The application of SLM in the field of medical devices
Table of Contents
Imagine a world where intricate medical devices, perfectly tailored to individual patients, are manufactured on-demand. This isn’t science fiction; it’s the reality of Selective Laser Melting (SLM), a revolutionary 3D printing technology transforming the future of healthcare.
SLM, also known as Laser Powder Bed Fusion (LPBF), utilizes a high-powered laser to meticulously melt and fuse metal powders layer by layer, building complex three-dimensional structures. This innovative process unlocks a plethora of possibilities for fabricating intricate medical devices with unprecedented customization and functionality.
But what exactly makes SLM such a game-changer in the medical device landscape? Let’s delve deeper into this transformative technology, exploring its applications, the specific metal powders used, and the potential impact it holds for the future of patient care.
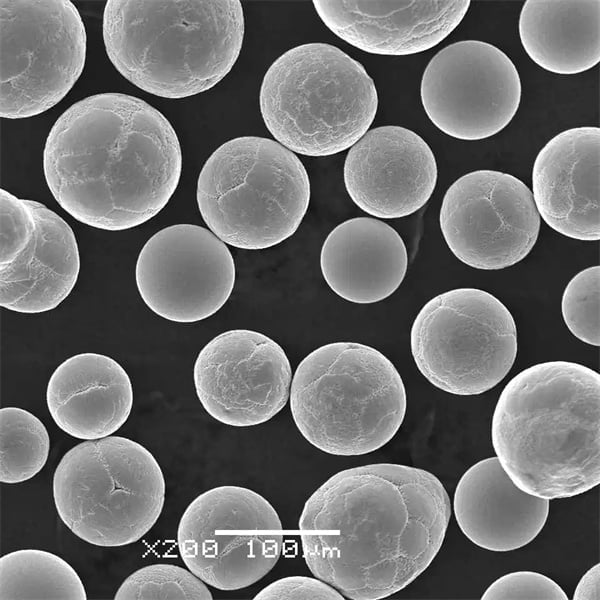
Applications of SLM in Medical Devices
SLM’s ability to create intricate, lightweight structures with biocompatible materials opens doors to a vast array of medical device applications. Here are some key areas where SLM is making significant strides:
SLM for Implants: A Perfect Fit
- Orthopedic Implants: Imagine a world where hip and knee replacements perfectly match a patient’s unique anatomy. SLM allows for the creation of customized implants with intricate lattice structures that promote bone ingrowth (osseointegration) and reduce stress shielding, a common complication with traditional implants. This translates to faster recovery times, improved implant longevity, and a significant reduction in revision surgeries.
- Cranio-Maxillofacial Implants: Following facial trauma or extensive surgery, SLM helps reconstruct complex facial features with remarkable precision. Customized craniofacial implants not only restore lost bone structure but also offer a natural aesthetic appearance, significantly improving a patient’s quality of life.
- Dental Implants: SLM revolutionizes dentistry by enabling the creation of personalized dental implants with superior strength and biocompatibility. These custom implants offer a more predictable and comfortable solution for patients seeking tooth replacements.
Beyond Implants: Expanding the Horizons
- Surgical Instruments: SLM facilitates the creation of complex surgical instruments with customized features and lightweight designs. Imagine a surgeon wielding instruments perfectly tailored to a specific procedure, enhancing their dexterity and surgical precision.
- Personalized Prosthetics: For individuals requiring prosthetics, SLM offers a path towards personalized solutions. By creating prosthetics that perfectly match a patient’s residual limb, SLM improves comfort, functionality, and overall patient satisfaction.
