Preparing High-Purity Powders
Table of Contents
Imagine a world where materials are crafted with unparalleled precision, where tiny particles hold the key to groundbreaking advancements. This is the realm of high-purity powders, and their preparation is a fascinating dance of science and meticulous engineering.
In this comprehensive guide, we’ll delve into the captivating world of high-purity powders. We’ll explore the common techniques used to create these marvels, unveil the applications that drive innovation, and equip you with the knowledge to navigate this exciting field. Buckle up, because we’re about to embark on a journey into the heart of material science!
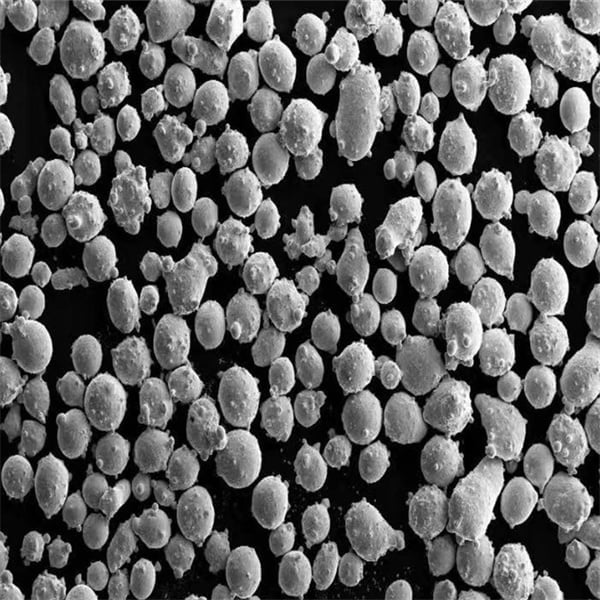
Common Technologies for Preparing High-Purity Powders
Just like baking a perfect cake requires the right ingredients and technique, preparing high-purity powders involves a variety of methods, each with its own strengths and quirks. Here’s a glimpse into some of the most widely used approaches:
- Physical Vapor Deposition (PVD): Picture this: we take a solid material, heat it up intensely (think evaporation!), and condense the vapor onto a cool surface. This creates a fine powder with exceptional purity, often used for advanced electronics and coatings.
- Chemical Vapor Deposition (CVD): Similar to PVD, but with a twist! Here, we introduce reactive gases into the mix. These gases decompose on the hot surface, forming the desired powder. This technique allows for precise control over the composition and structure of the powder, making it ideal for applications like semiconductors and solar cells.
- Electrolysis: Imagine a battery on steroids! By passing electricity through a solution containing a metal salt, we can coax the metal out in the form of a pure powder. This method is particularly useful for high-value metals like copper and titanium, where high purity is critical for their performance.
- Spray Pyrolysis: Think of a perfume atomizer, but instead of fragrance, we’re spraying a liquid precursor solution. As the droplets travel through a hot zone, they decompose, leaving behind a fine powder. This method offers versatility in terms of the materials that can be processed and is often used for ceramics and pigments.
- Precipitation: Imagine brewing a special potion. By carefully mixing solutions, we can induce a chemical reaction that forms a solid precipitate. This precipitate, after proper washing and drying, can be a high-purity powder. This technique is commonly used for metal oxides and hydroxides.
- Combustion Synthesis: Have you ever witnessed a fireworks display? Combustion synthesis is like a controlled explosion for good! By rapidly igniting a mixture of precursors, we can generate a high-purity powder. This method is particularly useful for materials like nitrides and carbides, which are difficult to prepare using other techniques.
- Grinding: Sometimes, simplicity reigns supreme! We can take a high-purity bulk material and grind it down into a fine powder. This method is cost-effective but may not be suitable for all materials, as grinding can introduce impurities and alter the particle size distribution.
These are just a few of the many techniques used to prepare high-purity powders. The choice of method depends on the desired material properties, cost considerations, and production scale.
