3D Printing Metal Powder suitable for SLM
Table of Contents
Imagine crafting intricate metal objects with pinpoint precision, layer by layer, from the comfort of your workshop. This isn’t science fiction; it’s the reality of Selective Laser Melting (SLM), a revolutionary 3D printing technology that’s transforming manufacturing. But at the heart of this process lies a crucial ingredient: metal powder.
Metal Powder for SLM
Metal powder for SLM isn’t your average sand from the beach. These specialized powders are meticulously engineered with specific particle size distributions, flow characteristics, and chemical compositions to ensure optimal performance in the SLM process.
Here’s a table summarizing the key characteristics of metal powder for SLM:
Characteristic | Description |
---|---|
Particle size distribution | Narrow and controlled distribution for precise layer formation and minimal porosity. |
Flowability | Excellent flow properties for smooth powder spreading during the printing process. |
Sphericity | Spherical or near-spherical particles for efficient packing and laser melting. |
Chemical composition | Tailored composition to achieve desired mechanical properties and functionality in the printed part. |
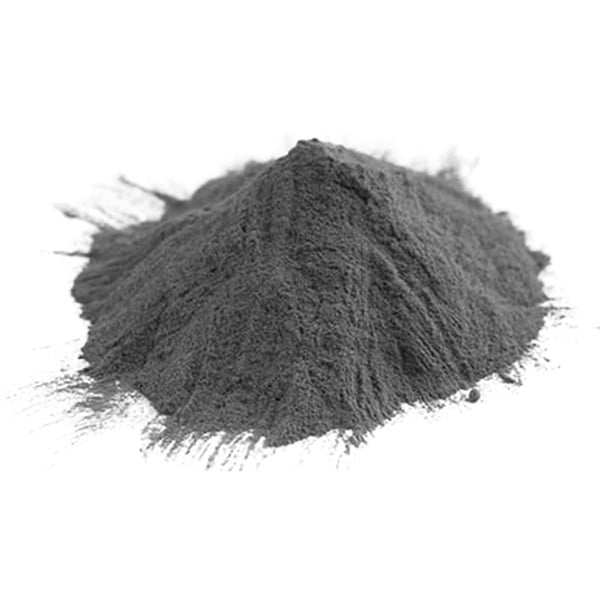
Exploring Different Metal Powders
The world of SLM metal powders boasts a diverse range of options, each offering unique advantages and catering to specific applications. Let’s delve into 10 popular metal powder choices:
- 316L Stainless Steel: A versatile and widely used option, offering excellent corrosion resistance, good mechanical properties, and biocompatibility. Think: medical implants, aerospace components, and chemical processing equipment.
- 17-4 PH Stainless Steel: Known for its high strength and hardness after heat treatment, ideal for applications requiring durability and wear resistance. Imagine: gears, shafts, and tools for demanding environments.
- Titanium Alloys (Ti6Al4V): A lightweight option with exceptional strength-to-weight ratio, biocompatible properties, and excellent corrosion resistance. Picture: aerospace components, biomedical implants, and sporting goods.
- Aluminum Alloys (AlSi10Mg): Offering a combination of good strength, ductility, and lightweight properties, making it suitable for applications requiring weight reduction and formability. Think: automotive components, heat exchangers, and prototypes.
- Inconel 625: A high-performance nickel-chromium superalloy known for its exceptional high-temperature strength, oxidation resistance, and resistance to harsh environments. Imagine: components for jet engines, nuclear reactors, and chemical processing equipment.
- Cobalt Chrome (CoCr): A biocompatible material with excellent wear resistance and corrosion resistance, widely used in the medical field for implants like joint replacements.
- Copper: Offering high thermal and electrical conductivity, making it suitable for heat sinks, electrical components, and applications requiring efficient heat dissipation.
- Tool Steel: Available in various grades for specific applications, offering high hardness, wear resistance, and hot work capabilities. Think: cutting tools, dies, and molds.
- Precious Metals (Gold, Silver, etc.): Used for creating jewelry, decorative items, and applications requiring high conductivity or specific optical properties.
- Emerging Options: The field of SLM metal powders is constantly evolving, with new materials like molybdenum, tantalum, and even metal-ceramic composites emerging for specialized applications.
