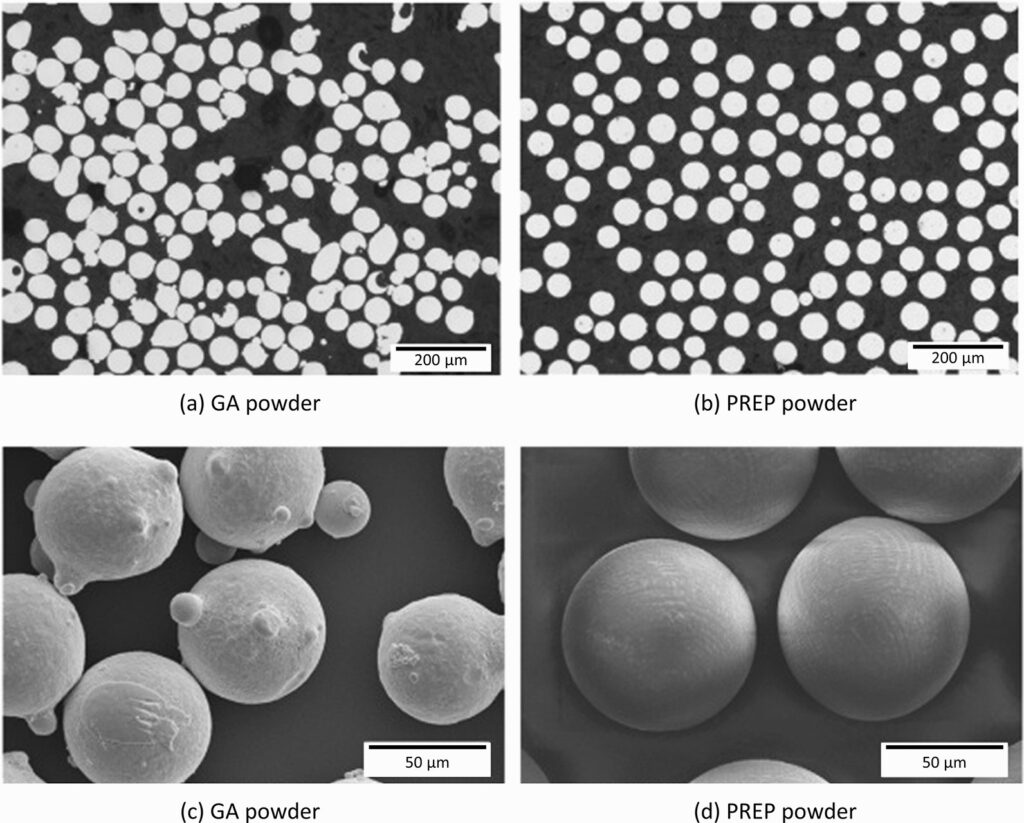
Spherical Al-Mg Alloy Powder: Lightweight Strength Like Never Before
Low MOQ
Provide low minimum order quantity to meet different needs.
OEM & ODM
Provide customized products and design services to meet unique customer needs.
Adequate Stock
Ensure fast order processing and provide reliable and efficient service.
Customer Satisfaction
Provide high quality products with customer satisfaction at the core.
share this article
Table of Contents
Overview of Spherical Al-Mg Alloy Powder
When it comes to modern materials with high performance and versatility, spherical Al-Mg alloy powder has emerged as a star player in industries that prioritize lightweight designs, strength, and corrosion resistance. Combining the best of aluminum (Al) and magnesium (Mg), this alloy powder is not just an engineering material—it’s a revolutionary solution for demanding applications like 3D printing, aerospace, automotive, and electronics.
Why is it so special? By processing aluminum and magnesium into a spherical powder form, manufacturers achieve a material with enhanced flowability, uniform size distribution, and optimized packing density, making it perfect for additive manufacturing, powder metallurgy, and even thermal spray coatings. These powders are engineered for precision, offering a combination of lightweight properties from magnesium and strength from aluminum, making them a go-to option for industries where performance and weight are critical.
