High Frequency Induction Melting
Table of Contents
Imagine a furnace that heats metal not with flames or burning fuel, but with the invisible power of electricity. This isn’t science fiction; it’s the reality of high frequency induction melting, a revolutionary technology transforming the way we melt metals, particularly metal powders.
What is High Frequency Induction Melting?
High frequency induction melting (HFIM) utilizes the principles of electromagnetism to heat and melt metals. Here’s the breakdown:
- Electromagnetic Coil: A coil of copper wire carries a high-frequency alternating current.
- Magnetic Field: This current creates a rapidly oscillating magnetic field around the coil.
- Eddy Currents: When a metal object is placed within this field, electric currents are induced within the metal itself. These are called eddy currents.
- Heat Generation: As the eddy currents flow through the metal’s resistance, they generate heat, rapidly melting the metal.
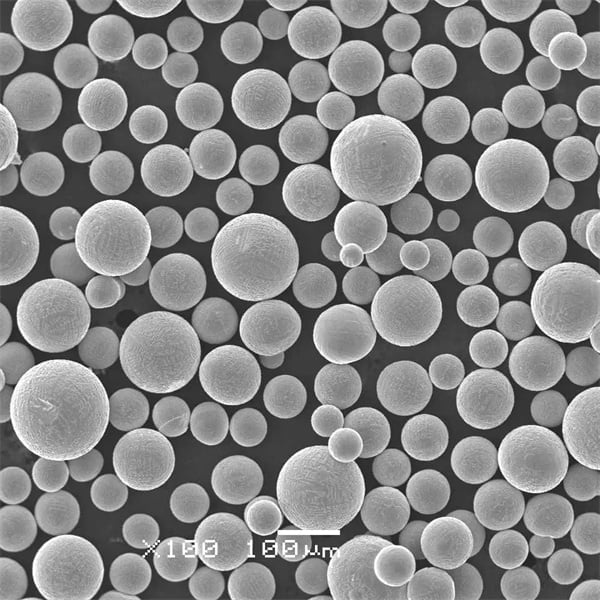
The Advantages of High Frequency Induction Melting
Feature | Advantage Description | Benefit/Impact |
---|---|---|
Clean and Precise Heating | Unlike traditional flame furnaces that rely on combustion and generate gaseous byproducts, High Frequency Induction Melting (HFIM) heats metal directly through electromagnetic induction. | This eliminates contamination from fuel or combustion products, resulting in a purer final product. Additionally, the precise control over heating allows for targeted melting of specific areas within the metal, minimizing the risk of overheating or uneven melting. |
Fast and Efficient Melting | HFIM utilizes the rapid generation of eddy currents within the metal itself to create heat. | This translates to significantly faster melting times compared to flame furnaces. The reduction in heating time not only translates to increased production output but also lowers overall energy consumption, making HFIM a more sustainable melting solution. |
Uniform Melting | The consistent heating pattern throughout the metal achieved by HFIM minimizes the formation of hot spots, a common issue with traditional methods. | This leads to a more uniform and consistent final product with predictable material properties. Reduced hot spots also minimize the risk of metal burning or degradation, leading to higher material yield. |
Minimal Metal Loss | Since HFIM is a contactless heating method, there’s minimal metal oxidation or burning that occurs during the melting process. | This translates to a higher yield of usable metal compared to traditional methods where a portion of the metal is inevitably lost due to oxidation or slag formation. Reduced metal loss not only improves material efficiency but also lowers overall production costs. |
Versatility | HFIM boasts a high degree of versatility when it comes to melting different materials. | The technology can be effectively used to melt a wide range of metals, including ferrous and non-ferrous alloys, as well as various metal powders. This adaptability makes HFIM a valuable tool for diverse industries with varying melting requirements. |
Applications of High Frequency Induction Melting
Industry | Application | Advantages of HFIM |
---|---|---|
Metal Casting | Foundries extensively utilize HFIM furnaces for melting various metals used in casting processes. | The clean and precise heating of HFIM ensures minimal contamination of the molten metal, leading to castings with superior quality and mechanical properties. Additionally, the fast melting times offered by HFIM contribute to increased production efficiency within foundries. |
Metal Additive Manufacturing (AM) | The precise control and clean heating of HFIM make it a perfect fit for melting metal powders used in 3D printing processes like Selective Laser Melting (SLM) and Electron Beam Melting (EBM). | Metal powders can be highly susceptible to oxidation during the melting process, which can negatively impact the final product’s properties. HFIM minimizes oxidation due to its contactless heating, resulting in high-quality metal powder melting for AM applications. The fast and uniform melting achieved by HFIM also contributes to the creation of strong and densely packed metal parts in the final 3D printed product. |
