How the Gas Atomization Process Works
Table of Contents
Overview
Gas atomization is a metal powder production method that uses high-velocity inert gas jets to disintegrate a molten metal stream into fine spherical powder particles. The gas atomization process achieves excellent control over powder particle size distribution, morphology, purity, and microstructure.
Key attributes of gas-atomized powder include spherical particle shape, high purity, fine sizes down to 10 microns, and uniform composition. Gas atomization facilitates advanced powder-based manufacturing techniques like metal injection molding, additive manufacturing, and powder metallurgy pressing and sintering.
This guide provides a comprehensive overview of the gas atomization process and powder. It covers atomization methods, particle formation, process parameters, equipment, applicable alloys, powder characteristics, product specifications, applications, and suppliers. Helpful comparison tables are included to summarize technical details.
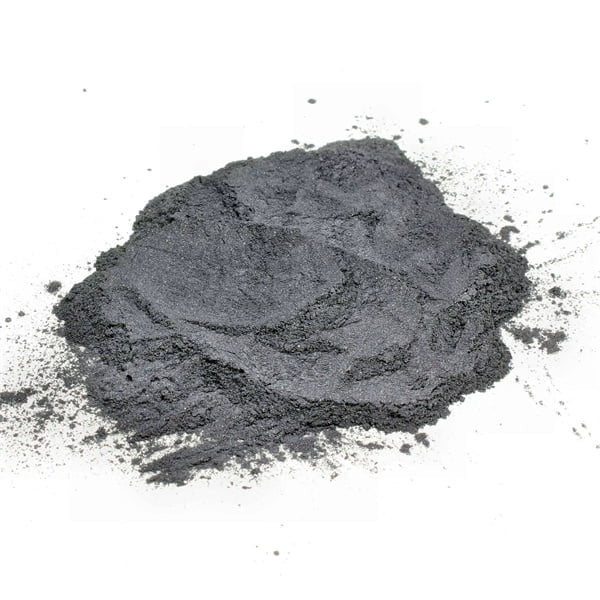
How the Gas Atomization Process Works
Gas atomization converts molten alloy into powder using the following fundamental steps:
Gas Atomization Process Stages
- Melting – Alloy is melted in an induction furnace and superheated above its liquidus temperature
- Pouring – Molten metal stream poured into an atomization chamber
- Atomization – High velocity inert gas jets disintegrate the metal into fine droplets
- Solidification – Metal droplets rapidly solidify into powder particles as they fall through the chamber
- Collection – Powder particles collected in a cyclone separator at bottom of tower
The key phenomenon occurs when the kinetic energy of the gas jets overcomes the metal’s surface tension to shear the liquid stream into droplets. These droplets freeze into powder particles with spherical morphology.
Careful process control allows tailored powder particle sizes, purity, and microstructures.
Methods of Gas Atomization
There are two primary methods of gas atomization used in industry:
Gas Atomization Methods
Method | Description | Advantages | Limitations |
---|---|---|---|
Close-coupled atomization | Nozzle in close proximity to melt pour point | Compact design, lower gas use | Potential melt contamination from nozzle |
Free-fall atomization | Nozzle located below pour point | Reduced melt contamination | Requires taller atomization tower |
Close-coupled designs recycle the atomizing gas but risk some melt oxidation. Free-fall offers cleaner atmosphere with less risk of nozzle reaction.
Additional variants include multiple gas nozzles, ultrasonic atomization, centrifugal atomization, and coaxial nozzle designs for specialized applications.
Gas Atomization Nozzle Designs
Various nozzle designs create the high velocity gas jets needed for atomization:
Gas Atomization Nozzle Types
Nozzle | Description | Gas Flow Pattern | Droplet Size |
---|---|---|---|
De Laval | Converging-diverging nozzle | Supersonic | Large, wide distribution |
Conical | Simple conical orifice | Sonic | Medium |
Slit | Elongated slit orifice | Sonic | Small |
Multiple | Array of micro-nozzles | Sonic/supersonic | Very small, narrow distribution |
De Laval nozzles use gas acceleration to supersonic velocities but have complex geometry. Sonic nozzles with simplified shapes offer more flexibility.
Smaller droplets and tightly controlled size distribution are achieved by using multiple micro-nozzles or slit configurations.
