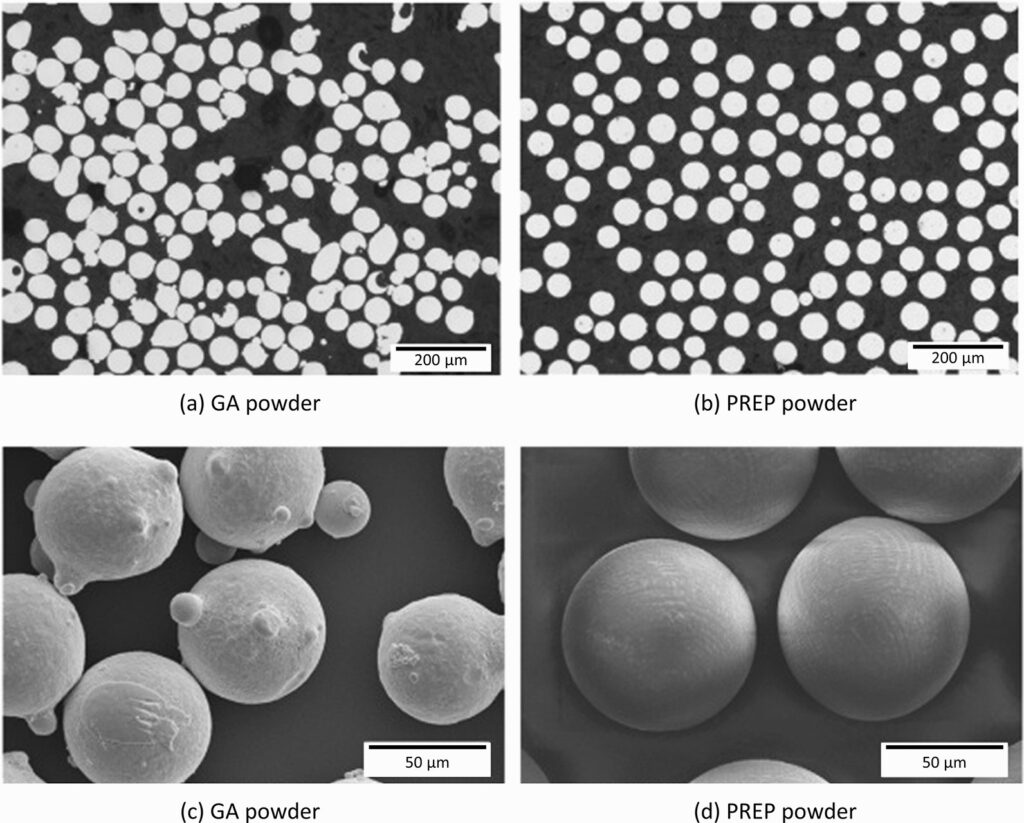
NiFeCrAlY Spherical Alloy Powder: Leading the Way in Corrosion-Resistant Materials
Low MOQ
Provide low minimum order quantity to meet different needs.
OEM & ODM
Provide customized products and design services to meet unique customer needs.
Adequate Stock
Ensure fast order processing and provide reliable and efficient service.
Customer Satisfaction
Provide high quality products with customer satisfaction at the core.
share this article
Table of Contents
Overview
Imagine a material that could withstand extreme temperatures, resist corrosion, and remain structurally sound under immense stress. That’s what NiFeCrAlY Spherical Alloy Powder brings to the table. This high-performance alloy, composed of Nickel (Ni), Iron (Fe), Chromium (Cr), Aluminum (Al), and Yttrium (Y), is engineered specifically for applications where durability, heat resistance, and corrosion protection are crucial.
Why is NiFeCrAlY such a game-changer? It’s all about its unique composition and the properties each element imparts. Nickel and iron form the alloy’s base, providing strength and ductility, while chromium enhances corrosion resistance. Aluminum contributes to oxidation resistance, and yttrium improves the alloy’s thermal stability, particularly in high-temperature environments such as aerospace and power generation.