Jewelry Making | Goldsmiths and jewelers leverage HFIM for its clean and precise melting of precious metals like gold, silver, and platinum. | The ability to precisely control the heating temperature in HFIM minimizes metal loss due to burning or excessive heat, which is a significant concern when dealing with precious metals. Additionally, the clean and contamination-free melting environment offered by HFIM ensures the preservation of the precious metal’s inherent luster and quality, leading to high-quality jewelry pieces. |
Heat Treatment | Induction heating, a core principle of HFIM, can be used for localized heat treatment of specific areas within a metal component. | This allows for targeted modification of the material properties in specific regions of the component. For instance, HFIM can be used to harden specific areas of a tool or component while leaving the core material ductile. The precise control over heating zones offered by HFIM minimizes the risk of unintended heat treatment of surrounding areas, leading to a more controlled and predictable process. |
Brazing and Soldering | The controlled heating capabilities of HFIM enable precise brazing and soldering of different metal components. | The ability to focus heat on the desired joining area minimizes the risk of damaging surrounding components, particularly in delicate applications involving temperature-sensitive materials. The fast and efficient heating provided by HFIM also contributes to faster brazing and soldering processes, leading to improved production throughput. |
Metal Powders for High Frequency Induction Melting
Metal powders offer unique advantages in various applications, but melting them traditionally can be challenging due to their high surface area and propensity for oxidation. HFIM overcomes these challenges, making it an ideal choice for melting various metal powders:
Common Metal Powders for HFIM:
Metal Powder | Description | Applications |
---|---|---|
Gas-Atomized Steel Powders: | Produced by injecting molten steel into an inert gas stream, creating fine, spherical particles. | Used in metal additive manufacturing (SLM) for high-performance steel components. |
Water-Atomized Steel Powders: | Similar to gas-atomized powders, but produced using a water stream, resulting in a less spherical and slightly coarser powder. | Used in metal injection molding (MIM) and other applications requiring lower cost powders. |
Stainless Steel Powders: | Available in various grades (316L, 17-4PH, etc.), offering corrosion resistance and high strength. | Used in SLM for components requiring excellent corrosion resistance and mechanical properties. |
Nickel-Based Alloy Powders: | Offer high strength and temperature resistance at elevated temperatures. | Used in SLM for aerospace, gas turbine, and other high-temperature applications. |
Aluminum Powders: | Lightweight and offer good electrical conductivity. | Used in SLM for lightweight components and applications requiring high electrical conductivity. |
Titanium Powders: | High strength-to-weight ratio and excellent corrosion resistance. | Used in SLM for aerospace and biomedical applications. |
Cobalt Chrome Powders: | Biocompatible and offer high wear resistance. | Used in SLM for medical implants and other wear-resistant applications. |
Copper Powders: | Excellent electrical conductivity and thermal conductivity. | Used in additive manufacturing for electrical components and heat sinks. |
Tungsten Powders: | Very high melting point and excellent heat resistance. | Used in applications requiring |
Inconel Powders: | A family of nickel-chromium superalloys offering exceptional high-temperature performance. | Used in SLM for gas turbine engine components and other high-temperature applications. |
Tool Steel Powders: | Available in various grades for specific cutting tool applications. | Used in SLM for the production of complex cutting tools with high wear resistance. |
Choosing the Right Metal Powder for HFIM
Selecting the right metal powder for your HFIM application requires careful consideration of several factors:
- Desired Properties: The final product’s required strength, corrosion resistance, weight, conductivity, and other properties will dictate the ideal metal powder choice.
- Particle Size and Morphology: The size and shape of the powder particles can influence flowability, packing density, and final product properties.
- Powder Purity: For critical applications, high-purity powders are essential to minimize contamination and ensure optimal performance.
- Cost: Metal powders can vary significantly in cost depending on the material, production method, and particle characteristics.
