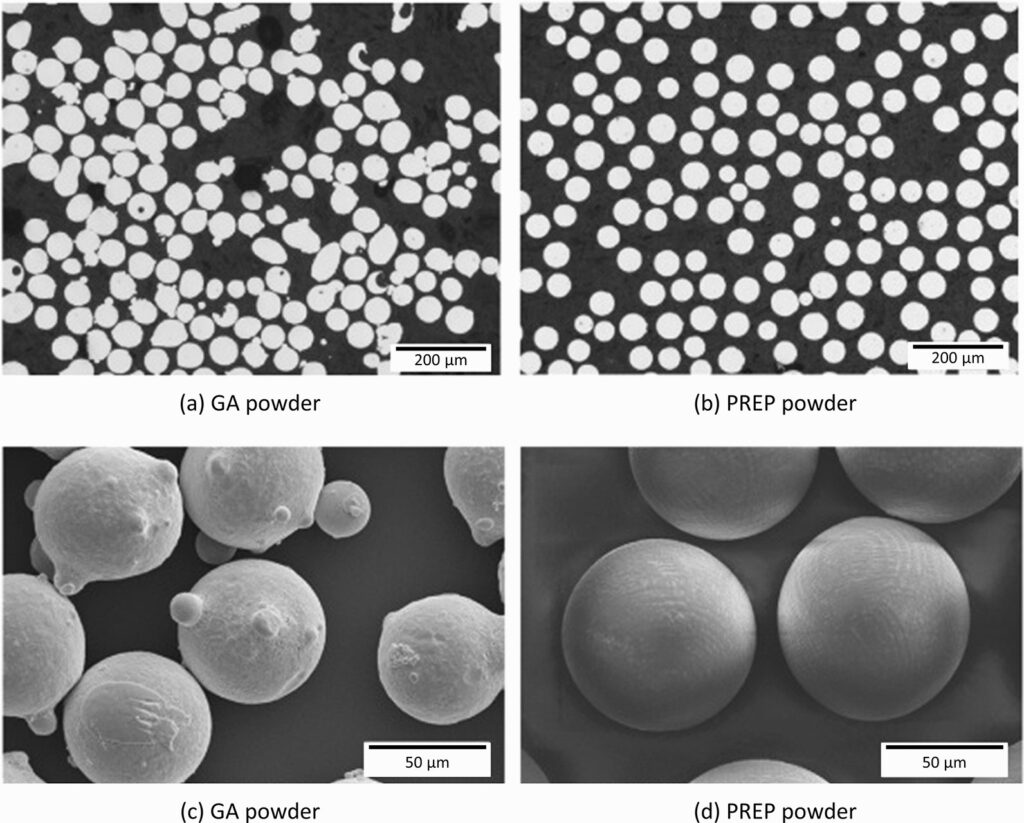
Spherical Copper Nickel Alloy CuNi Powder: The Essential Handbook for Superior Performance
Low MOQ
Provide low minimum order quantity to meet different needs.
OEM & ODM
Provide customized products and design services to meet unique customer needs.
Adequate Stock
Ensure fast order processing and provide reliable and efficient service.
Customer Satisfaction
Provide high quality products with customer satisfaction at the core.
share this article
Table of Contents
When it comes to cutting-edge materials that offer a unique blend of corrosion resistance, durability, and versatility, Spherical Copper Nickel Alloy (CuNi) Powder stands out. You’ve probably heard of copper-nickel alloys, especially if you’re in industries like marine engineering or electrical manufacturing. But what makes the spherical CuNi powder so special? Why is it becoming more popular in applications such as additive manufacturing, 3D printing, and powder metallurgy?
This comprehensive guide will walk you through everything you need to know about Spherical Copper Nickel Alloy CuNi Powder—from its composition and mechanical properties to its applications, pricing, and comparison with other materials. We’ll also cover the advantages and limitations of this powder compared to other alloys, ensuring you have all the information you need to make informed decisions for your next project.
Overview of Spherical Copper Nickel Alloy CuNi Powder
Spherical Copper Nickel Alloy (CuNi) Powder is made from a blend of copper (Cu) and nickel (Ni), with occasional traces of other elements such as iron (Fe) or manganese (Mn) to enhance specific properties. Its spherical shape is ideal for applications requiring smooth flow and uniform distribution, such as 3D printing or additive manufacturing. The spherical form leads to better packing density and flowability during production, making it a popular material for powder metallurgy and additive manufacturing processes.
This alloy is known for its corrosion resistance, especially in marine environments, and its ability to retain mechanical properties under high temperatures. The addition of nickel to copper significantly improves the alloy’s strength, ductility, and resistance to oxidation.
Why Is Spherical Copper Nickel Alloy CuNi Powder Important?
- Corrosion Resistance: CuNi alloys are famed for their resistance to sea water and brackish environments. This makes spherical CuNi powder an excellent choice for parts exposed to saltwater, such as marine engines and offshore platforms.
- High Mechanical Strength: The combination of copper and nickel offers an exceptional balance of strength and ductility, making this powder versatile for various industrial applications.