Exploring Specific Metal Powder Models
Now, let’s delve into the fascinating world of specific metal powder models! Here are ten examples to whet your appetite:
- Nickel Powder (Spherical): Imagine tiny, perfect spheres of nickel. These spherical powders offer excellent flowability and packing density, making them ideal for applications like battery electrodes and metal injection molding (MIM).
- Copper Powder (Electrolytic): High-purity copper, born from the power of electricity! This type of copper powder boasts excellent conductivity and is used in a variety of applications, from electrical components to heat sinks.
- Titanium Powder (Gas-Atomized): Imagine titanium dust, but with exceptional purity! Gas-atomized titanium powder is lightweight yet incredibly strong, making it a valuable material for aerospace and biomedical applications.
- Aluminum Powder (Atomized): Aluminum in a powdered form? You bet! Atomized aluminum powder offers a high surface area and is used in pyrotechnics, explosives (don’t worry, the controlled kind!), and even as a fuel additive.
- Iron Powder (Reduced): Iron minus the impurities? Reduced iron powder delivers high purity and good magnetic properties, making it essential for the production of soft magnetic components like transformers and inductors.
- Tungsten Carbide Powder (Spherical): Imagine the marriage of tungsten’s strength and carbide’s hardness! Spherical tungsten carbide powder offers exceptional wear resistance and is used in cutting tools, drill bits, and wear plates.
- Silver Powder (Flake): Silver in a flaky form? Believe it or not, silver flake powder offers a high surface area and excellent conductivity, making it ideal for applications like electrical contacts, conductive inks, and brazing alloys.
- Platinum Powder (Sponge): Platinum, the king of catalysts, in a sponge-like form? Platinum sponge powder has a highly porous structure, maximizing its catalytic activity, making it essential for catalytic converters in automobiles and various chemical reactions.
- Gold Powder (Spherical): A touch of luxury in powder form! Spherical gold powder offers a unique combination of conductivity, ductility, and corrosion resistance. It’s used in electronics, decorative applications, and even some biomedical devices.
- Molybdenum Powder (Carbonyl): Molybdenum, known for its high melting point, in a powdered form? Molybdenum carbonyl powder is a high-purity option, particularly useful for applications demanding high-temperature performance, such as crucibles, heating elements, and rocket engine components.
A Look at Additional Powder Properties
While purity is king in the realm of high-purity powders, other properties play a crucial role in determining their suitability for specific applications. Here are some key characteristics to consider:
- Particle Size and Distribution: Imagine a bag of marbles. If all the marbles are roughly the same size, that’s a uniform particle size distribution. This can significantly impact the powder’s flowability, packing density, and reactivity.
- Particle Morphology: The shape of the powder particles also matters! Spherical particles typically flow better and pack more densely than irregular ones. Flake-shaped particles, on the other hand, may offer a higher surface area, which can be beneficial for some applications.
- Surface Area: Think of the surface of a tennis ball versus a ping pong ball. The tennis ball has a larger surface area, which can be crucial for materials that rely on surface interactions, like catalysts or pigments.
- Crystalline Structure: How the atoms are arranged within the powder particles can influence their properties. For instance, a specific crystalline structure might offer superior strength or conductivity.
- Density: Just like feathers are lighter than lead, different powders have varying densities. This property is crucial for applications where weight is a critical factor, such as in aerospace components.
the Applications of High-Purity Powders
High-purity powders are the building blocks for a vast array of innovative technologies. Here’s a glimpse into some of the exciting applications they enable:
- Electronics: High-purity powders are essential for the production of advanced electronic components like capacitors, transistors, and battery electrodes. Their exceptional purity ensures consistent electrical properties and optimal device performance.
- Catalysis: Powders with high surface areas and specific crystalline structures play a vital role in various catalytic reactions. They accelerate chemical processes, making them essential for the production of clean fuels, pharmaceuticals, and a variety of chemicals.
- Additive Manufacturing: The world of 3D printing heavily relies on high-purity powders. These powders are melted or fused layer-by-layer to create complex three-dimensional objects, revolutionizing how we design and manufacture products.
- Coatings: High-purity powders can be sprayed or deposited onto surfaces to create protective or functional coatings. These coatings can improve wear resistance, corrosion resistance, electrical conductivity, and even offer decorative finishes.
