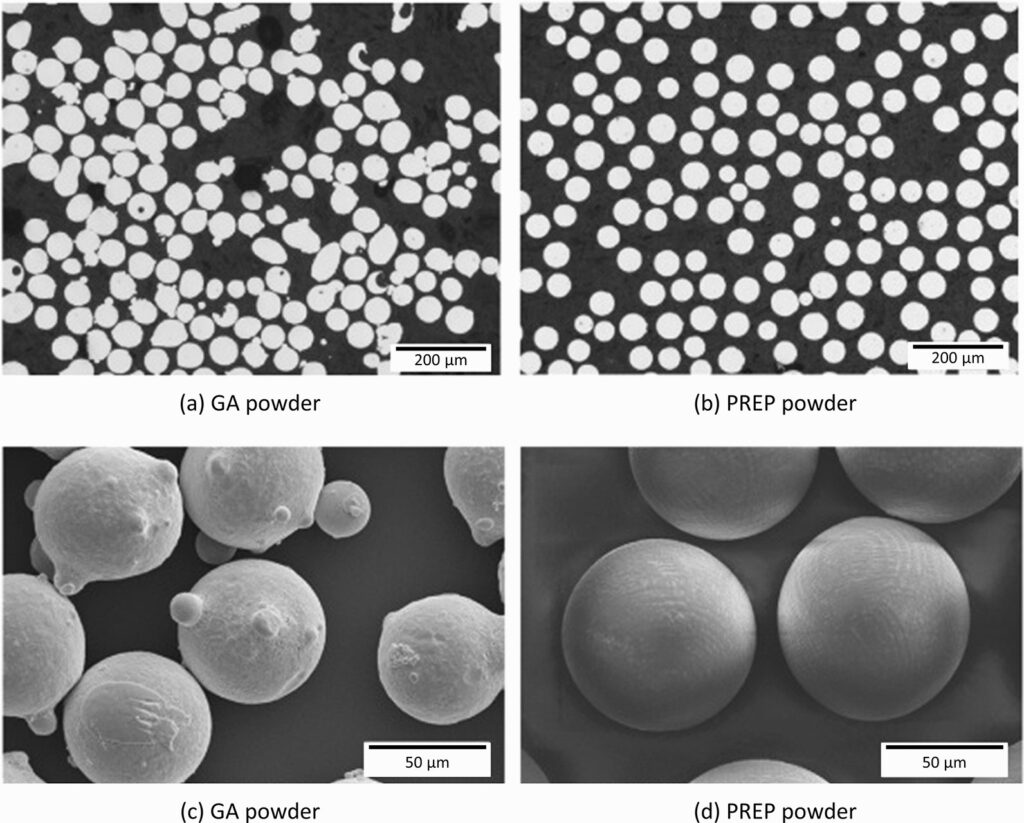
Spherical Casting Tungsten Carbide/Ni-Based Alloys: Top Choice for High-Performance Needs
Low MOQ
Provide low minimum order quantity to meet different needs.
OEM & ODM
Provide customized products and design services to meet unique customer needs.
Adequate Stock
Ensure fast order processing and provide reliable and efficient service.
Customer Satisfaction
Provide high quality products with customer satisfaction at the core.
share this article
Table of Contents
When it comes to materials that can endure extreme wear, high temperatures, and corrosive environments, spherical casting tungsten carbide combined with Ni-based alloys sits comfortably at the top. These materials are engineered for the toughest applications, offering unmatched durability and performance in industries ranging from aerospace to mining and oil & gas.
In this detailed guide, we’ll explore every aspect of spherical casting tungsten carbide/Ni-based alloys to help you understand their properties, applications, specifications, and more. Whether you’re an engineer, a procurement officer, or just someone curious about advanced materials, this article will cover everything you need to know.
Overview: What Is Spherical Casting Tungsten Carbide/Ni-Based Alloy?
Spherical Casting Tungsten Carbide
Tungsten carbide (WC) is a compound of tungsten and carbon, known for its exceptional hardness and wear resistance. When formed into spherical particles, tungsten carbide offers additional advantages, such as improved flowability and packing density, which are highly beneficial in applications like thermal spraying, powder metallurgy, and additive manufacturing.
- Key Characteristics: Extreme hardness, excellent wear and abrasion resistance, high melting point (approximately 2,780°C), and good thermal conductivity.
