introduction to Selective Laser Melting (SLM)
Table of Contents
I’d be glad to provide an informative and comprehensive article on Selective Laser Melting (SLM), incorporating the requested structure, SEO optimization, and engaging storytelling approach while adhering to your specific guidelines:
Selective Laser Melting (SLM)
Imagine a world where complex metal parts, previously impossible to manufacture with traditional techniques, can be created layer by layer with incredible precision. This visionary leap becomes reality with Selective Laser Melting (SLM), an additive manufacturing (AM) process transforming the landscape of metal fabrication.
What is SLM?
At its core, SLM, also known as direct metal laser sintering (DMLS), is a powder bed fusion (PBF) technique that utilizes a high-powered laser to selectively melt metal powder particles, building a three-dimensional object one layer at a time. This layer-by-layer approach, akin to building with tiny Lego bricks, allows for the creation of intricate geometries, hollow structures, and internal features unachievable with conventional methods like casting or machining.
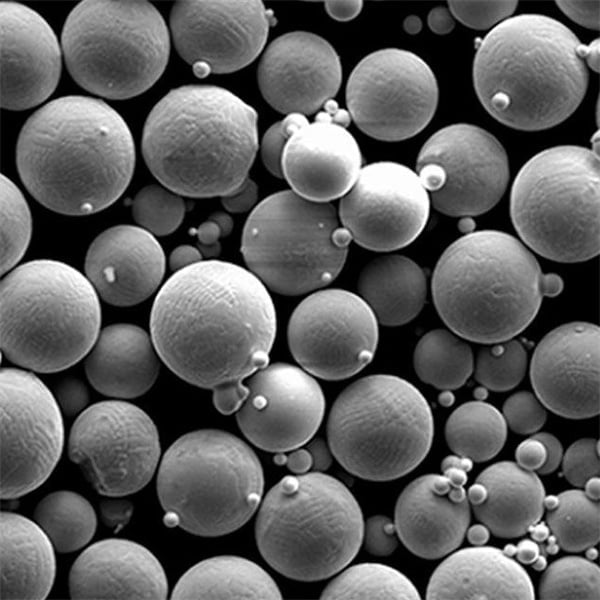
The Magic of SLM
- CAD Design: The journey begins with a computer-aided design (CAD) model, breathing life into the digital blueprint of the desired part.
- Powder Bed Preparation: A thin layer of metal powder, meticulously chosen for its properties and intended application, is spread across a platform within the SLM machine.
- Laser Melting: A high-powered laser beam, typically a Yb-fiber laser, scans the powder bed according to the digital slice extracted from the CAD model. The laser’s focused energy precisely melts the designated regions, fusing the metal particles to form a solid layer.
- Layer by Layer: The platform lowers slightly, and a fresh layer of powder is deposited. This meticulous dance of laser melting and powder deposition continues, meticulously building the object layer by layer until it’s complete.
- Post-Processing: Once complete, the printed part undergoes support structure removal and, depending on the material and application, additional treatments like heat treatment or surface finishing may be required.
Suitable metal powder for SLM
The success of SLM hinges on the selection of the appropriate metal powder. Each material boasts unique properties, influencing printability, mechanical performance, and cost. Here’s an exploration of ten commonly used metal powders in SLM:
Metal Powder | Composition | Properties | Applications |
---|---|---|---|
Stainless Steel 316L | Fe (66-70%), Cr (16-18%), Ni (10-14%), Mo (2-3%), Si (<1%), Mn (<2%) | Excellent corrosion resistance, high strength, biocompatible | Aerospace components, medical implants, chemical processing equipment |
Titanium Ti6Al4V | Ti (89-92%), Al (5.5-6.5%), V (3.5-4.5%) | High strength-to-weight ratio, good corrosion resistance, biocompatible | Aerospace parts, medical implants, sporting goods |
Inconel 625 | Ni (58%), Cr (20-23%), Mo (9%), Fe (5%), Mn (2%) | High-temperature strength, excellent corrosion resistance | Gas turbine components, heat exchangers, chemical processing equipment |
Aluminum AlSi10Mg | Al (88-92%), Si (9-11%), Mg (0.3-0.6%) | Good strength, lightweight, excellent printability | Automotive components, aerospace parts, consumer electronics |
Copper Cu | Cu (99.9%) | High electrical conductivity, good thermal conductivity | Heat exchangers, electrical components, fluid handling systems |
Nickel Ni | Ni (99.5%) | High electrical conductivity, magnetic properties | Electrical components, sensors, catalysts |
Cobalt CrCo | Co (60%), Cr (20%), W (15%) | High wear resistance, good corrosion resistance | Cutting tools, wear-resistant components, molds |
Tool Steel | Varies depending on specific type | High hardenability, wear resistance | Cutting tools, dies, molds |
Precious Metals (Gold, Silver, Platinum) | Varies depending on the metal | High value, specific electrical properties | Jewelry, electronics, medical devices |
-
Ti45Nb Powder for Additive Manufacturing
-
TiNb Alloy Powder
-
TiNbZrSn Alloy Powder
-
Ti6Al4V Powder Titanium Based Metal Powder for Additive Manufacturing
-
CPTi Powder
-
TC18 Powder : Unlocking the Power of Titanium Carbide
-
TC11 Powder : A Comprehensive Guide
-
TC4 ELI Powder
-
Best Ti-6Al-4V powder (TC4 Powder)for additive manufacturing
the Advantages and Limitations of SLM
The Advantages of SLM:
- Design Freedom: SLM empowers the creation of complex geometries, internal channels, and lightweight structures, pushing the boundaries of design possibilities.