- Biomedical Devices: Some high-purity powders, like titanium and tantalum, are biocompatible and can be used to manufacture implants for bones, joints, and other medical applications. Their purity minimizes the risk of rejection and ensures long-term functionality.
- Energy Storage: High-purity powders are crucial for the development of next-generation batteries. They can improve the energy density, power output, and lifespan of these energy storage devices.
Specifications, Sizes, Grades, and Standards
When it comes to high-purity powders, there’s a whole world of specifications, sizes, grades, and standards to navigate. Let’s delve into this essential aspect:
Property | Description | Example |
---|---|---|
Purity | The percentage of the desired element present in the powder. | Nickel powder (99.5% pure) |
Particle Size | The average diameter of the powder particles. | Aluminum powder (10-30 microns) |
Particle Size Distribution | How the particle sizes are spread out within the powder. | Spherical tungsten carbide powder (narrow size distribution) |
Particle Morphology | The shape of the powder particles. | Silver flake powder |
Surface Area | The total surface area of the powder particles per unit mass. | Molybdenum powder (high surface area) |
Crystalline Structure | The arrangement of atoms within the powder particles. | Copper powder (fcc – face-centered cubic) |
Density | The mass per unit volume of the powder. | Titanium powder (4.5 g/cm³) |
Grade | A designation indicating the overall quality and suitability of the powder for specific applications. | Electronic grade copper powder |
Standards | Established guidelines outlining the specifications and testing methods for high-purity powders. | ASTM International standards for metal powders (e.g., ASTM B883 for copper powder) |
Suppliers and Pricing
The world of high-purity powders boasts a diverse range of suppliers, each catering to specific needs and budgets. Here’s a brief overview:
- Metal Powder Producers: Major metal producers often have dedicated divisions specializing in high-purity powders. They offer a wide variety of materials and can cater to large-scale production needs.
- Specialty Powder Manufacturers: These companies focus exclusively on the production of high-purity powders. They may offer unique materials or specialize in specific particle size distributions or morphologies.
- Chemical Distributors: Many chemical distributors carry a selection of high-purity powders alongside other chemical products. This can be a convenient option for smaller research or development projects.
Pricing for high-purity powders can vary significantly depending on the material, purity level, particle size, and quantity. Generally, higher purity and finer particle sizes command a premium price. It’s essential to compare prices from multiple suppliers and consider factors like minimum order quantities and shipping costs.
A Pros and Cons Analysis
High-purity powders offer a multitude of advantages, but it’s crucial to understand their limitations as well. Here’s a balanced perspective:
Pros:
- Exceptional purity: This ensures consistent properties and optimal performance in the final application.
- Tailored properties: Powders can be engineered with specific particle sizes, morphologies, and surface areas to meet specific needs.
- Versatility: High-purity powders can be used in a wide range of applications across various industries.
- Advanced manufacturing: They enable the development of innovative technologies like additive manufacturing and advanced coatings.
Cons:
- Higher cost: Compared to lower purity alternatives, high-purity powders can be significantly more expensive.
- Production complexity: Manufacturing high-purity powders often requires specialized equipment and expertise.
- Handling precautions: Some high-purity powders can be reactive or hazardous, requiring special handling procedures.
Handling High-Purity Powders with Care
Working with high-purity powders demands a safety-first approach. Here are some essential precautions to consider:
- Respiratory protection: Always wear appropriate respirators to avoid inhaling airborne particles, especially when working with fine powders.
- Eye protection: Safety glasses or goggles are essential to protect your eyes from splashes or dust particles.
- Skin protection: Wear gloves to minimize skin contact with the powder, especially if it’s reactive or poses a health risk.
- Proper ventilation: Ensure adequate ventilation in your workspace to prevent the buildup of airborne particles.
- Flammable hazards: Be aware of the flammability of some metal powders and take appropriate precautions to prevent fires or explosions.
- Disposal considerations: High-purity powders may require special disposal procedures depending on their composition and potential hazards.
