Nickel Alloy X750 Powder
Nickel Alloy X750 is a precipitation-hardenable nickel-chromium alloy that offers excellent resistance to corrosion and oxidation. It is noted for retaining strength, toughness and ductility after age hardening and has remarkable high temperature strength.
X750 has good formability in the annealed condition and can be easily fabricated using standard shop forming practices. It can be readily forged or otherwise hot worked. Cold forming presents no particular problems. It also has excellent weldability.
Here is an overview of Nickel Alloy X750 powder properties and applications:
Low MOQ
Provide low minimum order quantity to meet different needs.
OEM & ODM
Provide customized products and design services to meet unique customer needs.
Adequate Stock
Ensure fast order processing and provide reliable and efficient service.
Customer Satisfaction
Provide high quality products with customer satisfaction at the core.
share this product
Table of Contents
Overview
Nickel Alloy X750 Powder is a precipitation-hardenable nickel-chromium alloy that offers excellent resistance to corrosion and oxidation. It is noted for retaining strength, toughness and ductility after age hardening and has remarkable high temperature strength.
X750 has good formability in the annealed condition and can be easily fabricated using standard shop forming practices. It can be readily forged or otherwise hot worked. Cold forming presents no particular problems. It also has excellent weldability.
Here is an overview of Nickel Alloy X750 powder properties and applications:
Composition:
- Nickel: 70%
- Chromium: 15%
- Iron: 7%
- Titanium and Aluminum additions
Properties:
- Excellent resistance to corrosion and oxidation
- Retains high strength and toughness up to 1300°F (704°C)
- Age hardenable
- Easy to fabricate
- Good weldability
Applications:
- Gas turbines components
- Turbocharger components
- Heat treating fixtures
- Nuclear fuel element spacers
- Chemical and food processing equipment
Types and Designations
Nickel Alloy X750 powder is available with different particle size distributions:
Type | Particle Size |
---|---|
Fine grade | 15-45 μm |
Medium grade | 45-106 μm |
Coarse grade | 106-250 μm |
It also has several standard specifications and designations:
- UNS N07750
- WNR 2.4668
- AMS 5667
- ASME SB-171
- ASTM B640
Composition and Properties
The typical composition and properties of Nickel Alloy X750 powder are:
Table 1: Chemical composition of Nickel Alloy X750 powder
Element | Composition (%wt) |
---|---|
Nickel (Ni) | 70.0 min |
Chromium (Cr) | 14.0-17.0 |
Iron (Fe) | 5.0-9.0 |
Titanium (Ti) | 0.7-1.2 |
Aluminum (Al) | 0.2-1.0 |
Carbon (C) | 0.08 max |
Manganese (Mn) | 1.0 max |
Silicon (Si) | 1.0 max |
Copper (Cu) | 0.5 max |
Sulfur (S) | 0.015 max |
Phosphorus (P) | 0.015 max |
Table 2: Physical properties of Nickel Alloy X750 powder
Property | Value |
---|---|
Density | 8.36 g/cc |
Melting Point | 2400-2550°F (1315-1399°C) |
Thermal Conductivity | 9.4-12.4 W/m-K (68-218°F) |
Modulus of Elasticity | 31 x 106 psi |
Electrical Resistivity | 617 μΩ-cm |
Coefficient of Thermal Expansion | 8.1 x 10-6/°F (14.6 μm/m-°C) |
Table 3: Mechanical properties of Nickel Alloy X750 powder
Mechanical Property | Value |
---|---|
Tensile Strength | 190-240 ksi (1310-1655 MPa) |
0.2% Yield Strength | 140-190 ksi (965-1310 MPa) |
Elongation | 10-22% |
Hardness | Rockwell C 35-45 |
Applications and Uses
Some of the key applications for Nickel Alloy X750 powder include:
Table 4: Applications of Nickel Alloy X750 powder
Industry | Applications |
---|---|
Aerospace | Gas turbine engine components, Turbocharger components |
Automotive | Exhaust valves and components |
Industrial | Heat treating fixtures and trays |
Oil & Gas | Wellhead components, valves, pumps |
Chemical | Reactor vessels, piping, heat exchangers |
Food Processing | Pressure vessels, evaporators |
Nuclear | Fuel element spacers and springs |
The excellent heat and corrosion resistance make X750 suitable for use in high temperature environments seen in gas turbines, turbochargers, industrial furnaces and other extreme applications up to 1300°F (704°C).
Its high strength is valuable for components under mechanical stresses like valves, pumps and high pressure vessels and piping.
The outstanding room temperature tensile, yield, and creep-rupture properties in combination with oxidation resistance and fabricability provide proven advantages for many critical chemical processing industry applications.
