Metal Additive Manufacturing (MAM)
Table of Contents
Metal Additive Manufacturing (MAM) is revolutionizing the manufacturing industry by offering unparalleled design freedom, efficiency, and customization. This cutting-edge technology, also known as 3D printing, uses metal powders to create complex and precise parts layer by layer. In this comprehensive guide, we’ll delve into the intricacies of MAM, exploring its types, applications, specifications, advantages, disadvantages, and more.
Overview of Metal Additive Manufacturing (MAM)
Metal Additive Manufacturing (MAM) represents a significant shift from traditional manufacturing methods. It involves the creation of three-dimensional objects by adding material layer by layer, based on digital models. This process allows for the production of complex geometries that would be impossible or highly inefficient to achieve through conventional techniques.
Key Details of MAM
- Process: Layer-by-layer addition of material
- Materials: Various metal powders (e.g., titanium, stainless steel, aluminum)
- Technology: Includes Selective Laser Melting (SLM), Electron Beam Melting (EBM), and Binder Jetting
- Applications: Aerospace, automotive, medical implants, tooling, and more
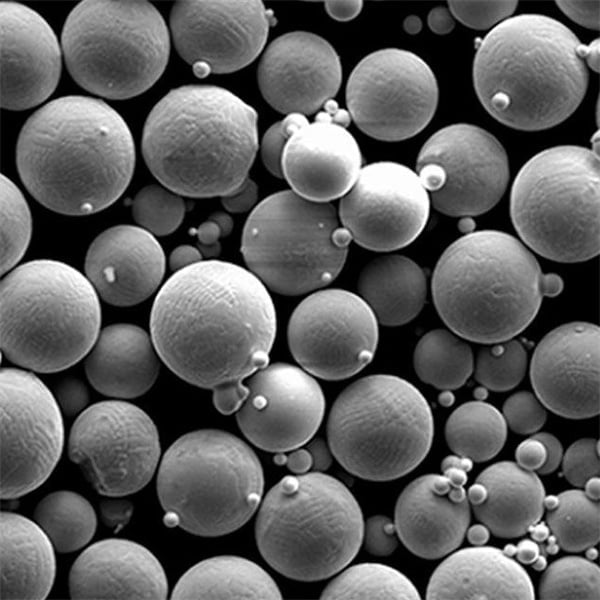
Types of Metal Additive Manufacturing Technologies
Metal Additive Manufacturing encompasses several distinct technologies, each with its unique characteristics and advantages. Let’s explore some of the primary types:
Selective Laser Melting (SLM)
SLM uses a high-power laser to selectively melt and fuse metal powders. This technology is known for its high precision and ability to produce dense, strong parts.
Electron Beam Melting (EBM)
EBM employs an electron beam to melt metal powders in a vacuum. It is particularly effective for producing parts with high mechanical properties and is commonly used in aerospace applications.
Binder Jetting
Binder Jetting involves the deposition of a liquid binding agent onto a bed of metal powder. The resulting “green” part is then sintered to create a solid metal component. This technology is ideal for producing large batches of parts with complex geometries.
Directed Energy Deposition (DED)
DED uses a focused energy source, such as a laser or electron beam, to melt metal powders or wires as they are deposited. This technology is highly versatile and can be used for repair and refurbishment applications.
Specific Metal Powder Models for MAM
Different metal powders are used in MAM, each offering unique properties suitable for various applications. Here are ten specific metal powder models:
Metal Powder | Description |
---|---|
Titanium Ti6Al4V | Widely used in aerospace and medical industries for its excellent strength-to-weight ratio and biocompatibility. |
Stainless Steel 316L | Known for its corrosion resistance, making it ideal for marine and chemical processing applications. |
Inconel 718 | A nickel-chromium alloy that maintains high strength and corrosion resistance at elevated temperatures. |
Aluminum AlSi10Mg | Lightweight and strong, commonly used in automotive and aerospace sectors. |
Cobalt-Chrome | Offers high wear resistance and is used in dental and orthopedic implants. |
Tool Steel H13 | Used for high-temperature applications and tooling due to its excellent hardness and toughness. |
Copper | Known for its thermal and electrical conductivity, suitable for heat exchangers and electrical components. |
Maraging Steel | Combines high strength and toughness, used in tooling and aerospace components. |
Nickel Alloy 625 | Corrosion and oxidation-resistant, used in marine and chemical industries. |
Tungsten | Extremely dense and heat-resistant, used in aerospace and defense applications. |
Applications of Metal Additive Manufacturing (MAM)
Metal Additive Manufacturing is transforming various industries by enabling the production of complex, customized, and high-performance parts. Here are some of the key applications:
Industry | Applications |
---|---|
Aerospace | Turbine blades, fuel nozzles, lightweight structural components |
Automotive | Engine components, custom brackets, lightweight structural parts |
Medical | Implants (e.g., hip and knee), dental prosthetics, surgical instruments |
Tooling | Injection molds, cutting tools, conformal cooling channels |
Defense | Lightweight armor, weapon components, unmanned aerial vehicle (UAV) parts |
Energy | Heat exchangers, turbine components, offshore drilling equipment |
Industrial | Custom jigs and fixtures, spare parts, complex machinery components |
Consumer Goods | Custom jewelry, eyewear, fashion accessories |
Specifications, Sizes, Grades, and Standards
Metal powders used in MAM come in various specifications, sizes, grades, and standards. Understanding these parameters is crucial for selecting the right material for a specific application.
