Alloy G-30 Powder
Alloy G-30 powder is a versatile nickel-based superalloy widely used in various industries due to its exceptional high-temperature strength, corrosion resistance, and creep resistance properties. This alloy powder is commonly used in additive manufacturing processes, such as powder bed fusion and directed energy deposition, for producing intricate and complex components for aerospace, energy, and other demanding applications.
Low MOQ
Provide low minimum order quantity to meet different needs.
OEM & ODM
Provide customized products and design services to meet unique customer needs.
Adequate Stock
Ensure fast order processing and provide reliable and efficient service.
Customer Satisfaction
Provide high quality products with customer satisfaction at the core.
share this product
Table of Contents
Alloy G-30 powder is a versatile nickel-based superalloy widely used in various industries due to its exceptional high-temperature strength, corrosion resistance, and creep resistance properties. This alloy powder is commonly used in additive manufacturing processes, such as powder bed fusion and directed energy deposition, for producing intricate and complex components for aerospace, energy, and other demanding applications.
Developed by the Special Metals Corporation, Alloy G-30 powder is renowned for its ability to withstand extreme temperatures, making it an ideal choice for manufacturing components that operate in harsh environments. Its unique composition and microstructure contribute to its superior performance, making it a popular choice among engineers and manufacturers in cutting-edge industries.
Alloy G-30 Powder Composition
The chemical composition of Alloy G-30 powder is carefully formulated to achieve the desired properties. Here’s a table showcasing the typical composition range:
Element | Composition (wt%) |
---|---|
Nickel | 52 – 57% |
Chromium | 28 – 32% |
Iron | 10 – 16% |
Cobalt | 4 – 7% |
Tungsten | 3 – 4.5% |
Aluminum | 0.3 – 0.7% |
Titanium | 0.5 – 2.5% |
Carbon | 0.03 – 0.12% |
This unique blend of elements contributes to the alloy’s exceptional strength, oxidation resistance, and thermal stability at elevated temperatures.
Key Properties and Characteristics of Alloy G-30 Powder
Alloy G-30 powder possesses a remarkable combination of properties that make it suitable for demanding applications:
Property | Description |
---|---|
High-Temperature Strength | Retains excellent strength at temperatures up to 1800°F (982°C) |
Oxidation and Corrosion Resistance | Excellent resistance to oxidation and corrosion, even in harsh environments |
Creep Resistance | Superior resistance to creep deformation at high temperatures |
Thermal Stability | Maintains dimensional stability and mechanical properties at elevated temperatures |
Weldability | Good weldability, making it suitable for welding and additive manufacturing processes |
Microstructural Stability | Maintains a stable microstructure during prolonged exposure to high temperatures |
These properties make Alloy G-30 powder an ideal choice for applications that require high-temperature performance, corrosion resistance, and dimensional stability.
Industrial Applications of Alloy G-30 Powder
Alloy G-30 powder finds widespread use in various industries due to its exceptional properties:
Industry | Applications |
---|---|
Aerospace | Turbine blades, combustion chambers, nozzles, and other hot section components |
Energy | Boiler tubing, heat exchanger components, and other high-temperature components |
Chemical Processing | Valves, pumps, and piping systems for handling corrosive media |
Automotive | Turbocharger components, exhaust system components |
Medical | Surgical instruments, implants, and prosthetic devices |
Additive Manufacturing | Powder bed fusion and directed energy deposition processes for complex component manufacturing |
The versatility of Alloy G-30 powder allows it to be used in a wide range of applications where high-temperature strength, oxidation resistance, and dimensional stability are critical.
Suppliers and Pricing of Alloy G-30 Powder
Alloy G-30 powder is available from various suppliers worldwide. The pricing can vary depending on factors such as quantity, purity, particle size distribution, and supplier. Here’s a table with some reputable suppliers and approximate pricing:
Supplier | Approximate Price Range (USD/kg) |
---|---|
Carpenter Technology | $150 – $250 |
Sandvik Materials Technology | $180 – $280 |
Höganäs AB | $160 – $270 |
ATI Powder Metals | $170 – $260 |
Praxair Surface Technologies | $190 – $280 |
Please note that these prices are subject to change and may vary based on specific requirements and market conditions.
Advantages and Limitations of Alloy G-30 Powder
Like any material, Alloy G-30 powder has its advantages and limitations, which should be carefully considered when selecting it for a specific application:
Advantages | Limitations |
---|---|
Exceptional high-temperature strength and creep resistance | Relatively expensive compared to some other alloys |
Excellent oxidation and corrosion resistance | Limited availability and supply compared to more common alloys |
Dimensional stability at elevated temperatures | Challenging to machine and work with due to its high strength |
Good weldability and suitability for additive manufacturing processes | May require special handling and processing techniques due to its unique properties |
Maintains mechanical properties and microstructural stability in harsh environments | Limited availability of specialized equipment and expertise for processing |
Versatile applications across various industries |
While Alloy G-30 powder offers superior performance in high-temperature and corrosive environments, its limitations, such as cost and availability, should be carefully weighed against the application requirements.
