K465 Alloy Powder
K465 alloy powder is a nickel-based superalloy that offers high strength and corrosion resistance at elevated temperatures. It is widely used in aerospace, power generation, and chemical processing industries.
Low MOQ
Provide low minimum order quantity to meet different needs.
OEM & ODM
Provide customized products and design services to meet unique customer needs.
Adequate Stock
Ensure fast order processing and provide reliable and efficient service.
Customer Satisfaction
Provide high quality products with customer satisfaction at the core.
share this product
Table of Contents
K465 Alloy Powder: Composition, Properties, Applications, and Specifications
K465 has become a popular choice for aerospace, power generation, and chemical processing industries where components are subjected to high temperatures or aggressive environments. It allows complex geometries to be 3D printed for optimal performance.
This article provides detailed information on the composition, properties, applications, specifications, availability, processing, and comparisons of K465 superalloy powder for additive manufacturing.
K465 Alloy Powder Composition
The nominal composition of K465 nickel-based superalloy powder is given below:
Element | Weight % |
---|---|
Nickel (Ni) | Balance |
Chromium (Cr) | 15 – 17% |
Cobalt (Co) | 9 – 10% |
Molybdenum (Mo) | 3% |
Tantalum (Ta) | 4.5 – 5.5% |
Aluminum (Al) | 5 – 6% |
Titanium (Ti) | 0.5 – 1% |
Boron (B) | 0.01% max |
Carbon (C) | 0.03% max |
Zirconium (Zr) | 0.01% max |
Niobium (Nb) | 1% max |
Nickel forms the base of the alloy and provides a face-centered cubic matrix for high temperature strength. Elements like chromium, cobalt, and molybdenum contribute to solid solution strengthening and enable precipitation hardening.
Aluminum and titanium are added to form gamma prime precipitates Ni3(Al,Ti) to provide hardness and creep resistance up to 700°C. Tantalum provides solid solution strengthening and forms carbides for grain structure control. Boron facilitates precipitation of complex carbides.
The balanced composition of K465 nickel superalloy powder results in a combination of strength, ductility, corrosion resistance, and weldability required for high performance additive manufactured components. The optimized levels of alloying elements can be tailored based on final part requirements.
K465 Alloy Powder Properties
K465 superalloy powder processed via laser powder bed fusion or electron beam melting exhibits the following properties in as-built and heat treated states:
Mechanical Properties
Property | As-Built Condition | After Heat Treatment |
---|---|---|
Tensile Strength | 1050 – 1250 MPa | 1150 – 1350 MPa |
Yield Strength | 750 – 950 MPa | 1000 – 1200 MPa |
Elongation | 10 – 25% | 8 – 15% |
Hardness | 35 – 45 HRC | 42 – 48 HRC |
- High strength levels comparable to cast and wrought Ni-based superalloys
- Ductility retained after heat treatment allows some forming/forging
- Precipitation hardening by gamma prime phase after solution treatment
Physical Properties
Property | Value |
---|---|
Density | 8.1 – 8.3 g/cc |
Melting Point | 1260 – 1350°C |
Thermal Conductivity | 11 – 16 W/m-K |
Thermal Expansion Coefficient | 12 – 16 x 10<sup>-6</sup> /K |
High Temperature Properties
Property | Value |
---|---|
Service Temperature | Up to 700°C |
Oxidation Resistance | Good up to 850°C |
Phase Stability | Retains strength up to 70% of melting point |
Creep Rupture Strength | 140 MPa at 700°C for 1000 hours |
- Retains over half its strength at maximum service temperature
- Resists oxidation and hot corrosion in gas turbine environments
- Excellent creep rupture strength under load at high temperature
Other Notable Properties
- Weldable using conventional fusion welding methods
- Good surface finish and dimensional accuracy in AM builds
- Customizable with different heat treatments
- High thermal fatigue and crack growth resistance
The balanced set of mechanical, physical, and thermal properties make K465 suitable for extreme environments faced in aerospace engines, power generation systems, and chemical processing equipment. The properties can be fine-tuned based on application requirements.
