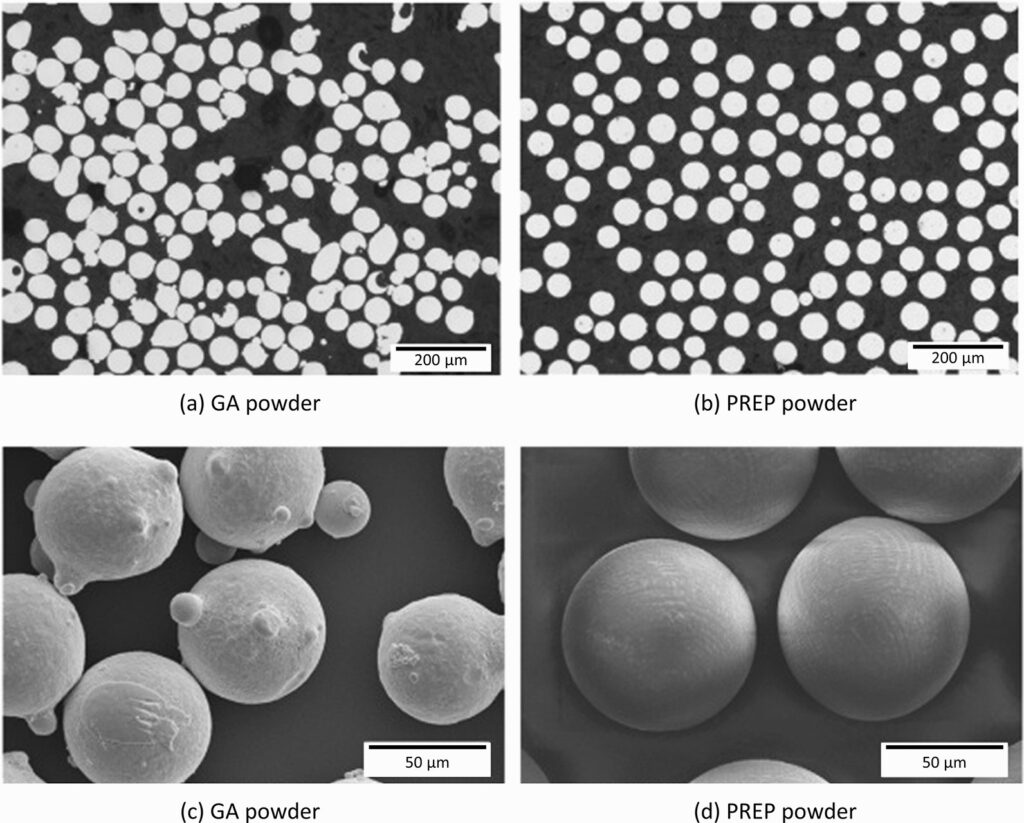
Spherical Casting Tungsten Carbide: Why It’s the Strongest Material for You
Low MOQ
Provide low minimum order quantity to meet different needs.
OEM & ODM
Provide customized products and design services to meet unique customer needs.
Adequate Stock
Ensure fast order processing and provide reliable and efficient service.
Customer Satisfaction
Provide high quality products with customer satisfaction at the core.
share this article
Table of Contents
Tungsten carbide is a name that practically screams durability and strength. But when you take it to the next level with spherical casting tungsten carbide, you’ve got a material that’s not just strong—it’s practically unstoppable. Whether you’re in mining, oil and gas, or the aerospace industry, there’s a good chance you’ve encountered spherical casting tungsten carbide in some form. And if you haven’t, it’s time to get acquainted.
This guide dives deep into all things spherical casting tungsten carbide. What is it exactly? Why is it so special compared to other forms of tungsten carbide? Most importantly, how can it benefit your specific industrial applications? We’ll leave no stone unturned as we break down everything from its properties and composition to its applications, suppliers, and pricing.
So, if you’re curious about how spherical casting tungsten carbide can revolutionize your operations, settle in. This is going to be a comprehensive yet conversational ride through one of the toughest materials on the planet.
Overview of Spherical Casting Tungsten Carbide
In the world of wear-resistant materials, spherical casting tungsten carbide stands out due to its unique shape and properties. Unlike traditional tungsten carbide, which is often irregularly shaped, spherical casting tungsten carbide consists of spherically shaped particles. This shape gives it an edge in certain applications, especially those involving abrasive wear and surface treatments like coatings and hardfacing.
Why does the shape matter? Well, think about it: When particles are spherical, they distribute stress more evenly and reduce the likelihood of weak points. It’s like comparing a jagged rock to a smooth pebble—the smooth pebble is much less likely to crack under pressure. This makes spherical casting tungsten carbide particularly useful in applications where uniform wear resistance is crucial, such as thermal spray coatings and metal matrix composites.
Key Features of Spherical Casting Tungsten Carbide
- Enhanced Uniformity: The spherical shape ensures consistent wear resistance across surfaces.
- High Hardness: Offers hardness levels similar to traditional tungsten carbide, making it highly resistant to wear and abrasion.
- Improved Flowability: The spherical particles flow more easily, making them ideal for coating applications.