Powder Formation and Solidification
The shearing of molten metal into droplets and subsequent solidification follow distinct mechanisms:
Powder Formation Stages
- Breakup – Rayleigh jet instability causes perturbations and droplet formation
- Distortion – Droplets elongate into ligaments due to air drag forces
- Rupture – Ligaments breakdown into droplets close to final size
- Solidification – Rapid cooling via gas contact and radiation forms solid particles
- Deceleration – Loss of velocity as particles move down through atomization chamber
The combined effects of surface tension, turbulence, and air drag determine final particle sizes and morphology. Maximum particle cooling rates over 1,000,000 °C/s quench metastable phases.
Process Parameters
Key gas atomization process parameters include:
Gas Atomization Process Parameters
Parameter | Typical Range | Effect on Powder |
---|---|---|
Gas pressure | 2-10 MPa | Increasing pressure reduces particle size |
Gas velocity | 300-1200 m/s | Higher velocity produces finer particles |
Gas flow rate | 0.5-4 m3/min | Increases flow for higher throughput and finer sizes |
Melt superheat | 150-400°C | Higher superheat reduces satellites and improves powder flow |
Melt pour rate | 10-150 kg/min | Lower pour rates improve particle size distribution |
Melt stream diameter | 3-8 mm | Larger stream allows higher throughput |
Separation distance | 0.3-1 m | Greater distance reduces satellite content |
Balancing these parameters allows control of powder particle size, shape, production rate, and other characteristics.
Alloy Systems for Gas Atomization
Gas atomization can process almost any alloy into powder form including:
Alloys Suitable for Gas Atomization
- Titanium alloys
- Nickel superalloys
- Cobalt superalloys
- Stainless steels
- Tool steels
- Low alloy steels
- Iron and nickel base alloys
- Precious metals
- Intermetallics
Gas atomization requires melting temperatures below the decomposition point of the atomizing gas. Typical gases include argon, nitrogen, and helium.
Refractory alloys with very high melting points like tungsten can be challenging to atomize and often require specialized processing.
Most alloys require melt superheating well above the liquidus temperature to maintain sufficient fluidity for atomization into finely dispersed droplets.
Characteristics of Gas Atomized Powder
Typical characteristics of gas atomized powder:
Gas Atomized Powder Characteristics
Characteristic | Description | Significance |
---|---|---|
Particle morphology | Highly spherical | Excellent flowability, packing density |
Particle size distribution | Adjustable in 10-150 μm range | Controls pressed density and sintering behavior |
Particle size span | Can achieve tight distributions | Provides uniform component properties |
Chemical purity | Typically >99.5% excluding planned alloys | Avoid contamination from nozzle reactions |
Oxygen content | <1000 ppm | Critical for high performance alloys |
Apparent density | Up to 60% of theoretical | Indicative of pressibility and handling |
Internal porosity | Very low | Good for microstructural homogeneity |
Surface morphology | Smooth with some satellites | Indicates process stability |
The spherical shape and adjustable size distribution facilitate usage in secondary powder consolidation processes. Tight control over oxygen and chemistry enables high performance alloys.
Specifications for Gas Atomized Powders
International standard specifications help define:
- Particle size distribution
- Apparent density ranges
- Hall flow rates
- Acceptable oxygen and nitrogen levels
- Allowable microstructure and porosity
- Chemical composition limits
- Sampling procedures
This supports quality control and reproducible powder behavior.
Specifications for Gas Atomized Powders
Standard | Materials | Parameters | Test Methods |
---|---|---|---|
ASTM B964 | Titanium alloys | Particle size, chemistry, microstructure | X-ray diffraction, microscopy |
AMS 4992 | Aerospace titanium alloys | Particle size, oxygen content | Sieve analysis, inert gas fusion |
ASTM B823 | Tool steel powder | Apparent density, flow rate | Hall flowmeter, Scott volumeter |
SAE AMS 5050 | Nickel alloys | Particle size, morphology | Laser diffraction, SEM |
MPIF 04 | Many standard alloys | Apparent density, flow rate | Hall flowmeter, tapped density |
Specifications are tailored to critical application requirements in aerospace, automotive, medical, and other quality-driven industries.
Applications of Gas Atomized Powder
Gas atomized powders enable manufacturing of high performance components via:
- Metal Injection Molding (MIM)
- Additive Manufacturing (AM)
- Hot Isostatic Pressing (HIP)
- Powder Forging
- Thermal and Cold Spray
- Powder Metallurgy Pressing and Sintering
Benefits versus wrought materials:
- Complex geometries with fine features
- Excellent mechanical properties
- Near full density consolidation
- Novel and customized alloys
- Range of material options
Gas atomization excels at producing spherical, flowing powders optimal for automated processing of intricate components with high quality standards across industries.
