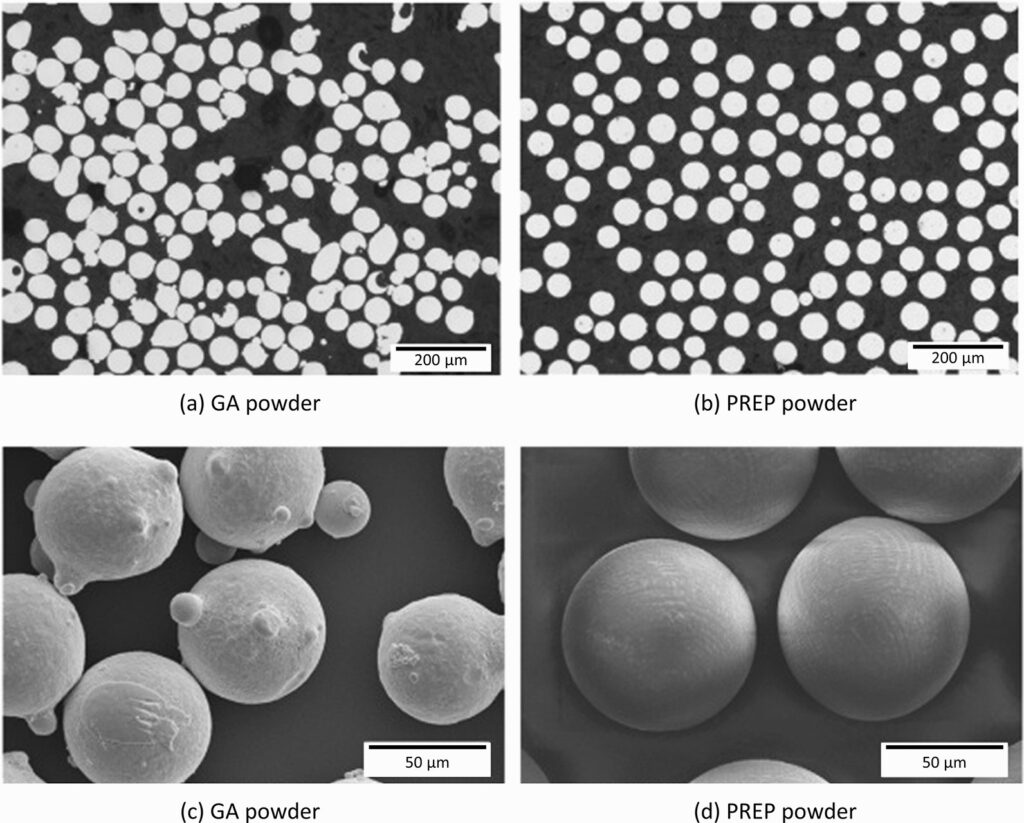
Spherical High-Entropy Alloy Powder: A Breakthrough for Precision Engineering
Low MOQ
Provide low minimum order quantity to meet different needs.
OEM & ODM
Provide customized products and design services to meet unique customer needs.
Adequate Stock
Ensure fast order processing and provide reliable and efficient service.
Customer Satisfaction
Provide high quality products with customer satisfaction at the core.
share this article
Table of Contents
In the ever-evolving world of materials science, spherical high-entropy alloy (HEA) powders are one of the most exciting innovations in recent years. These multi-component alloys, which often contain five or more principal elements in near-equal atomic ratios, offer superior mechanical properties, high strength, wear resistance, and exceptional thermal stability. If you’re involved in industries like additive manufacturing, aerospace, or automotive engineering, you’re probably already thinking about how these powders can transform your production processes.
But what exactly makes spherical high-entropy alloy powder so special? How does it compare to traditional materials like stainless steel, titanium alloys, or nickel-based superalloys? And perhaps more importantly, how can you use it to give your projects a competitive edge?
In this comprehensive guide, we’ll dive deep into the world of spherical high-entropy alloy powder—its composition, properties, applications, pricing, and much more. Stick with us, and by the end, you’ll have all the information you need to decide if this cutting-edge material is the right fit for your next project.
Overview: What is Spherical High-Entropy Alloy Powder?
Let’s start with the basics. High-entropy alloys (HEAs) are a relatively new class of materials that differ from traditional alloys in their composition. Instead of having one or two primary elements, HEAs consist of five or more elements mixed in (nearly) equal proportions. This unique composition results in unparalleled material properties, including high strength, excellent corrosion resistance, and remarkable thermal stability.