In this article, we’ll dive deep into the world of NiFeCrAlY Spherical Alloy Powder. We’ll break down its composition, explore its applications, and discuss comparisons with other similar materials. Whether you’re an engineer working on next-gen turbine blades or a manufacturer looking to improve your additive manufacturing processes, this guide has everything you need to know about NiFeCrAlY Spherical Alloy Powder.
What is NiFeCrAlY Spherical Alloy Powder?
The Basics of Alloy Powders
Before we get into the nitty-gritty of NiFeCrAlY, let’s first understand what makes alloy powders so crucial to modern industries. Alloy powders are finely milled or atomized versions of metal alloys, which can be used in additive manufacturing, thermal spraying, metal injection molding, and other powder metallurgy processes. The spherical shape of the powder is particularly important for additive manufacturing because it ensures better flowability, allowing the material to be deposited more smoothly and evenly.
Composition of NiFeCrAlY Spherical Alloy Powder
The secret sauce behind NiFeCrAlY lies in its carefully balanced combination of elements. Here’s a breakdown of its composition:
Element | Role in the Alloy |
---|---|
Nickel (Ni) | Provides strength, ductility, and corrosion resistance; helps in maintaining structural integrity at high temperatures. |
Iron (Fe) | Adds strength and durability, making the alloy more affordable while maintaining performance. |
Chromium (Cr) | Enhances oxidation resistance and corrosion protection, especially in harsh environments. |
Aluminum (Al) | Contributes to oxidation resistance, especially at elevated temperatures. |
Yttrium (Y) | Improves thermal stability and helps maintain the alloy’s structural integrity under cyclical heating. |
This combination makes NiFeCrAlY one of the most versatile and durable alloys available today, perfect for industries where high temperatures, oxidation, and corrosion are constant challenges.
Key Properties of NiFeCrAlY Spherical Alloy Powder
The real magic happens when these elements come together. Below is a table summarizing the key properties that make NiFeCrAlY Spherical Alloy Powder such a sought-after material:
Property | Description |
---|---|
Density | ~7.5 g/cm³ (may vary slightly based on exact composition) |
Melting Point | 1,350°C to 1,380°C |
Oxidation Resistance | Exceptional resistance to oxidation at temperatures up to 1,100°C, making it ideal for turbine blades and engine components |
Corrosion Resistance | Excellent resistance to corrosive environments, including saltwater and acidic gases |
Thermal Stability | High thermal stability, maintaining mechanical properties even after prolonged exposure to high temperatures |
Ductility | Maintains good ductility under stress, allowing it to resist cracking or failure under mechanical loads |
Wear Resistance | Moderate wear resistance, suitable for applications with moderate mechanical stress and abrasion |
Electrical Conductivity | Moderate, not typically used for applications requiring high electrical conductivity, but suitable for thermal applications |
Spherical Shape | Ensures excellent flowability for additive manufacturing and powder metallurgy processes |
Why These Properties Matter
Energy production, aerospace, and industrial manufacturing all require materials that can withstand extreme conditions. The ability of NiFeCrAlY to resist oxidation at high temperatures, along with its mechanical strength, makes it invaluable in these high-stress environments. For example, in gas turbine engines, components are exposed to extreme heat and corrosive gases. Traditional materials may degrade over time, but NiFeCrAlY maintains its properties, extending the lifespan of critical components.
Applications of NiFeCrAlY Spherical Alloy Powder
The versatility of NiFeCrAlY allows it to be used across a wide range of industries. Below is a breakdown of some of its most common applications:
Industry | Application |
---|---|
Aerospace | Turbine blades, engine components, and thermal barrier coatings for jet engines and gas turbines |
Power Generation | Components in gas turbines, boilers, and nuclear reactors that require high-temperature resistance |
Automotive | Exhaust systems and other parts exposed to high heat and corrosive gases |
Marine | Corrosion-resistant components for marine environments, such as propellers, shafts, and pumps |
Additive Manufacturing | 3D printing of complex parts used in high-stress environments, ensuring superior precision and durability |
Thermal Spray Coatings | Used to deposit protective coatings on engine parts, turbines, and other components exposed to high temperatures |
Real-World Examples
Let’s take a real-world example from the aerospace industry. Jet engines operate under incredibly harsh conditions, with temperatures soaring above 1,000°C during flight. Components like turbine blades must not only withstand these temperatures but also resist oxidation and corrosion caused by the harsh gases they come into contact with. NiFeCrAlY alloy powder is often used in thermal spray coatings to protect these components, extending their lifespan and improving the overall performance of the engine.
