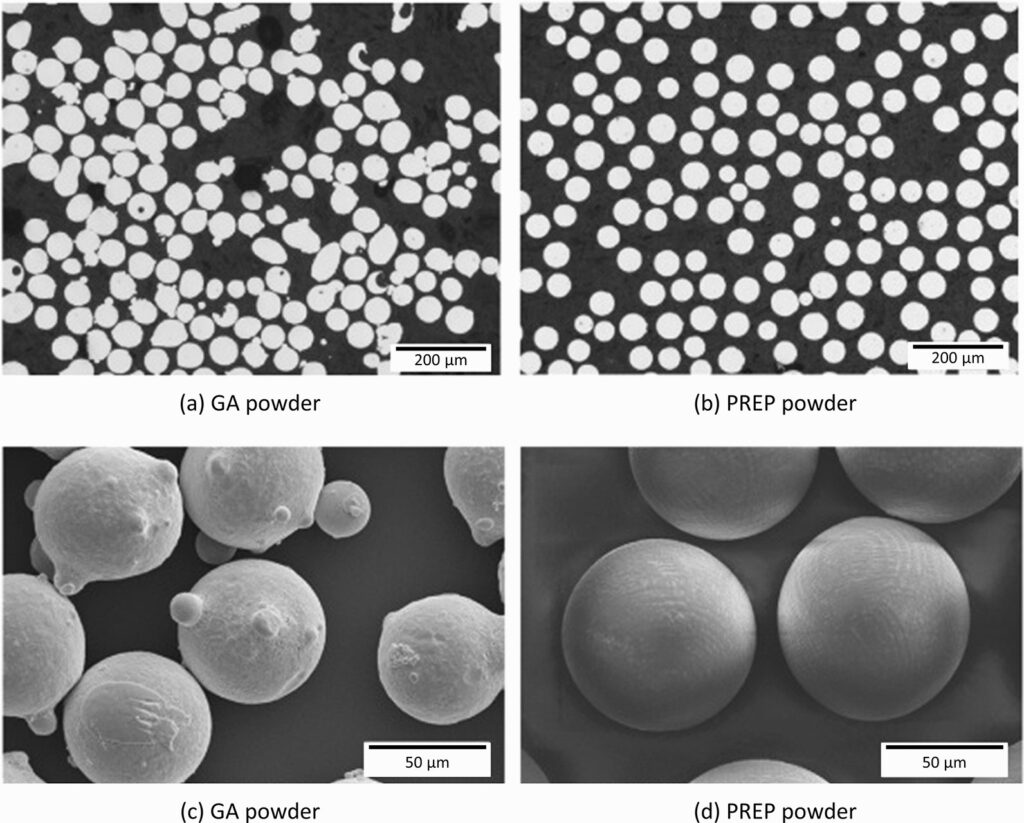
Ni15 Powder: Superior Heat Resistance and Strength in One Alloy
Low MOQ
Provide low minimum order quantity to meet different needs.
OEM & ODM
Provide customized products and design services to meet unique customer needs.
Adequate Stock
Ensure fast order processing and provide reliable and efficient service.
Customer Satisfaction
Provide high quality products with customer satisfaction at the core.
share this article
Table of Contents
If you’re working in industries that deal with high-performance materials, then you’ve probably heard of Ni15 powder. This material, a nickel-based alloy, is renowned for its unique balance of strength, corrosion resistance, and thermal stability. Whether you’re involved in additive manufacturing, aerospace, or automotive industries, Ni15 powder offers versatile applications that can meet the most demanding requirements.
This article is your ultimate guide to understanding Ni15 powder. We’ll break down everything, from its composition and properties to its various applications and technical specifications. You’ll also find comparisons with similar materials, supplier information, and answers to frequently asked questions. So, buckle up and let’s dive deep into the world of Ni15 powder!
Overview of Ni15 Powder
Ni15 powder is a nickel-chromium alloy containing approximately 15% chromium. It is primarily used in applications that require corrosion resistance and oxidation resistance at elevated temperatures. The alloy excels in conditions where materials are subjected to high heat and oxidizing atmospheres. Furthermore, Ni15 powder has excellent thermal stability, making it ideal for powder metallurgy, additive manufacturing, and thermal spray applications.
Key Features :
- Corrosion Resistance: Performs exceptionally well in corrosive environments, including oxidizing and slightly reducing atmospheres.
- Oxidation Resistance: Maintains integrity at high temperatures, offering long service life in extreme conditions.
- Thermal Stability: Withstands thermal cycling and prolonged heat exposure without degrading.
- Mechanical Strength: Offers high tensile strength and creep resistance at elevated temperatures.
- Versatile Applications: Suitable for a wide variety of industries, from aerospace to chemical processing.
