution can impact spreading efficiency |
Selective Melting | The electron beam, guided by computer-controlled scanning mirrors, selectively melts specific regions of the powder bed according to a sliced 3D model. The unmelted powder acts as support for overhanging structures, eliminating the need for external support structures common in other additive manufacturing techniques. | * High precision and accuracy in building complex geometries * Capability to create internal features and channels | * Careful scan path planning is necessary to optimize melting and minimize residual stress |
Layer-by-Layer Building | Following the melting of a single layer, a fresh layer of powder is deposited on top. The electron beam then selectively melts designated areas within this new layer, fusing it to the previously melted layer. This process continues iteratively until the entire 3D object is complete. | * Creates complex geometries in a step-wise manner * Enables efficient use of material, minimizing waste | * Build time can be longer compared to some other AM processes due to the layer-by-layer approach |
Heat Management and Build Platform | Thermal management plays a vital role in EBM. The build platform is typically preheated to a temperature slightly below the melting point of the powder to improve flowability and promote bonding. A water-cooled copper crucible further aids in heat dissipation and prevents warping of the final part. | * Minimizes thermal stresses and residual stress build-up * Contributes to dimensional accuracy and part quality | * Careful control of preheating temperature and cooling rates is necessary |
Part Removal and Post-Processing | Once the build process is complete, the chamber is brought back to atmospheric pressure. The built part remains adhered to the build platform and needs to be separated. Support structures, if any, are carefully removed using mechanical techniques. Depending on the application, post-processing steps like heat treatment, hot isostatic pressing, or machining may be employed to achieve the desired surface finish and mechanical properties. | * Minimizes post-processing steps due to high density and near-net-shape capabilities * Enables creation of functional parts | * Removal process requires care to avoid damaging delicate features * Heat treatment or other post-processing steps may add to overall processing time |
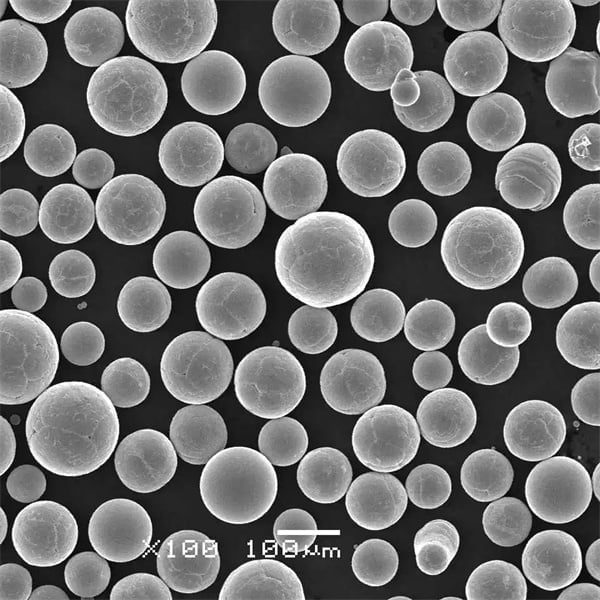
Key Specifications of electron beam melting machine
Specification | Description | Impact on Part Quality and Production |
---|---|---|
Beam Power (kW) | This refers to the total power output of the electron beam. | Higher beam power translates to faster melting speeds and increased throughput. It also allows for processing of thicker layers and denser materials. However, excessive power can lead to overheating and warping of the part. |
Build Envelope (mm) | This defines the maximum dimensions (length, width, height) of a part that can be manufactured in a single build. | A larger build envelope offers greater design flexibility for complex geometries. However, it also increases the machine footprint, powder consumption, and overall build time. |
Vacuum Level (Pa) | The pressure within the EBM chamber, crucial for preventing oxidation and contamination during the melting process. | A high vacuum (lower Pa value) ensures minimal interaction between the molten metal and atmospheric gases, resulting in parts with superior mechanical properties and high density. However, achieving and maintaining a deeper vacuum requires more powerful pumps, adding to the machine cost and complexity. |
Layer Thickness (μm) | The thickness of each individual layer of metal powder spread and melted during the build process. | Thinner layers offer finer detail and smoother surface finishes. However, they require more build time due to the increased number of layers needed. Conversely, thicker layers can be faster to build but may result in a rougher surface and potential internal porosity. |
Material Compatibility | The range of metal powders that the EBM system can process. | A wider material compatibility allows for the creation of parts from diverse alloys with specific properties suited for various applications. However, some materials have higher melting points or require specialized handling, which might limit machine options. |
In-Situ Monitoring | The ability to monitor the melting process in real-time using cameras or other sensors. | In-situ monitoring allows for early detection of defects like spatter or layer cracking, enabling corrective actions to be taken during the build. This can significantly improve yield and reduce the risk of part failure. |
