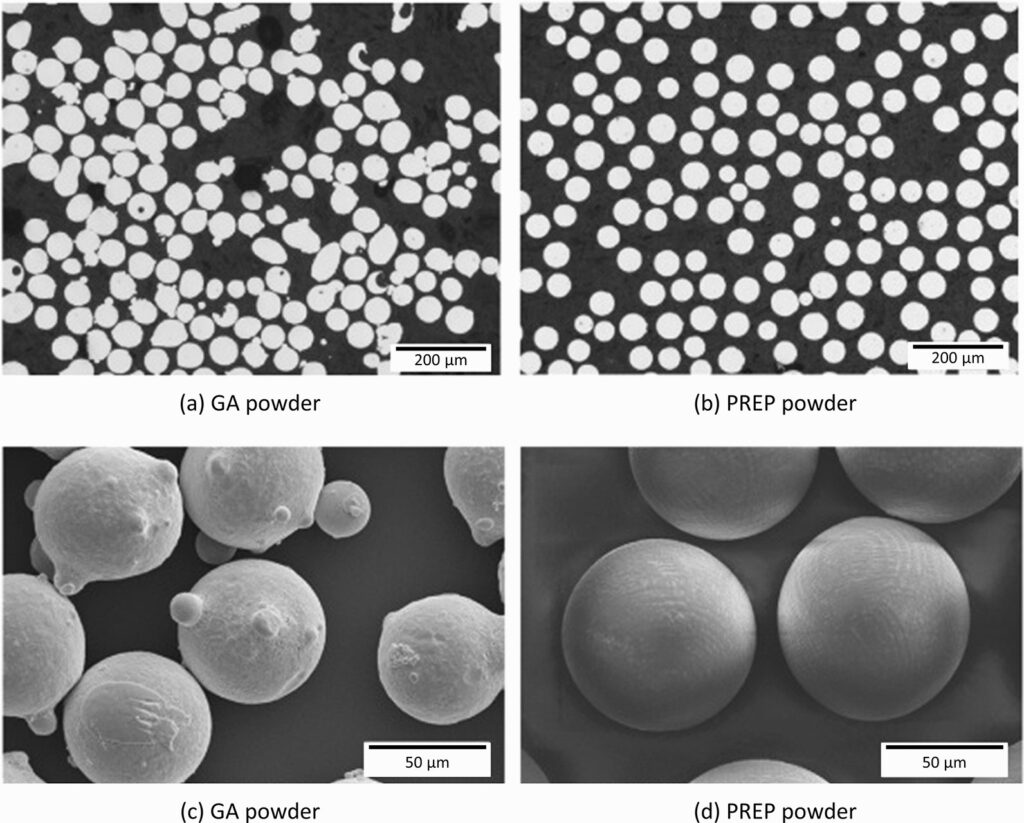
Fe-Co-Ni-Cr-Mn HEA Spherical Powder: Exceptional Toughness for Extreme Environments
Low MOQ
Provide low minimum order quantity to meet different needs.
OEM & ODM
Provide customized products and design services to meet unique customer needs.
Adequate Stock
Ensure fast order processing and provide reliable and efficient service.
Customer Satisfaction
Provide high quality products with customer satisfaction at the core.
share this article
Table of Contents
In the fast-evolving world of materials science, the Fe-Co-Ni-Cr-Mn HEA Spherical Powder has caught the attention of industries ranging from aerospace to automotive to additive manufacturing. This High Entropy Alloy (HEA) powder is celebrated for its unique chemical composition and impressive mechanical properties, which make it a versatile choice for demanding applications.
But what exactly makes Fe-Co-Ni-Cr-Mn HEA Spherical Powder stand out from traditional alloys? What are its main benefits and shortcomings, and how does it perform in real-world applications? Whether you’re an engineer, a researcher, or an industry professional, this guide will walk you through everything you need to know about this fascinating material.
Overview: What is Fe-Co-Ni-Cr-Mn HEA Spherical Powder?
Fe-Co-Ni-Cr-Mn HEA Spherical Powder represents a new class of alloys known as High Entropy Alloys (HEAs). Unlike conventional alloys, which are often dominated by one or two base elements, HEAs consist of five or more principal elements in near-equal proportions. In the case of Fe-Co-Ni-Cr-Mn, the alloy is composed primarily of iron (Fe), cobalt (Co), nickel (Ni), chromium (Cr), and manganese (Mn).