In the power generation sector, particularly in gas turbines, NiFeCrAlY is used to manufacture parts that are exposed to high heat and oxidative environments. The alloy’s ability to resist degradation under these conditions makes it an ideal choice for ensuring the efficiency and longevity of the turbine.
Specifications, Sizes, and Standards for NiFeCrAlY Spherical Alloy Powder
When selecting NiFeCrAlY Spherical Alloy Powder, it’s essential to ensure that the material meets the required specifications for your application. Below is a table summarizing typical specifications, available sizes, and relevant standards.
Specification | Details |
---|---|
Particle Size | Common particle sizes include 10-45 µm, 45-90 µm, and custom sizes for specific applications |
Purity | Typically ≥99%, ensuring minimal contamination for high-performance applications |
Shape | Spherical for improved flowability and packing density in additive manufacturing processes |
Grade | Available in various grades depending on application, such as aerospace, industrial, and marine |
Compliance Standards | Meets international standards like AMS 5895, ISO 9001, and ASTM B348 |
Packaging Options | Available in 1 kg, 5 kg, and 25 kg drums, with custom packaging for bulk orders |
Choosing the Right Grade for Your Application
The grade of NiFeCrAlY you choose will depend largely on your intended use. For example, aerospace-grade powders typically have higher purity levels and stricter adherence to standards like AMS 5895, while industrial-grade powders may be more cost-effective but slightly less pure. Understanding the differences between grades ensures that you’ll get the right material for your needs.
Suppliers and Pricing of NiFeCrAlY Spherical Alloy Powder
The price of NiFeCrAlY Spherical Alloy Powder can vary depending on factors such as grade, purity, and quantity. Below is a list of common suppliers and typical pricing ranges for this alloy.
Supplier | Region | Price Range (per kg) | Specialization |
---|---|---|---|
Supplier A | North America | $800 – $1,200 | Specializes in high-purity NiFeCrAlY powders for aerospace and medical fields |
Supplier B | Europe | $750 – $1,100 | Offers bulk pricing and custom powder sizes for industrial applications |
Supplier C | Asia | $700 – $1,050 | Focuses on industrial-grade NiFeCrAlY powders with competitive pricing |
Global Supplier D | Worldwide | $850 – $1,300 | Provides a wide range of grades and specifications for multiple industries |
Factors Affecting Pricing
Several factors influence the cost of NiFeCrAlY Spherical Alloy Powder:
- Grade: Aerospace-grade powders tend to be more expensive due to their strict adherence to purity and performance standards.
- Purity: The higher the purity, the higher the price, especially when contamination is not an option (e.g., medical or aerospace applications).
- Quantity: Bulk purchases often come with discounted rates, so buying in larger quantities can reduce the overall cost.
- Supplier Location: Regional differences in pricing and shipping costs can also affect the final price, especially for international orders.
Comparing NiFeCrAlY to Other Alloy Powders
When selecting a high-performance alloy powder, it’s essential to consider how NiFeCrAlY compares to other popular materials. Below is a table comparing NiFeCrAlY with two other commonly used alloys: Inconel 625 and Hastelloy X.
NiFeCrAlY vs. Inconel 625 vs. Hastelloy X
Property | NiFeCrAlY | Inconel 625 | Hastelloy X |
---|---|---|---|
Corrosion Resistance | Excellent | High | High |
Oxidation Resistance | Superior | High | Moderate |
Tensile Strength | High | Very High | Moderate |
Thermal Stability | Outstanding | Good | Moderate |
Cost | Moderate | High | High |
Applications | Aerospace, Energy, Marine | Aerospace, Marine, Energy | Aerospace, Marine, Chemical |
Comparing NiFeCrAlY to Inconel 625
Inconel 625 is another high-performance material known for its corrosion resistance and tensile strength. However, NiFeCrAlY offers better thermal stability and oxidation resistance, particularly in environments where temperatures exceed 1,000°C. While Inconel 625 may be better suited for applications requiring extreme mechanical stress, NiFeCrAlY excels in thermal barrier coatings and turbine components.