- Typical Applications: Cutting tools, wear-resistant coatings, and mining equipment.
Ni-Based Alloy (Nickel-Based Alloy)
Nickel-based alloys are a group of materials primarily composed of nickel, but they also contain other elements like chromium, molybdenum, and iron. These alloys are renowned for their high-temperature strength, oxidation resistance, and excellent corrosion resistance, particularly in harsh environments like chemical processing or aerospace applications.
- Key Characteristics: High corrosion resistance, excellent mechanical properties at elevated temperatures, and superior oxidation resistance.
- Typical Applications: Aerospace turbines, chemical reactors, and marine components.
By combining spherical tungsten carbide with a nickel-based alloy matrix, we get a composite material that is not only extremely tough but also highly resistant to wear, corrosion, and high temperatures.
Types, Composition, and Properties of Spherical Casting Tungsten Carbide/Ni-Based Alloys
Understanding the various types and compositions of spherical casting tungsten carbide/Ni-based alloys is essential for choosing the right material for your specific application. Depending on the specific binder material (often cobalt or nickel) and the grain size of the tungsten carbide, the properties of the alloy can vary significantly.
Types and Composition of Spherical Casting Tungsten Carbide/Ni-Based Alloys
Material | Composition | Key Properties | Common Uses |
---|---|---|---|
WC-Co (Tungsten Carbide + Cobalt) | Tungsten carbide (WC), Cobalt (Co) binder | Extremely hard, excellent wear resistance | Cutting tools, mining equipment, wear parts |
WC-Ni (Tungsten Carbide + Nickel) | Tungsten carbide (WC), Nickel (Ni) binder | High hardness, good corrosion resistance | Chemical processing, marine applications |
Ni-Based Alloy (Inconel®) | Nickel (Ni), Chromium (Cr), Iron (Fe), Molybdenum (Mo) | High-temperature strength, oxidation resistance | Aerospace, power generation |
WC-NiCrBSi (Tungsten Carbide + NiCrBSi) | Tungsten carbide (WC), Nickel-Chromium-Boron-Silicon (NiCrBSi) alloy binder | Excellent corrosion resistance, wear resistance | Wear-resistant coatings, thermal spraying |
Tungsten Heavy Alloys (WHAs) | Tungsten (W), Nickel (Ni), Iron (Fe) | High density, good ductility, high strength | Radiation shielding, aerospace counterweights |
Key Properties of Spherical Casting Tungsten Carbide/Ni-Based Alloys
Property | Tungsten Carbide | Ni-Based Alloys |
---|---|---|
Density | 15.6 g/cm³ | 8.4 g/cm³ |
Hardness | 70-90 HRC | 35-45 HRC |
Melting Point | 2,780°C (5,036°F) | 1,200°C – 1,400°C (2,192°F – 2,552°F) |
Thermal Conductivity | 110 W/m·K | 15-22 W/m·K |
Corrosion Resistance | Moderate | Excellent |
Wear Resistance | Superior | Good |
Oxidation Resistance | Limited | Exceptional |
Spherical tungsten carbide combined with Ni-based alloys offers a balance of extreme hardness and corrosion resistance, making it an ideal choice for high-performance applications in industries like oil & gas, aerospace, and mining.
Applications of Spherical Casting Tungsten Carbide/Ni-Based Alloys
The combination of tungsten carbide and Ni-based alloys creates a versatile material that can withstand extreme conditions, making it suitable for a wide range of industries. Here are some of the most common applications where spherical casting tungsten carbide/Ni-based alloys excel.
Common Applications of Spherical Casting Tungsten Carbide/Ni-Based Alloys
Industry | Application | Benefits |
---|---|---|
Aerospace | Turbine blades, exhaust systems, landing gear | High-temperature strength, oxidation resistance |
Oil & Gas | Drilling tools, valve components, wellhead equipment | Extreme wear resistance, corrosion resistance |
Mining | Excavation tools, crushers, grinding media | Superior hardness, high wear resistance |
Chemical Processing | Pumps, valves, heat exchangers | Excellent corrosion resistance in harsh chemical environments |
Thermal Spraying | Wear-resistant coatings for machinery parts | Improves service life, high corrosion and wear resistance |
Marine | Propellers, shaft sleeves, pumps | Excellent seawater corrosion resistance |
Power Generation | Gas turbine blades, heat exchangers | High-temperature and oxidation resistance |
Example Use Case: Oil and Gas Drilling
In the oil and gas industry, spherical casting tungsten carbide/Ni-based alloys are used extensively in drilling tools like drill bits, cutters, and valves. These components face extreme abrasive wear from drilling in rock formations, as well as exposure to corrosive fluids. The tungsten carbide provides superior hardness, while the Ni-based alloy matrix offers corrosion resistance, making this composite material the ideal choice for such harsh environments.