This unique balanced composition gives HEAs their distinct properties, such as:
- High strength and durability across a wide range of temperatures.
- Outstanding corrosion and oxidation resistance.
- Exceptional wear resistance, making it ideal for high-stress environments.
- Spherical powder shape, which provides superior flowability and packing density, especially important in additive manufacturing processes.
The spherical shape of the particles is crucial in many industrial applications, particularly in 3D printing and metal injection molding. The improved flow properties of spherical powders result in smoother, more consistent layers during the manufacturing process, which is crucial for achieving high-quality finished parts.
Composition, Properties, and Key Characteristics of Fe-Co-Ni-Cr-Mn HEA Spherical Powder
The key to understanding the performance of Fe-Co-Ni-Cr-Mn HEA Spherical Powder lies in its chemical composition and physical properties. The combination of five principal elements in near-equal proportions contributes to its unique mechanical properties, making it ideal for various demanding applications.
Chemical Composition of Fe-Co-Ni-Cr-Mn HEA Spherical Powder
Here’s a breakdown of the typical chemical composition for Fe-Co-Ni-Cr-Mn HEA Spherical Powder:
Element | Percentage (%) | Role in Alloy |
---|---|---|
Iron (Fe) | 20% – 25% | Provides structural strength and magnetic properties |
Cobalt (Co) | 20% – 25% | Enhances strength, magnetic properties, and toughness |
Nickel (Ni) | 20% – 25% | Improves corrosion resistance and thermal stability |
Chromium (Cr) | 15% – 20% | Increases corrosion and oxidation resistance |
Manganese (Mn) | 10% – 15% | Contributes to toughness and wear resistance |
This balanced composition results in a material that is strong, corrosion-resistant, and stable over a wide temperature range.
Physical and Mechanical Properties of Fe-Co-Ni-Cr-Mn HEA Spherical Powder
Below is a table that outlines some of the key properties of Fe-Co-Ni-Cr-Mn HEA Spherical Powder:
Property | Typical Range |
---|---|
Density | 7.5 – 8.0 g/cm³ |
Melting Point | 1,400 – 1,600°C |
Hardness (HRC) | 30 – 50 HRC (depending on heat treatment) |
Tensile Strength | 800 – 1,200 MPa |
Thermal Conductivity | 15 – 25 W/m·K |
Oxidation Resistance | Excellent up to 1,200°C |
Magnetic Properties | Strongly ferromagnetic, especially due to Fe and Co |
Corrosion Resistance | High, suitable for harsh environments |
Key Characteristics
- High-Temperature Strength: The alloy maintains its mechanical properties even at high temperatures, making it well-suited for applications such as jet engines and power turbines.
- Oxidation Resistance: Thanks to chromium and manganese, the powder offers excellent oxidation resistance, even in extreme temperatures.
- Magnetic Properties: The combination of iron, cobalt, and nickel makes this alloy highly ferromagnetic, which is important for applications like electric motors and magnetic sensors.
- Wear Resistance: The addition of manganese enhances the alloy’s wear resistance, making it ideal for applications requiring durability, such as tooling and industrial machinery.
- Corrosion Resistance: Its high chromium content ensures outstanding corrosion resistance, especially in oxidative environments, making it a good choice for environments exposed to moisture or chemicals.
Applications of Fe-Co-Ni-Cr-Mn HEA Spherical Powder
The unique properties of Fe-Co-Ni-Cr-Mn HEA Spherical Powder make it suitable for a wide range of industries. Its combination of high strength, oxidation resistance, and wear resistance means it can perform well in extreme environments where other materials might fail.
Common Applications for Fe-Co-Ni-Cr-Mn HEA Spherical Powder
Industry | Application |
---|---|
Aerospace | High-temperature turbine blades, heat-resistant components |
Automotive | High-performance engine parts, exhaust systems, turbochargers |
Power Generation | Gas turbines, steam turbines, nuclear reactors |
Additive Manufacturing | 3D printing of complex, high-strength parts |
Magnetic Applications | Magnetic sensors, actuators, electric motors |
Tooling and Dies | High-strength, wear-resistant tools and molds |
Medical Devices | Durable surgical tools, prosthetics, and implants |
Why Fe-Co-Ni-Cr-Mn HEA for Additive Manufacturing?
