High Temperature Alloy Powder
Table of Contents
High temperature alloy powders are materials that can withstand extremely high temperatures without deforming or deteriorating. These advanced materials are vital for applications in extreme environments like jet engines, gas turbines, rockets, nuclear reactors, and more.
Overview of High Temperature Alloy Powder
High temperature alloys, also known as superalloys, have excellent mechanical strength, resistance to thermal creep deformation, good surface stability, and corrosion and oxidation resistance at high temperatures. Key features include:
- Withstand temperatures over 1000°C
- Retain strength, toughness and stability at high temps
- Used for ultra-hot sections of jet engines and gas turbines
- Harder than titanium alloys and most steels
- Mainly nickel, cobalt or iron-based alloys
Composition: High temperature alloys contain complex combinations of materials like nickel, cobalt, iron, chromium, aluminum, tungsten, molybdenum, tantalum, niobium etc. in varying percentages. Precise composition is tailored to meet application needs.
Production: Superalloy powder is made using gas or water atomization of alloy melts into fine spherical powders optimized for additive manufacturing or thermal spraying. Other powder production methods include vacuum induction melting, vacuum arc melting, hot isostatic pressing and more.
Common Types: Popular classifications include nickel, cobalt and iron-based superalloys. Here are some common varieties:
- Nickel alloys – Inconel, Hastelloy, Waspaloy, Rene alloys
- Cobalt alloys – Haynes, HS alloys
- Iron alloys – A286, 9Cr steels
Key Properties: Superalloy powders offer exceptional properties like:
- High temperature strength – For loadbearing parts
- Resistance to creep and fatigue – Crucial for reliability
- Oxidation and corrosion resistance – Prevent deterioration
- Thermal stability – Consistent performance when hot
- Weldability – For manufacture and repair
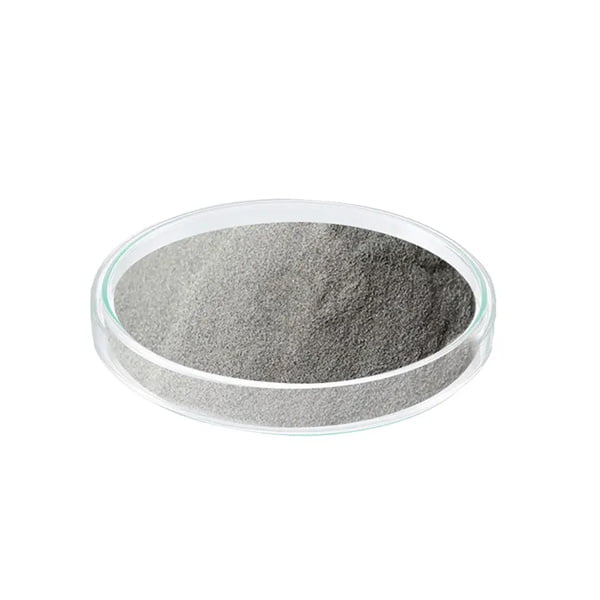
Applications of High Temperature Alloy Powder
Thanks to their extreme temperature durability, high temperature alloy powders are used to make components for the hottest sections of:
- Jet aircraft engines
- Land-based gas turbines
- Coal gasification plants
- Space rockets and nuclear reactors
- Oil and gas drilling equipment
Jet Engines: Superalloys make up over 50% of advanced jet engine parts like blades, combustor cans and afterburner components. Nickel alloys like Inconel 718 and René N5 excel in jet engine applications, resisting immense heat and centrifugal forces.
Gas Turbines: Iron and nickel-based alloys withstand the ultra-high temperatures inside gas turbine hot sections. Pieces like blades, nozzles and combustors operate at over 1000°C and rely on alloys like Inconel 738 and Haynes 230.
Coal Plants: Iron and nickel alloys in coal gasification plants must perform in excess of 850°C in highly corroding sulfur environments. Here, alloys like 310 stainless and Inconel 601 handle the heat.
Aerospace: High temperature nickel alloys make many rocket engine and nuclear reactor components for space applications. Samples include combustion chambers, thrust nozzles, fuel elements and fasteners made of NB-36 alloy.
Oil/Gas: Drilling operations often utilize high-cobalt HS-188 alloy for components and tools used in extremely hot, corrosive oil well environments.
Specifications of High Temperature Alloy Powder
Superalloy powder has a diverse range materials and compositions tailored to operate at varying temperature thresholds from 800°C to over 1000°C. Here are some common grades and specs:
Alloy | Base Material | Max Temp (°C) | Features |
---|---|---|---|
Inconel 625 | Nickel | 1000°C | Excellent corrosion resistance up to 980°C |
Hastelloy X | Nickel+Iron+Chromium | 1150°C | Resists oxidation and sulfidation |
Haynes 230 | Nickel+Chromium+Tungsten | 1100°C | Withstands thermal shock and cycling |
Incoloy 800 | Iron+Nickel+Chromium | 1150°C | Handles carburizing atmospheres |
René 41 | Nickel+Chromium | 1100°C | Jet engine alloy with good ductility |
Product Standards: Key specifications for popular alloys:
- Inconel 718 – AMS 5662, ASTM B637
- Hastelloy C276 – ASME SB574
- Incoloy 800H – AMS 5540A
- Haynes 214 – AMS 5759, AMS 5382
Powder Sizes: Different size fractions optimized for various AM processes:
- Laser powder bed fusion: 15-45 microns
- Binder jetting: 300+ microns
- Directed energy deposition: 45-150 microns
Comparison Between Superalloy Powder Materials
Various high temperature alloy options have relative strengths and weaknesses:
Parameter | Nickel Alloys | Cobalt Alloys | Iron Alloys |
---|---|---|---|
Max temperature | 1000-1150°C | 1000-1150°C | 700-1000°C |
Cost | Highest | Mid-range | Lowest |
Strength | Strong | Strongest | Strong |
Oxidation resistance | Best | Very good | Moderate |
Thermal fatigue | Excellent | Very good | Limited |
Examples | Inconel, Waspaloy | HS-188, Haynes 25 | 310 stainless, Fecralloy |
So nickel alloys generally outperform others in extreme temperatures and corrosion resistance. But cobalt alloys offer the greatest raw strength, while iron alloys provide budget options.