- Material Diversity: A vast array of metal powders caters to diverse applications, allowing for material selection based on specific performance needs.
- Reduced Waste: Compared to traditional subtractive manufacturing techniques, SLM minimizes material waste, promoting sustainability.
The Advantages of SLM (continued):
- Production Flexibility: SLM facilitates the creation of single parts or small batches without the need for expensive tooling, enabling on-demand manufacturing and rapid prototyping.
- Improved Functionality: SLM allows for the integration of complex features within a single part, enhancing functionality and reducing assembly complexity.
The Limitations of SLM:
- Cost: SLM machines and metal powders can be expensive, making this technology less suitable for high-volume, low-cost production.
- Surface Roughness: Due to the layer-by-layer nature of the process, SLM parts can exhibit a slightly rougher surface finish compared to some traditional methods. However, post-processing techniques can mitigate this to an extent.
- Material Properties: While the mechanical properties of SLM parts are generally good, they may not always perfectly match those of traditionally manufactured counterparts, particularly in specific alloys. Ongoing research and development are continuously improving material properties in SLM.
- Build Size Limitations: The build size of SLM machines is currently limited compared to some conventional techniques. However, larger machines are increasingly being developed.
application of SLM
SLM is steadily transforming various industries, leaving its mark on:
Aerospace: SLM’s ability to create lightweight, high-strength components is revolutionizing aircraft design, leading to fuel efficiency improvements and performance optimization.
Automobiles: The automotive industry is leveraging SLM for prototyping, creating lightweight structural components, and even producing customized parts for high-performance vehicles.
Medical Devices: SLM is playing a crucial role in the development of customized implants, prosthetics, and surgical instruments, offering enhanced biocompatibility and patient-specific solutions.
Consumer Goods: From personalized jewelry and sporting goods to innovative consumer electronics, SLM is enabling the creation of unique and functional products.
The Future of SLM: A Glimpse into the Horizon
As research and development in SLM continue to advance, we can expect to see even more exciting developments:
- Advanced materials: New metal powders with enhanced properties, including improved strength, heat resistance, and biocompatibility, are constantly being explored.
- Faster printing speeds and larger build sizes: Advancements in laser technology and machine design are pushing the boundaries of printing speed and build size limitations.
- Reduced costs: As technology matures and adoption increases, the cost of SLM machines and materials is expected to decrease, making this technology more accessible.
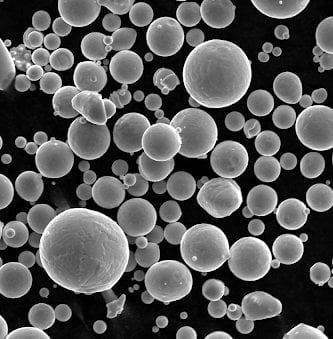
FAQs
Q: What are the typical costs associated with SLM?
A: The cost of SLM can vary significantly depending on several factors, including:
- Machine cost: The initial cost of the SLM machine can range from hundreds of thousands to millions of dollars.
- Material cost: The cost of metal powders can vary depending on the specific material and its properties.
- Part complexity: The complexity of the part design can significantly impact the printing time and material usage, influencing the overall cost.
- Post-processing requirements: Additional treatments like heat treatment or surface finishing can add to the final cost.
As a general estimate, the cost per kilogram of SLM-printed parts can range from several hundred dollars to tens of thousands of dollars.
Q: What are the strongest materials that can be printed using SLM?
A: Several high-strength materials can be printed using SLM, including:
- Inconel 625: This nickel-chromium-based superalloy boasts excellent high-temperature strength and is commonly used in demanding applications like gas turbine components.
- Titanium Ti6Al4V: This workhorse material offers a high strength-to-weight ratio and good corrosion resistance, making it popular for aerospace and medical applications.
- Tool steels: Various tool steel types can be printed using SLM, known for their superior wear resistance and hardness, ideal for cutting tools and dies.
It’s important to consult with SLM experts to determine the most suitable material for your specific application based on the required strength, other properties, and budget considerations.
Q: How does the surface roughness of SLM parts compare to traditionally manufactured parts?
A: Due to the layer-by-layer nature of the process, SLM parts can have a slightly rougher surface finish compared to parts produced by techniques like machining or casting. However, post-processing techniques like sandblasting, polishing, or machining can significantly improve the surface finish and achieve desired levels of smoothness.
Q: Is SLM an environmentally friendly manufacturing process?
A: Compared to traditional subtractive manufacturing techniques that generate significant material waste, SLM offers a more sustainable alternative. It allows for near-net-shape manufacturing, minimizing material waste. Additionally, the ability to produce parts on-demand can help reduce transportation needs
Conclusion
Selective Laser Melting (SLM) stands as a powerful testament to human ingenuity, pushing the boundaries of metal fabrication and unlocking a new era of design and manufacturing possibilities. As the technology continues to evolve, we can expect even more transformative applications across diverse industries. Whether it’s revolutionizing the way we build aircraft, creating life-changing medical implants, or fostering innovation in consumer goods, SLM is poised to leave an indelible mark on the future.
Share On
MET3DP Technology Co., LTD is a leading provider of additive manufacturing solutions headquartered in Qingdao, China. Our company specializes in 3D printing equipment and high-performance metal powders for industrial applications.
Inquiry to get best price and customized Solution for your business!
Related Articles
About Met3DP
Recent Update
Our Product
CONTACT US
Any questions? Send us message now! We’ll serve your request with a whole team after receiving your message.
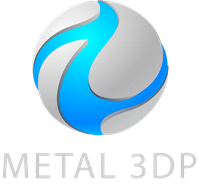
Metal Powders for 3D Printing and Additive Manufacturing