- Spherical Shape for Additive Manufacturing: The spherical form enhances the flowability and packing, ensuring consistent and high-quality results in 3D printing and powder-based manufacturing processes.
Composition and Properties of Spherical Copper Nickel Alloy CuNi Powder
To truly understand the benefits of Spherical CuNi Powder, we need to dig into its composition and mechanical properties. Each element in the alloy contributes specific qualities that make it suitable for high-performance applications.
Chemical Composition of Spherical Copper Nickel Alloy CuNi Powder?
The following table presents the typical elements found in copper-nickel alloys and their respective weight percentages, which may vary slightly depending on specific grades or product requirements.
Element | Weight Percentage (%) | Function/Contribution |
---|---|---|
Copper (Cu) | 60 – 90% | Base metal providing ductility and conductivity. |
Nickel (Ni) | 10 – 40% | Enhances corrosion resistance and strength. |
Iron (Fe) | 0.5 – 2.0% | Improves strength and oxidation resistance. |
Manganese (Mn) | 0.5 – 1.5% | Increases toughness and workability. |
Key Properties of Spherical Copper Nickel Alloy CuNi Powder?
Here’s a breakdown of the most critical properties that make Spherical CuNi Powder a go-to material for various industries:
Property | Typical Values |
---|---|
Density | 8.5 – 8.9 g/cm³ |
Ultimate Tensile Strength (UTS) | 300 – 600 MPa |
Yield Strength | 150 – 250 MPa |
Elongation at Break | 20 – 35% |
Electrical Conductivity | 5 – 10% IACS |
Thermal Conductivity | 30 – 50 W/m·K |
Melting Point | 1100°C – 1150°C |
Corrosion Resistance | Highly resistant to seawater and brine environments. |
Applications of Spherical Copper Nickel Alloy CuNi Powder
Spherical Copper Nickel Alloy Powder is versatile and finds use across several industries. Its unique properties—such as corrosion resistance, mechanical strength, and thermal stability—make it ideal for demanding applications where other materials may fall short.
Key Applications of Spherical Copper Nickel Alloy CuNi Powder?
Industry | Typical Applications |
---|---|
Marine | Shipbuilding, propeller shafts, valves, pumps |
Aerospace | Heat exchangers, hydraulic systems, landing gear |
Oil & Gas | Pipes, valves, bushings, fittings |
Electrical | Resistors, conductors, thermocouples |
Additive Manufacturing | 3D printed parts, rapid prototyping, custom components |
Marine Applications
Thanks to its resistance to seawater corrosion, CuNi alloys are commonly used in marine environments. Components such as propeller shafts, pumps, and valves are often made from CuNi because of its ability to withstand prolonged exposure to saltwater without degrading. Spherical CuNi Powder is especially advantageous in producing these components because it offers superior flowability and packing density during the manufacturing process.
Aerospace Applications
In the aerospace industry, Spherical CuNi Powder is used in components like heat exchangers, hydraulic systems, and landing gear parts. The alloy’s ability to maintain its mechanical properties at high temperatures is crucial for aerospace applications, where thermal management is vital.
Oil & Gas Applications
The oil and gas sector also benefits from the corrosion resistance of CuNi alloys. Spherical CuNi Powder is used to manufacture pipes, valves, and bushings that are exposed to corrosive fluids and harsh environmental conditions. The alloy’s ability to resist both oxidation and corrosion ensures long-lasting performance in subsea and offshore oil rigs.
Additive Manufacturing (3D Printing)
One of the most exciting uses of Spherical CuNi Powder is in additive manufacturing. The powder’s spherical shape ensures excellent flowability and packing density, which are essential for 3D printing processes like Selective Laser Melting (SLM) and Electron Beam Melting (EBM). This makes it ideal for producing custom components, prototypes, and small-batch manufacturing.
Specifications, Sizes, Grades, and Standards for Spherical Copper Nickel Alloy CuNi Powder
When selecting Spherical CuNi Powder for industrial use, understanding the specifications, particle sizes, and industry standards is crucial. These factors determine whether the powder is suitable for your specific application.
Common Specifications and Particle Sizes for Spherical Copper Nickel Alloy CuNi Powder?
Specification | Details |
---|---|
Particle Size Distribution | 10 – 45 µm (for additive manufacturing), 45 – 150 µm (for casting) |
Purity | ≥ 99.5% (alloy content) |
Bulk Density | 4.5 – 5.0 g/cm³ |
Flowability | 10 – 15 seconds/50g (measured via a Hall Flowmeter) |
Packaging | Available in 1kg, 5kg, 10kg, and bulk orders |
Standards | ASTM B151, ASTM B122, ISO 9001 |
Available Particle Sizes for Different Applications
Particle Size | Application |
---|---|
10 – 30 µm | High-precision additive manufacturing, laser sintering |
30 – 45 µm | Powder metallurgy, metal injection molding |
45 – 150 µm | Bulk powder applications, casting, sintering |
Why Particle Size Matters
The particle size of Spherical CuNi Powder affects its flowability, packing density, and surface finish. Finer powders (10 – 30 µm) are ideal for high-precision additive manufacturing, while coarser powders (45 – 150 µm) are more suited for casting and sintering processes.
