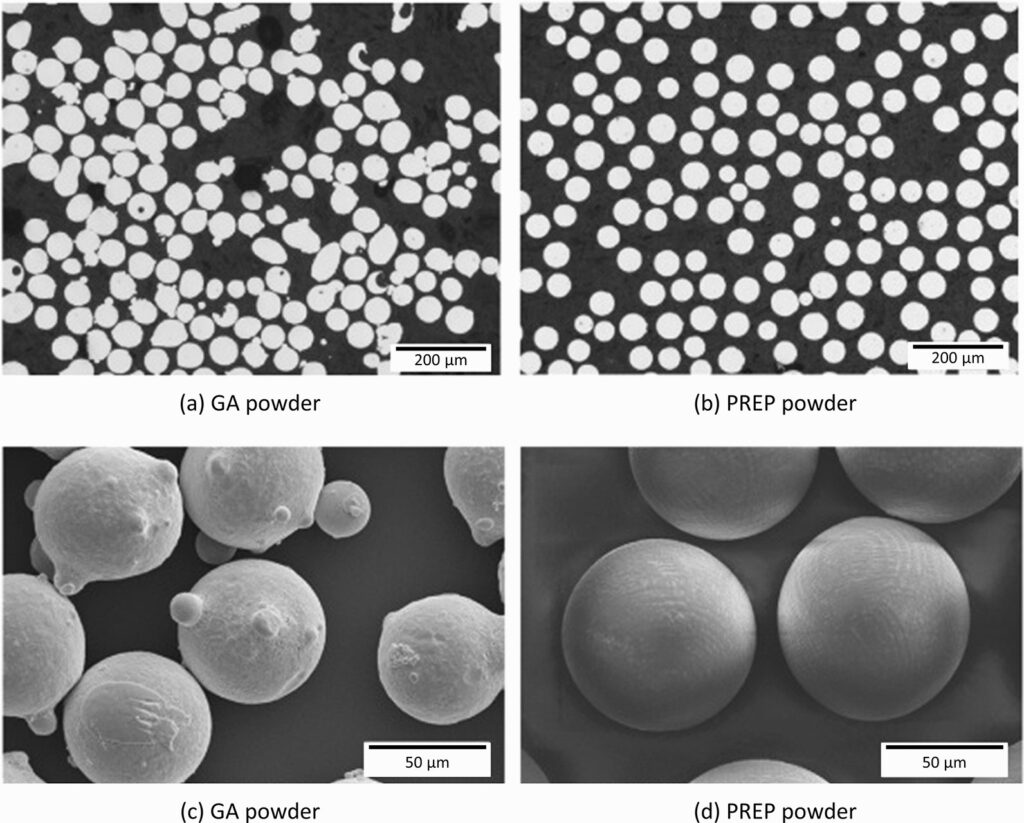
Why Spherical Cobalt-Based Alloy Brazing Powder is the Best for Tough Environments
Low MOQ
Provide low minimum order quantity to meet different needs.
OEM & ODM
Provide customized products and design services to meet unique customer needs.
Adequate Stock
Ensure fast order processing and provide reliable and efficient service.
Customer Satisfaction
Provide high quality products with customer satisfaction at the core.
share this article
Table of Contents
Overview of Spherical Cobalt-Based Alloy Brazing Powder
When it comes to brazing in high-performance applications, spherical cobalt-based alloy brazing powder stands out as a game-changer. Renowned for its high-temperature strength, excellent corrosion resistance, and wear performance, this material is vital for industries like aerospace, power generation, and medical equipment. Its unique properties allow it to bond metals effectively, even in extreme environments where other materials might fail.
But what makes this powder so special? It’s all in the details: the spherical particle shape ensures optimal flowability and uniform application, while cobalt’s natural properties provide strength and durability. Whether you’re working on turbine components, heat exchangers, or cutting tools, spherical cobalt-based alloy brazing powder ensures precision and reliability.
In this comprehensive guide, we’ll dive into the composition, properties, applications, specifications, suppliers, and pricing of spherical cobalt-based alloy brazing powder. Along the way, we’ll compare its advantages and limitations, answer common questions, and give you all the insights you need to make informed decisions. Let’s get started!
Composition and Characteristics of Spherical Cobalt-Based Alloy Brazing Powder
What Is It Made Of?
Cobalt-based brazing powders are carefully formulated to combine cobalt with other alloying elements like chromium, nickel, tungsten, and carbon. Each of these elements contributes to the material’s exceptional performance in high-temperature and corrosive environments.
Element | Typical Composition (%) | Role/Function |
---|---|---|
Cobalt (Co) | 40–70 | Core element, provides strength, heat resistance, and wear performance. |
Chromium (Cr) | 10–30 | Improves corrosion resistance and oxidation protection. |
Nickel (Ni) | 0–20 | Enhances ductility and strength in high-temperature environments. |
Tungsten (W) | 0–15 | Increases hardness and resistance to wear. |
Carbon (C) | 0–3 | Adds to the hardness and wear resistance. |
Others (e.g., Silicon, Iron) | ≤ 5 | Fine-tunes properties for specific applications. |
Key Characteristics
Why choose spherical cobalt-based alloy brazing powder over other options? Its unique combination of composition and spherical particle shape gives it several key advantages:
- Flowability: The spherical morphology ensures smooth flow and easy application, even in tight or complex geometries.
- High-Temperature Resistance: Cobalt alloys retain their strength at temperatures exceeding 1,000°C, making them ideal for turbine blades and other heat-stressed components.
- Corrosion and Oxidation Resistance: Chromium and nickel provide excellent resistance to harsh environments, including chemicals and extreme humidity.