Specifications, Sizes, Grades, and Standards for Spherical Casting Tungsten Carbide/Ni-Based Alloys
When selecting spherical casting tungsten carbide/Ni-based alloys, it’s important to understand the available specifications, sizes, grades, and standards. These factors will determine the material’s performance, durability, and suitability for your specific application.
Specifications for Spherical Casting Tungsten Carbide/Ni-Based Alloys
Specification | Details |
---|---|
Grade | WC-Co, WC-Ni, WC-NiCrBSi, Inconel®, Hastelloy® |
Particle Size | Typically ranges from 10µm to 150µm (microns), depending on application |
Hardness | Varies by grade; typically 70-90 HRC for tungsten carbide, 35-45 HRC for Ni-alloys |
Density | 15.6 g/cm³ for tungsten carbide composites |
Melting Point | Tungsten carbide: 2,780°C; Ni-based alloys: 1,200°C – 1,400°C |
Forms | Available in powders, castings, rods, and custom shapes |
Standards | ASTM B777 (Tungsten Heavy Alloys), ASTM B333 (Nickel-based alloys) |
Key Standards for Spherical Casting Tungsten Carbide/Ni-Based Alloys
- ASTM B777: Standard specification for tungsten heavy alloys, covering properties like density and strength.
- ASTM B333: Standard specification for nickel-based alloys used in high-temperature and corrosion-resistant applications.
These standards ensure that the materials meet the rigorous requirements for high-performance applications in critical industries like aerospace and oil & gas.
Suppliers and Pricing of Spherical Casting Tungsten Carbide/Ni-Based Alloys
Pricing for spherical casting tungsten carbide and Ni-based alloys can vary depending on the supplier, composition, and form of the material. Generally, these materials are more expensive than standard metals due to their high-performance characteristics, but the long-term benefits in durability and reduced maintenance often outweigh the initial cost.
Suppliers and Pricing for Spherical Casting Tungsten Carbide/Ni-Based Alloys
Supplier | Location | Materials Offered | Price per Kg (Approx.) |
---|---|---|---|
Kennametal Inc. | USA | Spherical tungsten carbide, nickel-based alloys | $250 – $700 |
Höganäs AB | Sweden | Nickel-based powders, tungsten carbide powders | $200 – $650 |
ATI Metals | USA | Inconel®, Hastelloy®, tungsten carbide composites | $220 – $680 |
Oerlikon Metco | Switzerland | Spherical tungsten carbide, thermal spray powders | $180 – $620 |
Sandvik AB | Sweden | Tungsten carbide, nickel-based powders | $240 – $690 |
The price range for spherical tungsten carbide and Ni-based alloys reflects their high-performance nature. While the upfront costs might seem high, these materials can provide significant cost savings over time by reducing part failures, downtime, and maintenance.
Pros and Cons of Spherical Casting Tungsten Carbide/Ni-Based Alloys
Like any material, spherical casting tungsten carbide/Ni-based alloys come with their own set of advantages and limitations. Understanding these pros and cons can help you decide if they are the right choice for your specific application.
Advantages and Limitations of Spherical Casting Tungsten Carbide/Ni-Based Alloys
Advantages | Limitations |
---|---|
Exceptional Wear Resistance: Tungsten carbide’s hardness makes it ideal for wear-intensive applications | Cost: These alloys are more expensive than standard steel or aluminum |
Corrosion Resistance: Ni-based alloys provide excellent protection in corrosive environments | Weight: Tungsten carbide is dense, which can be a disadvantage in applications where weight is a concern |
High-Temperature Stability: Both materials maintain their mechanical properties at elevated temperatures | Brittleness: Tungsten carbide can be brittle, limiting its use in high-impact applications |
Extended Lifespan: Reduced downtime and maintenance due to material longevity | Complex Manufacturing: The creation of these materials requires sophisticated processes and equipment |
For example, while tungsten carbide offers unrivaled hardness, it can be brittle in high-impact environments. On the other hand, Ni-based alloys provide superior corrosion resistance, making them ideal for marine or chemical processing. However, the higher cost of these materials may not be justified in applications where wear or corrosion is not a significant concern.