Advantages of HFIM for Metal Powders
Advantage | Description | Impact on Metal Powders |
---|---|---|
Minimized Oxidation | A significant challenge in traditional melting methods for metal powders is oxidation. The high surface area of the powder particles makes them particularly susceptible to reacting with oxygen at high temperatures. | HFIM’s contactless heating significantly reduces the risk of oxidation during the melting process. Since the metal powder isn’t directly exposed to a flame or high-temperature environment, minimal interaction with oxygen occurs. This translates to minimal formation of oxides within the melted metal, leading to a purer and higher-quality final product in applications like metal additive manufacturing (AM). |
Improved Flowability | Metal powders, particularly those with irregular shapes, can exhibit poor flowability, hindering their performance in AM processes. Uneven flow can lead to inconsistencies in powder bed density, impacting the final product’s quality. | The uniform heating provided by HFIM can improve the flowability of metal powders. As the powder particles are heated throughout the volume, they tend to become more spherical and free-flowing. This enhanced flowability translates to a more consistent powder bed in AM processes, leading to improved product quality and dimensional accuracy. |
Reduced Spatter | Traditional melting methods for metal powders can generate spatter, which refers to the ejection of molten metal droplets during the process. Spatter can cause various issues, including contamination of the surrounding environment and potential safety hazards for operators. | The controlled heating environment of HFIM minimizes the occurrence of spatter. Since the metal powder isn’t directly exposed to a high-temperature flame or subjected to significant physical agitation, the risk of molten metal droplets being ejected is significantly reduced. This leads to a cleaner and safer working environment for operators and minimizes the need for extensive post-processing steps to remove spatter from the final product. |
Faster Melting Rates | Rapid melting times are crucial for efficient metal powder processing, particularly in high-volume AM applications. Traditional methods can be limited by the time it takes to heat the entire powder bed uniformly. | The rapid generation of heat through eddy currents within the metal powder itself is a core advantage of HFIM. This translates to significantly faster melting times compared to traditional methods. Faster melting rates contribute to increased productivity in AM processes and allow for the creation of larger and more complex metal parts in a shorter timeframe. |
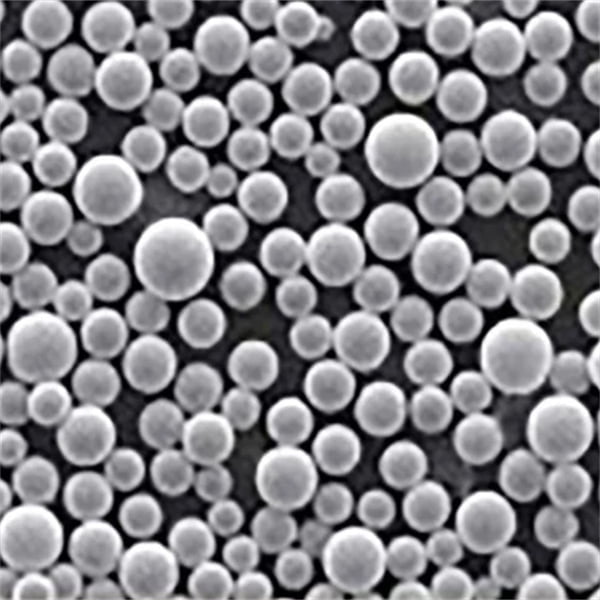
Challenges of HFIM for Metal Powders
Challenge | Description | Potential Impact |
---|---|---|
Powder Handling | Metal powders, particularly those with fine particle sizes, can be easily airborne and pose inhalation hazards if not handled properly. | The fine and lightweight nature of metal powders necessitates careful handling procedures during loading, unloading, and any maintenance processes involving the HFIM furnace. Inadequate ventilation systems or improper handling techniques can lead to the creation of a hazardous work environment for operators, with the risk of inhaling metal particles. |
Process Control | Achieving optimal melting results with metal powders using HFIM requires precise control over various furnace parameters. These parameters include temperature, power settings, and the surrounding atmosphere within the furnace. | Even slight variations in these parameters can significantly impact the final properties of the melted metal. For instance, excessively high temperatures can lead to excessive grain growth or even burning of the metal powder, while insufficient temperatures might result in incomplete melting. Strict adherence to established process parameters and the use of sophisticated control systems are crucial for achieving consistent and high-quality results with HFIM for metal powders. |
Cost | Compared to traditional melting equipment, HFIM furnaces can represent a higher initial investment cost. Additionally, the consumables associated with HFIM systems, such as crucibles and liners, can also contribute to ongoing operational costs. | While the long-term benefits of HFIM, including improved product quality, increased efficiency, and potentially lower material waste, can offset the initial cost over time, the upfront investment in the technology may be a barrier for some companies, particularly smaller operations. |
Considerations for Safe Operation of HFIM Systems
- Proper Training: Operators of HFIM systems should receive proper training on safe operation procedures to minimize the risk of electrical hazards and burns.
