Nickel Alloy C276 Powder
Nickel Alloy C276 powder, also known as Hastelloy C276 powder, is a nickel-molybdenum-chromium alloy powder with high corrosion resistance. It has excellent resistance to a wide range of corrosive environments, especially oxidation and chloride-ion stress corrosion cracking.
Low MOQ
Provide low minimum order quantity to meet different needs.
OEM & ODM
Provide customized products and design services to meet unique customer needs.
Adequate Stock
Ensure fast order processing and provide reliable and efficient service.
Customer Satisfaction
Provide high quality products with customer satisfaction at the core.
share this product
Table of Contents
Overview
Nickel Alloy C276 powder, also known as Hastelloy C276 powder, is a nickel-molybdenum-chromium alloy powder with high corrosion resistance. It has excellent resistance to a wide range of corrosive environments, especially oxidation and chloride-ion stress corrosion cracking.
Some key properties and characteristics of Nickel Alloy C276 powder include:
Nickel Alloy C276 Powder Key Properties
Composition | Nickel (Balance), Molybdenum (15-17%), Chromium (14.5-16.5%), Iron (4-7%), Tungsten (3-4.5%) |
Density | 8.89 g/cm3 |
Melting Point | 1390°C (2530°F) |
Thermal Conductivity | 11 W/m-K |
Electrical Resistivity | 1.24 microhm-cm |
Oxidation Resistance | Excellent up to 1095°C |
Corrosion Resistance | Extremely high in wide range of environments |
Key Attributes | High strength, good fabricability, outstanding corrosion resistance |
Nickel Alloy C276 powder can be used to manufacture parts using additive manufacturing techniques like selective laser sintering (SLS), direct metal laser sintering (DMLS), laser powder bed fusion (L-PBF) and binder jetting. This allows complex geometries to be created with very good mechanical properties.
Some of the key applications and uses of Nickel Alloy C276 powder include:
Applications of Nickel Alloy C276 Powder
Oil & Gas Industry | Wellhead valves, Christmas trees, flowlines, subsea components |
Chemical Industry | Pumps, valves, reaction vessels, heat exchangers |
Pollution Control | Scrubbers, precipitators, stacks, ducts, fans |
Pharmaceutical Industry | Reactor vessels, containers, valves, pipework |
Food Processing Industry | Tanks, valves, pipework, conveyors, nuts and bolts |
Marine Applications | Propeller shafts, corrosion-resistant fasteners, water-cooled exhaust manifolds |
Aerospace Industry | Engine mounts, exhaust nozzle guides, thrust reverser systems, nacelle components |
Composition
The typical composition of Nickel Alloy C276 powder is:
Typical Composition of Nickel Alloy C276 Powder
Element | Weight % |
---|---|
Nickel (Ni) | Balance |
Molybdenum (Mo) | 15-17% |
Chromium (Cr) | 14.5-16.5% |
Iron (Fe) | 4-7% |
Tungsten (W) | 3-4.5% |
Manganese (Mn) | 1% max |
Silicon (Si) | 0.5% max |
Phosphorus (P) | 0.02% max |
Sulfur (S) | 0.03% max |
Carbon (C) | 0.01% max |
The high nickel and molybdenum content gives Nickel Alloy C276 excellent corrosion resistance. The chromium helps provide oxidation resistance. Trace elements like manganese, silicon, phosphorus and sulfur are minimized as they can negatively impact corrosion resistance if present in higher amounts. The low carbon content minimizes carbide precipitation.
Properties and Characteristics
Nickel Alloy C276 powder has the following key properties and characteristics:
Properties of Nickel Alloy C276 Powder
Density | 8.89 g/cm3 |
Melting Range | 1315-1390°C (2400-2530°F) |
Thermal Conductivity | 11 W/m-K (~64 Btu-in/ft2-h-°F) |
Electrical Resistivity | 1.24 microhm-cm at 20°C |
Modulus of Elasticity | 205 GPa |
Poisson’s Ratio | 0.29 |
Tensile Strength | 515-750 MPa (75-110 ksi) |
Yield Strength (0.2% offset) | 205-515 MPa (30-75 ksi) |
Elongation | 25-45% |
Hardness | 25-35 HRC |
Oxidation Resistance | Resistant up to 1095°C |
Coefficient of Thermal Expansion | 13 μm/m-°C |
Heat Treatment | Solution treated and rapid quenched |
Some key features and advantages of Nickel Alloy C276 powder include:
- Extremely high corrosion resistance especially to pitting and crevice corrosion
- Excellent resistance to oxidation and other high temperature effects up to ~1100°C
- High strength from ambient up to elevated temperatures
- Good weldability using conventional welding methods
- Good formability allowing a range of fabrication options
- Higher strength compared to other nickel alloys
- Lower carbon content improves corrosion resistance
Specifications
Nickel Alloy C276 powder is available in various size ranges depending on the application and manufacturing process to be used. Some typical size specifications include:
Typical Size Specifications of Nickel Alloy C276 Powder
Particle Size | 15-45 μm |
Apparent Density | ~2.5 g/cm3 |
Flow Rate | ~25 s/50g |
Size Distribution | D10: 20 μm; D50: 35 μm; D90: 40 μm |
Larger powder sizes may be available up to 140 mesh size (~100 μm). Smaller powder is also produced down to nano powder size (~50 nm) for advanced applications.