Sizing and Specifications of Alloy G-30 Powder
Alloy G-30 powder is available in various particle size distributions to meet the requirements of different additive manufacturing processes and applications. Here’s a table with typical particle size ranges:
Particle Size Range (μm) | Application |
---|---|
10 – 45 | Powder bed fusion (PBF) processes |
45 – 106 | Directed energy deposition (DED) processes |
106 – 250 | Cold spray and thermal spray processes |
250 – 500 | Hot isostatic pressing (HIP) and other consolidation processes |
Additionally, Alloy G-30 powder is available in various grades and specifications, which may vary based on the supplier and intended application. Common specifications include:
- Chemical composition
- Particle size distribution
- Flowability
- Apparent density
- Oxygen content
- Other impurity levels
Manufacturers and suppliers may offer customized grades and specifications to meet specific customer requirements.
Standards and Certifications for Alloy G-30 Powder
Alloy G-30 powder is subject to several industry standards and certifications to ensure quality, consistency, and traceability. Some of the relevant standards and certifications include:
- ASTM B637: Standard Specification for Precipitation-Hardening Nickel Alloy Bars, Forgings, and Forging Stock for High-Temperature Service
- AMS 5383: Nickel Alloy, Corrosion and Heat-Resistant, Consumable Electrode or Vacuum Induction Melted, 52Ni – 29Cr – 11Fe – 6Co, Consumable Electrode Remelted or Vacuum Induction Melted, Annealed
- ISO 17296-3: Additive manufacturing – General principles – Part 3: Standard data format and certifying Additive Manufacturing data
- ISO/ASTM 52900: Additive manufacturing – General principles – Terminology
- NADCAP: National Aerospace and Defense Contractors Accreditation Program
Compliance with these standards and certifications ensures that Alloy G-30 powder meets the necessary quality, safety, and performance requirements for various applications, particularly in critical industries such as aerospace and energy.
FAQs
Question | Answer |
---|---|
What makes Alloy G-30 powder suitable for high-temperature applications? | Alloy G-30 powder is designed to maintain its strength, oxidation resistance, and creep resistance at elevated temperatures, making it an ideal choice for high-temperature applications such as turbine components, combustion chambers, and heat exchangers. |
How does Alloy G-30 powder compare to other nickel-based superalloys? | Compared to other nickel-based superalloys, Alloy G-30 powder offers superior high-temperature strength and creep resistance, making it more suitable for applications that require exceptional performance at elevated temperatures. However, it may be more expensive and less readily available than some other alloys. |
What are the typical additive manufacturing processes used with Alloy G-30 powder? | Alloy G-30 powder is commonly used in powder bed fusion (PBF) processes, such as selective laser melting (SLM) and electron beam melting (EBM), as well as directed energy deposition (DED) processes like laser metal deposition. These additive manufacturing processes allow for the production of complex and intricate components with excellent material properties. |
How does the particle size distribution affect the performance of Alloy G-30 powder? | The particle size distribution of Alloy G-30 powder plays a crucial role in its performance and suitability for different additive manufacturing processes. Finer particle sizes (10-45 μm) are typically used for PBF processes, while coarser particle sizes (45-106 μm) are better suited for DED processes. The particle size distribution affects factors such as flowability, packing density, and mechanical properties of the final component. |
What are the typical post-processing steps for components made from Alloy G-30 powder? | Depending on the application and requirements, components made from Alloy G-30 powder may undergo various post-processing steps, such as heat treatment, hot isostatic pressing (HIP), surface finishing, and inspection. These steps are essential to achieve the desired microstructure, mechanical properties, and dimensional accuracy. |
Are there any special handling or storage requirements for Alloy G-30 powder? | Alloy G-30 powder may require special handling and storage precautions due to its unique properties and composition. This may include measures to prevent contamination, maintain inert atmospheres, and control moisture levels. It is recommended to follow the supplier’s guidelines and industry best practices for handling and storing Alloy G-30 powder. |
What industries or applications benefit the most from using Alloy G-30 powder? | Alloy G-30 powder is particularly well-suited for industries and applications that require high-temperature performance, corrosion resistance, and dimensional stability, such as aerospace (turbine components, combustion chambers), energy (boiler tubing, heat exchangers), chemical processing (valves, pumps, piping systems), and automotive (turbocharger components, exhaust system components). Its exceptional properties make it an ideal choice for these demanding applications. |
How does the cost of Alloy G-30 powder compare to other materials used in additive manufacturing processes? | Alloy G-30 powder is generally more expensive than some other alloys used in additive manufacturing processes, primarily due to its unique composition and the specialized processing required to produce it. However, its superior performance characteristics and suitability for high-temperature applications often justify the higher cost for critical components in industries like aerospace and energy. |
Get Latest Price
About Met3DP
Product Category
HOT SALE
CONTACT US
Any questions? Send us message now! We’ll serve your request with a whole team after receiving your message.
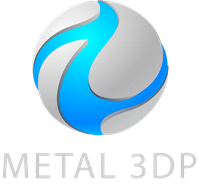
Metal Powders for 3D Printing and Additive Manufacturing