Gas Atomization Metal Powder: Revolutionizing Manufacturing with Tiny Particles
Table of Contents
Imagine a world where intricate metal parts are built layer by layer, not sculpted from solid blocks. This is the reality of additive manufacturing, and gas atomized metal powder is the magic dust that makes it possible. In this comprehensive guide, we’ll delve into the fascinating world of these tiny metallic particles, exploring their creation, properties, applications, and specific models that fuel innovation across various industries.
What is Gas Atomization Metal Powder?
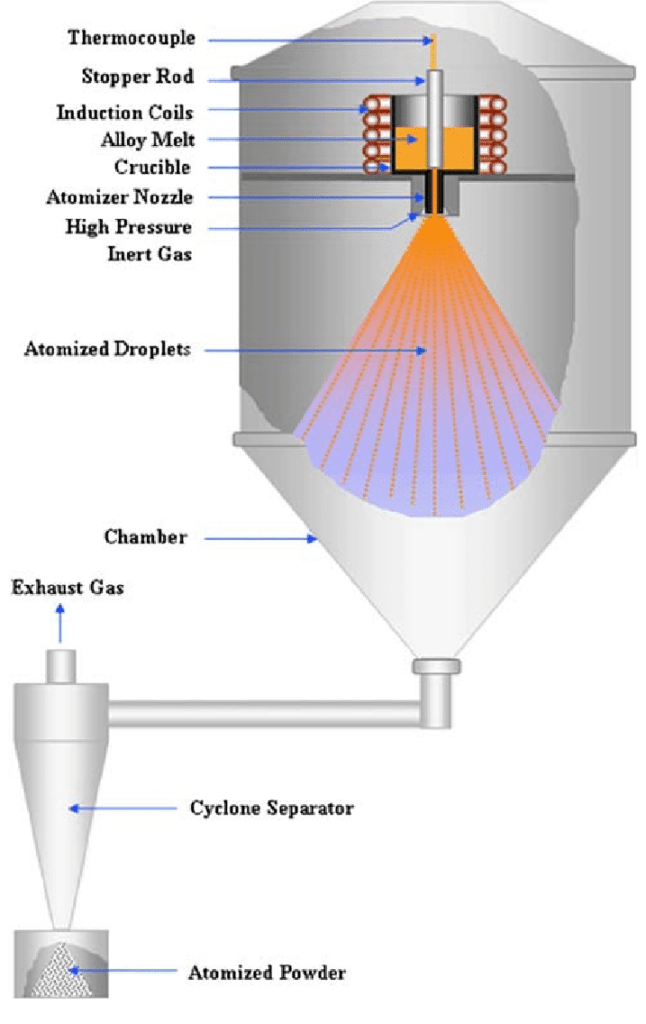
Gas atomized metal powder is a collection of spherical or near-spherical metal particles produced through a process called gas atomization. It involves melting the desired metal and then disintegrating the molten stream into fine droplets using a high-pressure gas jet. These rapidly solidified droplets cool and solidify mid-air, forming the free-flowing, high-quality metal powder we utilize in various applications.
Think of it like this: Imagine pouring molten chocolate onto a cold surface to create chocolate chips. Gas atomization operates on a similar principle, except at a much higher pressure and with various metals instead of chocolate.
Key Properties of Gas Atomization Metal Powder
The unique production process of gas atomization imparts several crucial properties to the resulting metal powders:
Property | Description & Significance |
---|---|
Spherical or near-spherical shape | Ensures optimal flowability, packing density, and printability in additive manufacturing processes. |
Fine particle size | Allows for high resolution and intricate details in 3D printed parts. |
High purity | Minimizes impurities and contamination, leading to stronger and more consistent final products. |
Excellent surface quality | Promotes good adhesion between powder particles during the 3D printing process. |
Tailorable properties | Different processing parameters can be adjusted to achieve specific desired properties, such as particle size and microstructure. |
These properties make gas atomized metal powders the ideal choice for various applications, particularly in additive manufacturing (3D printing), metal injection molding (MIM), and powder metallurgy (PM).
Applications of Gas Atomization Metal Powder
Gas atomized metal powders have revolutionized numerous industries by facilitating the creation of complex and intricate metal parts with unprecedented precision and flexibility. Here’s a glimpse into the diverse applications of these remarkable materials:
Industry | Applications |
---|---|
Aerospace | Lightweight, high-strength components for aircraft, satellites, and rocket engines. |
Automotive | Complex engine parts, gears, and lightweight body components. |
Medical | Biocompatible implants, custom prosthetics, and dental devices. |
Consumer Goods | Jewelry, sports equipment, and electronics components. |
Tooling | Intricate cutting tools and molds with improved wear resistance. |
The potential applications of gas atomized metal powders continue to expand, pushing the boundaries of design and manufacturing across various sectors.