Suppliers of High Temperature Alloy Powder
Many advanced material suppliers offer various superalloy powder types. Some major manufacturers include:
Supplier | Alloy Brands | Production Methods | Pricing |
---|---|---|---|
Sandvik | Osprey, Nikrotalloy | Gas atomization | $$$$ |
Praxair | Contalloy, Thermalloy | Vacuum induction melting | $$$ |
AMC Powders | Ferro-alloys | Water atomization | $-$$ |
Tekna | Ultramet alloys | Plasma spheroidization | $$$ |
Special Metals Corp | Inconel, René alloys | Multiple methods | $$$$ |
Pricing ranges based on alloy type, particle size distribution, sphericity, quantity, purity levels and more. Small lab quantities can cost over $500/kg. Large commercial batches average around $100-300/kg for common alloys.
Pros and Cons of High Temperature Alloy Powder
Pros | Cons |
---|---|
Withstand extreme temps over 1000°C | Very expensive, over 3X cost of steels |
Retain strength and resist creep deformation | Sensitive to minor impurities or defects |
Exceptional corrosion and oxidation resistance | Prone to strain-age cracking if improperly cooled |
Thermal stability and conductivity | Difficult to machine or work with using conventional methods |
Various alloying elements provide tailored properties | Requires advanced powder production and additive manufacturing methods |
In summary, superalloy’s outstanding thermal properties warrant their high price for ultra-hot applications. But they remain challenging materials to fabricate using traditional methods.
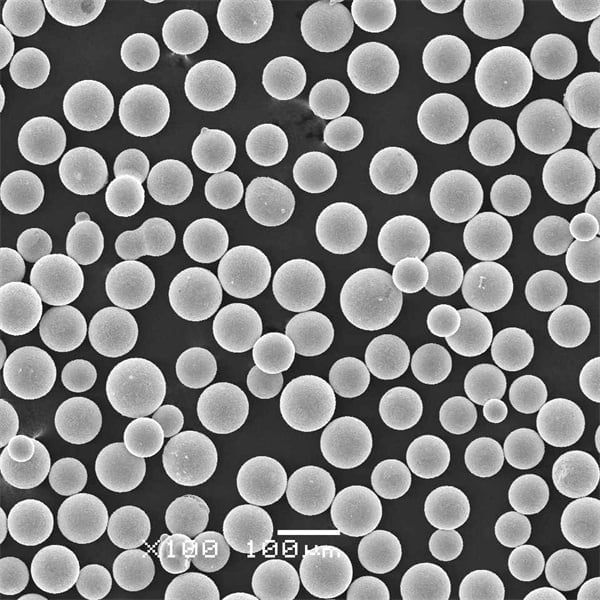
FAQs
Q: What makes superalloys withstand such extreme temperatures?
A: Careful combinations of nickel, cobalt, chromium, aluminum, tungsten etc. impart strength, resist creep and deterioration of properties at high operating temps over 85% of their melting points.
Q: What additive manufacturing methods work with superalloy powders?
A: Laser powder bed fusion and directed energy deposition are well-suited for processing high temperature alloy powder. Binder jetting is viable but can require additional sintering and infiltration steps.
Q: How are high temperature alloy components repaired or fixed?
A: Brazing, welding and thermal spray coatings using matching superalloy filler material can refurbish damaged components. Parts may also be salvaged via hot isostatic pressing.
Q: Are high temperature alloys recyclable?
A: Yes, superalloy scrap and powders can be reclaimed and reprocessed via vacuum induction melting and atomization into fresh powder feedstock for AM production. This provides significant cost savings.
Q: What are typical applications for iron-based high temperature alloys?
A: Lower cost iron superalloys are extensively used in fired heaters, ethylene furnaces, nuclear fuel cladding, power gen hardware, chemical refining equipment.
Share On
MET3DP Technology Co., LTD is a leading provider of additive manufacturing solutions headquartered in Qingdao, China. Our company specializes in 3D printing equipment and high-performance metal powders for industrial applications.
Inquiry to get best price and customized Solution for your business!
Related Articles
About Met3DP
Recent Update
Our Product
CONTACT US
Any questions? Send us message now! We’ll serve your request with a whole team after receiving your message.
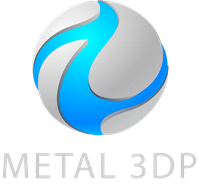
Metal Powders for 3D Printing and Additive Manufacturing