Composition and Properties of Ni15 Powder
The specific composition of Ni15 powder is what gives it its unique set of mechanical and thermal properties. By balancing nickel with chromium and other alloying elements, Ni15 powder achieves a blend of strength, oxidation resistance, and thermal stability that is difficult to match.
Chemical Composition
Element | Weight Percentage (%) | Function |
---|---|---|
Nickel (Ni) | 80.00 – 85.00 | Provides the base corrosion resistance and oxidation resistance. |
Chromium (Cr) | 14.00 – 16.00 | Improves oxidation resistance and adds resistance to high-temperature corrosion. |
Iron (Fe) | 2.00 – 4.00 | Enhances the overall strength of the alloy. |
Carbon (C) | 0.05 max | Contributes to hardness and wear resistance, but must be controlled to avoid brittleness. |
Silicon (Si) | 0.50 max | Enhances oxidation resistance and improves hot-forming properties. |
Manganese (Mn) | 1.00 max | Increases toughness and improves deoxidation during melting. |
Mechanical and Thermal Properties
Property | Value |
---|---|
Density | 8.4 g/cm³ |
Melting Point | 1350°C – 1400°C |
Ultimate Tensile Strength | 750-900 MPa |
Yield Strength (0.2% Offset) | 400-600 MPa |
Elongation at Break | 25-30% |
Thermal Conductivity | 11.2 W/m·K |
Oxidation Resistance | Maintains resistance up to 900°C in oxidizing atmospheres. |
Corrosion Resistance | Excellent in oxidizing and slightly reducing environments, such as sulfuric acid. |
Why These Properties Matter
When you’re designing parts for high-temperature or corrosive environments, you need a material that offers durability, strength, and resistance to environmental degradation. Ni15 powder provides all these characteristics, making it the go-to choice for industries like aerospace and chemical processing. Its ability to maintain mechanical integrity even under thermal cycling and corrosive stress ensures longer-lasting components, reducing the need for frequent replacements and costly downtimes.
Applications of Ni15 Powder
Thanks to its mechanical properties and thermal stability, Ni15 powder is used across a wide range of industries. Whether you’re looking to build high-temperature components or parts that require strong corrosion resistance, Ni15 powder is up to the task.
Common Applications
Industry | Application |
---|---|
Aerospace | Used in turbine blades, exhaust systems, and heat shields. |
Automotive | Ideal for turbocharger components and exhaust valves. |
Chemical Processing | Applied in heat exchangers, reactors, and corrosive fluid handling equipment. |
Power Generation | Suitable for gas turbines, boilers, and steam turbine components. |
Oil & Gas | Utilized in downhole drilling equipment and high-temperature valves. |
Additive Manufacturing | Perfect for 3D printing high-strength, corrosion-resistant parts in aerospace and medical. |
Thermal Spray Coatings | Used for surface coatings in boilers, turbines, and chemical processing equipment. |
Why Ni15 Powder Shines in These Applications
For instance, in the aerospace industry, Ni15 powder is often used in gas turbine blades and exhaust systems. These components operate in highly oxidizing atmospheres at elevated temperatures, and the material’s oxidation resistance ensures that it maintains its structural integrity over long periods of time. Similarly, in chemical processing, the alloy’s corrosion resistance to sulfuric acid and other chemicals makes it an indispensable material for reactors and heat exchangers.
Specifications, Sizes, and Standards for Ni15 Powder
When purchasing Ni15 powder, it’s essential to choose the right specifications to meet your specific application needs. Particle size, density, and composition can vary based on the form and intended use of the powder.
Specifications and Standards
Specification/Standard | Details |
---|---|
UNS Number | N06003 |
ASTM Standards | ASTM B333 (Nickel-Chromium-Iron Alloys), ASTM F3055 (Powder for Additive Manufacturing) |
AMS Standards | AMS 5397 (Nickel Alloy Castings) |
ISO Standards | ISO 15156-3 (Materials for use in sour gas environments) |
Powder Particle Size | Ranges from 15 to 45 microns, depending on the application (e.g., 3D printing, thermal spray). |
Density | 8.4 g/cm³ |
Melting Range | 1350°C – 1400°C |
Available Sizes and Forms
Form | Available Sizes |
---|---|
Powder | Particle sizes typically range from 15 to 45 microns, suitable for additive manufacturing and thermal spraying. |
Bars/Rods | Diameters from 0.5 inches to 3 inches, used for structural components. |
Sheets/Plates | Thicknesses from 1 mm to 50 mm, suitable for heat exchangers and reactor parts. |
Suppliers and Pricing of Ni15 Powder
When purchasing Ni15 powder, it’s crucial to find a reliable supplier who can provide high-quality material at a competitive price. Prices can vary depending on order volume, particle size, and supplier reputation.
