Inconel 718 Powder: Composition, Characteristics, Applications and Grades
Table of Contents
Inconel 718 powder is a nickel-chromium based alloy powder used primarily in additive manufacturing and metal powder bed fusion processes. This high-strength powder has excellent corrosion and heat resistance properties suited for aerospace, oil & gas, and industrial applications.
Overview of Inconel 718 Powder
Inconel 718 powder is a precipitation hardenable nickel-chromium alloy also known as NIMONIC PE16 or NiCr19Fe19Nb5Mo3. It offers a unique combination of properties like high yield, tensile and creep rupture strength, resistance to corrosion and oxidation, and hardenability.
This guide provides a detailed overview of Inconel 718 powder covering its composition and properties, product forms and sizes available, applications, grades meeting various specifications, major global suppliers, and typical pricing. Comparative analysis is presented in easy-to-use tables highlighting the advantages and limitations of this versatile superalloy powder.
Key Details of Inconel 718 Powder:
- Alloy system: Nickel-chromium
- Nickname: Superalloy 718
- Density: 8.19 g/cm3
- Melting point: 1260-1335°C
- Key features: High strength, hardness, weldability and machinability
- Common applications: Aerospace components like turbine blades, disciplined nozzles, cases and seals where heat and corrosion resistance is critical
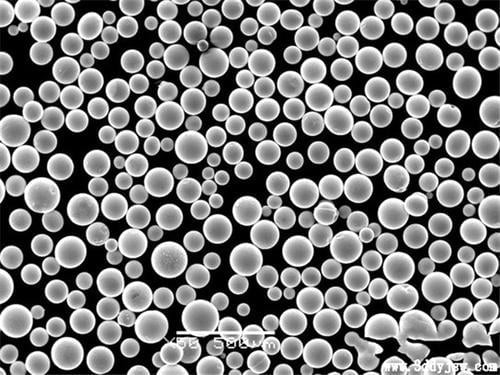
Composition and Properties of Inconel 718 Powder
The composition and microstructure of Inconel 718 powder results in a unique combination of properties making it suitable for high temperature applications.
Typical Composition (% Weight) of Inconel 718 Powder
Element | Min | Max |
---|---|---|
Nickel (Ni) | 50.00 | 55.00 |
Chromium (Cr) | 17.00 | 21.00 |
Iron (Fe) | Balance | 21.00 |
Niobium (Nb) | 4.75 | 5.50 |
Molybdenum (Mo) | 2.80 | 3.30 |
Titanium (Ti) | 0.65 | 1.15 |
Aluminum (Al) | 0.20 | 0.80 |
Cobalt (Co) | 1.00 | |
Copper (Cu) | 0.30 |
Key Properties of Inconel 718 Powder
Property | Value |
---|---|
Density | 8.19 g/cm3 |
Melting Range | 1260-1335°C |
Average Particle Size | 15-45 microns |
Oxygen Content | <0.1% |
Nitrogen Content | <0.1% |
Thermal Conductivity | 11.4 W/m-K |
Electrical Resistivity | 1.41 microohm-cm |
Young’s Modulus | 205 GPa |
Poisson’s Ratio | 0.294 |
Specific Heat | 435 J/kg-K |
Coefficient of Thermal Expansion | 12.8 μm/m-°C |
Tensile Strength | 1275 MPa (min) |
Key Characteristics and Benefits of Inconel 718 Powder:
- Retains strength and hardness at high operating temperatures
- Offers excellent resistance to oxidation and corrosion
- Provides good welding and machining characteristics
- Achieves high creep and rupture strength through precipitation hardening heat treatment
- Its high aluminum and titanium content result in formation of Ni3(Al, Ti) precipitates called gamma prime providing exceptional mechanical properties even above 650°C
Therefore, Inconel 718 is an attractive candidate for additive manufacturing technology like Direct Metal Laser Sintering (DMLS) to create strong, lightweight components for aircraft engines, power generation turbines, and process equipment used in harsh environments.
Applications and Uses of Inconel Powder
The unique combination of strength, fracture toughness, and corrosion resistance at elevated temperatures makes Inconel 718 suitable for a variety of critical applications across industries.
