Inconel 625 Powder for Additive Manufacturing Applications Guide
Table of Contents
Inconel 625 is a nickel-based superalloy widely used across aerospace, chemical processing, and energy industries owing to its high strength, corrosion resistance, and temperature capabilities. This guide covers Inconel 625 powder properties, manufacturing methods, industry applications, post-processing procedures, and suppliers.
Introduction to Inconel 625 Alloy Powder
Inconel 625 is a high performance alloy composed primarily of nickel, chromium, and molybdenum. Key characteristics include:
Table 1: Inconel 625 powder overview
Properties | Details |
---|---|
Nickel content | 58-63% |
Density | 8.44 g/cm3 |
Melting point | 1,260-1,340°C |
Tensile strength | 1,240 MPa |
Yield strength | 550 MPa |
Elongation | 30% |
Corrosion resistance | Excellent in extreme environments |
Workability | Readily welded and fabricated |
These properties support use across chemical processing, aerospace components, and oil/gas hardware. Additive manufacturing expands possibilities for custom, complex Inconel 625 parts.
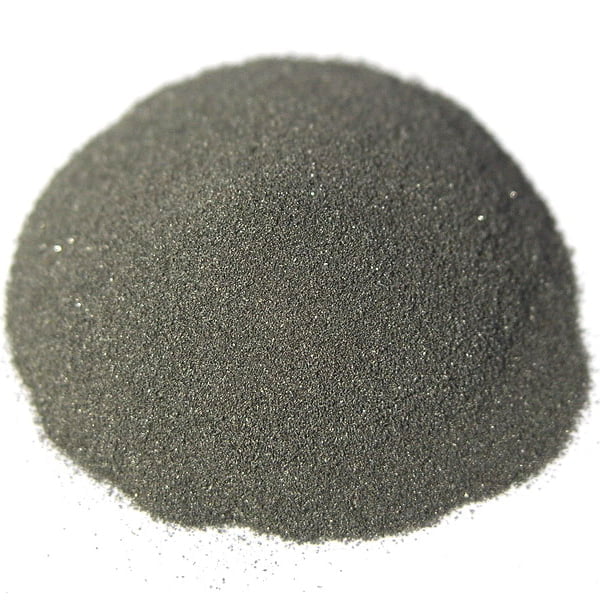
Chemical Composition
The Inconel 625 alloy composition consists of:
Table 2: Inconel 625 standard chemistry
Element | Weight % | Role |
---|---|---|
Nickel (Ni) | 58.0 – 63.0% | Matrix element |
Chromium (Cr) | 20.0 – 23.0% | Oxidation resistance |
Molybdenum (Mo) | 8.0 – 10.0% | Strengthening |
Niobium (Nb) | 3.15 – 4.15% | Precipitate hardening |
Iron (Fe) | ≤ 5% | Tramp element |
Carbon (C) | ≤ 0.10% | Impurity limit |
Manganese (Mn) | ≤ 0.5% | Residual |
Silicon (Si) | ≤ 0.5% | Deoxidizer |
Phosphorus (P) | ≤ 0.015% | Impurity limit |
Sulfur (S) | ≤ 0.015% | Impurity limit |
Aluminum (Al) | ≤ 0.4% | Impurity limit |
Careful optimization of nickel, chromium, molybdenum, and niobium is key for achieving desired mechanical properties.
Key Properties of Inconel 625 Powder
Table 3: Inconel 625 powder properties
Property | Value |
---|---|
Density | 8.44 g/cm3 |
Melting point | 1,260-1,340°C |
Thermal conductivity | 9.8 W/m-K |
Electrical resistivity | 134 μΩ-cm |
Modulus of elasticity | 207 GPa |
Poisson’s ratio | 0.29 |
Tensile strength | 1,240 MPa |
Yield strength | 550 MPa |
Elongation | 30% |
Hardness | ~36 HRC |
These attributes enable using Inconel 625 in load-bearing applications up to 700°C where resistance to thermal fatigue, oxidation, and creep are critical.
Production Method for Inconel 625 Powder
Table 4: Inconel 625 powder production methods
Method | Description | Characteristics |
---|---|---|
Gas atomization | High pressure gas nozzle disintegrates molten metal stream | Spherical powder ideal for AM |
Plasma atomization | Electrodes melted by plasma arcs/torches into droplets | Controlled powder size distribution |
Rotating electrode | Centrifugal disintegration of spinning molten metal by electric arcs | Narrowest particle distribution |
Advanced gas atomization processes allow tuning powder shape, surface chemistry, defects, and particle size distribution suitable for additive manufacturing to minimize porosity.
Applications of Inconel 625 Powder
The combination of strength, fracture toughness, weldability and corrosion resistance make Inconel 625 suitable for:
Table 5: Inconel 625 powder applications
Industry | Components |
---|---|
Aerospace | Turbine blades, combustion cans, rocket nozzles |
Oil and gas | Wellhead valves, downhole tools, drilling pipe |
Chemical processing | Reactor vessels, heat exchanger tubing |
Power generation | Gas turbine hot section parts, fuel nozzles |
Automotive | Turbocharger turbines, exhaust components |
Marine | Desalination systems, propellers, fittings |
In particular, additive enables cost-effective short run production of custom Inconel 625 components.