Melt Pool Geometry Control | The level of precision with which the electron beam can be focused and manipulated to control the shape of the molten metal pool. | Precise melt pool control minimizes heat-affected zones and residual stresses, leading to parts with enhanced mechanical performance and fatigue resistance. This is particularly important for applications with high-stress requirements. |
Powder Recoating System | The mechanism used to deliver and spread fresh metal powder across the build platform after each layer is melted. | An efficient recoating system ensures consistent powder layer thickness and minimizes the risk of contamination from residual powder particles. Blade and roller-based systems are common, each with its own advantages and limitations. |
Support Generation Software | The software used to design and generate support structures within the 3D model. | Well-designed support structures are crucial for preventing part distortion and ensuring proper heat dissipation during the build. Advanced software can optimize support placement and minimize material waste. |
Post-Processing Requirements | The level of post-processing needed to achieve the desired final part properties. | EBM parts typically require minimal post-processing compared to other additive manufacturing techniques. However, support structure removal and surface finishing may still be necessary depending on the application. |
Economics of Electron Beam Melting Adoption
Factor | Impact on Adoption | Explanation |
---|---|---|
Capital Expenditure | High | EBM machines carry a hefty upfront cost, ranging from $500,000 to several million dollars depending on build volume and capabilities. This can be a significant barrier for smaller manufacturers or those new to additive manufacturing. |
Operational Costs | Mixed | While EBM offers advantages like reduced material waste and near-net-shape manufacturing, it also incurs costs for powder material, energy consumption (due to the high-powered electron beam), and potential post-processing like support removal. However, these costs can be offset by reduced machining needs and improved part performance. |
Part Complexity | Positive | EBM excels at creating complex, near-impossible geometries with internal channels and lattices. This unlocks design freedom for lightweight, high-strength components in aerospace, medical, and other industries. The ability to create intricate features can justify the higher costs associated with EBM. |
Production Volume | Limited | EBM machines have slower build rates compared to some other additive manufacturing technologies. This makes them less suitable for high-volume production runs. However, EBM shines in applications where customization, small batch sizes, and performance are paramount. |
Material Compatibility | Expanding | EBM can handle a wider range of materials than many other 3D printing processes, including reactive and refractory metals, some alloys, and even certain ceramics. This versatility opens doors for new applications in demanding environments. Continued development of compatible materials will further drive adoption. |
Labor & Expertise | Specialized | Operating and maintaining EBM machines requires skilled personnel with knowledge of vacuum systems, electron beam technology, and metal powder handling. The scarcity of such expertise can be a hurdle for some companies, impacting adoption rates. |
Return on Investment (ROI) | Long-term | The economic viability of EBM hinges on a long-term perspective. While upfront costs are high, the benefits of EBM (e.g., lighter, stronger parts, reduced waste) often translate to cost savings and performance improvements over a product’s lifecycle. |
Government Incentives | Positive | Government support for research and development in additive manufacturing, including EBM, can accelerate adoption by lowering barriers to entry and encouraging innovation. Tax breaks or grants can incentivize companies to invest in EBM technology. |
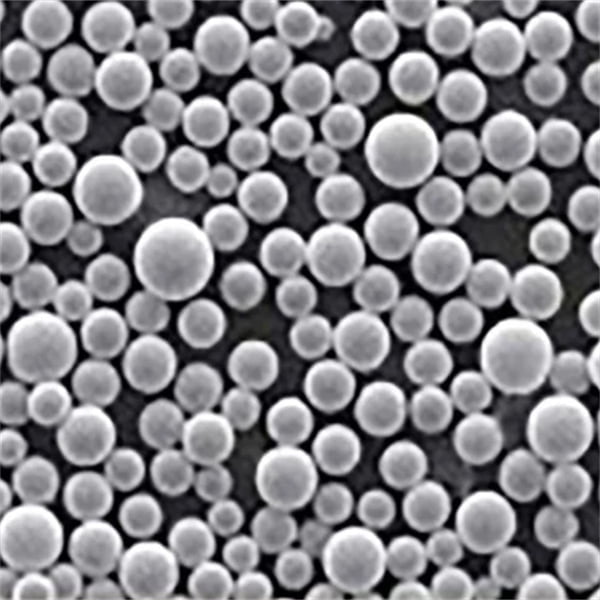
Popular Materials for EBM
Material Class | Alloy Examples | Properties | Applications |
---|---|---|---|
Titanium Alloys | Ti-6Al-4V, Ti-6Al-4V ELI | * Excellent strength-to-weight ratio * High biocompatibility * Corrosion resistant | * Aerospace components (wings, landing gear) * Medical implants (knee replacements, dental implants) * Sporting goods (golf clubs, bicycle frames) |
Nickel-Based Alloys | Inconel 625, Inconel 718 | * Exceptional high-temperature strength * Oxidation and corrosion resistance * Good weldability | * Turbine blades and discs for jet engines * Heat exchangers for chemical processing * Impeller shafts for pumps |
Cobalt-Chrome Alloys | CoCrMo, Haynes 214 | * High wear resistance * Biocompatible (limited applications) * Good hardness | * Joint replacements (hips, knees) * Cutting tools and wear parts * Dental implants (limited use due to potential chromium concerns) |
