Metal 3D Printing Powder
Table of Contents
Overview of metal 3d printing powder
Metal 3D printing powder refers to the raw material used in various metal additive manufacturing processes to produce three-dimensional metal parts layer by layer. Unlike traditional subtractive manufacturing that removes material, additive manufacturing builds up components by melting and fusing material together based on a digital 3D model.
Metal powders used in 3D printing enable the production of intricate, lightweight, and high-performance metal parts with complex geometries that are difficult or impossible to manufacture by conventional methods. The most common metal 3D printing technologies that utilize metal powders include:
- Direct Metal Laser Sintering (DMLS) – Uses a laser to selectively melt and fuse together layers of metal powder based on a 3D CAD model.
- Electron Beam Melting (EBM) – Uses an electron beam in a vacuum to melt and fuse powders together layer by layer.
- Binder Jetting – Liquid bonding agent is selectively deposited to join powder materials, which are later infused with bronze in a sintering furnace.
Metal 3D Printing Powder Types
Metal | Description | Properties | Applications |
---|---|---|---|
Stainless Steel | The most widely used metal powder in 3D printing due to its combination of affordability, corrosion resistance, and weldability. Common grades include 316L (marine grade), 17-4 PH (high strength and precipitation hardening), and 304 (general purpose). | – Excellent corrosion resistance – High strength – Good ductility – Biocompatible (certain grades) | – Aerospace components (non-critical) – Medical implants and devices – Chemical processing equipment – Automotive parts – Jewelry |
Titanium | A high-strength, low-weight metal prized for its biocompatibility and excellent strength-to-weight ratio. The most common alloy is Ti6Al4V (Titanium 6% Aluminum, 4% Vanadium). | – High strength-to-weight ratio – Excellent corrosion resistance – Biocompatible – High melting point | – Aerospace components (critical) – Biomedical implants (knee replacements, bone plates) – Marine components – Sporting goods (golf clubs, bicycles) |
Aluminum | A lightweight and affordable metal with good conductivity and machinability. Common alloys include 6061 (general purpose), 7075 (high strength), and 2024 (aerospace). | – Lightweight – Good conductivity – Excellent machinability – Recyclable | – Automotive parts (frames, wheels) – Aerospace components (non-critical) – Consumer electronics – Heat sinks |
Nickel Alloys | A class of high-performance alloys known for their exceptional heat resistance, corrosion resistance, and mechanical strength. Common varieties include Inconel 625 (outstanding resistance to harsh environments) and Inconel 718 (high strength at elevated temperatures). | – Exceptional heat resistance – Excellent corrosion resistance – High strength at elevated temperatures – Oxidation resistance | – Gas turbine engine components – Heat exchangers – Chemical processing equipment – Nuclear reactors |
Cobalt Chrome | A biocompatible alloy commonly used for its strength, corrosion resistance, and wear resistance. | – High strength – Excellent wear resistance – Good corrosion resistance – Biocompatible | – Biomedical implants (joint replacements, dental implants) – Cutting tools – Wear plates |
Tool Steels | A group of steels formulated for specific tooling applications such as cutting, forming, and shearing. Common types include H13 (hot work tool steel) and A2 (cold work tool steel). | – High hardness – Wear resistance – Dimensional stability – Toughness (depending on type) | – Cutting tools – Dies and molds – Punches and shears – Wear parts |