In the field of additive manufacturing (particularly 3D printing), Fe-Co-Ni-Cr-Mn HEA Spherical Powder has emerged as a top choice for creating high-performance parts. Its spherical shape ensures optimal flowability and layering, which are critical for producing high-precision components. Additionally, its high strength and corrosion resistance make it ideal for parts that will be exposed to extreme heat or chemical environments.
One of the main reasons why this powder is favored in additive manufacturing is its ability to create intricate designs while maintaining excellent material properties. Whether you’re printing a part for a jet engine or a medical implant, this alloy offers the reliability and durability needed for long-term performance.
Specifications, Sizes, and Standards for Fe-Co-Ni-Cr-Mn HEA Spherical Powder
When choosing Fe-Co-Ni-Cr-Mn HEA Spherical Powder for a specific application, knowing the available specifications, sizes, and industry standards is critical. This ensures that the material will meet the necessary performance requirements for your project.
Specifications for Fe-Co-Ni-Cr-Mn HEA Spherical Powder
Specification | Details |
---|---|
Particle Size Range | 15 – 53 μm (common for additive manufacturing) |
Purity | ≥ 99.5% |
Bulk Density | 4.5 – 6.0 g/cm³ (varies by particle size) |
Flow Rate (Hall Flow) | 20 – 35 s/50g |
Oxygen Content | ≤ 0.02% |
Packaging | Available in 1 kg, 5 kg, 10 kg, and bulk quantities |
Certification | ISO 9001, ASTM F3302 (Additive Manufacturing) |
Sizes of Fe-Co-Ni-Cr-Mn HEA Spherical Powder
The particle size of the powder can have a significant impact on its performance in various manufacturing processes. Smaller particles are typically preferred for higher precision applications, while larger particles may be used for faster build times or larger parts.
Particle Size | Application |
---|---|
15 – 30 μm | High-precision 3D printing and fine details |
30 – 45 μm | General 3D printing, metal injection molding |
45 – 53 μm | Faster build speeds, larger parts with less intricate detail |
Industry Standards for Fe-Co-Ni-Cr-Mn HEA Spherical Powder
To ensure the quality and consistency of the powder, it’s important that the material adheres to recognized industry standards. Here are some of the key standards applicable to Fe-Co-Ni-Cr-Mn HEA Spherical Powder:
- ISO 9001: Certification for quality management systems.
- ASTM F3302: Standard for additive manufacturing feedstock materials.
- AMS 4998: Aerospace material specification for high-performance alloys.
By adhering to these standards, manufacturers ensure that the powder performs reliably across various applications, from aerospace components to medical devices.
Suppliers and Pricing for Fe-Co-Ni-Cr-Mn HEA Spherical Powder
The cost of Fe-Co-Ni-Cr-Mn HEA Spherical Powder can vary based on a range of factors, including the particle size, purity, and supplier reputation. Generally, HEA powders are more expensive than traditional alloys due to their complex composition and the precision required in their production.
Top Suppliers and Pricing for Fe-Co-Ni-Cr-Mn HEA Spherical Powder
Supplier | Product Description | Price per kg (USD) | Comments |
---|---|---|---|
Höganäs AB | Fe-Co-Ni-Cr-Mn HEA powder, 15-45 μm | $350 – $550 | High-purity powder, ideal for additive manufacturing |
GKN Additive | HEA spherical powder for AM, 20-53 μm | $400 – $600 | Premium quality for high-stress applications |
Carpenter Additive | Fe-Co-Ni-Cr-Mn alloy powder, spherical, 25-50 μm | $375 – $575 | Suitable for metal injection molding and 3D printing |
Sandvik Osprey | HEA powder, spherical, 30-45 μm | $380 – $620 | High-performance powder for industrial applications |
Tekna Advanced Materials | Fe-Co-Ni-Cr-Mn HEA spherical powder, 20-53 μm | $400 – $650 | Suitable for high-temperature and high-wear parts |
Factors Affecting Pricing
Several factors can influence the price of Fe-Co-Ni-Cr-Mn HEA Spherical Powder, such as:
- Particle Size: Smaller particles are typically more expensive due to the extra processing required to achieve fine powder sizes.
- Purity: Higher purity powders (≥ 99.5%) are more costly but necessary for demanding applications like aerospace and medical devices.
- Order Quantity: Bulk purchases may come with discounts, lowering the price per kilogram.