Various national and international specifications apply to Nickel Alloy C276 powder based on composition, condition and testing:
- AMS 5874 – Wrought Nickel Alloy C276 for General Purposes
- ASME SB-574 – Wrought Nickel Alloy C276 for Pressure Vessels
- ASTM B575 – Standard Specification for Low-Carbon Nickel Alloy Plate, Sheet, and Strip
- ISO 15156/NACE MR0175/MR0103 – Petroleum and natural gas industries
Suppliers and Pricing
Some leading global suppliers of Nickel Alloy C276 powder include:
Key Suppliers of Nickel Alloy C276 Powder
Supplier | Location |
---|---|
Sandvik | Sweden |
Praxair | USA |
Carpenter Technology | USA |
Hoganas | Sweden |
LPW Technology | UK |
TLS Technik | Germany |
Nickel Alloy C276 powder is more expensive than nickel-based superalloys due to the high molybdenum content. Cost also depends significantly on order volume and particle size distribution. Some approximate powder pricing is:
- Small volumes (<100 kg) – $100-150 per kg
- Large volumes (>1,000 kg) – $50-90 per kg
How to Choose Nickel Alloy C276 Powder
There are a few key factors to consider when selecting Nickel Alloy C276 powder:
Key Selection Criteria for Nickel Alloy C276 Powder
Parameter | Details |
---|---|
Manufacturing Process | Match powder size and shape to requirements of additive or other process |
Part Properties | Strength, corrosion resistance, high temperature resistance needs |
Operating Conditions | Temperature, pressure, media to confirm adequate performance |
Industry Standards | Compliance for applications in oil & gas, chemical, food processing etc |
Part Geometry | Complexity, surface finish, precision requirements |
Testing and Certification | Confirm composition, lack of contamination, lot test reports |
Price | Balance performance needs with budget constraints |
It is critical to start by understanding the application, operating conditions and properties needed. The manufacturing process determines suitable powder characteristics like particle size distribution, morphology and flowability. Chemical composition should be confirmed with the supplier’s certificate of analysis. Sample testing can validate key properties before full-scale production.
Applications and Use Cases
Nickel Alloy C276 finds widespread use in demanding heat and corrosion environments across various industries:
Industries and Applications for Nickel Alloy C276 Powder
Industry | Components and Parts |
---|---|
Oil & Gas | Wellhead valves, subsea flowlines, connectors, offshore rigs |
Petrochemical | Heat exchangers, condensers, process vessels |
Marine | Shafts, propellers, fasteners, exhaust components |
Pollution Control | Scrubber internals, fans, ducts, stacks |
Food Processing | Tanks, pipework, valves, nuts/bolts |
Some specific application examples include:
- Oil platforms – Seawater lift pumps, piping systems, wellhead Christmas trees, subsea components like connectors, flowlines, jumpers etc.