Stainless Steels | 17-4PH, 316L | * Good corrosion resistance * Moderate strength * Biocompatible (limited applications) | * Medical instruments * Chemical processing equipment * Food and beverage processing components |
Emerging Materials | * Tungsten (W) * Tantalum (Ta) * Niobium (Nb) * Molybdenum (Mo) | * Ultra-high melting points * Excellent high-temperature properties * Limited research and development | * Potential applications in aerospace, defense, and nuclear industries (due to high melting points and resistance to extreme environments) |
Benefits of Electron Beam Melting
Benefit | Description | Impact |
---|---|---|
High-Density, Near-Net-Shape Parts | EBM creates parts with a density exceeding 99.5% of the theoretical density of the metal powder used. This eliminates porosity (tiny air pockets) common in other additive manufacturing methods, resulting in parts with exceptional strength, fatigue resistance, and dimensional accuracy. | This enables the creation of functional metal components for demanding applications in aerospace (turbine blades, engine housings), medical (dental implants, prosthetics), and automotive (lightweight, high-performance parts) industries. |
Superior Mechanical Properties | The high-vacuum environment and precise melting process in EBM minimize oxidation and contamination, preserving the inherent properties of the metal powder. This translates to parts with excellent tensile strength, creep resistance (ability to withstand deformation under stress at high temperatures), and fracture toughness. | EBM-produced parts can handle significant loads, operate effectively at elevated temperatures, and resist crack propagation, making them ideal for applications requiring durability and structural integrity in harsh environments. |
Processing of Refractory and Reactive Metals | Unlike traditional manufacturing methods limited by high melting points and reactivity, EBM excels at processing challenging materials like titanium alloys, tantalum, and Inconel. The vacuum environment prevents oxidation and allows for precise control of the melting process, ensuring successful fabrication. | This broadens the design possibilities for industries like aerospace and biomedical, where components require exceptional strength-to-weight ratios, biocompatibility (compatibility with living tissue), and high-temperature performance. |
Design Freedom for Complex Geometries | EBM’s layer-by-layer approach allows for the creation of intricate internal features, channels, and lattice structures impossible with conventional techniques. This design flexibility optimizes weight distribution, improves heat transfer, and enables the creation of components with superior functionality. | This benefit revolutionizes product design in industries like aerospace, where lightweight, high-strength components with complex cooling channels are crucial for engine efficiency. It also allows for the creation of customized medical implants that perfectly match a patient’s anatomy. |
Minimal Support Structures | Due to the high inherent strength of EBM-produced parts, minimal support structures are needed during the build process. This reduces post-processing time and material waste, as well as the risk of support structure damage to the final component. | This translates to faster production times, lower overall costs, and the ability to create intricate geometries that would be difficult or impossible to support with traditional methods. |
Reduced Material Waste | EBM is an additive manufacturing process, meaning material is added layer-by-layer to create the desired shape. This minimizes material waste compared to subtractive techniques like machining, where a significant portion of the raw material is removed to achieve the final form. | This benefit promotes sustainability and reduces production costs by maximizing material utilization. Additionally, unused powder from the build chamber can often be reused for subsequent builds, further minimizing waste. |
Overview of electron beam melting machine Suppliers
A variety of established industrial manufacturers and specialized new entrants provide electron beam melting solutions scalable from research to high volume production across aerospace, medical, automotive, and industrial sectors.
Table 8: Leading Electron Beam Melting System Manufacturers
Supplier | Details | Target Segments |
---|---|---|
GE Additive | Pioneered EBM technology | Aerospace, medical, automotive |
Sciaky | Largest envelope size | Aerospace structures |
Wayland Additive | Budget metal AM platforms | Small machine shops |
JEOL | Research grade EBM systems | Universities |
Nano Dimension | Multi-material capabilities | Electronics, defense |
Industry leader Arcam EBM, now part of GE Additive, established early leadership thanks to patented solutions and continues dominating the established medical implant and aerospace categories.