Precious Metals | Less common in metal 3D printing due to high cost, but offer unique properties such as high electrical conductivity, corrosion resistance, and biocompatibility. Examples include gold, silver, and platinum. | – High electrical conductivity – Excellent corrosion resistance – Biocompatible (certain types) – High reflectivity (depending on metal) | – Electrical connectors – Jewelry – Biomedical implants (limited use) – High-performance heat sinks |
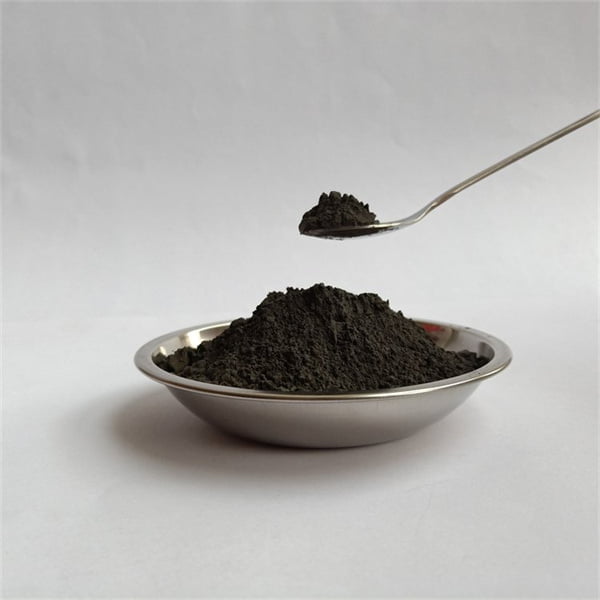
Metal Powder Production
Stage | Process | Description | Quality Control |
---|---|---|---|
Feedstock Acquisition | Material Selection | Selection of high-quality raw materials like titanium, steel, or aluminum alloys in various purities to meet desired final part properties. | Chemical composition analysis using techniques like X-ray fluorescence (XRF) or optical emission spectrometry (OES) |
** | Pre-processing** | Crushing and milling of bulk materials into smaller fragments to create a feedstock with a consistent particle size distribution suitable for further processing. | Particle size analysis using sieving or laser diffraction to ensure proper feedstock for atomization. |
Atomization | Gas Atomization** | Molten metal is injected into a high-pressure inert gas stream, creating a fine mist that rapidly cools and solidifies into spherical metal particles. | Particle size distribution, morphology (shape), and flowability analysis using laser diffraction and flowmeters to ensure optimal powder characteristics. |
** | Water Atomization** | Similar to gas atomization, but molten metal is injected into a high-pressure water stream. This method is generally used for less reactive metals like aluminum. | Similar quality control measures as gas atomization to ensure consistent particle properties. |
Post-Processing | Screening & Classification** | Powders are passed through sieves to remove oversized or undersized particles, achieving a narrow particle size distribution for optimal printing. | Particle size distribution analysis to verify adherence to desired particle size range. |
** | De-dusting & Cleaning** | Removal of impurities like oxides, moisture, and lubricants used during atomization to ensure high powder purity. | Chemical analysis techniques like XRF to measure oxygen content and ensure minimal surface contaminants. |
** | Spheroidization** | Optional step for certain applications. Powders undergo additional processing to improve their sphericity, leading to better flowability and printability. | Morphological analysis to assess particle roundness and ensure a high degree of sphericity. |
** | Vacuum Drying** | Removal of moisture trapped within the powder particles using a vacuum chamber to prevent defects during printing. | Karl Fischer titration to measure moisture content and ensure it falls within the acceptable range. |
** | Inert Gas Packaging** | Packing the finished powder in a sealed container filled with an inert gas like argon to minimize oxidation and maintain powder quality during storage and transportation. | Leak testing of containers and residual oxygen analysis to ensure proper packaging and minimal oxygen exposure. |
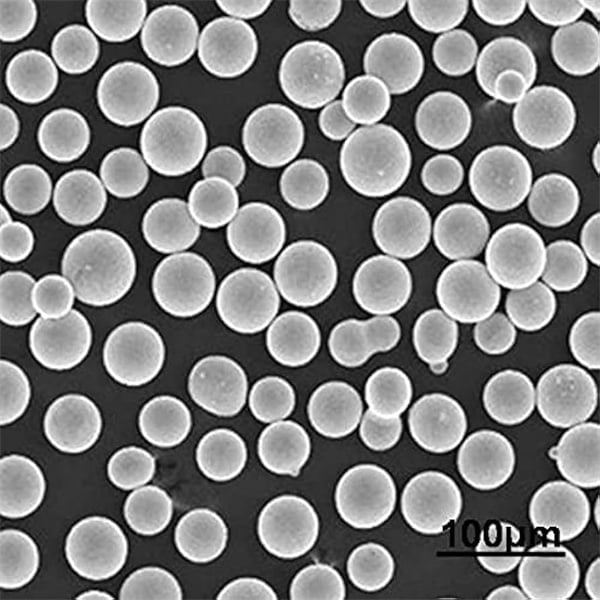
Metal Powder Attributes
Key powder attributes for 3D printing include:
Parameter | Description |
---|---|
Particle shape | Spherical, satellite, angular |
Particle size | Common range 10-100 microns |
Size distribution | Mix of fine and coarse particles |
Flowability | Ability of particles to flow under own weight |
Apparent density | Density as powder under normal conditions |
Tap density | Density after mechanical tapping/agitation |
Purity | Free of contaminants like oxides and nitrides |
Microstructure | Grain size, phase distribution, defects |
Moisture content | Must be kept low, in inert atmosphere |
Particle size and distribution directly impact powder flow, melting efficiency, surface quality, porosity, and mechanical properties. Finer sizes improve resolution while larger sizes reduce costs. A blend is ideal.