Metal Powders: The Building Blocks of Innovation
The success of SLM hinges on the specific metal powders used in the printing process. These powders, with their unique properties, determine the final device’s characteristics and performance. Here’s a closer look at some of the most commonly used metal powders in medical device applications:
Metal Powder | Composition | Properties | Characteristics | Applications |
---|---|---|---|---|
Titanium Alloy (Ti-6Al-4V) | 90% Titanium, 6% Aluminum, 4% Vanadium | Excellent biocompatibility, high strength-to-weight ratio, good corrosion resistance | Lightweight, strong, osseoconductive | Orthopedic implants (hip & knee replacements), dental implants, craniofacial implants |
Cobalt-Chromium Alloy (CoCrMo) | 60% Cobalt, 25% Chromium, 15% Molybdenum | High wear resistance, good biocompatibility, excellent mechanical properties | Strong, wear-resistant, corrosion-resistant | Hip and knee replacements, dental restorations, spinal implants |
Stainless Steel (316L) | 66% Iron, 16% Chromium, 10% Nickel, 2% Molybdenum | Affordable, good corrosion resistance, moderate strength | Cost-effective, biocompatible | Surgical instruments, medical devices requiring affordability and biocompatibility |
Tantalum | 100% Tantalum | Excellent biocompatibility, high radiopacity (visible on X-rays), good corrosion resistance | Biocompatible, radiopaque, corrosion-resistant | Craniofacial implants, dental implants, spinal implants |
Nickel-Titanium (NiTi) | 55% Nickel, 45% Titanium | Shape memory effect, superelasticity | Flexible, resilient | Orthopedic implants, stents, orthodontic wires |
Beyond this table, several other metal powders hold promise for medical applications, including:
- Magnesium Alloys: Biodegradable, promoting bone healing, ideal for temporary implants.
- Molybdenum Alloys: Excellent biocompatibility and corrosion resistance, suitable for long-term implants.
- Precious Metal Alloys: Offer superior corrosion resistance for specific applications.
Choosing the Right Metal Powder: A Balancing Act
The selection of the optimal metal powder for a specific medical device depends on a careful consideration of several factors:
- Biocompatibility: The material’s ability to coexist peacefully with the human body without causing adverse reactions is paramount.
- Mechanical Properties: The device’s intended use dictates its mechanical requirements. For instance, a hip replacement needs exceptional strength and fatigue resistance, while a surgical instrument might prioritize lightweight maneuverability.
- Corrosion Resistance: The material’s ability to withstand bodily fluids and prevent deterioration is crucial for long-term implant success.
- Osseointegration: For bone implants, the material’s ability to promote bone ingrowth is essential for a stable and functional implant.
- Cost: While cost shouldn’t be the sole deciding factor, it does play a role in device affordability and accessibility.
SLM allows engineers to explore a wider range of metal powders compared to traditional manufacturing methods. This opens doors to creating medical devices with a unique blend of properties, perfectly tailored to address specific patient needs and medical challenges.
Advantages and Limitations of SLM in Medical Devices
SLM, like any technology, boasts distinct advantages and limitations that need to be considered.
Advantages of SLM:
- Customization: The ability to create patient-specific devices with intricate geometries is a game-changer. This personalization can significantly improve implant fit, function, and long-term success.
- Complex Geometries: SLM overcomes limitations of traditional manufacturing by creating intricate lattice structures and internal features that enhance a device’s performance and biocompatibility.
- Lightweight Designs: SLM allows for the creation of lightweight devices with high strength-to-weight ratios, improving patient comfort and functionality, especially in prosthetics and surgical instruments.
- Reduced Waste: Compared to traditional subtractive manufacturing methods that generate significant scrap, SLM offers a more sustainable approach with minimal material waste.
Limitations of SLM:
- Cost: SLM machines and metal powders can be expensive, leading to higher upfront costs for device production. However, as the technology matures and adoption increases, costs are expected to decrease.
- Surface Roughness: SLM-produced parts can exhibit a slightly rougher surface finish compared to traditionally machined components. However, post-processing techniques can mitigate this roughness.
- Residual Stress: The SLM process can introduce residual stress within the printed part. Proper design optimization and heat treatment techniques help manage these stresses.
- Limited Material Selection: While the range of metal powders compatible with SLM is expanding, it’s still not as vast as those readily available for traditional manufacturing techniques.
The Future of SLM in Medical Devices
The future of SLM in medical devices is brimming with exciting possibilities. As research and development continue, we can expect advancements in:
- New Metal Powders: The development of novel metal powders with enhanced biocompatibility, mechanical properties, and printability will further expand the potential of SLM applications.
- Hybrid Manufacturing Techniques: Combining SLM with other manufacturing methods, such as machining or coating, could create devices with even more sophisticated functionalities.