Inconel 625 Powder Specifications
Table 6: Inconel 625 powder specifications
Parameter | Value |
---|---|
Purity | >99.9% |
Particle size | 15-45 microns |
Morphology | Highly spherical |
Phases | Solid solution γ-Ni + γ”-Ni3Nb |
Oxygen content | <300 ppm |
Apparent density | Typically >4 g/cm3 |
Flow rate | Hall flowmeter >23 sec/50g |
Tight control of powder quality and optimization for AM achieves dense printing and superior as-fabricated material performance.
Global Suppliers
Leading Inconel 625 powder suppliers for AM include:
Table 7: Inconel 625 powder manufacturers
Company | Location |
---|---|
Sandvik | Germany |
Praxair | United States |
Carpenter Additive | United States |
AP&C | Canada |
Erasteel | Sweden |
Tekna | Canada |
These premium specialists offer atomized Inconel 625 powder with controlled particle size, shape, chemistry, and defect population tailored for additive manufacturing applications.
Inconel 625 Powder Pricing
Table 8: Inconel 625 powder price dynamics
Parameter | Details |
---|---|
Quantity | Price per kg drops above ~50 kg |
Quality | Higher grades for AM cost 2-4x more than conventional powder |
Distribution | Tighter particle distributions more expensive |
Shape factors | High sphericity/smoothness increase price |
In general, Inconel 625 powder ranges from $50/kg to $150/kg for specialized varieties optimized for laser powder bed fusion or directed energy deposition printing.
Pros vs Cons of Inconel 625 Powder
Table 9: Inconel 625 powder advantages and challenges
Pros | Cons |
---|---|
Withstands extreme environments | Lower elongation/toughness than nickel alloys |
Five times more fracture resistant than steel | Susceptible to strain-age cracking |
Half the density of steel | Expensive compared to stainless steel |
Resists hot corrosion and pitting | Very high processing temperatures |
Custom alloy development possible | Tendency for porosity in AM parts |
Complex geometries from AM consolidation | Requires extensive post-processing |
Reduces lead times and cost for short runs | Limited large volume industrial suppliers |
With sound design and printing parameters, Inconel 625 enables lighter, stronger and more integrated components across demanding applications.
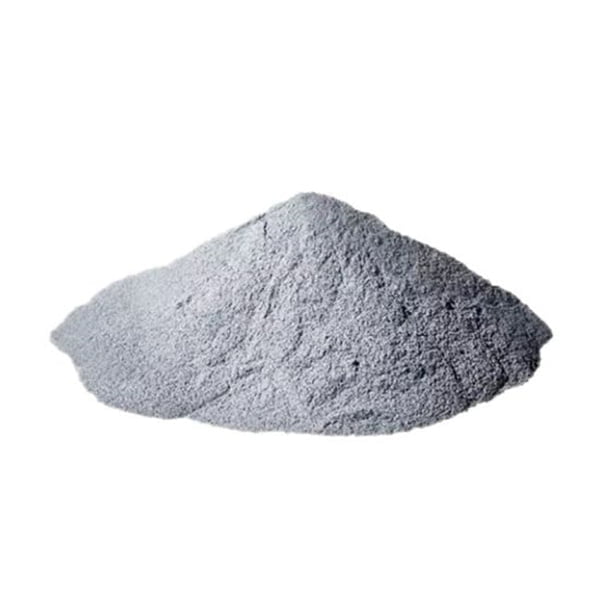
Frequently Asked Questions
Q: What particle size distribution is optimal for printing Inconel 625?
A: An Inconel 625 powder with particle sizes ranging from 15-45 microns allows high packing density and limits porosity during printing.
Q: What causes cracking in additively manufactured Inconel 625 parts?
A: Large residual stresses from the extreme thermal gradients during printing lead to cracking. Process optimizations like pre/post heating and providing structural supports are essential.
Q: What finish can be expected on as-printed Inconel 625 components?
A: Raw surface roughness typically ranges from 5-15 microns. Additional machining, grinding, electropolishing and other finishing produces smoother surfaces.
Q: What post-processing method is recommended for additive manufactured Inconel 625 parts?
A: Heat treatment, hot isostatic pressing, and surface conditioning are all recommended to relieve stresses, increase density, and improve surface finish.
Share On
MET3DP Technology Co., LTD is a leading provider of additive manufacturing solutions headquartered in Qingdao, China. Our company specializes in 3D printing equipment and high-performance metal powders for industrial applications.
Inquiry to get best price and customized Solution for your business!
Related Articles
About Met3DP
Recent Update
Our Product
CONTACT US
Any questions? Send us message now! We’ll serve your request with a whole team after receiving your message.
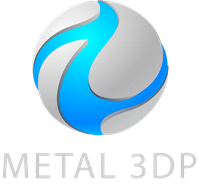
Metal Powders for 3D Printing and Additive Manufacturing