- Superior Packing Density: Due to its shape, spherical tungsten carbide can pack more densely, providing better protection in coatings and composite materials.
Composition and Properties of Spherical Casting Tungsten Carbide
Spherical casting tungsten carbide is produced using a high-temperature melting process, followed by rapid solidification, which allows the material to form into spherical particles. This process is what gives it its unique properties, setting it apart from other forms of tungsten carbide.
Let’s break down the composition and remarkable characteristics that make spherical casting tungsten carbide such a powerhouse material.
Characteristic | Description |
---|---|
Composition | Typically consists of 94-96% tungsten and 4-6% carbon, similar to other forms of tungsten carbide. |
Hardness (Vickers) | Hardness ranges from 2,500 to 3,500 HV, comparable to traditional tungsten carbide, making it highly wear-resistant. |
Density | Spherical tungsten carbide has a density of around 15.4 g/cm³, making it a highly compact and durable material. |
Melting Point | Withstands temperatures up to 2,870°C (5,198°F), making it ideal for high-temperature applications. |
Thermal Conductivity | Offers good thermal conductivity, which helps in dissipating heat during high-friction operations. |
Corrosion Resistance | Spherical tungsten carbide has moderate corrosion resistance, but it can be enhanced with coatings if necessary. |
Sphericity | The high degree of sphericity improves the material’s flowability and packing density, particularly useful in coatings. |
These properties make spherical casting tungsten carbide invaluable in industries that require not only extreme hardness but also superior flowability and uniform wear resistance.
Types of Spherical Casting Tungsten Carbide
There are several variations of spherical casting tungsten carbide, each optimized for specific applications. The differences often come down to grain size, bonding agents, or additional materials that enhance specific properties like toughness or corrosion resistance.
Type | Description |
---|---|
Macro-Grain Spherical Tungsten Carbide | Larger grain sizes (50-150 µm) provide higher toughness, ideal for applications needing impact resistance like drilling or mining tools. |
Micro-Grain Spherical Tungsten Carbide | Tiny grains (<1 µm) offer superior hardness, making it perfect for cutting tools and precision instruments where wear resistance is critical. |
Cobalt-Bonded Spherical Tungsten Carbide | Cobalt is added as a binder to increase toughness and reduce brittleness, especially in high-impact applications. |
Nickel-Bonded Spherical Tungsten Carbide | Nickel as the binder improves corrosion resistance, making it a better choice for chemically aggressive environments. |
Spherical Tungsten Carbide with Coatings | Often coated with other materials like chromium or cobalt to enhance specific properties such as corrosion resistance or toughness. |
Each type of spherical casting tungsten carbide brings something different to the table, allowing you to select the best option for your specific application needs.
Applications of Spherical Casting Tungsten Carbide
Because of its unique properties, spherical casting tungsten carbide is used in a wide array of applications across industries. Its superior wear resistance, combined with its spherical shape, makes it particularly effective in coating technologies and abrasive environments.
Industry | Applications |
---|---|
Mining and Drilling | Used in drill bits, wear-resistant parts, and cutting tools that are exposed to extreme abrasion and impact. |
Aerospace | Applied in thermal spray coatings for components that operate in high-temperature environments like turbine blades and engine parts. |
Oil and Gas | Utilized in downhole tools and valve coatings to protect against wear and corrosion in harsh drilling environments. |
Manufacturing | Commonly used in metal matrix composites (MMCs) and hardfacing applications to extend the life of industrial machinery and tools. |
Automotive | Employed in engine components and brake systems that require high wear resistance and durability under friction. |
Surface Coating Technologies | Essential for plasma spray, HVOF (High-Velocity Oxy Fuel), and other coating techniques that demand high flowability and even distribution. |
Defense and Military | Found in armor-piercing ammunition and other military-grade components where extreme hardness and toughness are necessary. |
The consistent performance of spherical casting tungsten carbide across such a wide range of industries clearly demonstrates its versatility and resilience.
Specifications, Sizes, Grades, and Standards for Spherical Casting Tungsten Carbide
Understanding the various specifications and industry standards for spherical casting tungsten carbide is essential when selecting the right product for your needs. Different industries may require specific sizes, grades, or standards to ensure optimal performance.
Specification | Description |
---|---|
Grain Size | Available in sizes ranging from <1 µm (micro-grain) to 150 µm (macro-grain), depending on the required balance between hardness and toughness. |
Purity Level | Typically contains 94-96% tungsten, with the remaining percentage being carbon and trace elements, ensuring high hardness and wear resistance. |
Bonding Materials | Common bonding agents include cobalt and nickel, which enhance toughness and corrosion resistance, respectively. |
Industrial Standards | Adheres to standards such as ISO 9001 for quality management and ISO 513 for cutting tools, ensuring consistent quality across different applications. |
Hardness (HV) | The hardness of spherical casting tungsten carbide ranges from 2,500 to 3,500 HV, depending on the grain size and bonding materials. |
Sphericity | High sphericity ensures better flowability and packing density, which is crucial for coating and composite material applications. |
ASTM Standards | Meets ASTM B777 standards for tungsten products and ASTM F288 for aerospace applications, ensuring it meets performance and safety regulations. |
These specifications ensure that spherical casting tungsten carbide is tailored to meet the demanding requirements of your application, whether you’re coating a turbine blade or reinforcing a mining tool.