Comparing NiFeCrAlY to Hastelloy X
Hastelloy X is commonly used in chemical processing and aerospace applications due to its excellent high-temperature strength. However, NiFeCrAlY surpasses it in terms of oxidation resistance, making it a better choice for high-temperature turbine components. Where Hastelloy X might fail after prolonged exposure to high heat, NiFeCrAlY maintains its structural integrity, reducing the need for frequent replacements.
Advantages and Limitations of NiFeCrAlY Spherical Alloy Powder
Advantages
Advantage | Description |
---|---|
High-Temperature Resistance | Maintains performance at temperatures up to 1,100°C, making it ideal for turbines and jet engines. |
Corrosion Resistance | Exceptional resistance to corrosive environments, including saltwater and acidic gases. |
Oxidation Resistance | Superior oxidation resistance, even at elevated temperatures, thanks to its aluminum and yttrium content. |
Ductility | Good ductility, allowing it to withstand mechanical stress without cracking or failing. |
Spherical Shape | Ensures excellent flowability and packing density, making it perfect for 3D printing and powder metallurgy. |
Limitations
Limitation | Description |
---|---|
Cost | More expensive than traditional alloys, particularly for high-purity or aerospace-grade powders. |
Manufacturing Complexity | Requires advanced additive manufacturing or thermal spray techniques, which can increase production costs. |
Availability | Not as widely available as conventional alloys, though demand is growing in sectors like aerospace and energy. |
Frequently Asked Questions (FAQ) About NiFeCrAlY Spherical Alloy Powder
Question | Answer |
---|---|
What is NiFeCrAlY Spherical Alloy Powder? | It is a high-performance alloy composed of Nickel, Iron, Chromium, Aluminum, and Yttrium, designed for high-temperature and corrosive environments. |
What industries use NiFeCrAlY Spherical Alloy Powder? | Commonly used in aerospace, energy, marine, automotive, and thermal spray coatings for high-performance applications. |
How does NiFeCrAlY compare to Inconel? | NiFeCrAlY offers better oxidation resistance and thermal stability, while Inconel provides higher tensile strength. |
Is NiFeCrAlY Spherical Alloy Powder magnetic? | No, NiFeCrAlY is generally non-magnetic, making it suitable for applications where magnetic interference could be an issue. |
Can NiFeCrAlY be used in additive manufacturing? | Yes, the powder’s spherical shape ensures superior flowability and makes it perfect for 3D printing and powder metallurgy processes. |
What sizes are available for NiFeCrAlY powder? | Common sizes include 10-45 µm and 45-90 µm, with custom sizes available depending on the application. |
How much does NiFeCrAlY cost? | Prices typically range from $700 to $1,300 per kg, depending on the grade, purity, and quantity purchased. |
What is the advantage of using NiFeCrAlY in aerospace? | Its high-temperature resistance, oxidation resistance, and corrosion protection make it ideal for turbine blades and engine components. |
Conclusion
NiFeCrAlY Spherical Alloy Powder is revolutionizing industries that demand materials capable of withstanding extreme conditions. From aerospace to power generation, this alloy’s unique combination of strength, oxidation resistance, and thermal stability makes it a standout choice for high-stress applications.
Whether you’re looking to improve the durability of turbine blades, enhance the performance of engine components, or explore new possibilities in additive manufacturing, NiFeCrAlY offers the longevity and performance you need. While it may come at a higher cost than traditional alloys, its superior properties make it an investment worth considering in any industry where failure is not an option.
Get Latest Price
About Met3DP
Product Category
HOT SALE
CONTACT US
Any questions? Send us message now! We’ll serve your request with a whole team after receiving your message.
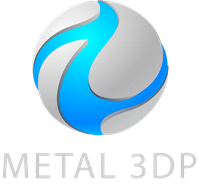
Metal Powders for 3D Printing and Additive Manufacturing