But why the spherical shape? In advanced manufacturing processes like additive manufacturing (AM) or 3D printing, the shape of the powder particles matters a lot. Spherical powders ensure better flowability, packing density, and layer uniformity—all of which are essential for precision manufacturing.
Key Features of Spherical High-Entropy Alloy Powder
- Multi-component composition: Typically containing five or more elements in near-equal proportions (e.g., Fe, Ni, Cr, Co, Ti).
- Exceptional mechanical properties: High strength, hardness, and excellent wear resistance.
- Thermal stability: Performs well in high-temperature environments, maintaining structural integrity.
- Corrosion resistance: Resistant to oxidation and corrosion in harsh environments.
- Spherical shape: Enables superior flowability and packing density, critical for additive manufacturing.
- Versatility: Used across industries like aerospace, automotive, energy, and medical.
Types, Composition, and Properties of Spherical High-Entropy Alloy Powder
While all high-entropy alloys share the characteristic of having multiple principal elements, the exact composition and properties can vary widely depending on the specific alloy system. Let’s explore the different types of HEA powders, their composition, and the mechanical properties that make them stand out.
Types and Composition of Spherical High-Entropy Alloy Powder
Type | Typical Composition | Primary Applications |
---|---|---|
Cantor Alloy (CoCrFeMnNi) | Co, Cr, Fe, Mn, Ni (equimolar ratio) | Aerospace, automotive, corrosion-resistant components |
AlCoCrFeNi | Al, Co, Cr, Fe, Ni | High-temperature applications, power generation, turbines |
FeCoCrNiMo | Fe, Co, Cr, Ni, Mo | Wear-resistant coatings, high-stress environments |
TiZrHfNbTa | Ti, Zr, Hf, Nb, Ta | Biomedical implants, aerospace components, cryogenic materials |
AlTiVCrFe | Al, Ti, V, Cr, Fe | Lightweight structures, high-strength components |
Each of these high-entropy alloys offers a unique combination of properties that makes them suitable for different applications. For example, Cantor alloys are known for their excellent corrosion resistance, while AlCoCrFeNi alloys are prized for their high-temperature stability.
Physical and Mechanical Properties of Spherical High-Entropy Alloy Powder
Property | Typical Value |
---|---|
Density | ~6.5 to 8.5 g/cm³ (depending on composition) |
Melting Point | 1,200°C to 1,600°C |
Hardness (Vickers) | 300 to 600 HV |
Tensile Strength | 1,000 to 1,500 MPa |
Thermal Conductivity | 5 to 15 W/m·K |
Modulus of Elasticity | 150 to 220 GPa |
Corrosion Resistance | Excellent in seawater and aggressive chemical environments |
Oxidation Resistance | High, especially at elevated temperatures |
The mechanical properties of spherical high-entropy alloy powders are heavily influenced by their multi-component composition, which allows these materials to perform well in high-stress and high-temperature environments. For instance, the tensile strength of HEA powders can easily surpass that of conventional materials like stainless steel or titanium, making them ideal for critical applications in the aerospace or automotive industries.
Applications of Spherical High-Entropy Alloy Powder
The unique properties of spherical high-entropy alloy powder make it highly versatile, with applications across a wide range of industries. Let’s dive into some of the most common uses for this advanced material and why it’s gaining traction in high-tech manufacturing processes.
Key Applications of Spherical High-Entropy Alloy Powder
Industry | Application | Why HEA Powder? |
---|---|---|
Aerospace | Turbine blades, engine components, structural parts | High strength-to-weight ratio, excellent thermal stability |
Additive Manufacturing | 3D printing of complex geometries | Superior flowability, high packing density, and excellent layer uniformity |
Medical | Biomedical implants, prosthetics | Biocompatibility, corrosion resistance, and high mechanical strength |
Automotive | Lightweight engine parts, high-performance exhaust systems | High strength, excellent wear resistance, and heat tolerance |
Energy | Power generation components, nuclear reactors | Exceptional thermal stability and corrosion resistance |
Tooling | Cutting tools, wear-resistant coatings | High hardness, wear resistance, and prolonged tool life |
Example: High-Entropy Alloys in Aerospace Applications
In the aerospace industry, weight savings and mechanical performance are critical factors. Spherical high-entropy alloy powders are increasingly being used to manufacture engine components, turbine blades, and structural parts because they offer a superior strength-to-weight ratio compared to traditional materials like superalloys. Additionally, their oxidation resistance and ability to perform at high temperatures make them a perfect fit for turbine blades, which need to withstand extreme conditions without losing integrity.