- Wear Resistance: Tungsten and carbon add hardness, making this powder perfect for abrasive conditions.
- Versatility: Compatible with a wide range of base metals, including stainless steel, nickel alloys, and superalloys.
Properties of Spherical Cobalt-Based Alloy Brazing Powder
The exceptional performance of spherical cobalt-based alloy brazing powder is rooted in its physical, thermal, and mechanical properties. Below is a detailed overview:
Property | Value/Range | Significance |
---|---|---|
Density | ~8.0–9.0 g/cm³ | High density contributes to strong, durable joints. |
Melting Range | 1,150–1,350°C | Suitable for applications requiring high-temperature brazing. |
Thermal Conductivity | ~15–25 W/m·K | Moderate heat transfer, ideal for components exposed to thermal cycling. |
Hardness | ~400–600 HV | Excellent wear resistance for abrasive environments. |
Corrosion Resistance | Outstanding | Resists oxidation and chemical degradation in harsh environments. |
Particle Size | 10–100 µm | Optimized for uniform application in automated brazing systems. |
Applications of Spherical Cobalt-Based Alloy Brazing Powder
Thanks to its unique properties, spherical cobalt-based alloy brazing powder is used in a variety of demanding applications across multiple industries. Here’s a breakdown of its key uses:
Application | Industry | Details |
---|---|---|
Gas Turbines | Aerospace, Energy | Bonds components exposed to extreme heat and mechanical stress. |
Cutting Tools | Manufacturing | Forms wear-resistant joints in high-performance cutting and drilling tools. |
Medical Implants | Healthcare | Used for biocompatible joints in surgical tools and implants. |
Heat Exchangers | HVAC, Power Generation | Ensures corrosion-resistant, leak-proof connections in heat exchangers. |
Aerospace Components | Aerospace | Provides durable bonds for jet engine parts and other high-temperature components. |
Automotive Exhaust Systems | Automotive | Bonds parts in exhaust systems that withstand extreme heat and corrosive gases. |
Industrial Valves and Pumps | Oil and Gas | Creates strong joints in components exposed to abrasive and corrosive environments. |
Specifications, Sizes, and Standards
To meet the demands of various applications, spherical cobalt-based alloy brazing powders are produced in different sizes, grades, and standards. Below is an overview of typical specifications:
Specification | Details |
---|---|
Particle Size Range | 10–50 µm (precision applications), 50–100 µm (general brazing). |
Available Grades | Standard and high-purity cobalt-based alloys. |
Standards Compliance | AWS A5.8 (American Welding Society), ISO 17672 (International Brazing Standards). |
Packaging Options | 1 kg, 5 kg, 10 kg containers, vacuum-sealed to prevent oxidation. |
Suppliers and Pricing Details
Several reputable manufacturers produce and supply spherical cobalt-based alloy brazing powders. Below is a snapshot of key suppliers and their pricing:
Supplier | Grade Offered | Price (USD/kg) | Location | Contact |
---|---|---|---|---|
Wall Colmonoy | High-Performance Alloys | $400–$600 | USA/UK | www.wallcolmonoy.com |
Höganäs | Cobalt-Based Powders | $350–$550 | Sweden | www.hoganas.com |
Kennametal | Wear-Resistant Alloys | $450–$700 | USA | www.kennametal.com |
Oerlikon Metco | Specialty Brazing Alloys | $500–$800 | Switzerland | www.oerlikon.com |
Stellite (Deloro) | Cobalt-Based Powders | $400–$650 | USA | www.deloro.com |
Advantages and Limitations of Spherical Cobalt-Based Alloy Brazing Powder
Every material has its strengths and weaknesses. Here’s a comparison of the advantages and limitations of spherical cobalt-based alloy brazing powder:
Advantages | Limitations |
---|---|
Exceptional high-temperature performance. | Higher cost compared to other brazing alloys. |
Excellent wear resistance for abrasive conditions. | Requires precise heating control during brazing. |
Corrosion-resistant in harsh environments. | Not ideal for low-temperature applications. |
Smooth flowability for precise joints. | May require specialized equipment for application. |
Compatible with a variety of base metals. | Limited availability in some regions. |
FAQs About Spherical Cobalt-Based Alloy Brazing Powder
Question | Answer |
---|---|
What is spherical cobalt-based alloy brazing powder? | A powdered material used for high-performance metal bonding in extreme environments. |
What metals can it bond? | Commonly bonds stainless steel, nickel alloys, and superalloys. |
What is its melting range? | Typically between 1,150–1,350°C, depending on the alloy composition. |
Why is the spherical shape important? | It ensures better flowability, even distribution, and reduced waste. |
Is it environmentally safe? | Yes, but proper PPE is recommended during handling to prevent inhalation. |
Conclusion
Spherical Cobalt-Based Alloy Brazing Powder is a high-performance material designed for demanding applications where strength, durability, and resistance to extreme conditions are critical. Whether you’re bonding components in aerospace, power generation, or manufacturing, this powder offers unmatched performance and reliability.
While it may come with a higher cost, the investment pays off in applications requiring high-temperature strength, wear resistance, and corrosion durability. If you’re ready to upgrade your brazing processes, explore trusted suppliers, compare grades, and see how this innovative material can transform your projects.
Get Latest Price
About Met3DP
Product Category
HOT SALE
CONTACT US
Any questions? Send us message now! We’ll serve your request with a whole team after receiving your message.
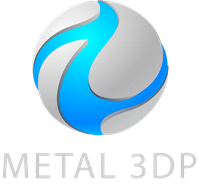
Metal Powders for 3D Printing and Additive Manufacturing