K465 Alloy Powder Applications
The major applications of additive manufactured K465 superalloy parts include:
Aerospace:
- Combustor liners,augmentors, flame holders in jet engines
- Structural brackets, frames, housings, fittings
- Hot section components like turbine blades and vanes
- Rocket propulsion systems and spacecraft engines
Power Generation:
- Heat exchangers, piping, valves, manifolds in boilers and heat recovery systems
- Gas turbine hot gas path components like nozzles, shrouds
- Solar power receivers and collectors
Automotive:
- Turbocharger wheels and housings
- Exhaust system manifolds and components
Chemical Processing:
- Reformer tubes, reaction vessels, heat exchanger components
- Piping, valves, pumps for corrosive chemicals
- Tooling like mandrels, fixtures for composite parts
Benefits:
- Withstands sustained use at over 700°C lower density than competing alloys
- Oxidation and corrosion resistance in hot gas environments
- Reduces component weight compared to cast nickel alloys
- Enables complex optimized geometries not possible with casting
- Consolidates multiple parts into one printed component
- Saves material waste relative to subtractive methods
- Shorter lead times compared to traditional processing
K465 is frequently used as substitute for heavier, costlier superalloys in aerospace engines and land-based power systems. The alloy powder can be tailored to meet requirements in extreme temperature, pressure, and corrosive service conditions.
K465 Alloy Powder Specifications
K465 alloy powder for AM processes is supplied by various manufacturers to the following nominal specifications:
Parameter | Specification |
---|---|
Particle size distribution | 15 – 53 microns |
Oxygen content | 0.05% max |
Nitrogen content | 0.05% max |
Morphology | Spheroidal |
Apparent density | 4.0 – 4.5 g/cc |
Tap density | 4.5 – 5.0 g/cc |
Flow rate | 15 – 25 s/50g |
- Powder particle size distribution optimized for AM processes
- High powder flowability ensures uniform layer spreading
- Low oxygen content minimizes risk of defects in builds
- Spherical morphology provides good packing and powder bed density
Additional Requirements:
- Powder should be handled in an inert atmosphere to prevent contamination
- Moisture content must be kept below 0.1 wt% for good powder flow
- Temporary storage life up to 1 year in sealed containers with argon
- Open containers to be used within 1 week to avoid degradation
Meeting powder specifications in terms of size, shape, chemistry, and handling is critical to achieving high density AM parts with expected mechanical properties.
K465 Alloy Powder Availability
K465 superalloy powder can be sourced from major suppliers like:
Manufacturer | Product Name |
---|---|
Praxair | TA1 |
Carpenter Additive | CarTech K465 |
Sandvik Osprey | K465-TCP |
Erasteel | Stellite AM K465 |
The alloy powder is sold in various sizes ranging from 1 kg containers for R&D purposes up to 1000 kg containers for production volumes. Prices range from $90-150 per kg based on quantity and manufacturer.
Lead times for procurement typically range from 2-8 weeks after order confirmation. Customized particle size distributions and special handling may require a longer lead time.
K465 powder inventory should be monitored closely and reordered well in advance of running out. Shortages can cause costly AM machine downtime. Consider spacing out orders over time to maintain stock.
K465 Alloy Powder Processing
Parameter Ranges for AM Processes:
Process | Preheating Temp | Layer Thickness | Laser Power | Scan Speed | Hatch Spacing |
---|---|---|---|---|---|
DMLS | 150 – 180°C | 20 – 60 μm | 195 – 250 W | 600 – 1200 mm/s | 0.08 – 0.12 mm |
EBM | 1000 – 1100°C | 50 – 200 μm | 5 – 25 mA | 50 – 200 mm/s | 0.1 – 0.2 mm |
- DMLS = Direct metal laser sintering
- EBM = Electron beam melting
- A wider range of parameters allows flexibility to optimize for surface finish, build time, or mechanical properties
- Preheating reduces residual stresses; higher for EBM due to higher temperatures
- Slower scan speeds improve density but prolong build time
- Fine hatch spacing reduces porosity but requires more scan passes
Post-Processing:
- Removal of parts from build plate using EDM wire cutting
- Removal of residual powder via glass bead blasting
- Stress relief heat treatment at 870°C for 1 hour
- HIP treatment at 1160°C under 100 MPa pressure for 4 hours
- Age hardening heat treatment at 760°C for 10 hours
Benefits of Post-Processing:
- HIP closes internal voids and minimizes porosity
- Heat treatments relieve residual stress and achieve optimal hardness
- Yields close to 100% dense parts with mechanical properties equivalent to cast and wrought
- Additional hot isostatic pressing (HIP) and heat treatments can further enhance properties
Parameter selection, support structures, build orientation, post-processing steps are all optimizable based on AM technology used and properties required.
