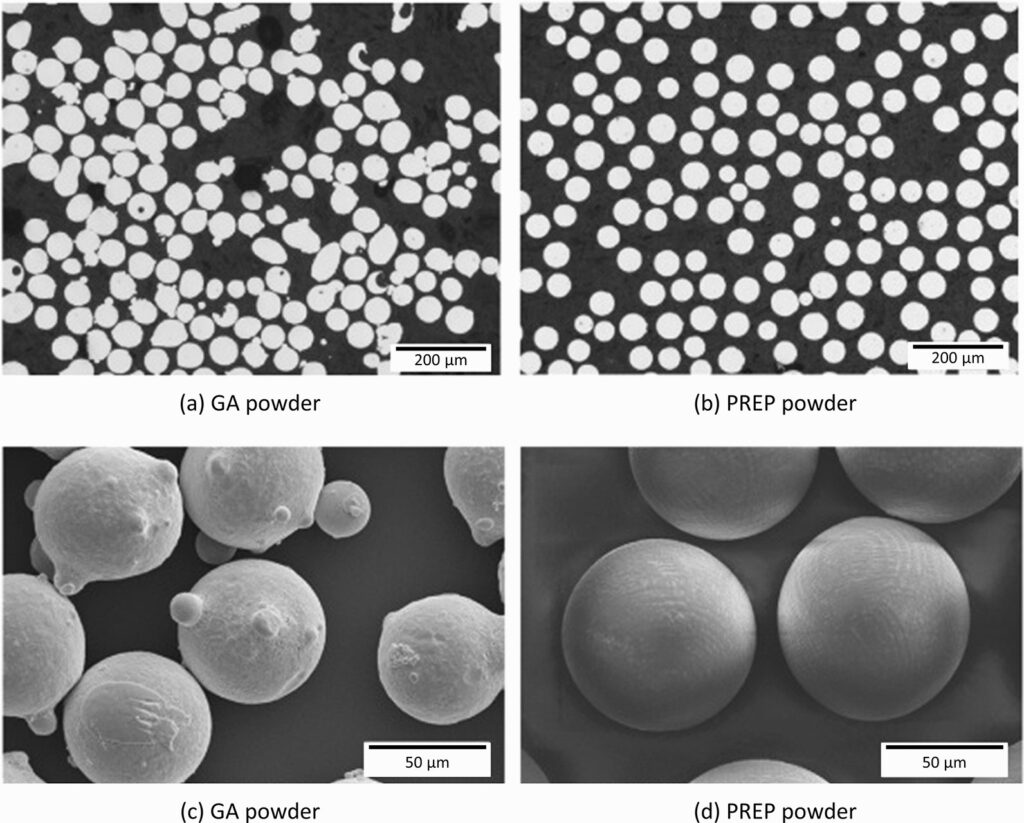
H13 Spherical Stainless Steel Alloy Powder: The Perfect Choice for High-Temperature Applications
Low MOQ
Provide low minimum order quantity to meet different needs.
OEM & ODM
Provide customized products and design services to meet unique customer needs.
Adequate Stock
Ensure fast order processing and provide reliable and efficient service.
Customer Satisfaction
Provide high quality products with customer satisfaction at the core.
share this article
Table of Contents
Overview of H13 Spherical Stainless Steel Alloy Powder
If you’re venturing into the world of metal powders, particularly for additive manufacturing (3D printing), H13 Spherical Stainless Steel Alloy Powder is a material you need to know about. It’s an ideal choice for applications where wear resistance, toughness, and thermal stability are crucial. Known for its versatility, H13 is widely used across industries like aerospace, automotive, and tooling thanks to its unique set of properties.
In this extensive guide, we’ll dive deep into the composition, properties, applications, and much more about H13 Spherical Stainless Steel Alloy Powder. Whether you’re a manufacturer looking to optimize your processes or an engineer exploring the best materials for high-temperature applications, this guide will provide the insight you need.
So, why is H13 stainless steel powder such a popular choice? It’s simple: reliability. This alloy offers a high strength-to-weight ratio, excellent thermal fatigue resistance, and is capable of withstanding extreme heat while maintaining its hardness. Plus, its spherical shape makes it perfect for powder metallurgy and 3D printing, ensuring a smooth production process and uniform part quality.
Key Details at a Glance
- Material: H13 Spherical Stainless Steel Alloy Powder
- Primary Uses: Tooling, aerospace, automotive, additive manufacturing
- Key Properties: High thermal stability, wear resistance, toughness
- Best Applications: High-temperature environments, tooling, molds
In the sections below, we’ll break down everything from the composition of H13 to its unique properties, applications, and even pricing. Let’s get started by understanding the composition that makes this alloy stand out.