Specifications of Metal Powders
Parameter | Description |
---|---|
Particle Size | Typically ranges from 15 to 45 microns, affecting the resolution and surface finish of printed parts. |
Chemical Composition | Must meet specific alloy standards (e.g., ASTM, ISO) to ensure material properties and performance. |
Purity | High purity levels (99.9% or higher) are required to avoid defects and ensure consistent performance. |
Flowability | Influences the powder’s ability to spread evenly during the printing process. |
Density | Affects the final part’s density and mechanical properties. |
Moisture Content | Low moisture content is essential to prevent oxidation and ensure powder stability. |
Sizes and Grades of Metal Powders
Metal Powder | Available Sizes (Microns) | Grades | Standards |
---|---|---|---|
Titanium Ti6Al4V | 20-40, 15-45 | Grade 5, Grade 23 | ASTM F2924, ISO 5832-3 |
Stainless Steel 316L | 15-45 | 316L, 1.4404 | ASTM A276, ISO 5832-1 |
Inconel 718 | 20-40 | UNS N07718, W.Nr. 2.4668 | ASTM B637, AMS 5662 |
Aluminum AlSi10Mg | 20-63 | – | DIN EN 1706 |
Cobalt-Chrome | 20-53 | CoCrMo, CoCrW | ASTM F75, ISO 5832-4 |
Tool Steel H13 | 15-45 | H13, 1.2344 | ASTM A681 |
Copper | 15-45 | OFHC, C11000 | ASTM B170 |
Maraging Steel | 20-45 | 18Ni300 | ASTM A538 |
Nickel Alloy 625 | 15-45 | UNS N06625, W.Nr. 2.4856 | ASTM B443, AMS 5599 |
Tungsten | 20-45 | – | ASTM B777 |
Suppliers and Pricing Details
Finding reliable suppliers and understanding the pricing of metal powders is crucial for implementing MAM effectively. Here’s a look at some key suppliers and the typical pricing range:
Supplier | Metal Powders | Pricing (per kg) |
---|---|---|
Höganäs | Stainless Steel, Tool Steel, Nickel Alloys | $50 – $300 |
GKN Additive | Titanium, Aluminum, Stainless Steel | $100 – $400 |
LPW Technology | Inconel, Maraging Steel, Cobalt-Chrome | $200 – $600 |
Sandvik | Titanium, Stainless Steel, Nickel Alloys | $150 – $500 |
AP&C (GE Additive) | Titanium, Aluminum, Inconel | $200 – $700 |
Carpenter Additive | Tool Steel, Stainless Steel, Nickel Alloys | $150 – $450 |
EOS | Titanium, Stainless Steel, Aluminum | $200 – $600 |
Renishaw | Stainless Steel, Tool Steel, Titanium | $100 – $500 |
Carpenter Technology | Maraging Steel, Nickel Alloys, Titanium | $250 – $650 |
Metco | Copper, Tungsten, Stainless Steel | $80 – $400 |
Advantages and Disadvantages of Metal Additive Manufacturing (MAM)
Like any technology, Metal Additive Manufacturing has its pros and cons. Understanding these can help in making informed decisions about its adoption and implementation.