Suppliers and Pricing of Spherical Casting Tungsten Carbide
When sourcing spherical casting tungsten carbide, it’s important to consider not just the price but also the reputation of the suppliers, the purity of the material, and the consistency of particle size. Pricing can vary significantly depending on these factors, as well as the volume of the order.
Supplier | Country | Price Per Kg (USD) | Purity Levels Available | Special Features |
---|---|---|---|---|
Global Tungsten & Powders Corp. | United States | $900 – $1,400 | 94-96% Tungsten | A leading supplier for aerospace and oil industries, offering consistent high-purity spherical tungsten carbide. |
H.C. Starck Tungsten | Germany | $950 – $1,500 | 95-96% Tungsten | Known for supplying high-grade tungsten carbide powders for thermal spray coatings and industrial wear parts. |
Buffalo Tungsten | United States | $850 – $1,200 | 94-95% Tungsten | Competitive pricing for bulk orders, with a focus on mining and drilling industries. |
Zhuzhou Cemented Carbide Group | China | $700 – $1,100 | 94-96% Tungsten | One of the largest suppliers of tungsten carbide, specializing in mining, drilling, and wear-resistant components. |
ALMT Corp | Japan | $1,000 – $1,500 | 95-96% Tungsten | Renowned for high-precision spherical tungsten carbide used in aerospace and high-temperature applications. |
Pricing for spherical casting tungsten carbide is influenced by factors such as grain size, purity, and bonding materials. Higher purity levels and finer grains typically command higher prices, but the enhanced performance and longevity often justify the investment.
Advantages and Limitations of Spherical Casting Tungsten Carbide
While spherical casting tungsten carbide offers a host of benefits, it’s not without its limitations. Let’s break down the pros and cons to help you decide if it’s the right material for your application.
Advantages | Limitations |
---|---|
Superior Wear Resistance: Its hardness makes it ideal for high-wear environments, significantly extending the life of tools and components. | High Cost: Spherical casting tungsten carbide can be expensive, especially for high-purity and micro-grain varieties. |
Even Stress Distribution: The spherical shape reduces weak points and ensures more uniform wear across surfaces. | Brittleness: Despite its toughness, it can still be brittle under extreme impact, especially if not properly bonded or treated. |
Improved Flowability: Spherical particles flow more easily, making them ideal for coating applications like plasma spray. | Difficult to Machine: Due to its hardness, machining spherical tungsten carbide requires specialized tools and expertise. |
High-Temperature Stability: Performs well in high-heat environments, maintaining its properties even at elevated temperatures. | Limited Ductility: Like all tungsten carbide forms, it lacks flexibility, making it unsuitable for applications requiring deformation. |
While the advantages of spherical casting tungsten carbide often outweigh the limitations, it’s essential to weigh these factors depending on your specific use case.
Frequently Asked Questions (FAQ) About Spherical Casting Tungsten Carbide
Let’s address some of the most common questions people have about spherical casting tungsten carbide.
Question | Answer |
---|---|
What is spherical casting tungsten carbide? | It’s a form of tungsten carbide produced in spherical particles, known for its high wear resistance and flowability, especially in coating applications. |
How is it different from regular tungsten carbide? | The spherical shape offers better flowability and more uniform wear resistance, making it ideal for coatings and composites. |
What industries use spherical tungsten carbide? | Commonly used in mining, oil and gas, aerospace, and manufacturing industries for high-wear and high-impact applications. |
How much does spherical tungsten carbide cost? | Prices range from $700 to $1,500 per kilogram, depending on the supplier, grain size, and purity level. |
What are the benefits of spherical particles? | The spherical shape ensures better packing density, improved flowability, and more even stress distribution in wear-resistant applications. |
Can spherical tungsten carbide be machined? | Yes, but it requires specialized machining tools due to its extreme hardness, making conventional machining difficult. |
Conclusion
Spherical casting tungsten carbide is a powerhouse material that combines the extreme hardness and wear resistance of tungsten carbide with the added benefits of a spherical shape. Whether you’re using it for thermal spray coatings in the aerospace industry, hardfacing for mining tools, or composite materials in manufacturing, its ability to deliver consistent, long-lasting performance is unmatched.
Sure, the upfront cost may be higher than other materials, but the extended lifespan, better flowability, and uniform wear resistance make it a smart investment in the long run. Whether you’re dealing with high temperatures, abrasive environments, or high-impact applications, spherical casting tungsten carbide is a material that will not let you down.
So, is spherical casting tungsten carbide the right choice for your next project? If you need a material that’s tough, durable, and performs under pressure—literally—it just might be.
Get Latest Price
About Met3DP
Product Category
HOT SALE
CONTACT US
Any questions? Send us message now! We’ll serve your request with a whole team after receiving your message.
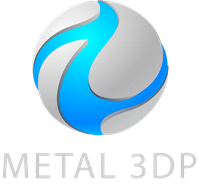
Metal Powders for 3D Printing and Additive Manufacturing