Powder shape and surface texture determine inter-particle friction, flowability, spreadability, and bulk density. Smooth, spherical powders flow and spread optimally with high packing density.
Controlling powder attributes and customizing alloys requires expertise in metallurgy, powder production, additive manufacturing processes, and materials science.
Applications of metal 3d printing powder
Industry | Application | Benefits | Material Considerations |
---|---|---|---|
Aerospace | Lightweight, high-strength components for aircraft (e.g., brackets, heat exchangers) Rocket engine parts Fuel injectors | Reduced weight for improved fuel efficiency Complex internal geometries for optimized performance Production of intricate lattice structures for heat dissipation | Titanium alloys for their exceptional strength-to-weight ratio and high-temperature performance Inconel for its ability to withstand extreme heat and pressure Aluminum alloys for lightweight structures in non-critical areas |
Medical | Customizable prosthetics and implants (e.g., hip replacements, dental crowns) Surgical instruments with improved ergonomics Biocompatible materials for bone regeneration scaffolds | Personalized medical devices that perfectly match patient anatomy Porous structures to promote bone ingrowth for better osseointegration Reduced need for invasive surgeries with patient-specific instrumentation | Titanium and tantalum for their biocompatibility and excellent osseointegration properties Stainless steel for its strength and corrosion resistance in certain applications Cobalt-chrome alloys for wear resistance in high-stress implants |
Automotive | Lightweight components for weight reduction and improved fuel economy (e.g., wheels, suspension parts) High-performance engine components Customizable racing parts | Design freedom for complex geometries that enhance performance Rapid prototyping for faster design iteration Production of limited-edition or one-off parts | Aluminum alloys for lightweight structures with good strength Titanium alloys for high-strength components in high-stress applications Nickel alloys for their ability to withstand extreme temperatures and pressures |
Consumer Goods | Luxury jewelry and bespoke design pieces Limited-edition sporting goods Customizable consumer electronics components | Production of intricate and unique designs Reduced waste compared to traditional subtractive manufacturing Mass customization for personalized products | Precious metals like gold, silver, and platinum for high-value jewelry Stainless steel and aluminum alloys for durable consumer goods Copper for its aesthetic appeal and thermal conductivity in electronics |
Energy | * Components for heat exchangers and reactors * Additive manufacturing of complex turbine blades * Production of customized parts for oil and gas exploration | * High-performance materials for use in demanding environments * Lightweight structures for improved efficiency * Design freedom for optimizing heat transfer and fluid flow | Nickel alloys for their exceptional high-temperature strength and corrosion resistance Stainless steel for its durability and resistance to harsh conditions Inconel for its ability to withstand extreme heat and pressure in nuclear applications |
metal 3d printing powder Suppliers
There are several leading global suppliers that manufacture standard and custom metal powders specifically for 3D printing:
Supplier | Headquarters | Powder Materials |
---|---|---|
Sandvik | Sweden | Stainless steels, nickel alloys, titanium alloys, tool steels |
Carpenter Additive | USA | Stainless steels, cobalt chrome, copper, nickel alloys |
Praxair | USA | Titanium, nickel superalloys, stainless steel |
GKN Powder Metallurgy | USA | Stainless steels, titanium, aluminum alloys |
LPW Technology | UK | Titanium alloys, aluminum alloys, stainless steels |
Supplier capability to customize alloy chemistry, modify powder characteristics, ensure batch-to-batch consistency, and collaborate on part quality are important factors in powder sourcing decisions.