Remember: This list is not exhaustive, and the choice of metal powder ultimately depends on your specific project requirements and desired properties.
Applications of Metal Powders in SLM
The applications of SLM metal powders are as diverse as the materials themselves. Here are some key areas where SLM is making waves:
Industry |
---|
Aerospace: Lightweight and high-strength components for aircraft, spacecraft, and satellites. |
Medical: Biocompatible implants, prosthetics, and surgical instruments. |
Automotive: Lightweight and high-performance components for engines, transmissions, and suspension systems. |
Consumer Goods: Jewelry, sporting goods, and customized design pieces. |
Diving Deeper: Specifications, Sizes, Grades, and Standards
Choosing the right metal powder for your SLM project requires delving into deeper details like specifications, sizes, grades, and standards. Here’s a breakdown to guide you:
Specifications:
- Particle size distribution: Typically measured in micrometers (µm) and expressed as a range (e.g., 15-45 µm). A narrower distribution ensures better layer formation and reduces porosity.
- Sphericity: Measured as a percentage, indicating how close the particles are to perfect spheres. Higher sphericity improves packing density and laser melting efficiency.
- Chemical composition: Defined by the specific elements and their percentages in the powder. This directly influences the final properties of the printed part.
Sizes:
Metal powders for SLM are generally available in a range of particle sizes, typically between 15 and 100 micrometers. The optimal size depends on the specific application and desired properties. For example, finer powders offer smoother surface finishes but may be more challenging to flow freely.
Grades:
Metal powders come in different grades, often denoted by numbers or letters. These grades signify the purity level, specific chemical composition, or additional treatments applied to the powder. For instance, a higher grade of stainless steel powder might have a lower carbon content, leading to improved corrosion resistance.
Standards:
Several international and national standards govern the quality and specifications of metal powders for SLM. These standards ensure consistency, safety, and performance reliability. Some prominent examples include:
- ASTM International (ASTM): Develops and publishes technical standards for various materials, including metal powders for additive manufacturing.
- EOS GmbH: A leading manufacturer of SLM machines also publishes material data sheets and application guidelines for specific metal powders they offer.
- German Institute for Standardization (DIN): A German national organization that publishes standards for various industries, including additive manufacturing.
Suppliers and Pricing
Finding the right supplier for your chosen metal powder is crucial. Here are some factors to consider:
- Reputation and experience: Choose a reputable supplier with experience in supplying high-quality metal powders for SLM.
- Material options: Look for a supplier offering a diverse range of metal powders to cater to your specific needs.
- Technical support: Ensure the supplier provides adequate technical support and guidance to answer your questions and assist with material selection.
- Pricing and lead times: Compare pricing and lead times across different suppliers to find the best fit for your budget and project timeline.
Pricing:
The cost of metal powder for SLM varies significantly depending on the chosen material, grade, and quantity. Generally, higher-performance materials like Inconel 625 and precious metals will be more expensive compared to standard stainless steel or aluminum powders. Additionally, the volume you purchase can also influence the price, with larger quantities typically commanding lower per-unit costs.
Here’s a table summarizing the typical price range for some common SLM metal powders (prices are indicative and may vary depending on supplier and market conditions):
Metal Powder | Price Range (USD/kg) |
---|---|
316L Stainless Steel | $50 – $100 |
17-4 PH Stainless Steel | $75 – $125 |
Ti6Al4V | $100 – $200 |
Aluminum Alloys (AlSi10Mg) | $30 – $50 |
Inconel 625 | $200 – $300 |
Remember: These prices are for informational purposes only and should not be considered definitive quotes. It’s crucial to contact potential suppliers directly for accurate and up-to-date pricing information.
Advantages and Limitations
Each metal powder for SLM comes with its own set of advantages and limitations. Understanding these trade-offs is essential for making informed decisions:
Advantages:
- Design freedom: SLM enables the creation of intricate and complex geometries, previously impossible with traditional manufacturing techniques.
- Lightweighting: Metal powders offer opportunities to create lightweight components, crucial for industries like aerospace and automotive.
