MIM Metal Powder
Table of Contents
Metal injection molding, or MIM metal powder, is a manufacturing process gaining popularity for its ability to produce complex, high-precision metal parts in high volumes. At its core, the MIM process utilizes a feedstock consisting of fine metal powder particles mixed with a binder material. When injected into a mold, this feedstock allows intricate shapes to be formed that would be difficult or impossible with other metalworking techniques.
The key ingredient that makes MIM viable is the specialized MIM metal powder used. This powder, usually less than 20 microns in particle size, provides the metal content of the final part. However, not all metal powders work well for MIM. The characteristics of the powder such as composition, particle size distribution, morphology, flow rate, and purity can impact the injection molding process and properties of finished components.
This guide takes an in-depth look at MIM metal powders—what they are, how they work, and how to select the right one. It covers everything from powder production methods, classifications, and industry standards to how composition and powder attributes affect MIM feedstock behavior and part qualities. Read on for an comprehensive overview of this integral MIM raw material.
MIM metal powder Composition
The MIM process accommodates a wide range of metals and alloys as the powder base material. Each offers different properties from high strength steels to shape memory alloys. Common categories include:
Metal or Alloy | Key Characteristics |
---|---|
Stainless steels | Corrosion resistance, high strength, some magnetic properties |
Tool steels | Very high hardness and wear resistance |
Low alloy and carbon steels | Magnetic properties, heat treatability, lower cost |
Copper alloys | High thermal and electrical conductivity |
Tungsten heavy alloys | Extremely high density, vibration damping |
Shape memory alloys | Transformational shape change, biocompatibility |
Precious metals | Corrosion resistance, high conductivity, aesthetic qualities |
Table: Common MIM metal powder compositions and their notable qualities
The specific chemical composition is a key factor determining the properties and performance of the final MIM part. As such, powder manufacturers closely control compositions to tighten tolerances.
Common elements alloyed with base metals like iron, nickel, and cobalt serve various purposes:
- Chromium, molybdenum, vanadium – increase strength, toughness, wear resistance
- Carbon, boron, titanium – enhance hardenability through heat treatment
- Nickel, manganese – modulate transformation temperatures
- Copper – improves conductivity and corrosion resistance
- Tungsten, tantalum – substantially increase density
The flexibility of MIM allows designers to optimize properties like stiffness, hardness, or electrical resistivity for their particular application through careful material selection.
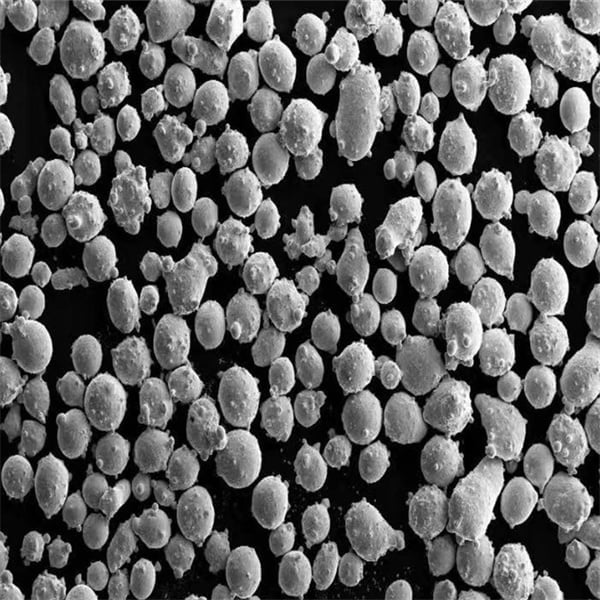
MIM metal powder Production Methods
Several mature methods exist for producing metallic powders on the scale and precision necessary for MIM. The two most prominent routes are:
Process | Description | Typical Materials | Cost Level |
---|---|---|---|
Gas atomization | Molten metal stream disintegrated by high pressure inert gas jets into fine droplets that solidify into powder | Most common method for MIM; wide alloy range including steels, superalloys, tool steels, precious metals | Higher cost |
Water atomization | Molten metal stream disintegrated into droplets by high pressure water jets; less control over particle size distribution | Less common for MIM; typically lower-alloy materials like carbon steels | Lower cost |
Electrolytic | Metal cations in electrolyte solution are deposited onto cathode and collected as powder; particle attributes highly controllable | Used for copper, iron, and cobalt powders | Moderate cost |
Carbonyl | Thermal decomposition of metal carbonyl vapor results in pure metallic powder formation | High-purity nickel, iron, and cobalt | Higher cost |
Table: Comparison of common commercial MIM metal powder production routes
Secondary processing such as annealing, crushing, sieving, and mixing are used to achieve target particle size distribution, morphology, and other properties. Ready-to-use MIM powders are highly spherical with controlled microstructure tailored to alloy and application.