Spherical Casting Tungsten Carbide/Ni-Based Alloys Compared to Other Materials
When choosing materials for high-performance applications, it’s important to compare spherical casting tungsten carbide/Ni-based alloys to other materials such as stainless steel, titanium, and chromium carbide. Each material has its strengths and weaknesses, and understanding how they stack up will help you make the best choice.
Comparison of Spherical Casting Tungsten Carbide/Ni-Based Alloys with Other Materials
Material | Properties | Cost Comparison | Applications |
---|---|---|---|
Spherical Tungsten Carbide | Extremely hard, brittle, high wear resistance | High cost | Cutting tools, coatings, wear parts |
Ni-Based Alloys | High corrosion resistance, good high-temperature strength | High cost | Aerospace, chemical processing |
Stainless Steel | Good corrosion resistance, moderate strength | Lower cost | General manufacturing, medical devices |
Titanium | High strength-to-weight ratio, excellent corrosion resistance | Higher cost | Aerospace, marine, medical implants |
Chromium Carbide | Good wear resistance, lower hardness than tungsten carbide | Lower cost | Wear-resistant coatings, industrial applications |
Compared to materials like stainless steel or titanium, both spherical tungsten carbide and Ni-based alloys provide superior wear resistance, corrosion resistance, and temperature stability. However, they are generally more expensive, making them ideal for high-performance applications where longevity and durability are critical.
Frequently Asked Questions (FAQ) About Spherical Casting Tungsten Carbide/Ni-Based Alloys
Common Questions About Spherical Casting Tungsten Carbide/Ni-Based Alloys
Question | Answer |
---|---|
What is spherical casting tungsten carbide used for? | Spherical casting tungsten carbide is used for high-wear applications such as cutting tools, thermal spraying, and wear-resistant coatings. |
What industries use Ni-based alloys? | Ni-based alloys are commonly used in aerospace, chemical processing, marine, and power generation industries due to their high corrosion resistance and high-temperature strength. |
What is the cost of spherical casting tungsten carbide? | The cost typically ranges from $250 to $700 per kilogram, depending on the supplier and specific composition. |
How does tungsten carbide compare to stainless steel? | Tungsten carbide is much harder and more wear-resistant than stainless steel, but it is also more brittle and expensive. Stainless steel, on the other hand, offers good corrosion resistance and is more affordable. |
What are the main benefits of Ni-based alloys? | Ni-based alloys offer excellent corrosion resistance, high-temperature strength, and oxidation resistance, making them ideal for harsh environments. |
How are spherical casting tungsten carbide and Ni-based alloys made? | These materials are typically manufactured using processes like powder metallurgy, thermal spraying, and advanced casting techniques. |
Conclusion
In conclusion, spherical casting tungsten carbide/Ni-based alloys represent some of the most advanced materials available for high-performance applications. Whether you’re working in aerospace, oil & gas, mining, or chemical processing, these materials offer unmatched durability, wear resistance, and corrosion resistance.
The combination of tungsten carbide and Ni-based alloys results in a material that can withstand the toughest conditions, from high temperatures to corrosive environments. While these materials may come with a higher upfront cost, their long-term durability and reduced maintenance requirements often make them a cost-effective solution for critical applications.
By understanding the types, properties, and applications of spherical casting tungsten carbide/Ni-based alloys, as well as comparing them to other materials, you can make informed decisions that will enhance the performance and longevity of your components. So, if you’re in need of a material that can handle extreme conditions without breaking a sweat, these alloys should be at the top of your list!
Get Latest Price
About Met3DP
Product Category
HOT SALE
CONTACT US
Any questions? Send us message now! We’ll serve your request with a whole team after receiving your message.
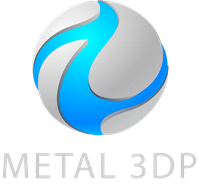
Metal Powders for 3D Printing and Additive Manufacturing