Suppliers and Pricing for Spherical Copper Nickel Alloy CuNi Powder
The price of Spherical Copper Nickel Alloy Powder varies depending on factors like particle size, purity, and order volume. Several suppliers around the globe produce high-quality CuNi powder for various industrial applications.
Top Suppliers and Pricing for Spherical Copper Nickel Alloy CuNi Powder?
Supplier | Product Description | Price per kg (USD) | Comments |
---|---|---|---|
LPW Technology | Spherical CuNi powder for additive manufacturing | $150 – $220 | Known for high-quality powders for AM applications. |
Höganäs | CuNi alloy powder for powder metallurgy | $140 – $200 | Leading supplier of powders for sintering and casting. |
Sandvik Osprey | CuNi powder for marine applications | $130 – $190 | Offers marine-grade powders with high corrosion resistance. |
Carpenter Additive | CuNi powder for aerospace and 3D printing | $160 – $230 | Specializes in powders for aerospace and AM industries. |
Tekna | High-purity CuNi powder for custom manufacturing | $140 – $210 | Focuses on high-purity powders for demanding applications. |
Factors Influencing Pricing
- Particle size: Finer powders (10 – 30 µm) geared for high-precision additive manufacturing tend to cost more due to the extra processing involved.
- Order volume: As with many industrial materials, buying in bulk can significantly reduce the price per kilogram.
- Supplier reputation: Premium suppliers with a history of quality control and certified standards may charge higher prices.
- Special applications: Powders designed for specific industries like aerospace or marine may have stricter quality standards, resulting in higher costs.
Comparing the Pros and Cons of Spherical Copper Nickel Alloy CuNi Powder
Like any material, Spherical CuNi Powder comes with its own set of advantages and limitations. Let’s take a closer look at the pros and cons to help you decide if it’s the right choice for your application.
Advantages of Spherical Copper Nickel Alloy CuNi Powder
Advantage | Description |
---|---|
Exceptional corrosion resistance | Ideal for marine and offshore applications exposed to saltwater. |
High strength and toughness | Provides excellent mechanical properties, even at elevated temperatures. |
Spherical shape | Ensures superior flowability and packing density in additive manufacturing. |
Thermal stability | Maintains mechanical strength at high temperatures, making it suitable for aerospace. |
Good machinability | Easily machined, making it ideal for precision components. |
Limitations of Spherical Copper Nickel Alloy CuNi Powder
Limitation | Description |
---|---|
Higher cost | More expensive than standard copper or nickel alloys due to its corrosion resistance. |
Lower electrical conductivity | Compared to pure copper, CuNi alloys have reduced electrical conductivity. |
Potential work hardening | May require annealing or heat treatment to restore ductility after cold working. |
Oxidation at high temperatures | Requires surface coatings or treatments to prevent oxidation in high-temperature environments. |
Frequently Asked Questions (FAQ) About Spherical Copper Nickel Alloy CuNi Powder
What industries commonly use Spherical Copper Nickel Alloy Powder?
| Answer: Spherical CuNi Powder is widely used in industries such as marine engineering, aerospace, oil & gas, electrical manufacturing, and additive manufacturing. Its corrosion resistance, strength, and performance at high temperatures make it ideal for these demanding sectors.
How does Spherical CuNi Powder compare to other copper alloys?
| Answer: Compared to other copper alloys, Spherical Copper Nickel Alloy CuNi Powder? offers superior corrosion resistance—especially in marine environments—and better mechanical strength. However, it is typically more expensive due to its nickel content, and has lower electrical conductivity than pure copper.
Is Spherical CuNi Powder suitable for additive manufacturing?
| Answer: Yes! The spherical shape of CuNi powder ensures excellent flowability and packing density, which are critical for 3D printing and additive manufacturing processes like Selective Laser Melting (SLM) and Electron Beam Melting (EBM).
What is the price range for Spherical Copper Nickel Alloy Powder?
| Answer: The price of Spherical CuNi Powder typically ranges from $130 to $230 per kilogram, depending on factors such as particle size, purity, and order volume.
Can Spherical CuNi Powder be used in high-temperature environments?
| Answer: Absolutely! Spherical CuNi Powder maintains its mechanical properties and corrosion resistance even at elevated temperatures, making it suitable for applications like aerospace components, heat exchangers, and industrial furnaces.
Conclusion: Why Choose Spherical Copper Nickel Alloy CuNi Powder?
In conclusion, Spherical Copper Nickel Alloy (CuNi) Powder offers a unique combination of mechanical strength, corrosion resistance, and thermal stability, making it a top choice for industries ranging from marine engineering to aerospace and additive manufacturing. While it may come with a higher price tag compared to other alloys, its long-term performance and durability in demanding environments make it a worthwhile investment.
Whether you’re 3D printing high-performance components, building marine structures, or manufacturing aerospace parts, Spherical CuNi Powder is a high-quality material that delivers exceptional results where strength and resistance matter most.
Get Latest Price
About Met3DP
Product Category
HOT SALE
CONTACT US
Any questions? Send us message now! We’ll serve your request with a whole team after receiving your message.