Specifications, Sizes, Grades, and Standards for Spherical High-Entropy Alloy Powder
When selecting spherical high-entropy alloy powders for your project, it’s important to be aware of the available specifications, sizes, and grades. Different applications may require different particle sizes or compositions, and ensuring your material meets the necessary standards is crucial for performance and safety.
Common Specifications and Grades of Spherical High-Entropy Alloy Powder
Specification | Value |
---|---|
Purity | 98.0% – 99.9% (depending on alloy type) |
Particle Size | 10 µm to 100 µm (varies depending on application) |
Flowability | Excellent for use in powder bed fusion and laser powder bed fusion |
Packing Density | High, ensuring uniformity in additive manufacturing processes |
Standards | ASTM B243, ASTM F3302 (Additive Manufacturing), ASTM B212 (metal powders) |
Grade | Different grades based on elemental composition (e.g., AlCoCrFeNi, TiZrNbMoTa) |
Available Sizes and Forms
The particle size of the powder is crucial for determining its suitability for different manufacturing processes. For example, smaller particles are ideal for additive manufacturing or powder bed fusion, while larger particles may be better suited for powder metallurgy processes that require high packing density.
Size Range | Application |
---|---|
10–20 µm | Thin films, coatings, electronics, and microstructures |
20–45 µm | Additive manufacturing, laser powder bed fusion, fine powder metallurgy |
45–100 µm | Aerospace components, large-scale 3D printing, powder metallurgy |
Standards for Spherical High-Entropy Alloy Powder
It’s essential that spherical HEA powders meet the relevant industry standards, especially for use in critical industries like aerospace and medical devices.
- ASTM F3302: Standard for additive manufacturing of metallic components.
- ASTM B243: Standard terminology for powder metallurgy.
- ASTM B212: Standard test method for density of metal powders.
Suppliers and Pricing of Spherical High-Entropy Alloy Powder
Pricing for spherical high-entropy alloy powder can vary depending on factors like purity, composition, particle size, and the production method used. As a relatively new material, HEA powders are generally more expensive than traditional materials, but their performance advantages can offset the cost in high-tech applications.
Suppliers of Spherical High-Entropy Alloy Powder
Supplier | Location | Available Grades | Price per Kg (Approx.) |
---|---|---|---|
American Elements | USA | Cantor alloys, AlCoCrFeNi, TiZrNbMoTa | $500 – $2,500 |
TLS Technik | Germany | High-purity HEA powders for additive manufacturing | $600 – $3,000 |
Goodfellow | UK | Cantor alloy, Ti-based HEA powders | $700 – $2,800 |
Advanced Refractory Metals | USA | High-purity HEA powders, multi-component alloys | $550 – $2,700 |
Stanford Advanced Materials | USA | AlCoCrFeNi, Ti-based HEA powders | $600 – $3,200 |
Factors Affecting the Price of Spherical High-Entropy Alloy Powder
Several factors influence the cost of spherical HEA powder:
- Purity: Higher purity powders are more expensive due to the additional processing required.
- Alloy Composition: Complex alloys with more exotic elements like tantalum or hafnium tend to be more expensive.
- Particle Size: Finer powders require more advanced production techniques, which drives up the price.
- Production Method: Methods like gas atomization or plasma spheroidization ensure high-quality powders, but they also add to the cost.
- Bulk Purchasing: As with most materials, buying in larger quantities can help reduce the overall cost per kilogram.
Advantages and Limitations of Spherical High-Entropy Alloy Powder
While spherical high-entropy alloy powder offers many benefits, it’s important to consider both the advantages and limitations to determine whether it’s the right material for your specific application.
Advantages and Limitations of Spherical High-Entropy Alloy Powder
Advantages | Limitations |
---|---|
High Strength-to-Weight Ratio: Ideal for lightweight, high-strength components | Cost: High-entropy alloys are generally more expensive than traditional materials |
Thermal Stability: Performs well in high-temperature environments | Production Complexity: HEA powders require advanced manufacturing techniques |
Corrosion Resistance: Excellent in aggressive environments | Limited Availability: High-quality HEA powders may be harder to source |
Wear Resistance: Ideal for high-wear applications like cutting tools | Processing Difficulty: Requires specialized equipment for additive manufacturing |
Versatility: Suitable for a wide range of industries and applications | Research Stage: Some HEAs are still in the experimental phase, limiting their commercial use |
For example, while spherical HEA powder is an ideal material for aerospace and medical implants due to its high strength and thermal stability, it may not be the best choice for more cost-sensitive projects where cheaper materials like steel or aluminum could suffice.