Metal Powder Costs
Metal Type | Price Range (USD per kg) | Common Applications | Key Considerations |
---|---|---|---|
Standard Metals | $50 – $100 | * Aluminum (AlSi10Mg) * Stainless Steel (316L) * Titanium (Ti6Al4V) | * Generally cost-effective options for prototypes and low-stress parts. * Aluminum offers good strength-to-weight ratio and machinability. * 316L stainless steel is known for its corrosion resistance. * Ti6Al4V finds use in aerospace and medical sectors due to its biocompatibility and high strength-to-weight ratio. |
High-Performance Metals | $300 – $600 | * Nickel Superalloys (Inconel 625) * Cobalt Chrome (CoCr) * Tool Steel (H13) | * Targeted for applications requiring exceptional mechanical properties at high temperatures or wear resistance. * Inconel 625 is an aerospace workhorse due to its ability to withstand extreme temperatures and maintain strength. * CoCr is popular in medical implants due to its biocompatibility and high strength. * H13 is a go-to for tooling applications due to its exceptional hardness and wear resistance. |
Precious Metals | $1,000 – $50,000+ | * Gold * Silver * Platinum | * Primarily used for aesthetic or high-value applications in jewelry, electronics, and aerospace. * Gold offers excellent electrical conductivity and corrosion resistance. * Silver is known for its antimicrobial properties and high thermal conductivity. * Platinum finds use in high-temperature crucibles and electrical contacts due to its melting point and resistance to corrosion. |
Rare Earth Metals | Contact Vendor | * Yttrium * Neodymium * Erbium | * Limited availability and unique properties drive up costs. * Yttrium finds use in solid-state lasers and superconductors. * Neodymium is a key component in high-powered magnets. * Erbium is used in fiber optic amplifiers and lasers. |
Metal Powder Specifications
Industry standards are evolving on specifications, test methods and powder certification:
Standard | Organization | Scope |
---|---|---|
ASTM F3049 | ASTM International | Standard guide for characterizing metal powders for AM |
ASTM F3056 | ASTM International | Specification for additive manufacturing nickel alloy |
AS9100 rev D | SAE International | Aerospace quality management systems |
ISO/ASTM 52900 | ISO/ASTM | Standard terminology for AM – General principles |
ISO/ASTM 52921 | ISO/ASTM | Standard for metal powders used in DMLS/SLM |
Key powder properties like particle size distribution, flow rate, density, and composition are tested as per these specifications. Customers may require additional testing data, batch analysis reports, and compliance certificates from metal powder manufacturers.
Pros and Cons of Metal 3D Printing Powders
Feature | Pros | Cons |
---|---|---|
Design Freedom | * Enables intricate geometries impossible with traditional methods. * Creates lightweight structures with internal lattices for superior strength-to-weight ratio. * Allows for on-demand customization of parts. | * Limited only by the printer’s build volume and software capabilities. |
Material Properties | * Wide range of metal powders available, each with unique properties like high strength, heat resistance, or biocompatibility. * Parts can achieve properties comparable to traditionally manufactured metals. | * Powder characteristics can affect printability and final product quality. * Some high-performance metals require specialized printing environments. |
Production Efficiency | * Reduces waste compared to subtractive manufacturing techniques. * Enables production of complex parts in a single step, eliminating the need for assembly. * Shortens lead times for prototyping and low-volume production runs. | * Not suitable for mass production due to slower printing speeds and higher material costs. * Requires careful post-processing to achieve desired surface finish and dimensional accuracy. |
Safety | * Certain metal powders can be hazardous due to flammability or toxicity. * Requires proper handling procedures and personal protective equipment (PPE) to minimize risks. | * Bound metal filaments offer a safer alternative for some applications. * Advancements in powder handling technologies are improving safety. |
Cost | * High initial investment for metal 3D printers and powder materials. * Ongoing costs associated with powder handling, maintenance, and waste disposal. | * Can be cost-effective for complex parts or small production runs compared to traditional methods. * Potential for reduced labor costs and streamlined production workflows. |
Environmental Impact | * Reduced material waste compared to subtractive manufacturing. * Potential for on-demand production, minimizing excess inventory and transportation needs. | * Energy-intensive printing process can have a higher environmental footprint. * Disposal of waste powder requires proper handling to minimize environmental impact. |
The Future of Metal 3D Printing Powders
Key trends shaping the future roadmap for metal powders:
New alloys: More alloy choices matching properties of forged aluminum and titanium will expand adoption in structural components. R&D is ongoing on high strength steels, copper alloys and precious metals.