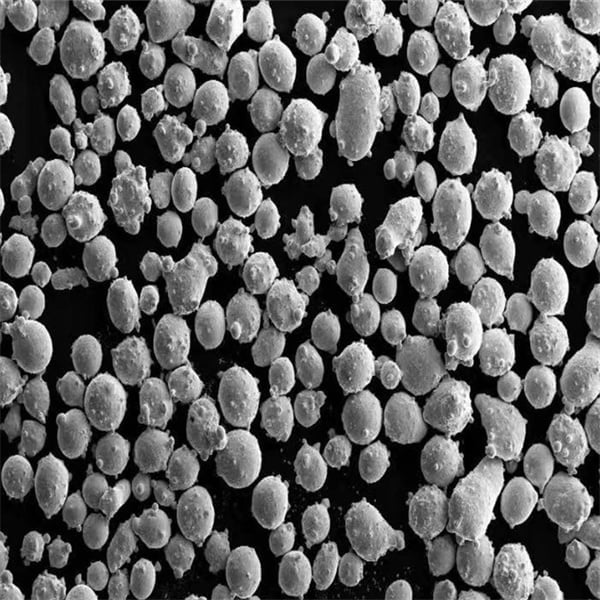
FAQ
Q: What are the advantages of using high-purity powders compared to lower purity alternatives?
A: High-purity powders offer several advantages:
- Consistent performance: The high purity minimizes variations in properties, leading to more reliable and predictable performance in the final application.
- Enhanced functionality: Certain properties, like electrical conductivity or catalytic activity, can be significantly improved with higher purity.
- Reduced processing problems: Impurities can sometimes cause issues during processing, such as weak bonds or unwanted reactions. High purity powders minimize these problems.
Q: How are high-purity powders typically shipped?
A: High-purity powders are often shipped in sealed containers under an inert atmosphere (like argon) to prevent oxidation or contamination during transport. The specific packaging will depend on the material, quantity, and desired level of protection.
Q: Can high-purity powders degrade over time?
A: Yes, some high-purity powders can degrade over time, especially if not stored properly. Here are some factors that can influence their stability:
- Exposure to air: Certain powders can oxidize or react with moisture in the air, leading to the formation of surface contaminants.
- Light sensitivity: Some materials, like certain organic powders, can degrade when exposed to light.
- Temperature: High temperatures can accelerate degradation processes in some powders.
Here are some tips for storing high-purity powders to minimize degradation:
- Store in sealed containers: Use airtight containers made from materials compatible with the powder.
- Maintain an inert atmosphere: For highly reactive powders, consider storing them under an inert gas like argon to prevent oxidation.
- Control temperature and humidity: Store the powders in a cool, dry environment to minimize the risk of degradation.
- Follow manufacturer recommendations: Always refer to the manufacturer’s specifications for proper storage conditions.
Q: Where can I find more information about specific high-purity powders and their properties?
A: There are several resources available to learn more about specific high-purity powders:
- Metal powder supplier websites: Many metal powder suppliers provide detailed information about the materials they offer, including specifications, properties, and safety data sheets (SDS).
- Technical data sheets: Manufacturers often provide technical data sheets (TDS) for their powders, which detail the material’s properties, composition, and performance characteristics.
- Scientific literature: For in-depth information on the properties and behavior of specific high-purity powders, you can consult scientific journals and research articles.
Share On
MET3DP Technology Co., LTD is a leading provider of additive manufacturing solutions headquartered in Qingdao, China. Our company specializes in 3D printing equipment and high-performance metal powders for industrial applications.
Inquiry to get best price and customized Solution for your business!
Related Articles
About Met3DP
Recent Update
Our Product
CONTACT US
Any questions? Send us message now! We’ll serve your request with a whole team after receiving your message.
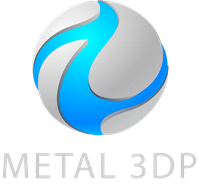
Metal Powders for 3D Printing and Additive Manufacturing
COMPANY
PRODUCT
cONTACT INFO
- Qingdao City, Shandong, China
- [email protected]
- [email protected]
- +86 19116340731