Suppliers and Pricing
Supplier | Price Range (per kg) | Notes |
---|---|---|
Höganäs AB | $150 – $250 | Specializes in metal powders for additive manufacturing and thermal spray applications. |
Sandvik Materials | $160 – $270 | Offers advanced materials for aerospace and industrial applications. |
Oerlikon Metco | $155 – $260 | Known for high-quality powders used in thermal spraying and laser cladding. |
Kennametal Stellite | $140 – $240 | Provides powders for corrosion-resistant and high-temperature applications. |
The cost of Ni15 powder generally ranges from $140 to $270 per kilogram, depending on the supplier, particle size, and order volume.
Advantages and Limitations of Ni15 Powder
Every material comes with its own set of advantages and limitations, and Ni15 powder is no exception. Understanding these pros and cons can help you make an informed decision about whether this material suits your specific needs.
Advantages
Advantage | Description |
---|---|
High-Temperature Strength: Retains strength at temperatures up to 900°C. | Ideal for aerospace, automotive, and industrial applications. |
Corrosion Resistance: Performs well in oxidizing and slightly reducing environments. | Perfect for chemical processing and oil & gas industries. |
Versatile Applications: Can be used for additive manufacturing, thermal spraying, and more. | Suitable for a wide range of industries, from aerospace to power generation. |
Thermal Stability: Withstands thermal cycling and prolonged exposure to high heat. | Ensures long service life in high-temperature environments. |
Limitations
Limitation | Description |
---|---|
Cost: More expensive than many other nickel alloys and stainless steels. | May not be suitable for budget-conscious projects. |
Density: Heavier than some other materials like aluminum or titanium. | Not ideal for applications where weight is a critical factor. |
Machinability: Can be challenging to machine due to its high hardness. | Requires specialized machining techniques, which may increase manufacturing time and cost. |
Ni15 Powder vs. Other Nickel-Based Alloys
How does Ni15 powder compare to other nickel-based alloys? Below is a comparison with commonly used high-temperature materials.
Alloy | Strengths | Limitations |
---|---|---|
Ni15 Powder | Excellent oxidation resistance, high strength at elevated temperatures. | Higher cost, more challenging to machine. |
Inconel 625 | Superior corrosion resistance in aqueous environments. | Less thermal stability than Ni15 at high temperatures. |
Monel 400 | Excellent in marine applications due to corrosion resistance. | Limited oxidation resistance at elevated temperatures. |
Stainless Steel 316 | Lower cost, good general corrosion resistance. | Poor high-temperature performance compared to Ni15. |
FAQs
Have more questions about Ni15 powder? Below are answers to some of the most commonly asked questions.
Question | Answer |
---|---|
What is Ni15 powder used for? | It is used in aerospace, automotive, chemical processing, and power generation industries for high-temperature, corrosion-resistant components. |
How much does Ni15 powder cost? | Prices typically range from $140 to $270 per kilogram, depending on the supplier, particle size, and order volume. |
Can Ni15 powder be used in 3D printing? | Yes, it is suitable for additive manufacturing in high-performance parts requiring corrosion resistance and thermal stability. |
What industries use Ni15 powder? | Industries such as aerospace, automotive, oil & gas, and chemical processing make extensive use of Ni15 for its thermal and corrosion resistance. |
Is Ni15 powder weldable? | Yes, it can be welded, but it requires specialized techniques due to its high melting point and oxidation resistance. |
How does Ni15 powder compare to Inconel 625? | While both are nickel-based alloys, it offers better thermal stability at elevated temperatures, but Inconel 625 excels in aqueous corrosion resistance. |
Conclusion: Why Ni15 Powder is the Ideal Choice for High-Temperature and Corrosive Applications
In conclusion, Ni15 powder stands out as a highly versatile and high-performance material, offering exceptional resistance to oxidation, corrosion, and high temperatures. Whether you work in aerospace, automotive, or chemical processing, Ni15 powder provides the mechanical strength and thermal stability needed for critical applications.
While the material may come at a higher cost compared to some other nickel-based alloys, the long-term benefits of using Ni15 powder—such as enhanced durability and reduced maintenance—make it a worthwhile investment for demanding environments. If you’re looking for a material that can withstand the heat and provide lasting performance, you can’t go wrong with Ni15 powder.
Get Latest Price
About Met3DP
Product Category
HOT SALE
CONTACT US
Any questions? Send us message now! We’ll serve your request with a whole team after receiving your message.
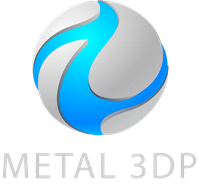
Metal Powders for 3D Printing and Additive Manufacturing