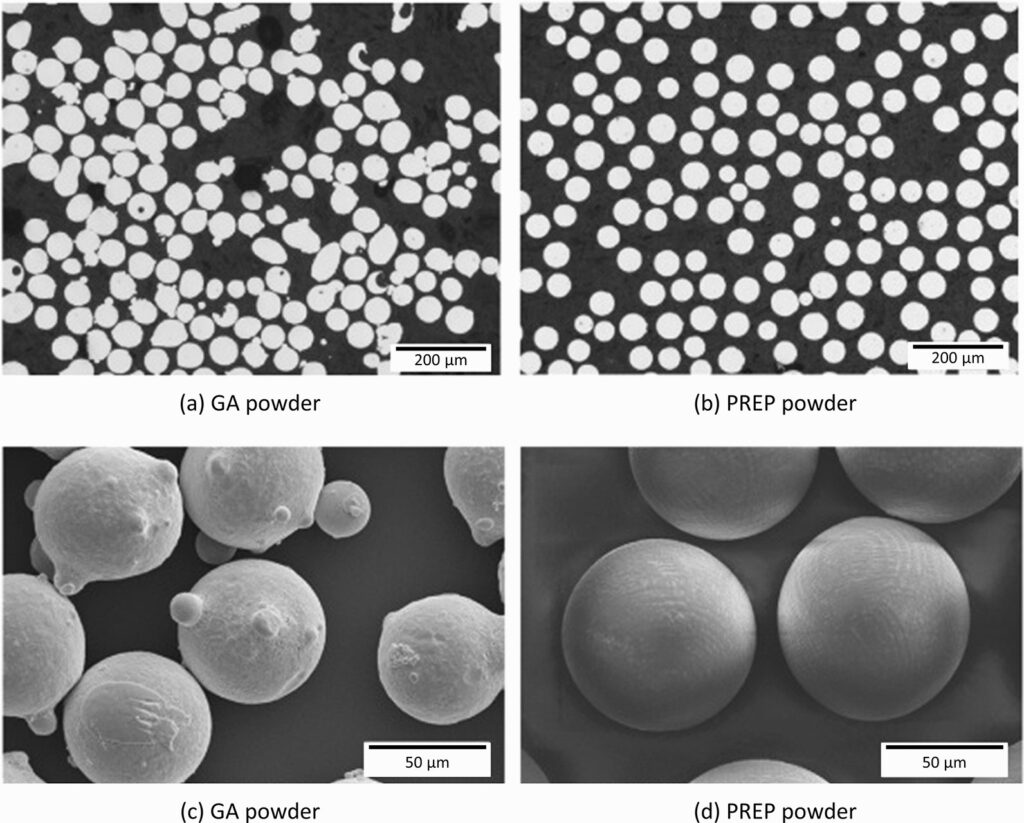
PTA/Flame Spray Powder: The Ultimate Guide to Surface Coating Solutions
Low MOQ
Provide low minimum order quantity to meet different needs.
OEM & ODM
Provide customized products and design services to meet unique customer needs.
Adequate Stock
Ensure fast order processing and provide reliable and efficient service.
Customer Satisfaction
Provide high quality products with customer satisfaction at the core.
share this article
Table of Contents
In industries where material durability, corrosion resistance, and wear protection are paramount, PTA (Plasma Transferred Arc) and Flame Spray powders have emerged as indispensable solutions. These powders are used in advanced surface coating processes to enhance the performance and longevity of components, especially in harsh environments. If you’re new to the world of thermal spraying or looking for more detailed insights, you’re in the right place.
This guide will take you through the fundamentals of PTA and Flame Spray powders, their types, applications, specifications, and more. Whether you’re an engineer, manufacturer, or just curious about industrial coatings, this comprehensive guide will cover all your needs.
Overview of PTA/Flame Spray Powders
PTA and Flame Spray powders are metallic and ceramic materials used to coat surfaces, typically through thermal spray techniques. These powders are melted and sprayed onto a substrate to form a protective layer, which can significantly improve the surface properties of the component being coated.
Key Features of PTA/Flame Spray Powders:
- Composition: Typically made from metals, alloys, or ceramics.
- Primary Use: Surface protection against wear, corrosion, heat, and oxidation.
- Coating Methods: Applied using Plasma Transferred Arc (PTA) or Flame Spray technologies.
- Industries: Widespread use in aerospace, oil & gas, automotive, and manufacturing industries.
- Benefits: Extended component life, improved performance, and reduced maintenance costs.
Both PTA coating and Flame Spray processes are highly customizable, allowing users to select powders that best suit their specific application needs. The result? Stronger, more durable surfaces that can withstand extreme environments.
Types, Composition, and Properties of PTA/Flame Spray Powders
The choice of powder depends on the specific requirements of the coating application—whether you need wear resistance, corrosion protection, or thermal insulation. PTA and Flame Spray powders come in various forms, each tailored for different functionalities.