- Personal Protective Equipment (PPE): Wearing appropriate PPE, including gloves, eye protection, and respiratory protection (if necessary), is crucial for operator safety.
- Grounding and Shielding: Proper grounding and shielding of the furnace are essential to prevent stray currents and electromagnetic interference.
- Maintenance: Regular maintenance of the HFIM system is critical to ensure optimal performance and safety.
Future of High Frequency Induction Melting
HFIM technology is rapidly evolving, with advancements in:
- Solid-State Power Supplies: These provide more precise control over the heating process and offer improved efficiency.
- Vacuum and Inert Atmosphere Melting: These techniques allow for melting of reactive metals that are prone to oxidation in air.
- Integration with Additive Manufacturing: As additive manufacturing continues to grow, HFIM will become increasingly integrated as a reliable and precise melting solution for metal powders.
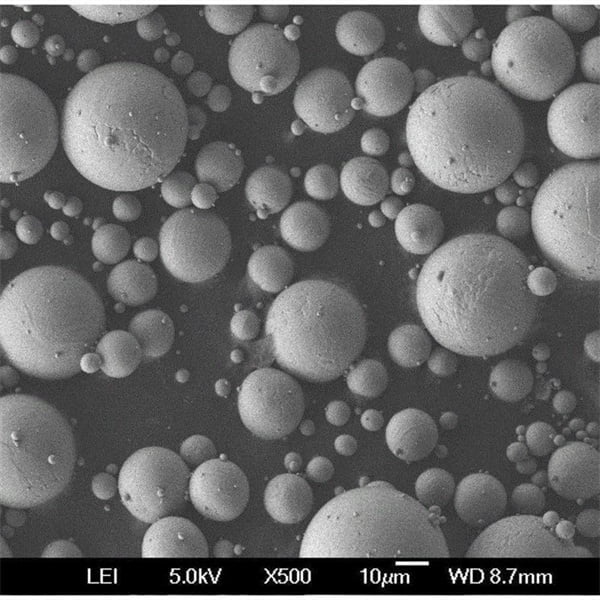
FAQ
Question | Answer |
---|---|
What are the limitations of HFIM? | While HFIM offers numerous advantages, it may not be suitable for all applications. The upfront cost of the furnace system can be higher compared to traditional methods. Additionally, melting very large quantities of metal might be more efficient using other methods. |
Can HFIM be used for melting other materials besides metals? | While primarily used for metals, HFIM can also be used for melting certain conductive materials like some types of semiconductors. |
What are the environmental benefits of HFIM? | Compared to traditional fuel-fired furnaces, HFIM offers a cleaner and more energy-efficient melting process, reducing greenhouse gas emissions. |
Where can I find more information about HFIM systems? | Several manufacturers offer HFIM furnaces, and many provide detailed information on their websites or through technical brochures. |
Share On
MET3DP Technology Co., LTD is a leading provider of additive manufacturing solutions headquartered in Qingdao, China. Our company specializes in 3D printing equipment and high-performance metal powders for industrial applications.
Inquiry to get best price and customized Solution for your business!
Related Articles
About Met3DP
Recent Update
Our Product
CONTACT US
Any questions? Send us message now! We’ll serve your request with a whole team after receiving your message.
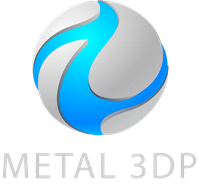
Metal Powders for 3D Printing and Additive Manufacturing
COMPANY
PRODUCT
cONTACT INFO
- Qingdao City, Shandong, China
- [email protected]
- [email protected]
- +86 19116340731