Typical Applications and Uses of Inconel 718 Powder
Industry | Components |
---|---|
Aerospace | Engine parts like blades, cases, fasteners where fatigue strength is critical |
Oil & Gas | Wellhead equipment, downhole tools for sour service environments |
Power Generation | Coal gasification heat exchangers, heat treating equipment |
Automotive | Turbocharger rotors, exhaust gas recirculation coolers |
Metalworking | Extrusion dies for reactive metals like titanium, hot-work tool steel inserts |
Additive Manufacturing | Laser powder bed fusion of fully dense functional metal parts with complex geometry |
The most common application is in aircraft engines to manufacture critical rotating parts like discs and fastener as well as cases and seals that must withstand sustained operation for long durations at temperatures approaching 700°C.
Over 50% of the wrought alloy market consumption goes into jet engine components highlighting the importance of Inconel 718 in aerospace. Additive manufacturing now allows lighter weight optimized geometries not possible with casting or forging.
Grades and Specifications of Inconel 718 Powder
Inconel 718 powder for AM processes must meet various international and regional standards for chemistry and particle size distribution. The common grades are listed below:
Standard Grades and Specifications of Inconel 718 Powder
Grade | Specification |
---|---|
Inconel 718 | AMS 5662, AMS 5664, AMS 5832 |
Inconel 718 | UNS N07718 |
Inconel 718 | W.Nr. 2.4668 |
Inconel 718 | DIN NiCr19Fe19NbMo3 |
These specifications impose strict control over the chemical composition and impurity levels. Custom alloys tailored for specific applications are also possible through minor adjustments of Nb, Ti, Al content.
All batches undergo rigorous quality testing to verify chemistry, particle size distribution, flow characteristics etc. before release. Common inspection methods include optical microscopy, SEM, energy dispersive X-ray spectroscopy etc.
Related metal powders for 3d printing:
Particle Size Distribution of Inconel 718 Powder
To achieve high density and mechanical integrity of 3D printed parts using Inconel 718, the powder particle size distribution (PSD) must meet certain thresholds.
Typical Particle Size Distribution Requirements of Inconel 718 Powder for DMLS Process
Particle Size (μm) | Distribution (%) |
---|---|
15 to 45 | ≥ 90% |
<15 | ≤ 10% |
45 to 105 | ≤ 10% |
>105 | ≤ 1% |
Finer atomization allows better flow and packing but reduces productivity. The average size is usually kept between 15-45 microns range for optimal print results. By adjusting gas flow dynamics, the powder maker can customize distributions shifting the peak within this range.
Global Suppliers of Inconel 718 Powder
Some of the major established suppliers manufacturing Inconel 718 powder for additive manufacturing globally are:
Key Suppliers and Manufacturers of Inconel 718 Powder
Company | Country |
---|---|
Sandvik Osprey | United Kingdom |
Carpenter Additive | United States |
Praxair | United States |
AP&C | Canada |
Erasteel | France |
Aubert & Duval | France |
SLM Solutions | Germany |
These players use inert gas atomization technique under protective atmosphere to produce fine Inconel 718 powder suitable for laser printing process. High purity single lot material optimized for flowability, apparent density and repeatable performance help achieve high quality metal parts.
Besides these large companies, several smaller regional players also offer custom made Inconel 718 powder. However quality certification and testing to validate chemistry and cleanliness may not be as robust.
Pricing Trends of Inconel 718 Powder
Price of Inconel 718 powder depends on quantity, quality grade, particle size distribution, supplier margins and geographical factors. Some typical pricing ranges are:
Indicative Pricing Ranges of Inconel 718 Powder
Quantity | Price per kg (USD) |
---|---|
1 kg | 800 – 1000 |
10 kg | 500 – 800 |
100 kg | 250 – 500 |
Economies of scale allow bulk orders to be cheaper on a per kg pricing basis. Small R&D quantities below 5 kg quantity may have higher pricing.
Within a fixed quantity, powder that meets more stringent specifications for impurities, particle size distribution authorized by aerospace standards commands higher prices. For e.g. AS9100 certified Inconel 718 powder with lot traceability is 25-30% more expensive. Location and shipping costs also impact end pricing.