Composition and Key Properties of H13 Spherical Stainless Steel Alloy Powder
The composition of H13 is what gives it its distinctive properties. Classified as a chromium hot-work tool steel, this alloy is specifically engineered to handle high temperatures and extreme thermal cycling. The spherical form of the powder makes it especially useful in processes like additive manufacturing, where flowability and consistency are critical.
Composition of H13 Spherical Stainless Steel Alloy Powder
Element | Percentage Composition |
---|---|
Carbon (C) | 0.32-0.45% |
Chromium (Cr) | 4.75-5.50% |
Molybdenum (Mo) | 1.10-1.75% |
Vanadium (V) | 0.80-1.20% |
Silicon (Si) | 0.80-1.20% |
Manganese (Mn) | 0.20-0.50% |
Phosphorus (P) | Max 0.030% |
Sulfur (S) | Max 0.030% |
This balanced mix of carbon, chromium, molybdenum, and vanadium provides the alloy with its hardness, toughness, and thermal stability. The addition of chromium ensures oxidation resistance, while vanadium enhances wear resistance—both critical for high-stress environments.
Key Properties of H13 Spherical Stainless Steel Alloy Powder
Property | Value |
---|---|
Density | 7.80 g/cm³ |
Hardness | 50-54 HRC |
Tensile Strength | ~1500 MPa |
Yield Strength | ~1300 MPa |
Thermal Conductivity | 28.6 W/m·K |
Melting Point | ~1426°C |
Thermal Fatigue Resistance | Excellent |
Creep Resistance | High |
Oxidation Resistance | High |
Why These Properties Matter
- Hardness and Wear Resistance: With a hardness range of 50-54 HRC, H13 is incredibly resistant to abrasion and wear, making it ideal for tooling and mold-making.
- Thermal Stability: One of the standout features of H13 is its ability to maintain its strength and hardness at elevated temperatures, up to 600°C. This makes it ideal for high-temperature applications like die-casting and forging.
- Toughness: H13 offers a great balance between hardness and toughness, which means it’s not only hard enough to resist wear but also tough enough to withstand thermal cycling without cracking.
Applications of H13 Spherical Stainless Steel Alloy Powder
So, where does H13 Spherical Stainless Steel Alloy Powder really shine? Thanks to its high wear resistance, thermal stability, and toughness, this alloy is used across a range of industries. From tooling to aerospace, H13 offers a reliable solution for parts that need to endure extreme conditions.
Common Applications by Industry
Industry | Applications |
---|---|
Tooling | Molds, dies, punches, extrusion tools, die-casting dies |
Aerospace | High-temperature engine components, aerospace tooling |
Automotive | High-stress components, transmission parts, engine blocks |
Additive Manufacturing | Custom tooling, prototypes, complex shapes for high-precision applications |
Energy | Turbine blades, high-temperature seals, offshore drilling equipment |
Tooling and Molds: Durability and Precision
In the tooling industry, H13 is a go-to material for making dies and molds. Whether you’re working with plastic injection molding or die-casting, H13’s ability to resist thermal cracking and wear ensures that the tooling lasts longer, even when subjected to multiple cycles of heating and cooling.
Aerospace: High-Temperature Reliability
The aerospace industry demands materials that can withstand extreme environments, and H13 is no exception. The alloy is used in high-temperature engine components and aerospace tooling, where its thermal fatigue resistance ensures that parts remain intact even after prolonged exposure to extreme heat.
Automotive: Strength and Longevity
In the automotive sector, H13’s unique mix of strength and toughness makes it a great choice for high-stress components like transmission parts, engine blocks, and gear systems. Its ability to resist wear and corrosion ensures that parts last longer, offering better performance and lower maintenance costs.
Additive Manufacturing: Customized Precision
As additive manufacturing continues to grow, H13 Spherical Stainless Steel Alloy Powder has become a favored material for 3D printing custom parts. Its spherical shape ensures smooth flow through the printer, and its high-strength properties result in durable, high-precision components.
Specifications, Sizes, and Standards for H13 Alloy Powder
Choosing the right specifications and sizes for your project is crucial, especially when you’re dealing with high-performance alloys like H13. Below, we’ll outline the common sizes, grades, and industry standards that apply to H13 Spherical Stainless Steel Alloy Powder.
Specifications and Standards for H13 Spherical Steel
Specification | Details |
---|---|
Powder Particle Size | 15-45 µm, 45-105 µm |
Purity | ≥ 99.5% |
ASTM Standards | ASTM A681, ASTM F3001 |
ISO Standards | ISO 4957 for tool steels |
Available Forms | Powder, bars, sheets, wires |
Grades Available | H13 Tool Steel |
Powder Particle Size and Purity
The particle size of H13 powder typically ranges between 15-45 µm or 45-105 µm, depending on the specific application. For additive manufacturing, a finer particle size is preferred, while larger sizes may be used for powder metallurgy or traditional sintering processes.