In this article, we’ll take a deep dive into everything you need to know about spherical Al-Mg alloy powder—its composition, types, unique properties, applications, specifications, pricing, and more. Whether you’re a materials scientist or an industrial engineer, this guide will help you understand why this alloy powder is a game-changer for modern manufacturing.
Types, Composition, and Properties of Spherical Al-Mg Alloy Powder
The spherical Al-Mg alloy powder is a carefully engineered material. Its unique properties stem from the balance of its composition and the precision in its manufacturing process. Let’s explore the different types, composition, and why these powders behave the way they do.
Types of Spherical Al-Mg Alloy Powder
Type | Description |
---|---|
High-Purity Al-Mg Alloy Powder | Contains ≥99.5% pure aluminum and magnesium, designed for aerospace and medical applications. |
Standard Al-Mg Alloy Powder | Includes minor alloying elements like zinc or silicon to enhance strength and thermal resistance. |
Nano-Sized Al-Mg Alloy Powder | Ultra-fine powder (<100 nm) with enhanced surface area for advanced applications like fuel cells. |
Coated Al-Mg Alloy Powder | Powders coated with protective layers to reduce oxidation and improve storage stability. |
Composition of Spherical Al-Mg Alloy Powder
Element | Typical Proportion (%) | Role in the Alloy |
---|---|---|
Aluminum (Al) | 85-95% | Provides lightweight properties, strength, and thermal conductivity. |
Magnesium (Mg) | 5-15% | Enhances corrosion resistance, reduces density, and improves machinability. |
Zinc (Zn) | <2% | Increases toughness and wear resistance (optional in some alloys). |
Silicon (Si) | <1% | Improves castability and thermal stability in high-temperature environments. |
Properties of Spherical Al-Mg Alloy Powder
Property | Details |
---|---|
Density | ~2.4–2.7 g/cm³, significantly lighter than traditional metal powders. |
Melting Point | ~600-650°C, suitable for applications requiring moderate heat resistance. |
Corrosion Resistance | Excellent, especially in marine or high-humidity environments. |
Flowability | Outstanding due to the spherical shape, making it ideal for additive manufacturing. |
Strength-to-Weight Ratio | High, combining lightweight properties with excellent mechanical strength. |
Oxidation Sensitivity | Moderate; requires proper storage to prevent degradation over time. |
Thermal Conductivity | Good, enabling applications in heat-dissipating components like electronics casings. |
The balance of strength, lightweight properties, and corrosion resistance is what makes spherical Al-Mg alloy powder so effective in industries where performance and durability are critical.
Applications of Spherical Al-Mg Alloy Powder
Thanks to its exceptional properties, spherical Al-Mg alloy powder finds applications across a variety of industries. Here’s where this material is making waves:
Common Applications of Spherical Al-Mg Alloy Powder
Industry | Application |
---|---|
Aerospace | Lightweight structural components, fuel-efficient engine parts, heat shields, and satellite panels. |
Automotive | Engine components, lightweight chassis parts, and crash-resistant frames for fuel efficiency. |
Additive Manufacturing | High-precision 3D-printed parts for aerospace, medical, and consumer electronics. |
Biomedical | Biocompatible implants, surgical tools, and lightweight prosthetics. |
Electronics | Heat sinks, casings, and other thermal management components for consumer and industrial devices. |
Marine | Corrosion-resistant parts for boats, submarines, and offshore equipment. |
Defense | Lightweight armor, drones, and aerospace defense systems requiring high strength and durability. |
Example: Spherical Al-Mg Alloy Powder in Additive Manufacturing
In additive manufacturing (commonly known as 3D printing), the flowability and uniform particle distribution of spherical Al-Mg alloy powder ensure precise layering and bonding during the printing process. This results in stronger, lighter, and more intricate structures that are impossible to achieve with traditional manufacturing techniques. For example, aerospace engineers use Al-Mg powder to print complex turbine blades, reducing aircraft weight while maintaining structural integrity.