Types of PTA/Flame Spray Powders
Powder Type | Composition | Properties | Common Use |
---|---|---|---|
Nickel-Based Alloys | Nickel, Chromium, Boron | Excellent corrosion and wear resistance | Valves, shafts, and turbine blades |
Cobalt-Based Alloys | Cobalt, Chromium, Tungsten | High-temperature strength and wear resistance | Aerospace and power generation components |
Iron-Based Alloys | Iron, Chromium, Molybdenum | Cost-effective, good wear resistance | Automotive and general industrial components |
Ceramic Powders | Alumina, Zirconia, Titania | High hardness, thermal insulation | Thermal barrier coatings in gas turbines |
Carbide Powders | Tungsten Carbide, Chromium Carbide | Extreme wear resistance, high hardness | Cutting tools, mining equipment, and pumps |
Composite Powders | Mixture of metals and ceramics | Combined properties of metals and ceramics | High-performance coatings for specialized uses |
Each type of powder offers specific advantages. Nickel-based alloys are excellent for corrosion resistance, while carbide powders provide unmatched wear protection. Ceramic powders, on the other hand, are perfect for thermal barriers in high-temperature environments.
Properties of PTA/Flame Spray Powders
Property | Description |
---|---|
Melting Point | Varies by composition (e.g., Nickel-based alloys: 1,200–1,450°C) |
Hardness | Ranges from medium to extremely hard (HRC 40-70) |
Corrosion Resistance | High, depending on alloy composition (Nickel and Cobalt-based powders excel) |
Wear Resistance | Extremely high, particularly with carbide and ceramic-based powders |
Thermal Conductivity | Low for ceramic coatings, high for metallic coatings |
Oxidation Resistance | Excellent, particularly for alloys with chromium or aluminum content |
Density | Varies significantly (e.g., Tungsten Carbide: 15.6 g/cm³; Nickel-based alloys: 8.9 g/cm³) |
These properties make PTA and Flame Spray powders ideal for applications where components are exposed to extreme conditions, such as high temperatures, corrosive environments, or mechanical wear.
Applications of PTA/Flame Spray Powders
PTA/Flame Spray powders are used across a wide range of industries to protect components and extend their operational life. These powders allow industries to save on maintenance costs and avoid frequent equipment replacement.
Key Applications of PTA/Flame Spray Powders
Industry | Application | Benefits |
---|---|---|
Aerospace | Coating turbine blades and engine parts | High-temperature resistance, corrosion protection |
Oil & Gas | Coating valves, pumps, and drilling equipment | Extreme wear and corrosion resistance |
Automotive | Coating engine parts, pistons, and gear components | Improved wear resistance and extended service life |
Power Generation | Coating boiler tubes, steam turbines, and heat exchangers | Improved heat resistance and reduced oxidation |
Manufacturing | Coating molds, dies, and machine components | Enhanced wear resistance and reduced maintenance costs |
Mining | Coating mining equipment, drill bits, and excavation tools | Extreme hardness and wear resistance |
Medical | Coating surgical tools and implants | Biocompatibility and corrosion resistance |
Marine | Coating ship components and offshore equipment | Corrosion protection in seawater environments |
Pulp & Paper | Coating rolls, cutter blades, and pumps | Wear protection and corrosion resistance in harsh environments |
In industries such as aerospace and oil & gas, durability and resistance to extreme conditions are non-negotiable. PTA/Flame Spray powders provide the necessary protection to ensure that components perform reliably, even in the most demanding environments.
Specifications, Sizes, and Grades of PTA/Flame Spray Powders
When selecting PTA or Flame Spray powders, it’s important to consider the exact specifications required for your application. These include factors such as particle size, powder grade, and hardness.
Specifications and Grades of PTA/Flame Spray Powders
Specification | Details |
---|---|
Particle Size | Ranges from 5 to 150 microns, depending on the desired coating thickness |
Powder Form | Spherical, irregular, or angular |
Purity | High-purity versions available for critical applications |
Hardness | Varies by composition (e.g., Tungsten Carbide > HRC 70) |
Density | Varies based on the powder type (e.g., Cobalt-based alloys: 8.9 g/cm³) |
Flowability | Important for efficient spraying, particularly in Flame Spray processes |
Bond Strength | High bond strength to substrates, often > 10,000 psi |
Standards | Conforms to industry standards such as ASTM, ISO, and AWS |
Choosing the correct particle size and hardness is crucial. Finer particles are generally used for thinner coatings, while coarser particles are used when a thicker, more durable layer is required.
Suppliers and Pricing of PTA/Flame Spray Powders
The cost of PTA/Flame Spray powders can vary significantly based on the material, purity, and specific application requirements. Below is a guide to some of the leading suppliers and typical pricing.