Improved powders: Tighter controls on size distribution, shape and microstructure will lead to powders tailored for specific AM processes and applications. This enhances quality and material properties.
Recycling systems: Cross-industry infrastructure to collect, characterize and reuse metal powders in a closed-loop will make 3D printing more sustainable.
Automated workflows: Streamlined workflows for powder handling using containers, sensors and automated guided vehicles will improve safety, consistency and productivity.
Certification infrastructure: Centralized institutes providing powder certification and part qualification services will instill confidence in critical industries like medical and aerospace to adopt AM.
Specialization: System manufacturers, metal powder producers, part buyers, software companies and material scientists specializing in niche aspects of the AM value chain will drive focused innovation.
Cost reduction: Approaches like bulk powder manufacturing, standardized alloys, automated post-processing and digital inventory management will improve economics.
With continued progress across these areas, industrialization and mainstream adoption of metal 3D printing is poised for strong growth over the next decade across several key markets.
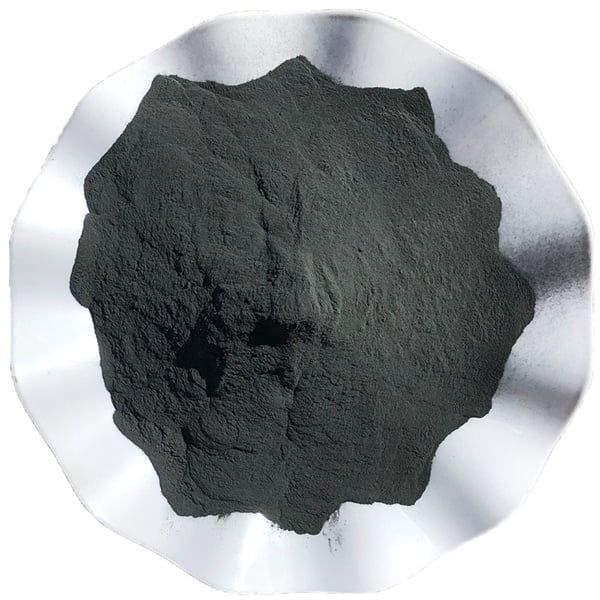
FAQ
Q: What is the most commonly used metal powder in 3D printing?
A: 316L stainless steel is the most widely used metal powder today due to its good mechanical properties, weldability and corrosion resistance. Other popular options are titanium Ti64 and aluminum AlSi10Mg.
Q: How to choose the right metal powder for an application?
A: Key considerations are operating temperature, corrosion resistance, wear resistance, part strength, weight requirements, conductivity needs, biocompatibility, food contact status and post-processing constraints. Discuss application details with powder manufacturers for alloy recommendations.
Q: Does using finer metal powder improve part quality?
A: Finer powders (~10-45 microns) improve resolution, surface finish and precision because thinner layers can be fused. But this lowers build speeds and increases costs. Mixing fine and coarse particles offers a balanced approach.
Q: How are metal powders kept safe and free of contamination during storage and handling?
A: Metal powders are high reactive and prone to oxidation. Moisture absorption degrades powder quality over time as well. So inert gas atmospheres, vacuum storage, sealed containers and minimal oxygen/water exposure with automated powder handling are essential.
Q: Can metal powders be reused to reduce material costs in 3D printing?
A: Yes, but reuse comes with strings attached. Unused powder can be reused but extensive testing is needed to check for contamination, variations in particle size distribution or composition during multiple cycles. Such characterization adds costs and risks.
Share On
MET3DP Technology Co., LTD is a leading provider of additive manufacturing solutions headquartered in Qingdao, China. Our company specializes in 3D printing equipment and high-performance metal powders for industrial applications.
Inquiry to get best price and customized Solution for your business!
Related Articles
About Met3DP
Recent Update
Our Product
CONTACT US
Any questions? Send us message now! We’ll serve your request with a whole team after receiving your message.
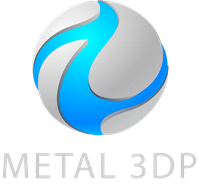
Metal Powders for 3D Printing and Additive Manufacturing