Purity is also a key factor, particularly for high-performance applications like aerospace or medical devices. H13 powders generally offer a purity of 99.5% or greater, ensuring that the final parts maintain excellent mechanical properties.
Standards Compliance
When working with H13 Spherical Stainless Steel Alloy Powder, it is essential to ensure that the material meets the relevant ASTM and ISO standards. These standards ensure that the material is suitable for use in specific applications, whether it’s for tooling, high-temperature components, or additive manufacturing.
Suppliers and Pricing for H13 Spherical Stainless Steel Alloy Powder
The cost of H13 Spherical Stainless Steel Alloy Powder can vary based on factors such as supplier, quantity, and purity levels. Knowing where to source this material and what to expect in terms of pricing will help you plan your project and budget effectively.
Suppliers and Pricing Information
Supplier | Price Range (per kg) | Notes |
---|---|---|
Supplier A | $150 – $250 | Offers bulk discounts for larger orders |
Supplier B | $170 – $260 | Custom particle size options available |
Supplier C | $160 – $240 | Specializes in additive manufacturing powders |
Supplier D | $155 – $245 | High-purity options for critical applications |
Factors Affecting Pricing
- Quantity: As with most materials, buying in bulk can significantly reduce the cost per kilogram of H13 powder. Larger orders may qualify for discounts from suppliers.
- Purity: Higher purity levels, especially for aerospace-grade applications, will generally command a higher price, but this also ensures better performance and durability.
- Custom Particle Sizes: For additive manufacturing or powder metallurgy, custom particle sizes may be required, which can slightly increase the price.
Advantages and Limitations of H13 Spherical Stainless Steel Alloy Powder
While H13 Spherical Stainless Steel Alloy Powder offers a host of benefits, it’s essential to consider both its advantages and limitations when deciding whether it’s the right material for your project.
Advantages of H13 Spherical Stainless Steel Alloy Powder
Advantage | Why It Matters |
---|---|
High Thermal Stability | Withstands high heat without losing strength, ideal for die-casting, and forging. |
Exceptional Wear Resistance | Ideal for tooling and molds that undergo repeated use and abrasion. |
Versatility | Can be used in multiple industries, from aerospace to automotive. |
Good Toughness | Tough enough to resist cracking under thermal cycling. |
3D Printing Ready | Spherical shape ensures smooth flow and precision in additive manufacturing. |
Limitations of H13 Spherical Stainless Steel Alloy Powder
Limitation | Why It Matters |
---|---|
High Machining Costs | Due to its hardness, it can be challenging and costly to machine. |
Limited Corrosion Resistance | While it performs well in high temperatures, it may not be ideal for highly corrosive environments. |
Higher Price | Compared to some other tool steels, H13 can be more expensive, particularly in powder form. |
Frequently Asked Questions (FAQs) About H13 Spherical Stainless Steel Alloy Powder
If you’re still curious about H13 Spherical Stainless Steel Alloy Powder, we’ve compiled a list of frequently asked questions to help you better understand this versatile material.
Question | Answer |
---|---|
What is H13 Spherical Stainless Steel Powder used for? | It’s popular in tooling, molds, aerospace components, and additive manufacturing due to its wear resistance and thermal stability. |
Is H13 powder suitable for 3D printing? | Yes, the spherical shape ensures smooth flow through printers, and its high strength makes it ideal for durable, precise parts. |
How does H13 compare to other tool steels? | H13 offers superior thermal stability and wear resistance compared to other tool steels, making it a top choice for high-temperature applications. |
What is the typical hardness of H13? | H13 typically has a hardness of 50-54 HRC, making it highly resistant to wear and abrasion. |
Is H13 corrosion-resistant? | While H13 offers some corrosion resistance, it’s not as corrosion-resistant as stainless steels and may not be suitable for highly corrosive environments. |
Conclusion
In conclusion, H13 Spherical Stainless Steel Alloy Powder is a versatile and high-performance material that excels in high-temperature and high-wear applications. Its ability to maintain hardness and strength at elevated temperatures makes it a top choice in industries like tooling, aerospace, and automotive. Whether you’re looking to create durable molds for plastic injection or need high-strength components for 3D printing, H13 offers the reliability and performance you need.
No material is without its challenges, and H13 does come with some limitations, including its higher cost and machining difficulty. However, for applications where thermal stability and wear resistance are key, H13 remains one of the best choices on the market.
Get Latest Price
About Met3DP
Product Category
HOT SALE
CONTACT US
Any questions? Send us message now! We’ll serve your request with a whole team after receiving your message.
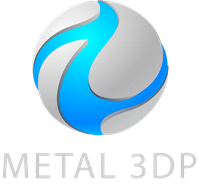
Metal Powders for 3D Printing and Additive Manufacturing