Advantages of MAM
Advantage | Description |
---|---|
Design Flexibility | Allows for the creation of complex geometries that are impossible with traditional manufacturing methods. |
Material Efficiency | Uses only the material necessary for the part, reducing waste. |
Customization | Enables the production of customized parts tailored to specific needs. |
Reduced Lead Times | Shortens the time from design to production, accelerating product development cycles. |
On-Demand Production | Facilitates just-in-time manufacturing, reducing inventory costs. |
Lightweight Structures | Produces parts with optimized weight without compromising strength. |
Disadvantages of MAM
Disadvantage | Description |
---|---|
High Initial Costs | The cost of MAM equipment and materials can be significant. |
Material Limitations | Not all metals are suitable for additive manufacturing. |
Surface Finish | Parts often require post-processing to achieve the desired surface finish. |
Size Constraints | The build volume of MAM machines is limited, restricting the size of parts that can be produced. |
Technical Expertise | Requires specialized knowledge and skills to operate and maintain the equipment. |
Comparing Metal Additive Manufacturing Technologies
Let’s compare some of the primary MAM technologies based on key parameters:
Parameter | SLM | EBM | Binder Jetting | DED |
---|---|---|---|---|
Precision | High | Moderate | Moderate | Moderate |
Material Density | High | High | Lower | High |
Surface Finish | Good | Moderate | Poor | Moderate |
Build Speed | Moderate | High | High | Moderate |
Suitable Materials | Wide range | Limited to conductive metals | Wide range | Wide range |
Cost | High | High | Lower | High |
Typical Applications | Aerospace, medical | Aerospace, medical | Industrial, automotive | Repair, refurbishment |
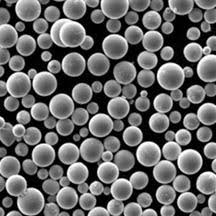
Conclusion
Metal Additive Manufacturing (MAM) is a transformative technology with the potential to revolutionize various industries by offering unparalleled design freedom, efficiency, and customization. With advancements in materials and processes, MAM continues to push the boundaries of what is possible in manufacturing. Whether you’re looking to produce complex aerospace components, customized medical implants, or efficient tooling, MAM offers a versatile and efficient solution.
FAQ
What is Metal Additive Manufacturing (MAM)?
Metal Additive Manufacturing (MAM) is a process that creates three-dimensional metal parts by adding material layer by layer based on digital models. This technology allows for the production of complex geometries and customized parts that are difficult or impossible to achieve with traditional manufacturing methods.
What are the main types of MAM technologies?
The main types of MAM technologies include Selective Laser Melting (SLM), Electron Beam Melting (EBM), Binder Jetting, and Directed Energy Deposition (DED). Each technology has its unique characteristics, advantages, and applications.
What are some common metal powders used in MAM?
Common metal powders used in MAM include Titanium Ti6Al4V, Stainless Steel 316L, Inconel 718, Aluminum AlSi10Mg, Cobalt-Chrome, Tool Steel H13, Copper, Maraging Steel, Nickel Alloy 625, and Tungsten.
What industries benefit from MAM?
Industries that benefit from MAM include aerospace, automotive, medical, tooling, defense, energy, industrial, and consumer goods. MAM enables these industries to produce complex, high-performance, and customized parts efficiently.
What are the advantages of MAM?
Advantages of MAM include design flexibility, material efficiency, customization, reduced lead times, on-demand production, and the ability to create lightweight structures without compromising strength.
What are the disadvantages of MAM?
Disadvantages of MAM include high initial costs, material limitations, the need for post-processing to achieve desired surface finishes, size constraints of parts, and the requirement for specialized technical expertise.
How do I choose the right metal powder for MAM?
Choosing the right metal powder for MAM depends on factors such as the desired mechanical properties, chemical composition, particle size, purity, and application requirements. Consulting with suppliers and understanding the specific needs of your project can help in selecting the appropriate material.
What are the costs associated with MAM?
The costs associated with MAM include the price of metal powders, which can range from $50 to $700 per kilogram depending on the material, as well as the costs of MAM equipment, maintenance, and post-processing. Initial setup costs can be high, but MAM can offer long-term savings through material efficiency and reduced lead times.
Can MAM be used for large-scale production?
MAM is typically used for small to medium-scale production, prototyping, and customized parts. While it offers advantages in terms of design flexibility and efficiency, it may not always be cost-effective for large-scale production compared to traditional manufacturing methods.
What is the future of Metal Additive Manufacturing?
The future of Metal Additive Manufacturing is promising, with ongoing advancements in materials, processes, and technology. As MAM continues to evolve, it is expected to become more accessible, cost-effective, and widely adopted across various industries, driving innovation and enabling new possibilities in manufacturing.
Share On
MET3DP Technology Co., LTD is a leading provider of additive manufacturing solutions headquartered in Qingdao, China. Our company specializes in 3D printing equipment and high-performance metal powders for industrial applications.
Inquiry to get best price and customized Solution for your business!
Related Articles
About Met3DP
Recent Update
Our Product
CONTACT US
Any questions? Send us message now! We’ll serve your request with a whole team after receiving your message.
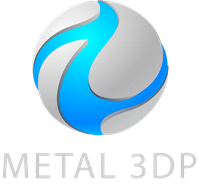
Metal Powders for 3D Printing and Additive Manufacturing