Spherical High-Entropy Alloy Powder vs. Other Materials
When deciding whether spherical HEA powder is the right material for your project, it’s essential to compare it to other common materials like titanium alloys, aluminum, and stainless steel. Let’s explore how HEA powders stack up against these materials in terms of performance, cost, and applications.
Comparison of Spherical High-Entropy Alloy Powder with Other Materials
Material | Key Properties | Cost Comparison | Common Applications |
---|---|---|---|
High-Entropy Alloys (HEA) | High strength, thermal stability, corrosion resistance | More expensive than most metals | Aerospace, medical implants, additive manufacturing |
Titanium Alloys | Lightweight, high strength, biocompatible | Similar or slightly cheaper than HEAs | Aerospace, medical implants, automotive |
Aluminum | Lightweight, good corrosion resistance | Cheaper than HEAs | Automotive, aerospace, construction |
Stainless Steel | High strength, good wear resistance | Much cheaper than HEAs | Construction, tools, industrial machinery |
Compared to titanium alloys, high-entropy alloys offer similar strength but outperform in thermal stability and corrosion resistance. However, titanium is still the go-to material for applications where biocompatibility is critical, such as in medical implants. On the other hand, aluminum and stainless steel offer lower costs but lack the high-performance properties of HEAs, making them less suitable for critical applications.
Frequently Asked Questions (FAQ) About Spherical High-Entropy Alloy Powder
Common Questions About Spherical High-Entropy Alloy Powder
Question | Answer |
---|---|
What makes high-entropy alloys different from traditional alloys? | HEAs are composed of five or more principal elements in near-equal ratios, leading to superior mechanical properties. |
Why are HEA powders spherical? | The spherical shape improves flowability, packing density, and layer uniformity, which are essential for additive manufacturing. |
What industries use spherical high-entropy alloy powder? | Common industries include aerospace, automotive, medical, and energy due to the material’s high strength, wear resistance, and thermal stability. |
How does the price of HEA powder compare to traditional materials? | HEA powders are generally more expensive than traditional materials like stainless steel or aluminum due to the complexity of their composition and production. |
Can spherical HEA powder be used for 3D printing? | Yes, spherical HEA powders are often used in additive manufacturing because their flowability and packing density are ideal for laser powder bed fusion and other 3D printing techniques. |
How does HEA powder compare to titanium alloys? | HEA powders offer better thermal stability and corrosion resistance, but titanium alloys are still preferred for applications requiring biocompatibility. |
Are high-entropy alloys safe for medical implants? | Some HEAs, like TiZrNbMoTa, are biocompatible and suitable for medical implants, though further research is ongoing. |
What particle size is best for additive manufacturing? | Particle sizes between 20 µm and 45 µm are typically ideal for additive manufacturing and laser powder bed fusion. |
Conclusion: Is Spherical High-Entropy Alloy Powder Right for Your Project?
In conclusion, spherical high-entropy alloy powder is a revolutionary material that offers high strength, thermal stability, and corrosion resistance—properties that make it an ideal choice for aerospace, medical, and automotive applications. While it comes with a higher price tag compared to more conventional materials like aluminum or stainless steel, its unmatched performance in extreme conditions makes it worth the investment for high-tech applications.
However, HEA powders are still relatively new, and while they hold immense promise, they may not be suitable for every project—especially if cost is a major concern. If your project demands exceptional mechanical properties and the ability to perform in high-stress or high-temperature environments, then spherical high-entropy alloy powder is likely the right choice for you. But for less demanding applications, traditional materials like titanium or steel may still serve you well.
Ultimately, spherical HEA powders are helping to push the boundaries of what’s possible in advanced manufacturing, and their future looks brighter than ever. If you’re ready to take your engineering projects to the next level, it’s time to seriously consider incorporating this cutting-edge material into your processes.
Get Latest Price
About Met3DP
Product Category
HOT SALE
CONTACT US
Any questions? Send us message now! We’ll serve your request with a whole team after receiving your message.
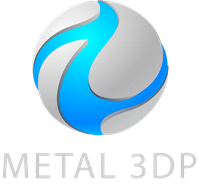
Metal Powders for 3D Printing and Additive Manufacturing