Meanwhile, new entrants like Wayland aim to expand adoption by targeting small and medium manufacturers with economical starting platforms.
Collaborations on materials, part qualification, and machine optimization between producers, researchers, and end-user groups will ultimately expand EBM penetration across further critical applications.
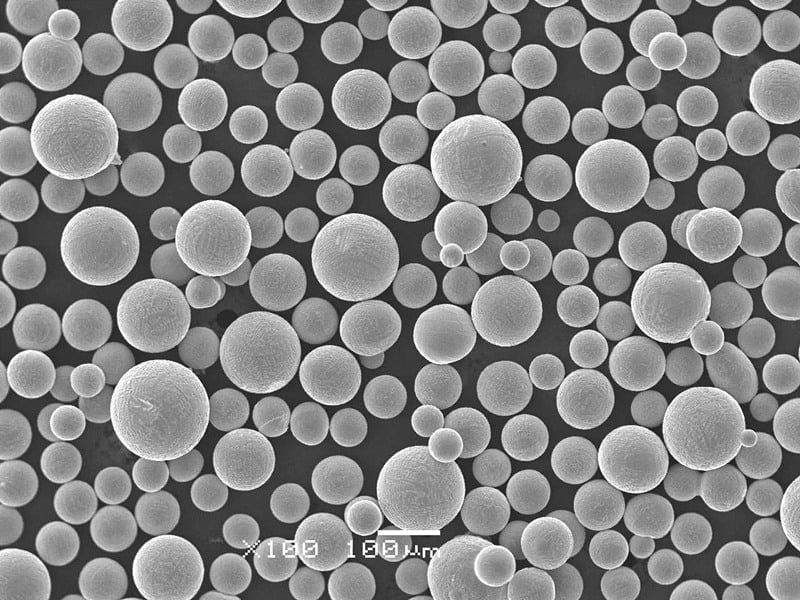
Future Outlook for Electron Beam Melting Adoption
Propelled by superior production speed capabilities plus exceptional mechanical properties impossible with other metal additive or conventional process, EBM adoption appears positioned for massive expansion across aerospace, medical device, automotive, and industrial categories over the next 5-7 years.
Broader awareness of EBM benefits beyond prototyping into full-scale production is expected to drive equipment investments as organizations leverage 3D printing to reshape supply chains.
Larger build envelopes now commercially accessible also enable consolidation of assemblies into fewer components, further optimizing inventory logistics and lead times.
However, declines in system costs combined with increased materials availability must continue improving smaller manufacturers’ access to EBM technology. Streamlining ancillary powder handling tools and post-processing workflows will also simplify adoption.
Overall, EBM sustains strong momentum to penetrate an increasingly wider range of production applications thanks to unmatched deposition rates and exceptional resultant material properties relative to alternate metal additive or legacy fabrication processes.
FAQ
Q: What facility infrastructure is needed to support EBM?
A: Expect 500+ sq. ft for the machine itself, with more space for powder handling stations and post-processing. Concrete floor reinforcement for 12,000+ lb equipment loads is typical.
Q: How many operators per EBM machine are required?
A: One technician can support several EBM units depending on automation level and production volumes. Additional staff handles powder operations, post-processing tasks, maintenance, and engineering.
Q: What materials cannot be processed with EBM technology?
A: Non-conductive polymers cannot be processed with electron beams. But EBM accommodates practically any conductive metal alloy system otherwise manufacturable.
Q: What safety risks are associated with EBM technology?
A: High power electron beam voltages pose arc flash risks requiring proper enclosures and controls. Reactive metal powder exposure also requires protocols for fire and inhalation dangers necessitating protective equipment and training.
Q: Does EBM require any secondary heat treatment?
A: Certain alloys benefit from heat treatment to further enhance microstructures and tailor mechanical properties. However, the rapid solidification cycles and high pre-heat temperatures intrinsic to the EBM process typically eliminate these post-processing steps.
Share On
MET3DP Technology Co., LTD is a leading provider of additive manufacturing solutions headquartered in Qingdao, China. Our company specializes in 3D printing equipment and high-performance metal powders for industrial applications.
Inquiry to get best price and customized Solution for your business!
Related Articles
About Met3DP
Recent Update
Our Product
CONTACT US
Any questions? Send us message now! We’ll serve your request with a whole team after receiving your message.
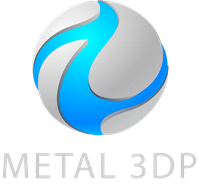
Metal Powders for 3D Printing and Additive Manufacturing