Comparative Analysis of Inconel 718 Powder
Comparative Analysis of Properties Vs Competing Superalloy Powders
Properties | Inconel 718 | Inconel 625 | Hastelloy X | Waspaloy |
---|---|---|---|---|
Density (g/cm3) | 8.19 | 8.44 | 8.22 | 8.22 |
Melting Point (°C) | 1260-1335 | 1350 | 1260-1350 | 1315 |
Tensile Strength (MPa) | 1275 | 860 | 550 | 1110 |
Yield Strength (0.2% offset) | 1103 | 450 | 240 | 965 |
Elongation (%) | 19 | 35+ | N/A | 15 |
Young’s Modulus (GPa) | 205 | 207 | 196 | 186 |
Electrical Resistivity (μΩ-cm) | 1.41 | 1.41 | 1.16 | 1.73 |
Thermal Conductivity (W/m-K) | 11.4 | 9.8 | 11.4 | 18.4 |
Coefficient of Thermal Expansion (μm/m-°C ) | 12.8 | 12.8 | 12.4 | 13 |
Comparative Analysis of Costs
Parameters | Inconel 718 | Inconel 625 | Hastelloy X | Waspaloy |
---|---|---|---|---|
Relative Material Cost | High | Medium | High | Medium |
Manufacturability | Medium | High | Medium | Low |
Cost Effectiveness | Low | High | Low | Medium |
Pros and Cons Comparison
Inconel 718 | |
---|---|
Pros | – Retains strength at high operating temps – Excellent oxidation and corrosion resistance -Precipitation hardening improves strength -Good weldability and machinability -Higher strength than Inconel 625 -Used widely in aerospace engines |
Cons | – Heavy density compared to titanium alloys -Difficult to machine in hardened state -Relatively expensive -Lower thermal conductivity than waspaloy |
Inconel 718 strikes the optimal balance between high temperature strength, hardness, corrosion resistance and cost for critical parts operating at 500-700°C across mission-critical applications in extreme environments.
FAQs
Q: What is Inconel 718 Nickel Superalloy?
A: Inconel 718 (UNS N07718) nickel superalloy powder is a precipitation-hardenable alloy designed for extreme environments temperatures up to 700°C, requiring high yield, tensile, and creep-rupture properties combined with oxidation and corrosion resistance.
Q: What industries use Inconel 718 powder?
A: Key industries using Inconel 718 powder for additive manufacturing include aerospace for engine components, oil & gas well drilling tools, automotive turbocharger parts, metal extrusion dies, nuclear reactors, and chemical processing equipment.
Q: What particle size is used in AM processes?
A: For powder bed fusion techniques like DMLS, particle sizes between 15-45 microns are optimal, with <10% below 15 microns and <1% above 105 microns distribution most common.
Q: What are some alternatives to Inconel 718 powder?
A: Some alternatives include Inconel 625, Hastelloy X and Waspaloy powders which offer better cost effectiveness but compromise on high strength and hardness at operating temperatures above 600 °C making them unsuitable for aerospace applications.
Q: What standards does Inconel 718 comply with?
A: Common grades meeting international specifications are AMS 5662, AMS 5664, AMS 5832, UNS N07718, DIN 2.4668 for chemistry and particle size distribution.
Q: Is Inconel 718 powder reusable?
A: Yes, Inconel 718 unused powder can be reused after passing through a powder recycling system to separate out particles with satellites and checking chemistry. Savings between 20-30% can be realized using recycled powder.
Share On
MET3DP Technology Co., LTD is a leading provider of additive manufacturing solutions headquartered in Qingdao, China. Our company specializes in 3D printing equipment and high-performance metal powders for industrial applications.
Inquiry to get best price and customized Solution for your business!
Related Articles
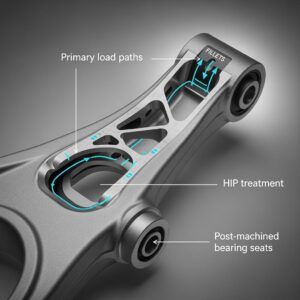
Metal 3D Printing for U.S. Automotive Lightweight Structural Brackets and Suspension Components
Read More »About Met3DP
Recent Update
Our Product
CONTACT US
Any questions? Send us message now! We’ll serve your request with a whole team after receiving your message.