Specifications and Availability
Nickel Alloy X750 powder is readily available from leading global specialty metal suppliers in various size distributions:
Table 5: Nickel Alloy X750 powder sizes and dimensions
Type | Particle Size | **ASTM Screen Size ** |
---|---|---|
Ultrafine | 1-5 μm | N/A |
Fine | 15-45 μm | -325 mesh |
Medium | 45-106 μm | 140-325 mesh |
Coarse | 106-250 μm | -140 mesh |
Table 6: Indicative pricing for Nickel Alloy X750 powder
Type | Condition | Price ($/kg) |
---|---|---|
Powder | -325 Mesh | $75 – $150 |
Powder | 140-325 Mesh | $50 – $120 |
Powder | -140 Mesh | $45- $100 |
Pricing can vary based on quantity and exact specifications. Contact leading manufacturers and suppliers for custom quotes.
Comparison with Alloy 718
Nickel Alloy X750 is part of the high-performance nickel-chromium family with similar compositions to the popular Alloy 718.
Here is a comparison between Alloy X750 and Alloy 718 powders on key parameters:
Table 8: Nickel Alloy X750 vs. Alloy 718 Comparison
Property | X750 | 718 |
---|---|---|
Density (g/cc) | 8.36 | 8.19 |
Melting Range (°F) | 2400-2550 | 2300-2350 |
Tensile Strength (ksi) | 190-240 | 160-220 |
Creep Strength | Better | Good |
Fabricability | Better | Moderate |
Weldability | Excellent | Moderate |
Corrosion Resistance | Excellent | Moderate |
Oxidation Resistance | Excellent | Poor |
Cost | Moderate | Inexpensive |
Availability | Moderate | Readily Available |
In summary, Alloy X750 demonstrates:
- Higher creep strength for high temperature serviceability
- Better fabricability and weldability for ease of manufacture
- Significantly improved corrosion and oxidation resistance
- Moderate cost premium over 718
Alloy X750 is the preferred choice for extreme environments while Alloy 718 offers a more economical solution for less critical applications.
Advantages and Limitations
Some of the main advantages and limitations of Nickel Alloy X750 powder include:
Table 9: Advantages of Nickel Alloy X750 powder
Advantages |
---|
Excellent room temperature tensile, yield and rupture strength |
Retains tensile strength up to 1300°F (704°C) |
Resistant to creep and thermal fatigue cracking |
Outstanding resistance to corrosion in reducing and oxidizing media up to 1800°F (982°C) |
Excellent oxidation resistance up to 2200°F (1204°C) |
Good formability in annealed state |
Readily forged or hot worked |
Easy to weld using conventional methods |
Processing and Manufacturing
Nickel Alloy X750 powder can be processed into finished components using various methods:
Casting
- Investment casting is commonly used. Ceramic molds enable pouring at 2600-2800°F (1427-1538°C). Produces highly sound castings.
- Sand casting can also be done but extra feeding of liquid metal is needed to get soundness. Special sand binders may be required.
- Shell mold casting yields products comparable to investment cast. Thin rolls can be produced.
- Continuous casting in graphite molds is widely used for producing billets for further processing.
Table 11: Casting specifications
Process | Sizes | Tolerances | Finishes |
---|---|---|---|
Investment | 0.1-100 lbs | ± 0.030 in/in | As-cast, HIP |
Sand | 25-2000 lbs | ± 0.125 in/in | As-cast, ground |
Shell | 0.5-75 lbs | ± 0.060 in/in | As-cast |
Continuous Cast | 3-12 in dia billets | ± 0.125 in/in dia | Hot worked |
Typical casting defects like hot tears, microporosity and segregation can occur but can be minimized by proper gating/risering, mold design and pouring/shakeout practices.
Deformation Processing
Hot working is performed between 2150-2300°F (1177-1260°C) followed by air cooling. Warm working is done below 1900°F (1038°C). Cold working may require intermediate annealing.
Common methods include:
- Forging: Closed die process produces best properties
- Rolling: Both flat and shape rolling performed. Minimum thickness reduction 30%
- Extrusion: Excellent properties achieved in sections up to 8 in dia
- Drawing: Heavy wire/bar can be drawn. Intermediate softening may be needed.
Table 12: Key specifications
Method | Size ranges | Reductions | Finishes |
---|---|---|---|
Forging | 0.1-1000 lbs | 30-90% | Hot worked |
Rolling | 0.05-500 lbs | 30-80% | Hot band |
Extrusion | 0.5-500 lbs | 75-90% | As extruded |
Drawing | 0.003-3 in dia | 30-65% | Bright annealed |
Joining Processes
All standard methods can effectively join X750 parts. Matching alloys preferred for optimum properties.