Models of Gas Atomization Metal Powder
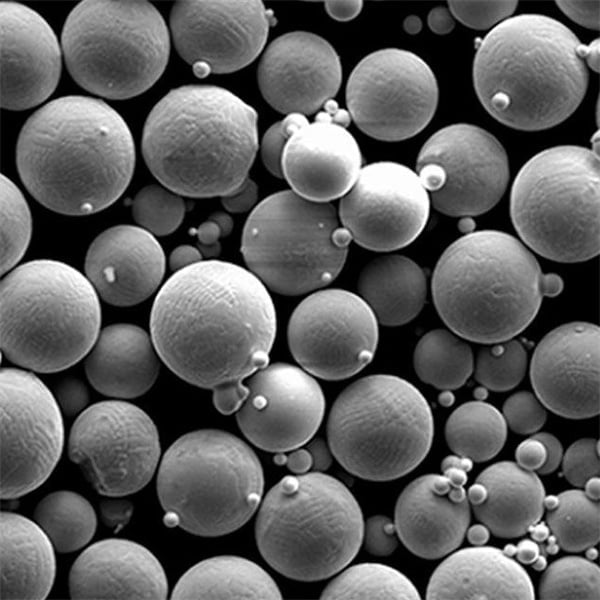
The world of gas atomized metal powders boasts a diverse range of materials, each with unique properties and applications. Here are ten prominent examples:
- 316L Stainless Steel: A versatile and widely used austenitic stainless steel powder known for its excellent corrosion resistance and weldability.
- Titanium (Ti-6Al-4V): A high-strength, low-weight titanium alloy powder commonly used in aerospace and medical applications due to its biocompatibility.
- Inconel 625: A superalloy powder known for its exceptional high-temperature strength and oxidation resistance, ideal for jet engine components and other demanding environments.
- Aluminum (AlSi10Mg): A popular aluminum alloy powder offering a good balance of strength, ductility, and castability, often used in automotive and aerospace applications.
- Nickel (Ni): A pure nickel powder valued for its excellent electrical conductivity and corrosion resistance, used in electronics and battery applications.
- Copper (Cu): A pure copper powder offering high electrical and thermal conductivity, often used in electrical components and heat sinks.
- Cobalt-Chrome (CoCr): A biocompatible alloy powder commonly used in the production of hip implants and other medical devices due to its wear resistance and strength.
- Tool Steel: Various tool steel powders exist, each tailored for specific cutting tool applications, offering exceptional wear resistance and hardness.
- Tungsten Carbide (WC): A hard and wear-resistant powder used in drill bits, cutting tools, and other applications requiring high abrasion resistance.
- Precious Metals: Gold, silver, and other precious metal powders are used in jewelry, electronics, and other.
Comparing and Contrasting Popular Gas Atomization Metal Powder
While all gas atomized metal powders share some key properties, specific materials offer distinct advantages and disadvantages based on their composition and properties. Here’s a comparative analysis of some popular choices:
Feature | 316L Stainless Steel | Titanium (Ti-6Al-4V) | Inconel 625 | Aluminum (AlSi10Mg) |
---|---|---|---|---|
Strength | Moderate | High | Very high | Moderate |
Weight | Moderate | Low | High | Low |
Corrosion Resistance | Excellent | Good | Excellent | Moderate |
Biocompatibility | No | Yes | No | No |
Cost | Moderate | High | Very high | Low |
Applications | General-purpose components, medical devices | Aerospace, medical | High-temperature environments | Automotive, aerospace |
Choosing the right material:
This table highlights the trade-offs between different metal powders. For instance, 316L stainless steel offers a good balance of properties at a moderate cost, making it suitable for various applications. However, if weight is critical, titanium becomes a compelling choice despite its higher cost. Similarly, Inconel 625 reigns supreme in high-temperature environments but comes at a premium price.
Beyond the table:
- Nickel and copper: These pure metal powders excel in specific applications requiring high electrical conductivity (electronics, heat sinks) but may not be suitable for structural components due to their lower strength.
- Cobalt-chrome and tool steel: These specialized powders cater to specific needs, such as wear resistance in medical implants (cobalt-chrome) or cutting tools (tool steel).
- Precious metals: While not commonly used in large volumes due to their higher cost, precious metal powders offer unique properties like excellent conductivity and aesthetics for specific applications in jewelry, electronics, and specialized industrial uses.
Remember: Selecting the optimal gas atomized metal powder requires careful consideration of the desired properties, application requirements, and cost constraints.
Demystifying the Details: Specifications, Sizes, Grades, and Standards
Gas atomized metal powders are available in various specifications, sizes, grades, and standards to cater to diverse manufacturing needs. Understanding these parameters is crucial for selecting the appropriate powder for your project.
Key specifications:
- Chemical composition: Refers to the specific elements and their percentages in the powder.