- Material properties: A vast array of metal powders allows for tailoring the final part’s properties like strength, corrosion resistance, and biocompatibility.
- Reduced waste: SLM minimizes material waste compared to traditional subtractive manufacturing methods.
Limitations:
- Cost: SLM machines and metal powders can be expensive compared to traditional manufacturing methods.
- Build size limitations: Current SLM machines have limitations on the size of parts they can produce.
- Surface roughness: SLM-printed parts may require additional post-processing for achieving a smooth surface finish.
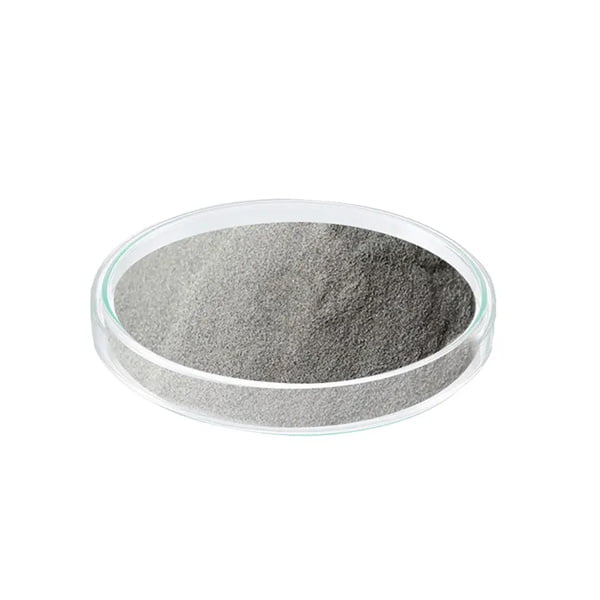
FAQs
Q: What are the safety considerations when handling metal powders?
A: Metal powders can pose a safety risk, including inhalation hazards and potential flammability. It’s crucial to follow proper safety protocols when handling metal powders, including wearing appropriate personal protective equipment (PPE) like gloves, respirators, and safety glasses. Additionally, proper ventilation and safe powder handling procedures are vital to minimize risks.
Q: How are metal powders stored?
A: Metal powders are often sensitive to moisture and oxygen exposure, which can affect their flowability and printability. Therefore, proper storage is crucial. Metal powders are typically stored in sealed containers under controlled temperature and humidity conditions.
Q: Can I recycle metal powder from failed prints?
A: In some cases, it might be possible to recycle metal powder from failed prints; however, this process requires specific equipment and expertise. Additionally, the recycled powder might not perform identically to virgin powder and may require additional processing before reuse. It’s recommended to consult the material supplier and your specific SLM equipment manufacturer for guidance on powder recycling.
Q: What are the future trends in metal powders for SLM?
A: The future of SLM metal powders is promising, with several exciting trends emerging:
- Development of new materials: Researchers are continuously exploring new materials and alloys suitable for SLM, pushing the boundaries of achievable properties and functionalities.
- Improved powder characteristics: Advancements in powder manufacturing technologies are leading to powders with better flowability, tighter particle size distribution, and improved sphericity, ultimately enhancing printing performance and part quality.
- Sustainability focus: There’s a growing focus on developing sustainable metal powders made from recycled materials or utilizing environmentally friendly production processes.
These trends indicate an ever-evolving landscape of metal powders for SLM, offering exciting possibilities for the future of additive manufacturing.
Share On
MET3DP Technology Co., LTD is a leading provider of additive manufacturing solutions headquartered in Qingdao, China. Our company specializes in 3D printing equipment and high-performance metal powders for industrial applications.
Inquiry to get best price and customized Solution for your business!
Related Articles
About Met3DP
Recent Update
Our Product
CONTACT US
Any questions? Send us message now! We’ll serve your request with a whole team after receiving your message.
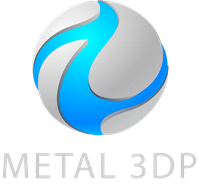
Metal Powders for 3D Printing and Additive Manufacturing
COMPANY
PRODUCT
cONTACT INFO
- Qingdao City, Shandong, China
- [email protected]
- [email protected]
- +86 19116340731