Welding: Gas tungsten arc (GTAW) and gas metal arc welding (GMAW) most widely employed. Resistance and laser beam welding also occasionally applied. Matching composition filler rods are used. Joints exhibit excellent strength. Proper preheat and post weld heat treatment essential to avoid cracking.
Brazing: Vacuum brazing gives best combination of strength and temperature resistance. Various silver braze alloys used with brazing done at 1900-2000°F (1038-1093°C). Critical to control clearances, fluxes and atmosphere.
Table 13: Joining recommendations
Process | Methods | Filler Metals | Comments |
---|---|---|---|
Welding | GTAW, GMAW | Alloy 625, 725 | Observe maximum interpass temps |
Brazing | Vacuum | Silver brazes | Fluxless preferred |
Cladding | Roll bonding | Copper alloys | Hot roll plated |
Fastening | Bolting, riveting | Alloy X750 | Use cold worked holes |
Post Processing Treatments
Solution heat treating and age hardening are used to develop optimum properties:
Solution Treatment – Performed at 2100-2300°F (1149-1260°C) followed by air or water quenching. Enables subsequent age hardening.
Age Hardening – Age at 1325-1425°F (± 25°F) for 10-50 hours followed by air cooling. Achieves precipitation hardening for maximum strength levels.
Optional stabilization treatment involves 850-1200°F for 1-16 hours to stabilize against future property changes.
Table 14: Post processing specifications
Process | Treatment | Expected Properties |
---|---|---|
Solution Treating | 2150°F (1177°C), 30 min, AC | Optimized microstructure |
Age Hardening | 1350°F (732°C), 24 hrs, AC | 190-240 ksi UTS |
Stabilization | 1000°F (538°C), 4 hrs, AC | Stable hardness |
Powder Production
Nickel Alloy X750 powder is commercially produced by gas atomization and water atomization methods. Particle size distribution tightly controlled through specialized nozzles and calibrated sieving. High purity inert gas used to prevent contamination.
Table 15: Powder production methods
Process | Sizes | Rate | Purity |
---|---|---|---|
Gas Atomization | 10-250 μm | 30-200 kg/hr | 99.9% |
Water Atomization | 25-150 μm | 20-100 kg/hr | 99.7% |
Both gas and water atomized powders show spherical particle morphology ideal for additive manufacturing, metal injection molding and other powder metallurgy applications.
Design Data
Key design data parameters for Nickel Alloy X750 are summarized below for reference during engineering and component design activities:
Table 16: Design data parameters for Nickel Alloy X750
Category | Values | Comments |
---|---|---|
Density | 0.302 lb/in3 | Moderate weight |
Young’s Modulus | 30.8 x 106 psi | Stiffness |
Poisson’s Ratio | 0.294 | – |
Shear Modulus | 11.7 x 106 psi | Resistance to shape change |
Electrical Resistivity | 617 μΩ-cm | Higher resistance than copper |
Coefficient of Friction | 0.46-0.80 | Varies based on surface finish |
Thermal Conductivity | 113-124 BTU-in/hr-ft2-°F | Higher than stainless steels |
Specific Heat | 0.106 BTU/lb-°F | – |
Mean CTE | 7.3 x 10-6 in/in-°F | Average between RT-500°F |
Prandtl Number | 0.012 | Ratio of momentum diffusivity to thermal diffusivity |
Heat Transfer Coefficient | 120-200 BTU/hr-ft2-°F | Depends on environment |
Structural Load Conditions
For structural engineering calculations at temperature extremes, use:
- Tensile yield strength: 140-190 ksi
- Compressive yield strength: 170-220 ksi
- Modular ratio, E (Alloy X750)/E (Steel): 1.0
At room temperature up to 500°F – Moderate corrosion rate of less than 0.002 in/yr expected.
Up to 1900°F – Excellent resistance to hot corrosion and oxidation. Use parabolic rate constant kp = 3.4 x 10-8 mg2/cm4/s.
Creep and Fatigue Resistance
Alloy X750 demonstrates excellent creep resistance. Rupture strength higher than 80 ksi for 100,000 hrs at 1300°F (980°C).
For cyclic fatigue conditions, use:
- Endurance (106 cycle) fatigue strength of 95-100 ksi
- Reduction factor of 1.0 for machined surface finish rather than as-fabricated
Environment has small effect on fatigue strength. Use fatigue reduction factor = 0.95 for air environment.
Machining Nickel Alloy X750
Nickel Alloy X750 has excellent machinability in the annealed state and can be machined using most standard workshop methods and tools.