Global Suppliers of Gas Atomized Powders
Prominent global suppliers of gas atomized powders include:
Gas Atomized Powder Manufacturers
Company | Materials | Capabilities |
---|---|---|
ATI Powder Metals | Titanium, nickel, tool steel alloys | Broad alloy range, high volumes |
Praxair Surface Technologies | Titanium, nickel, cobalt alloys | Wide alloy selection, toll processing |
Sandvik Osprey | Stainless steels, low alloy steels | Specialists in ferrous materials |
Höganäs | Tool steels, stainless steels | Custom alloys, additive manufacturing powders |
Carpenter Additive | Titanium, nickel, cobalt alloys | Custom alloys, specialized particle sizes |
Smaller regional suppliers also offer gas atomized powders, often servicing niche alloys or applications.
Many providers also undertake sieving, blending, coating, and other powder post-processing operations.
Advantages vs. Limitations of Gas Atomization
Gas Atomization – Pros and Cons
Advantages | Limitations |
---|---|
Spherical powder morphology | Higher upfront capital costs |
Controlled particle size distributions | Requires high purity inert gas |
Applicable to many alloy systems | Refractory alloys challenging to atomize |
Clean powder chemistry and microstructure | Can experience nozzle erosion |
Rapid powder quenching preserves metastable phases | Requires melt superheating well above liquidus |
Continuous powder production process | Powder shape limits green strength |
The spherical shape and fine sizes of gas atomized powder provide distinct advantages but come at a higher operational cost versus simpler mechanical comminution processes.
Selecting Gas Atomized Powder
Key aspects when selecting gas atomized powder:
- Desired chemistry and alloy composition
- Target particle size distribution
- Suitable apparent and tap density ranges
- Oxygen and nitrogen limits dictated by application
- Flow characteristics for automated powder handling
- Sampling procedures to ensure representativeness
- Vendor technical expertise and customer service
- Total cost considerations
Testing prototype builds helps qualify new alloys and gas atomized powders for an application. Collaborating closely with the powder producer enables optimization.
FAQ
What is the smallest particle size that gas atomization can produce?
Specialized nozzles can produce single-digit micron powder down to 1-5 microns. However, ultrafine powder has very low apparent density and exhibits strong interparticle Van der Waals forces, requiring careful handling.
What causes powder satellites during gas atomization?
Satellites form when droplets are too large or collide and partially rejoin before fully solidifying. Higher superheat, lower pour rates, and increased separation distance all help reduce satellites.
Why is high purity inert gas required for gas atomization?
High velocity gas jets can erode metal from the nozzle over time and contaminate powder. Reactive gases like nitrogen and oxygen also negatively affect powder purity and alloy performance.
How does gas atomization compare to water atomization?
Water atomization produces more irregular powder at larger sizes of 50-150 microns typically. Gas atomization allows finer sizes down to 10 microns with spherical morphologies preferred for pressing and sintering applications.
What is centrifugal atomization?
In centrifugal atomization, molten metal is poured into a spinning disk that throws off fine molten metal droplets that solidify into powder. This method offers higher production rates than gas atomization but reduced powder size and shape control.
Can you switch alloys quickly during gas atomization?
Yes, with specialized equipment the melt stream can be changed rapidly to produce composite and alloyed powders. However, cross-contamination between alloys should be minimized through chamber purging.
Conclusion
The gas atomization process produces spherical, flowing metallic powders with tightly controlled particle size distribution, purity, and microstructural characteristics optimal for advanced powder consolidation processes across critical applications. Careful manipulation of process parameters and specialized nozzle designs allow extensive control over final powder characteristics. With continued development, gas atomization provides engineers greater ability to manufacture high-performance components in creative new ways.
Share On
MET3DP Technology Co., LTD is a leading provider of additive manufacturing solutions headquartered in Qingdao, China. Our company specializes in 3D printing equipment and high-performance metal powders for industrial applications.
Inquiry to get best price and customized Solution for your business!
Related Articles
About Met3DP
Recent Update
Our Product
CONTACT US
Any questions? Send us message now! We’ll serve your request with a whole team after receiving your message.
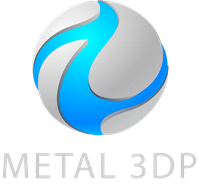
Metal Powders for 3D Printing and Additive Manufacturing
COMPANY
PRODUCT
cONTACT INFO
- Qingdao City, Shandong, China
- [email protected]
- [email protected]
- +86 19116340731