Suppliers and Pricing of PTA/Flame Spray Powders
Supplier | Location | Powder Types Available | Price per Kg (Approx.) |
---|---|---|---|
Praxair Surface Technologies | USA | Nickel-based, Cobalt-based, Carbide powders | $100 – $500 |
Höganäs | Sweden | Iron-based, Nickel-based powders | $80 – $400 |
Kennametal | USA | Tungsten Carbide, Ceramic powders | $200 – $600 |
Oerlikon Metco | Switzerland | Metal and ceramic powders | $150 – $450 |
Saint-Gobain | France | Composite and Ceramic powders | $120 – $500 |
Wall Colmonoy | USA, UK | Nickel and Cobalt-based alloys | $130 – $400 |
Nickel and cobalt-based powders tend to be more expensive due to their excellent high-temperature and corrosion-resistant properties. Ceramic and carbide powders typically fall on the higher end of the pricing scale due to their extreme hardness and wear resistance.
Advantages and Limitations of PTA/Flame Spray Powders
Like any material, PTA/Flame Spray powders come with their own set of advantages and limitations. Understanding these can help you determine the best powder for your specific application.
Advantages vs. Limitations of PTA/Flame Spray Powders
Advantages | Limitations |
---|---|
Highly Durable Coatings: Exceptional wear and corrosion resistance | Cost: High-quality powders can be expensive |
Versatile: Suitable for a range of industries and applications | Application Complexity: Requires specialized equipment |
High-Temperature Resistance: Can withstand extreme heat | Surface Preparation: Requires meticulous prep work |
Customizable: Powders can be tailored to specific needs | Oxidation: Some powders may oxidize if not properly applied |
Extended Component Life: Reduces maintenance and downtime | Porosity: Some coatings may have slight porosity, affecting performance |
The high durability and customizability of these powders are clear advantages, but the cost and complexity of application are important factors to consider. While the initial investment might be higher, the extended lifespan of components often justifies the expense.
PTA/Flame Spray Powders vs. Other Coating Materials
When it comes to surface coatings, there are several alternatives to PTA/Flame Spray powders, such as thermal spray coatings, hard chrome plating, and chemical vapor deposition (CVD). How do they compare?
PTA/Flame Spray Powders vs. Other Coating Materials
Coating Material | Key Properties | Cost Comparison | Applications |
---|---|---|---|
PTA/Flame Spray Powders | High wear resistance, customizable coatings | Moderate to high | Aerospace, Oil & Gas, Automotive |
Hard Chrome Plating | Excellent wear resistance, but toxic process | Lower cost, but environmental concerns | Automotive, Heavy Machinery |
Thermal Spray Coatings | Moderate durability, less complex application | Lower cost | General industrial applications |
Chemical Vapor Deposition (CVD) | High precision, excellent corrosion resistance | High cost, complex process | Semiconductor, Aerospace |
Compared to thermal spray coatings, PTA/Flame Spray powders offer higher precision and durability, though at a higher cost. Hard chrome plating remains a cheaper alternative but comes with environmental and health hazards due to the toxic chemicals involved. CVD coatings provide high precision but are often cost-prohibitive for large-scale industrial applications.
Frequently Asked Questions (FAQ) About PTA/Flame Spray Powders
Common Questions About PTA/Flame Spray Powders
Question | Answer |
---|---|
What is PTA coating? | PTA (Plasma Transferred Arc) coating uses metallic powders to create durable, high-strength coatings. |
What industries use Flame Spray powders? | Aerospace, automotive, oil & gas, and manufacturing industries use Flame Spray powders. |
How are PTA and Flame Spray powders applied? | Powders are applied through thermal spray processes, where they are melted and sprayed onto the surface. |
What materials are used in PTA/Flame Spray powders? | Common materials include nickel-based, cobalt-based, ceramic, and carbide powders. |
What is the cost of PTA/Flame Spray powders? | Costs range from $80 to $600 per kilogram, depending on the material and purity. |
Are PTA and Flame Spray coatings durable? | Yes, these coatings are highly durable, offering excellent wear and corrosion resistance. |
Can ceramic powders be used in Flame Spray processes? | Yes, ceramic powders like alumina and zirconia are commonly used for thermal insulation and wear resistance. |
Conclusion
PTA and Flame Spray powders are at the forefront of industrial surface coating technologies. Their ability to provide enhanced protection from wear, corrosion, and high temperatures has made them invaluable in industries ranging from aerospace to oil & gas.
By choosing the right powder for the job—whether it’s a nickel-based alloy for corrosion resistance or a ceramic powder for thermal barriers—you can significantly extend the life of your components and reduce maintenance costs. While the upfront investment in these powders and their application processes can be higher, the long-term savings and improved performance are well worth it.
As industries continue to demand more from their materials, PTA and Flame Spray powders will undoubtedly play an ever-growing role in meeting those challenges. Whether you’re looking to improve wear resistance or protect components in extreme environments, PTA/Flame Spray powders offer a versatile and reliable solution.
Get Latest Price
About Met3DP
Product Category
HOT SALE
CONTACT US
Any questions? Send us message now! We’ll serve your request with a whole team after receiving your message.
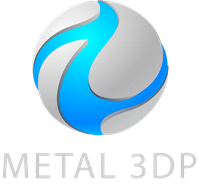
Metal Powders for 3D Printing and Additive Manufacturing