Chip breakers recommended for effective chip control. Rigid setups needed to minimize vibration. Positive rake cutting tools with sharp cutting edges provide longest tool life.
Low thermal conductivity leads to heat concentration so copious coolant should be used.
Table 17: Machining methods
Method | Tool Materials | Speeds/Feeds | Comments |
---|---|---|---|
Turning | High speed steel, Carbide, Ceramic, CBN, PCD | 100-250 sfm | Use heavy depths of cut |
Drilling | Carbide with TiAlN coating | 10-30 sfm | Peck drill larger diameters |
Threading | Carbide inserts | 4-10 ipr | Maintain tool nose radius |
Milling | Carbide, |
Processing and Manufacturing
Nickel Alloy X750 powder can be processed into parts using various methods:
Additive Manufacturing
Additive manufacturing (AM), also known as 3D printing, uses the nickel alloy powder as feedstock for building up components layer by layer. Some AM techniques suitable for X750 include:
Direct Metal Laser Sintering (DMLS)
- Powder is selectively melted by a high power laser
- Produces fully dense parts with fine microstructure
- Excellent dimensional accuracy and surface finish
- Complex geometries possible
Electron Beam Melting (EBM)
- Powder is melted by an electron beam in vacuum
- Achieves near full density with good strength
- Lower surface finish compared to laser processes
- Fast build rates due to higher beam power
Binder Jetting
- Liquid bonding agent selectively deposited to join powder particles
- Cost-effective process with high productivity
- Requires post-processing like sintering and infiltration
- Larger parts possible with good geometric freedom
Cold Spray
- Powder particles accelerated to supersonic speeds and impacted on to a substrate
- Kinetic energy bonds particles to surface
- Thick coatings and freeform shapes can be built up
- Minimal heating preserves base material properties
Table 11: Additive manufacturing processes for Nickel Alloy X750
Process | Precision | Surface Finish | Mechanical Properties | Geometry | Speed |
---|---|---|---|---|---|
DMLS | High | Excellent | Predictable | Complex | Slow |
EBM | High | Moderate | Consistent | Complex | Moderate |
Binder jet | Moderate | Poor | Variable | Simple | Fast |
Cold spray | Low | Rough | Anisotropic | Simple | Fast |
Parameters like laser power, beam size, hatch spacing, and scanning strategy can be optimized to control part density, surface quality, microstructure and mechanical performance.
Heat treatments like hot isostatic pressing (HIP) and aging may be applied post-processing to further enhance densification and material properties.
Casting
The X750 alloy can also be induction melted and cast into ingots, billets and bars using processes like:
- Vacuum induction melting
- Electroslag remelting
- Investment casting
Cast products serve as feedstock for subsequent breakdown operations like forging, rolling and extrusion. They can also be machined directly into net shape components.
Deformation Processing
Various deformation techniques can be applied to cast nickel alloy feedstock:
Forging
- Pressing or hammering cast ingots between dies
- Improves strength through grain flow and work hardening
- Near net shapes can be achieved
Rolling
- Compressing and reducing thickness between rolls
- Produces sheets, strips and plates
- Controls grain structure and enhances properties
Extrusion
- Forcing through a die opening
- Forms long sections with fixed cross-section
- Dense product with uniform fine grains
Drawing
- Pulling through a die using tensile force
- Reduces cross-section of bars, tubes or wires
- Increased strength and hardness
The alloy is annealed periodically during working to restore ductility and avoid cracking. Final heat treatment and aging follows to achieve desired characteristics.
FAQs
Q: What is Nickel Alloy X750?
A: X750 is a precipitation-hardenable nickel-chromium alloy with excellent strength up to 1300°F (700°C), outstanding corrosion and oxidation resistance, and good fabrication characteristics.
Q: What are the typical applications for X750?
A: Gas turbines components, turbocharger parts, nuclear fuel elements, chemical processing equipment, food processing vessels – anywhere needing capability at high temperatures in harsh environments.
Q: Is Nickel Alloy X750 weldable?
A: Yes, X750 has good weldability for a high-strength precipitation-hardened alloy. Gas tungsten arc and gas metal arc welding can produce sound welds. Stress relieving heat treatment is often employed after welding.
Get Latest Price
About Met3DP
Product Category
HOT SALE
CONTACT US
Any questions? Send us message now! We’ll serve your request with a whole team after receiving your message.
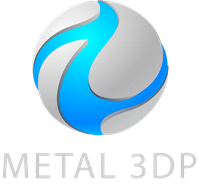
Metal Powders for 3D Printing and Additive Manufacturing