MIM metal powder Particle Size
A defining quality of MIM feedstock is the fine particle size necessary to achieve high sintered density and complex geometry formation. For stainless steel 17-4PH, a common MIM alloy, the particle size distribution chart below depicts the typical range:
Typical particle size distribution for gas-atomized 17-4PH stainless steel per MPIF Standard 35
Key takeaways:
- Over 90% of particles fall between 1-20 microns
- Median particle size between 4-5 microns
- Powders outside this distribution may cause molding or sintering defects
Controlling particle size is crucial for powder flow and packing density during injection. Ultrafine particles can be cohesive and agglomerate, while large particles cause wall friction and uneven binder distribution. MIM powders must balance these factors.
MIM Metal Powder Morphology
In addition to controlling size on a microscopic scale, powder shape and surface structure are also vital. Gas atomization produces highly spherical, smooth powders optimal for MIM feeding.
Comparatively, water atomized particles, while more irregular, can offer better interparticle friction and green strength. Blends of powder morphologies are sometimes utilized.
Micrographs comparing common MIM powder morphologies
Considerations around powder morphology:
- Smooth, spherical particles improve flow rates through molding equipment
- Rougher particles with satellites can mechanically interlock to boost green strength
- Irregular shapes make particles more cohesive and prone to agglomeration
The feedstock formulator selects an optimal balance between powder flow and binder adhesion based on final part needs.
MIM Metal Powder Standards
Globally adopted standards help define quality metrics and test procedures for metal powders. They allow powders to be reliably compared between suppliers. Some notable ones include:
- MPIF Standard 35 – Covers particle size characterization, hall flow rate, tap density, and more for MIM powders
- ASTM B833 – Guide for powder metallurgy tool steels suitable for MIM processing
- ISO 22068 – Specifies requirements for stainless steel powders for MIM
Reputable powder vendors test every powder lot and provide documentation showing conformance. These data sheets give the MIM feedstock formulator a baseline to qualify new materials.
How Powder Properties Affect MIM Processing
A powder’s composition and attributes can significantly impact each stage of MIM – from molding behavior to final material properties after sintering.
Injection Molding Effects
Powder characteristics that influence injection molding performance
Details on how each factor affects mold filling and green part quality:
- Particle size – Ultrafine powders resist flow and cause molding defects. Overly coarse particles create binder segregation issues.
- Morphology – Smooth, spherical particles enhance flow through feed systems. Satellite particles increase friction but boost green strength.
- Tap density – Higher density improves particle packing and reduces binder volume needed.
- Hall flow rate – Measures time for 50g of powder to flow through standardized funnel. Flow rates under 30 seconds signal cohesion problems.
- Chemistry – Alloy composition influences melting temperature, apparent density, surface tension with binder.
Sintering Behavior
During sintering, the binder is first removed from the molded (“green”) part before thermal processes fuse the metallic particles into a dense structure. Powder attributes like particle size, purity, oxide levels, and alloy chemistry affect these mechanisms.