- Reduced Costs: As SLM technology becomes more widespread and production scales up, the cost of SLM-produced devices is expected to decrease, making them more accessible to patients.
- Regulatory Landscape: Regulatory bodies are actively working on establishing clear guidelines for SLM-produced medical devices, fostering greater adoption and innovation.
SLM is not just a manufacturing technology; it’s a paradigm shift in how we design and create medical devices. By harnessing the power of SLM, we can move towards a future of personalized medicine, where medical devices are tailored to individual needs, leading to improved patient outcomes and a higher quality of life.
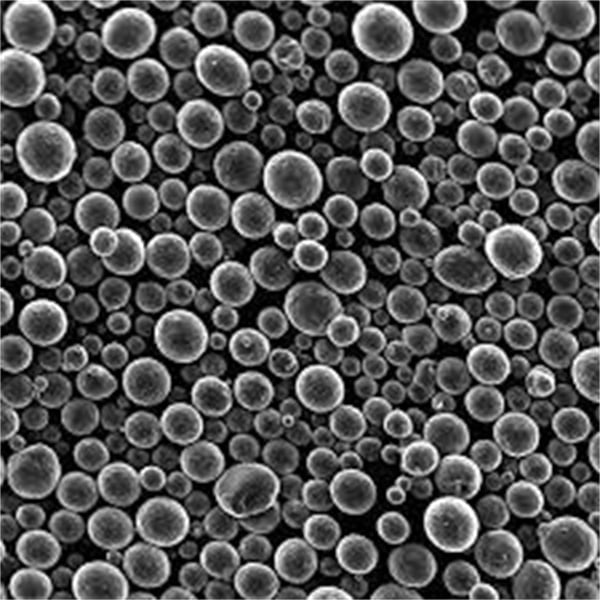
FAQ
Question | Answer |
---|---|
Is SLM SLM stronger than traditional manufacturing methods for medical devices? | The strength of a medical device depends on the chosen metal powder and its properties. However, SLM allows for the creation of complex internal structures that can enhance the overall strength-to-weight ratio of a device compared to traditional methods that rely on machining from solid blocks. |
Can SLM be used to create devices made of multiple materials? | Not currently. SLM is limited to using a single metal powder per printing process. However, researchers are exploring techniques for multi-material SLM or combining SLM with other manufacturing methods to create devices with features from different materials. |
How long does it take to create a medical device using SLM? | The printing time depends on the size and complexity of the device. Printing times can range from hours to days. However, additional post-processing steps like heat treatment and surface finishing can add to the overall production time. |
What are some of the biggest challenges hindering the widespread adoption of SLM in medical devices? | Cost is a major factor. Additionally, ensuring consistent quality control and developing a robust regulatory framework for SLM-produced devices are ongoing challenges. |
Is SLM an environmentally friendly technology? | Compared to traditional manufacturing methods that generate significant scrap metal, SLM offers a more sustainable approach with minimal material waste. However, the energy consumption during the SLM process needs to be considered for a complete environmental assessment. |
Conclusion
Selective Laser Melting (SLM) is revolutionizing the medical device landscape, ushering in an era of personalized medicine. With its ability to create intricate, biocompatible devices tailored to individual needs, SLM holds immense potential to improve patient outcomes and quality of life. While challenges remain, ongoing advancements in materials, technology, and regulations pave the way for a future where SLM becomes a mainstream manufacturing process for a wide range of groundbreaking medical devices.
Share On
MET3DP Technology Co., LTD is a leading provider of additive manufacturing solutions headquartered in Qingdao, China. Our company specializes in 3D printing equipment and high-performance metal powders for industrial applications.
Inquiry to get best price and customized Solution for your business!
Related Articles
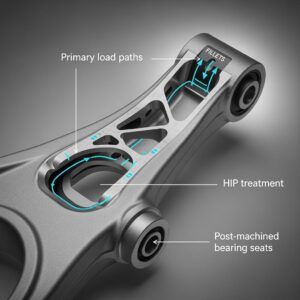
Metal 3D Printing for U.S. Automotive Lightweight Structural Brackets and Suspension Components
Read More »About Met3DP
Recent Update
Our Product
CONTACT US
Any questions? Send us message now! We’ll serve your request with a whole team after receiving your message.