- Particle size distribution: Indicates the range of particle sizes present in the powder, influencing flowability, packing density, and final product properties.
- Apparent density: Measures the bulk density of the powder, impacting powder handling and storage.
- Flowability: Describes how easily the powder flows, affecting its suitability for specific manufacturing processes.
Size variations:
Gas atomized metal powders typically range in size from 10 micrometers to 150 micrometers, with some powders reaching even smaller or larger sizes for specialized applications. Selecting the appropriate size depends on the desired part features and the specific 3D printing or other manufacturing technique employed.
Understanding grades:
Similar to other materials, gas atomized metal powders come in various grades based on their purity, oxygen content, and other factors. Choosing the appropriate grade ensures the final product meets the desired mechanical properties and performance requirements.
Meeting the standards:
Several industry standards govern the production and quality control of gas atomized metal powders. These standards ensure consistency, safety, and reliable performance of the materials. Common standards include ASTM International (ASTM) and the International Organization for Standardization (ISO) specifications.
Navigating the options:
Suppliers typically provide detailed specifications and data sheets for their gas atomized metal powders. Consulting these resources and collaborating with experienced professionals in the field can guide you in selecting the most suitable powder for your specific needs.
Finding the Right Fit: Suppliers and Pricing
The global market for gas atomized metal powders boasts numerous established and emerging suppliers offering a diverse range of materials and specifications. Here’s an overview of navigating the supplier landscape and pricing considerations:
Major suppliers:
- MET3DP (China)
- Höganäs AB (Sweden)
- AMETEK Engineered Materials (USA)
- LPW Technology Ltd (UK)
- SLM Solutions GmbH (Germany)
Pricing considerations:
- Material: The cost of the raw metal significantly influences the final price of the powder. Precious metals like gold and platinum naturally command a higher price compared to common metals like aluminum.
- Processing parameters: Specific processing techniques and control measures employed during atomization can impact the final cost.
- Quantity: Purchasing larger quantities often translates to lower per-unit costs due to economies of scale.
It’s advisable to compare offerings from multiple reputable suppliers, considering factors like material selection, desired specifications, pricing, delivery timelines, and customer support. Online marketplaces and industry publications can serve as valuable resources for researching potential suppliers and comparing their offerings.
Addressing Common Concerns: FAQ about Gas Atomization Metal Powder
Here are some frequently asked questions (FAQs) regarding gas atomized metal powders:
Q: What are the advantages of using gas atomized metal powders compared to traditional manufacturing methods?
A: Gas atomized metal powders offer several advantages, including:
- Design freedom: Enables the creation of complex geometries and intricate features not achievable with traditional techniques.
- Lightweight structures: Allows for the production of lightweight components with high strength-to-weight ratios, crucial in various industries like aerospace.
- Reduced waste: Minimizes material waste compared to subtractive manufacturing methods.
- Mass customization: Enables the production of customized parts in small batches, ideal for prototyping and niche applications.
Q: What are the limitations of using gas atomized metal powders?
A: Some limitations to consider include:
- Cost: Gas atomized metal powders can be more expensive than traditional materials, especially for high-performance alloys and precious metals.
- Surface roughness: 3D printed parts from metal powders may exhibit a slightly rougher surface finish compared to machined components, though post-processing techniques can improve surface quality.
- Limited material selection: While the range of available powders is expanding, it may not encompass all desired materials compared to traditional options.
Q: How is the environmental impact of gas atomized metal powders compared to traditional manufacturing methods?
A: The environmental impact of gas atomization is a complex issue with ongoing research. While the process can be energy-intensive, it can also offer potential benefits like reduced material waste and lower energy consumption compared to traditional machining methods that generate significant scrap. Responsible sourcing of raw materials and implementing sustainable practices throughout the supply chain are crucial for minimizing the environmental footprint of gas atomized metal powders.
The future of gas atomization:
Gas atomization technology is constantly evolving, with advancements in process control, powder characteristics, and the development of novel materials pushing the boundaries of what’s possible. As the technology matures and production costs become more competitive, gas atomized metal powders are poised to play an increasingly significant role in shaping the future of manufacturing across various industries.
Share On
MET3DP Technology Co., LTD is a leading provider of additive manufacturing solutions headquartered in Qingdao, China. Our company specializes in 3D printing equipment and high-performance metal powders for industrial applications.
Inquiry to get best price and customized Solution for your business!
Related Articles
About Met3DP
Recent Update
Our Product
CONTACT US
Any questions? Send us message now! We’ll serve your request with a whole team after receiving your message.
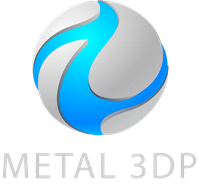
Metal Powders for 3D Printing and Additive Manufacturing
COMPANY
PRODUCT
cONTACT INFO
- Qingdao City, Shandong, China
- [email protected]
- [email protected]
- +86 19116340731