Powder Property | Sintering Influence |
---|---|
Particle size distribution | Too many ultrafine particles hinder interparticle bonding and densification |
Impurity levels | Impurities impair interparticle bonding and lead to defects |
Oxygen/nitrogen levels | Excessive oxide or nitride phases inhibit densification |
Alloy content | Affects liquid phase formation, sintering kinetics, microstructural evolution |
Table: How powder characteristics impact sintering behavior and final part qualities
Through long experience, powder producers select parameters optimized for MIM processing of each alloy system while meeting cost targets.
Grades of MIM metal powder
For common MIM alloys like 316L stainless steel and 17-4PH precipitation hardened stainless, multiple powder grades are offered catering to different applications:
Grade | Characteristics | Typical Applications |
---|---|---|
Standard | Fully qualified MIM powder meeting size and chemistry specifications | High volume applications not requiring stringent mechanical properties |
High Performance | Additional screening for surface quality; lower oxide content; tighter particle size control | Applications requiring higher strength, ductility, and impact resistance |
Plasma Spheroidized | Further processing to achieve extremely smooth, spherical morphology | Components with thin walls, fine features, tight dimensional control |
Table: Comparison of 316L stainless steel MIM powder grades
Higher grade powders typically enable thinner walls, finer details, better tolerances and mechanical performance to be reached. This comes at a higher powder cost, so standard grades are used for high volume, moderate property applications to control component price.
MIM Metal Powder Pricing
As a specialized material requiring extensive processing, MIM powders demand a premium over standard metal powders for applications like powder metallurgy pressing and additive manufacturing.
Material | Powder Grade | Cost per kg |
---|---|---|
316L Stainless Steel | Standard | $50-60 |
316L Stainless Steel | High Performance | $65-75 |
17-4PH Stainless Steel | Standard | $65-80 |
17-4PH Stainless Steel | High Performance | $90-110 |
Table: Example pricing ranges for common MIM metal powders
To offset higher powder expenses, MIM targets small complex components with economical high volume production. Part miniaturization and design consolidation also improve cost structure.
Factors influencing MIM powder pricing:
- Base alloy cost – precious metals highest, commodity alloys lowest
- Production method – water atomization lower cost than gas atomization
- Additional screening and quality control steps
- Purchase volume – wholesale pricing enables volume discounts
- Market dynamics – raw material and energy pricing fluctuations cause price variability
MIM Metal Powder Handling
To prevent contamination and maintain flow characteristics, MIM powders must be properly handled:
- Store sealed powders in a cool, dry, inert environment to minimize oxidation
- Avoid direct sunlight or UV radiation to prevent microstructural damage
- Handle and transport containers with care; use grounded equipment to prevent static charge buildup
- Pour and transfer using inert atmosphere glove boxes whenever possible
- Before usage, mix containers thoroughly to redistribute particle sizes and prevent segregation
Powders that exceed shelf life or become contaminated must not be used for feedstock, as they will degrade part properties. Always follow supplier recommendations for proper powder handling.
MIM Metal Powder Suppliers
Several major corporations have become market leaders by specializing in gas-atomized metal powder production on the scale required by MIM feedstock manufacturers. Notable MIM powder vendors include:
Company | Headquarters | MIM Portfolio |
---|---|---|
Sandvik Osprey | Neath, UK | Wide alloy range; high cleanliness standards |
Carpenter Powder Technology | Pittsburgh, USA | Narrow size distributions; high tap densities |
Höganäs | Höganäs, Sweden | Broad alloy selection; high purity standards |
Atmix Corp | Japan | Focus on stainless, tool and alloy steels |
Table: Major global suppliers of specialty MIM metal powders
Reputable suppliers manufacture powders under tight quality control and perform extensive product testing to ensure batch-to-batch consistency. Long term partnerships between powder producer and MIM feedstock formulator are typical.
Frequently Asked Questions
What is the most common metal powder used for MIM feedstocks?
The workhorse of MIM is stainless steel, representing over 50% of the MIM metals market. 316L stainless and 17-4PH precipitation hardening stainless steel are the most prevalent compositions used. The corrosion resistance and excellent mechanical properties make stainless an ideal MIM material across many applications.
Why is the MIM powder particle size so small compared to metal powders for pressing?