- Supplier Reputation: Established suppliers with a strong track record of quality may charge more than lesser-known vendors.
Advantages and Limitations of Fe-Co-Ni-Cr-Mn HEA Spherical Powder
Like any material, Fe-Co-Ni-Cr-Mn HEA Spherical Powder has its advantages and limitations. Understanding these can help you determine whether it’s the right material for your project.
Advantages of Fe-Co-Ni-Cr-Mn HEA Spherical Powder
Advantages | Details |
---|---|
High-Temperature Strength | Excellent mechanical properties at extreme temperatures, ideal for aerospace and power generation. |
Oxidation Resistance | Highly resistant to oxidation at temperatures up to 1,200°C, suitable for high-heat applications. |
Magnetic Properties | Strong ferromagnetic properties due to Fe-Co-Ni content, useful in electric motors and magnetic sensors. |
Wear Resistance | Excellent wear resistance, making it ideal for tooling and industrial machinery. |
Corrosion Resistance | High resistance to corrosion, especially in oxidizing environments. |
Versatility | Can be used across a wide range of industries, from additive manufacturing to medical devices. |
Limitations of Fe-Co-Ni-Cr-Mn HEA Spherical Powder
Limitations | Details |
---|---|
Cost | Generally more expensive than traditional alloys due to its complex composition and precision manufacturing requirements. |
Processing Complexity | May require specialized equipment for additive manufacturing and metal injection molding. |
Limited Availability | Not as widely available as conventional alloys, leading to potential longer lead times. |
Post-Processing Requirements | Heat treatment or surface finishing may be necessary to achieve the desired mechanical properties. |
FAQs About Fe-Co-Ni-Cr-Mn HEA Spherical Powder
Frequently Asked Questions
Question | Answer |
---|---|
What does HEA stand for in Fe-Co-Ni-Cr-Mn HEA powder? | HEA stands for High Entropy Alloy, which refers to alloys with five or more main elements in near-equal proportions. |
What industries use Fe-Co-Ni-Cr-Mn HEA powder? | Common industries include aerospace, automotive, power generation, additive manufacturing, and medical devices. |
Is Fe-Co-Ni-Cr-Mn HEA powder suitable for 3D printing? | Yes, its spherical shape and flowability make it ideal for additive manufacturing processes like 3D printing. |
How does Fe-Co-Ni-Cr-Mn HEA compare to traditional steel alloys? | It offers better high-temperature strength, oxidation resistance, and magnetic properties than traditional steel alloys. |
What particle size is best for additive manufacturing? | For 3D printing, a particle size range of 15-45 μm is typically ideal. |
Is Fe-Co-Ni-Cr-Mn HEA powder magnetic? | Yes, due to its cobalt, nickel, and iron content, Fe-Co-Ni-Cr-Mn HEA is strongly ferromagnetic. |
What are the main advantages of Fe-Co-Ni-Cr-Mn HEA powder? | Its high strength, wear resistance, oxidation resistance, and corrosion resistance make it suitable for extreme environments. |
Conclusion: Why Fe-Co-Ni-Cr-Mn HEA Spherical Powder is the Future of Advanced Manufacturing
In conclusion, Fe-Co-Ni-Cr-Mn HEA Spherical Powder is a high-performance material that offers unmatched strength, wear resistance, and oxidation resistance. Its unique composition and spherical shape make it ideal for a wide range of industries, including aerospace, automotive, power generation, and additive manufacturing.
While it may come at a higher cost than traditional alloys, the long-term benefits—including durability, performance, and versatility—make it a worthwhile investment for industries that demand the best. Whether you’re looking to 3D print complex parts or create components for high-stress environments, Fe-Co-Ni-Cr-Mn HEA Spherical Powder is a material that can meet your needs.
Ready to elevate your next project with Fe-Co-Ni-Cr-Mn HEA Spherical Powder?
Get Latest Price
About Met3DP
Product Category
HOT SALE
CONTACT US
Any questions? Send us message now! We’ll serve your request with a whole team after receiving your message.
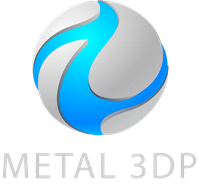
Metal Powders for 3D Printing and Additive Manufacturing
COMPANY
PRODUCT
cONTACT INFO
- Qingdao City, Shandong, China
- [email protected]
- [email protected]
- +86 19116340731