- Petrochemical plants – Heat exchanger tubing, condenser tubes, process vessels and tanks, pipes and valves carrying corrosive media
- Marine vessels – Components like propeller shafts, water-cooled exhaust manifolds, corrosion-resistant fasteners
- Desalination – Intake screens, high pressure pump components and plungers, reverse osmosis membrane housings
- Pollution control systems – FGD and SCR system internals like fans, ducts, stacks, scrubber liners exposed to acidic gases or seawater
- Food/beverage processing – Pipework, process vessels and tanks, nuts/bolts, valves carrying acidic foods
Some typical components manufactured in Nickel Alloy C276 powder include:
Typical Components Using Nickel Alloy C276 Powder
Components | Descriptions |
---|---|
Pumps | Centrifugal, positive displacement pumps for corrosive liquids |
Impellers | For process handling highly acidic or saline solutions |
Valves | Gate, ball, butterfly, globe valves in piping systems |
Nozzles | Spray nozzles for pollution control scrubbers |
Reaction Vessels | For chemical synthesis reactors under high temperature and pressure |
Heat Exchanger Tubes | Straight tubes or complex serpentine geometries |
Pipe Fittings | Elbows, tees, reducers conveying various corrosive media |
Nickel Alloy C276 Powder vs Alternatives
Nickel Alloy C276 is compared below with key alternative nickel and stainless-steel alloys:
Comparison of Nickel Alloy C276 Powder with Alternatives
Alloy | Corrosion Resistance | Temperature Resistance | Cost | Fabrication |
---|---|---|---|---|
Nickel Alloy C276 | Extremely High | Excellent to 1100°C | High | Good machinability/weldability |
Alloy C22 | Very Good | Very Good to ~1200°C | High | Weldable |
Alloy 625 | High | Excellent up to 1000°C | Medium | Easy fabrication |
316/316L Stainless Steel | Moderate | Fair up to 300°C | Low | Most readily fabricated |
Duplex Stainless | Excellent | Limited to 250°C | Low | More difficult fabrication |
Nickel Alloy C276 provides the best corrosion resistance across a wide range of aggressive environments compared to alternatives. It can reliably perform at high operating temperatures exceeding 1000°C. These benefits do come at a higher cost due to its specialized composition rich in strategic alloys. However, its ease of fabrication using standard methods provides a cost advantage over other more complex, proprietary alloys.
Limitations of Nickel Alloy C276
Despite its high performance, Nickel Alloy C276 does have some limitations to consider:
Limitations of Nickel Alloy C276 Powder
Limitation | Description |
---|---|
Cost | More expensive than stainless steels due to nickel and molybdenum content |
Fabrication | Heavier sections over 50mm can show lower corrosion resistance |
Section Thickness | Maximum recommended section is 25mm for optimum performance |
Thermal Processing | Special control of heating/cooling cycles needed to avoid impairing properties |
Thinner sections up to 25mm maintain consistently high corrosion resistance throughout. Care must also be taken to properly solution treat and quench finished parts to achieve full corrosion resistance without precipitation of deleterious phases. Overall though, Nickel Alloy C276 is engineered to be quite forgiving to fabricate relative to other highly alloyed materials.
FAQ
FAQ about Nickel Alloy C276 Powder
Question | Answer |
---|---|
What industries use Nickel Alloy C276? | Petrochemical, oil & gas, marine applications, chemical processing, pollution control, desalination |
Why is C276 better than stainless steel? | Far higher corrosion resistance, performs well at much higher temperatures |
What is Nickel Alloy C276 used for? | Pipes, valves, pumps, heat exchangers, fasteners – wetted parts in contact with aggressive chemicals/fluids |
What is the corrosion resistance of C276? | Extremely high resistance to pitting, crevice corrosion, stress corrosion cracking across range of acids, chlorides etc |
Can you weld Nickel Alloy C276? | Yes, C276 offers excellent weldability using a range of welding processes |
What alloy is similar to C276? | Alloy C22 offers comparable corrosion resistance but lower fabricability |
Is Hastelloy C276 expensive? | Yes, it costs more than stainless steel due to nickel/molybdenum but offers superior performance |
Is Nickel Alloy C276 compatible with seawater? | Yes, it has excellent resistance to saline environments making it ideal for marine applications |
Conclusion
Nickel Alloy C276 powder provides outstanding corrosion and temperature resistance coupled with good fabrication characteristics. This makes it an excellent choice for manufacturing critical parts and components exposed to aggressive operating environments across oil & gas, chemical processing and other industries. It does come at a premium cost but offers long, reliable service life with lower maintenance demands compared to other alloys. With additive manufacturing, it enables high complexity parts with properties equaling or exceeding tradition manufacturing. For extreme chemical corrosion or high temperatures approaching 1100°C, Nickel Alloy C276 is an ideal alloy system.
Get Latest Price
About Met3DP
Product Category
HOT SALE
CONTACT US
Any questions? Send us message now! We’ll serve your request with a whole team after receiving your message.
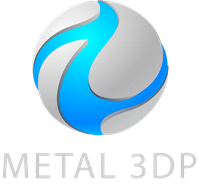
Metal Powders for 3D Printing and Additive Manufacturing