How powder laser 3D printing Drive Innovation in R&D
Table of Contents
powder laser 3D printing:Rapid Prototyping
Imagine a world where:
- You could test an innovative product within days, not months.
- Making design tweaks felt as effortless as editing a document.
This is the power of rapid prototyping, a revolutionary approach that has fundamentally changed the way we bring ideas to life.
The Need for Speed
Traditionally, crafting prototypes was a painstaking endeavor. It could take weeks, even months, to create a single physical model, often hindering the design process. Rapid prototyping shatters this limitation. By leveraging technologies like 3D printing, complex models can be produced in a fraction of the time, allowing researchers and engineers to test and refine their ideas with unprecedented speed.
The Power of Iteration
Rapid prototyping isn’t just about speed; it’s about empowering exploration. With traditional methods, making changes to a physical prototype often meant starting from scratch. However, the beauty of digital design lies in its malleability. Software allows designers to modify their creations effortlessly, enabling them to rapidly iterate through multiple versions of a prototype. This reduces development timelines and significantly increases the chances of finding the optimal solution.
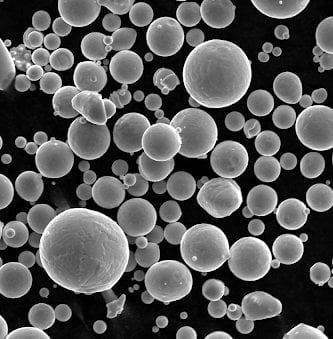
Complex Designs Made Possible:
Powder laser 3D printing technology has revolutionized the realm of manufacturing by unlocking a new era of design freedom. Unlike traditional methods, which often face limitations in shaping materials, this innovative process allows for the creation of intricate and complex geometries previously deemed impossible.
This newfound freedom empowers designers to:
- Push the boundaries of functionality: By overcoming traditional limitations, 3D printing enables the creation of components with intricate internal structures and channels, leading to enhanced performance and functionality in the final product.
- Embrace lightweight design: The ability to produce complex, hollow structures allows for significant weight reduction. This is particularly beneficial in industries like aerospace and automotive, where even a minor weight saving can translate to improved fuel efficiency and overall performance.
- Simplify and consolidate: The freedom of design offered by 3D printing opens doors to consolidate multiple components into a single, unified structure. This not only simplifies the manufacturing process but also reduces the number of parts needed for assembly, leading to a more streamlined and efficient product.
powder laser 3D printing:Material Exploration
The world of materials is constantly evolving, and two exciting advancements are pushing the boundaries of what’s possible: new alloys and bioprinting.
New Alloys: Tailoring Metal for Demand
Imagine being able to design a metal from scratch, one that possesses the exact properties you need for a specific application. This is the promise of custom-blended metal powders. Traditionally, alloys are created by combining different metals in fixed proportions. However, this new approach allows researchers to mix and match metal powders with unprecedented precision, creating unique combinations never seen before. This opens doors for lightweight yet strong materials for aerospace, corrosion-resistant alloys for marine environments, and even metals with shape-memory capabilities.
Bioprinting: Printing the Building Blocks of Life
While new alloys revolutionize the world of metal, bioprinting takes an even more audacious leap, venturing into the realm of living materials. This technology utilizes powder laser techniques similar to 3D printing, but instead of traditional materials, it uses biocompatible materials like cells and bio-inks. This opens up a future where we can potentially print custom medical implants perfectly matched to a patient’s needs, or even dream further of printed tissues and organs to address organ failure and revolutionize medicine.
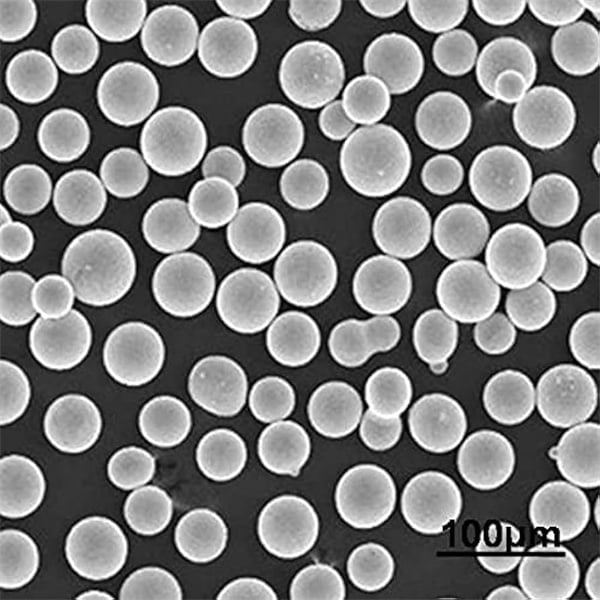
Cost-Efficiency (in the long run):
Minimizing Waste
Traditional manufacturing often relies on subtractive methods, where they start with a block of material and remove sections to create the desired object. This process can generate significant scrap material, which is often unusable and adds to waste disposal costs. In contrast, 3D printing employs an additive approach, building the object layer by layer using precise amounts of material. This significantly minimizes waste, leading to cost savings in the long run.
Streamlined Prototyping
Bringing new products to market often involves creating numerous prototypes to test functionality and design. Traditionally, this required custom molds or tooling, which can be expensive and time-consuming to produce. 3D printing allows for rapid prototyping, as the same digital model can be used to create multiple iterations quickly and inexpensively. This reduces development costs and accelerates the product development process, ultimately saving time and money in the long run.
Uniquely Efficient
3D printing offers a unique combination of these two advantages. Unlike alternative methods that might excel in one area but struggle with the other, 3D printing simultaneously minimizes waste and streamlines prototyping, making it a highly cost-effective solution in the long run.
Share On
MET3DP Technology Co., LTD is a leading provider of additive manufacturing solutions headquartered in Qingdao, China. Our company specializes in 3D printing equipment and high-performance metal powders for industrial applications.
Inquiry to get best price and customized Solution for your business!
Related Articles
About Met3DP
Recent Update
Our Product
CONTACT US
Any questions? Send us message now! We’ll serve your request with a whole team after receiving your message.
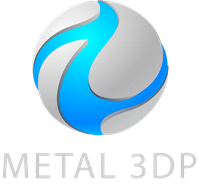
Metal Powders for 3D Printing and Additive Manufacturing