In metal injection molding, a key advantage is producing very complex, delicate shapes not practical through powder pressing techniques. To fill intricate mold details, ultrafine powders on the order of 5-15 microns are needed. The fine powder can more easily flow into microscopic mold features. Smaller particles also pack together more densely during injection, allowing efficient binder loading.
How much does MIM metal powder impact the properties of a finished part?
Powder characteristics significantly influence properties like strength, hardness, impact resistance, and corrosion resistance for the final component. Control of parameters like particle size distribution, impurity levels, oxygen content, and alloy chemistry allow properties to be optimized through careful powder specification and qualification.
Why is high “hall flow rate” important for MIM powders?
Hall flow rate uses standardized equipment to measure the mass flow rate of the powder through a conical funnel. It correlates to ease of feeding during injection molding. Powders prone to clumping or cohesive forces restricting flow will have low flow rates and cause molding problems like short shots, incomplete filling, or binder separation. Fluidizing additives are sometimes used to increase flow rate.
How should MIM metal powder be stored properly?
MIM powders require specialized handling to prevent deterioration before usage in feedstock. Sealed containers should be kept in a cool, dry, inert atmosphere to minimize oxidation and contamination. Avoid direct sunlight, excessive humidity, or high temperatures during storage and transport. Ground all handling equipment prevent static charge accumulation on the powder surface. Always follow the powder supplier recommendations for proper storage and handling.
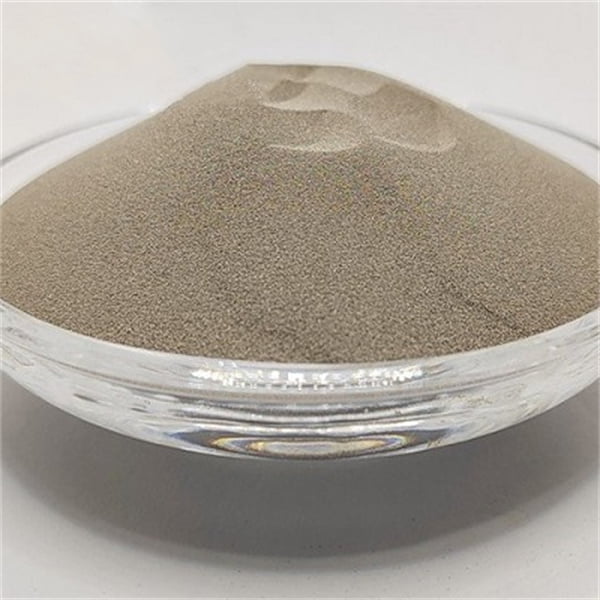
Conclusion
The ultrafine, spherical metal powders purpose-made for metal injection molding serve as the fundamental raw material enabling the process. Their specialized composition, size ranges, morphology, cost structure, handling requirements, and effects on feedstock rheology and final part qualities make them unique from other metal powders.
Through continual improvement in atomization processing, screening methodologies, and quality control, powder producers offer tailored solutions for each alloy that balance performance and economics. By selecting a powder grade optimal for their specific component geometry, tolerances, and property targets, MIM manufacturers can fully leverage the process flexibility in areas like complex electronics housings, medical instruments, and high performance aerospace components.
With increased adoption, expanding alloy portfolios, and maturing supply chains, MIM metal powders will fuel further innovation in developing precision metal components using this transformative manufacturing method.
Share On
MET3DP Technology Co., LTD is a leading provider of additive manufacturing solutions headquartered in Qingdao, China. Our company specializes in 3D printing equipment and high-performance metal powders for industrial applications.
Inquiry to get best price and customized Solution for your business!
Related Articles
About Met3DP
Recent Update
Our Product
CONTACT US
Any questions? Send us message now! We’ll serve your request with a whole team after receiving your message.
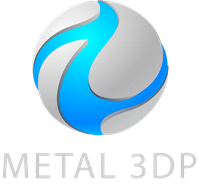
Metal Powders for 3D Printing and Additive Manufacturing