Specifications, Sizes, and Standards for Spherical Al-Mg Alloy Powder
To meet the demands of various industries, spherical Al-Mg alloy powder is manufactured with strict specifications. Below are the typical grades, sizes, and standards to look for when selecting this material.
Specifications and Sizes of Spherical Al-Mg Alloy Powder
Specification | Details |
---|---|
Particle Size | Available in ranges like 10-45 µm (fine) to 45-150 µm (coarse), suitable for different applications. |
Purity | ≥99.5%, ensuring minimal impurities for consistent performance. |
Shape | Spherical, critical for flowability and uniformity in powder-based processes. |
Density | ~2.4–2.7 g/cm³, optimized for lightweight applications. |
Coating Options | Polymers or oxides for enhanced oxidation resistance and storage stability. |
Compliance Standards | Meets industry standards such as ASTM B221 for aerospace and automotive applications. |
Suppliers and Pricing for Spherical Al-Mg Alloy Powder
Finding reliable suppliers is essential for ensuring quality and consistency in spherical Al-Mg alloy powder. Here’s an overview of leading suppliers and their pricing.
Leading Suppliers and Pricing Information
Supplier | Region | Price Range (per kg) | Specialization |
---|---|---|---|
Advanced Metal Powders | USA | $120 – $180 | High-purity Al-Mg powders for aerospace and medical applications. |
MetalTech Europe | Europe | $140 – $200 | Customizable alloys for additive manufacturing and powder metallurgy. |
Asia Alloys Co. | Asia | $100 – $150 | Bulk orders for industrial-scale applications. |
Global Alloy Solutions | Global | $130 – $190 | Supplies coated powders for improved oxidation resistance. |
Comparing Pros and Cons of Spherical Al-Mg Alloy Powder
While spherical Al-Mg alloy powder offers numerous benefits, it’s essential to weigh its advantages and limitations to determine its suitability for your application.
Advantages of Spherical Al-Mg Alloy Powder
Advantage | Description |
---|---|
Lightweight | Reduces weight in aerospace, automotive, and marine industries. |
Corrosion Resistance | Performs well in harsh environments, especially marine and humid conditions. |
High Flowability | Ensures precision and efficiency in additive manufacturing processes. |
Thermal Conductivity | Ideal for electronics and heat-dissipating components. |
Limitations of Spherical Al-Mg Alloy Powder
Limitation | Description |
---|---|
Cost | Higher than traditional materials due to advanced processing requirements. |
Oxidation Sensitivity | Requires proper storage to prevent degradation over time. |
Processing Challenges | Demands specialized equipment and expertise for effective application. |
Frequently Asked Questions (FAQ) About Spherical Al-Mg Alloy Powder
Question | Answer |
---|---|
What is spherical Al-Mg alloy powder used for? | It’s used in aerospace, automotive, biomedical, and additive manufacturing applications. |
How is it stored safely? | Store in airtight containers away from heat and moisture to prevent oxidation. |
Is it suitable for 3D printing? | Yes, its flowability and uniform size distribution make it ideal for additive manufacturing. |
What industries benefit most from it? | Aerospace, automotive, marine, electronics, and medical fields. |
How much does it cost? | Prices typically range from $100 to $200 per kilogram, depending on specifications. |
Conclusion
Spherical Al-Mg alloy powder is not just another material—it’s a high-performance solution for industries that demand lightweight strength, corrosion resistance, and precision. Whether you’re designing next-gen aerospace components, 3D printing intricate parts, or creating corrosion-resistant electronics, this material offers the perfect balance of versatility and performance. While it may come with higher costs, its advantages in advanced applications make it a worthwhile investment for those looking to stay ahead in the competitive world of modern engineering.
Get Latest Price
About Met3DP
Product Category
HOT SALE
CONTACT US
Any questions? Send us message now! We’ll serve your request with a whole team after receiving your message.
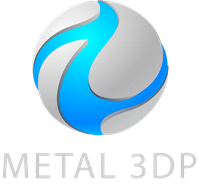
Metal Powders for 3D Printing and Additive Manufacturing