How K465 Compares with Other Superalloy Powders
K465 vs Inconel 718
Alloy | K465 | Inconel 718 |
---|---|---|
Density | Higher | Lower |
Tensile Strength | Similar | Similar |
Service Temperature | 100°C higher | Up to 650°C |
Cost | 2X more expensive | More economical |
- K465 chosen for higher temperature capability where cost increase is justified
- Inconel 718 more economical for lower temperature applications
K465 vs Haynes 282
Alloy | K465 | Haynes 282 |
---|---|---|
Processability | Better | More difficult |
Thermal conductivity | Higher | Lower |
Service temperature | Similar | Similar |
Cost | Similar | Similar |
- K465 easier to laser print and post-process without cracking
- Haynes 282 more prone to solidification cracks during builds
K465 vs CM 247 LC
Alloy | K465 | CM 247 LC |
---|---|---|
Density | Lower | Higher |
Strength | Similar | Similar |
Ductility | Higher | Lower |
Cost | Lower | Higher |
- K465 has better combinaton of strength and ductility
- Lower cost alloy alternative to CM 247 LC
K465 vs Inconel 625
Alloy | K465 | Inconel 625 |
---|---|---|
Service Temperature | Higher | Up to 700°C |
Corrosion Resistance | Moderate | Excellent |
Cost | Higher | Lower |
Availability | More limited | Readily available |
- Inconel 625 chosen where corrosion resistance trumps high temperature capability
- K465 preferred for jet engine parts seeing extreme temperatures
Understanding where K465 excels or falls short compared to alternatives aids material selection for AM components. The alloy can be tailored to shift the balance between cost, availability, processability, and properties.
K465 Alloy Powder – Frequently Asked Questions
Q: What pre-processing steps are required for K465 powder?
A: K465 powder needs to be dried for 1-4 hours at 100-150°C to remove moisture absorbed during shipping and storage. Sieving between 20-63 microns will eliminate large particles that can cause recoater issues.
Q: Does K465 require hot isostatic pressing (HIP) post-processing?
A: HIP is recommended but not mandatory for K465. It helps close internal voids and achieve maximum density and mechanical properties. HIP at 1160°C under 100 MPa for 4 hours is typical.
Q: What heat treatments can be used to tailor K465 properties?
A: Solution treatment at 1150°C plus single or double aging between 700-850°C is used to optimize strength and ductility. Rapid cooling after solution treatment enhances properties.
Q: Is K465 superalloy weldable for repair purposes?
A: Yes, K465 can be welded using ER NiCrMo-10 filler metal. Solution treatment at 1175°C and aging at 845°C is required after welding to restore properties.
Q: What manufacturing defects can occur with K465 builds?
A: Lack of fusion porosity, cracking between layers, delamination, and distortion are potential defects requiring parameter optimization. Lower preheat and faster scan speeds increase risk.
Q: What finishing methods can be used on additively manufactured K465 parts?
A: Machining, shot peening, chemical etching, and electropolishing allow surface roughness improvement. This facilitates NDE inspection and improves fatigue life.
Q: Does K465 alloy powder require special storage precautions?
A: K465 powder rapidly absorbs moisture, so storage in sealed argon purged containers is required. Use within 1 week of opening container to prevent degradation.
Q: What safety precautions are needed when handling K465 powder?
A: K465 powder is not flammable but may cause skin/eye irritation. Use protective gloves, clothing, face shields. Avoid inhalation and install proper ventilation.
Conclusion
K465 nickel superalloy powder has found increased adoption in additive manufacturing, enabling lightweight, high strength components with complex geometries. Its balanced composition provides a potent combination of mechanical properties, oxidation resistance, thermal stability, and weldability. These attributes make K465 suitable for aerospace propulsion systems, land-based power generation equipment, and chemical processing hardware enduring sustained high temperature service.
Understanding the niche where K465 outperforms alternatives such as Inconel 718 or Haynes 282 allows proper material selection. Careful control of AM process parameters, powder quality, heat treatments, and hot isostatic pressing is necessary to obtain optimal microstructure and performance. As additive manufacturing capabilities continue evolving, engineered materials like K465 will open new possibilities for designing next generation high temperature components with extended service life.
Get Latest Price
About Met3DP
Product Category
HOT SALE
CONTACT US
Any questions? Send us message now! We’ll serve your request with a whole team after receiving your message.
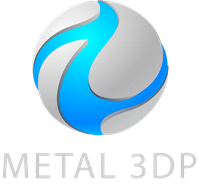
Metal Powders for 3D Printing and Additive Manufacturing