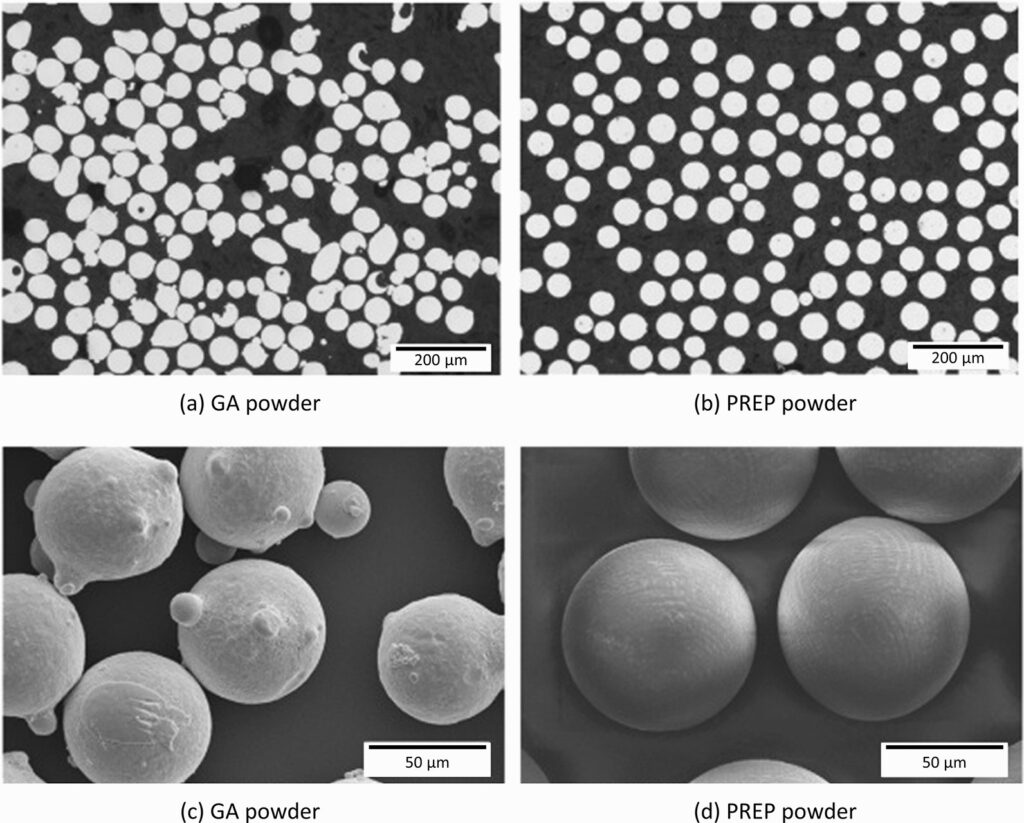
Spherical Mold Steel Alloy Powder: Exceptional Quality for Demanding Applications
Low MOQ
Provide low minimum order quantity to meet different needs.
OEM & ODM
Provide customized products and design services to meet unique customer needs.
Adequate Stock
Ensure fast order processing and provide reliable and efficient service.
Customer Satisfaction
Provide high quality products with customer satisfaction at the core.
share this article
Table of Contents
In the realm of modern manufacturing, materials selection is critical. One material that has been making significant strides in recent years is Spherical Mold Steel Alloy Powder. Whether you’re in the automotive, aerospace, or tooling industry, understanding the properties and applications of this alloy powder could offer you a competitive edge.
In this ultimate guide, we’ll break down everything you need to know about Spherical Mold Steel Alloy Powder—from its unique properties to its diverse applications and pricing. This article will serve as your go-to resource for selecting and utilizing this material to its full potential.
Overview: What is Spherical Mold Steel Alloy Powder?
Let’s start with the basics. Spherical Mold Steel Alloy Powder is a type of metal powder specifically designed for additive manufacturing (AM) and metal injection molding (MIM) processes. Its spherical shape makes it ideal for high-precision applications, because it ensures excellent flowability, packing density, and uniform layer deposition—all crucial factors for 3D printing and mold manufacturing.
But why steel alloys? Steel alloys are known for their strength, hardness, and resistance to wear—qualities that are indispensable for tools and molds. Combining these properties with the benefits of powder metallurgy gives manufacturers a highly versatile material that offers both mechanical performance and production efficiency.
Why Spherical?
The spherical shape isn’t just an aesthetic choice. Unlike irregularly shaped particles, spherical powders are easier to handle, flow more smoothly through machinery, and produce more uniform layers during additive processes. Think of pouring sand versus pouring marbles into a container—one clumps, the other flows freely. The same principle applies to spherical powder, ensuring tighter packing and superior material characteristics.
Composition, Properties, and Characteristics of Spherical Mold Steel Alloy Powder
Understanding the composition and properties of Spherical Mold Steel Alloy Powder is essential for determining whether it’s right for your project. Different steel alloys are designed to meet various performance criteria, and the exact composition can influence factors like hardness, wear resistance, corrosion resistance, and machinability.
Chemical Composition of Spherical Mold Steel Alloy Powder
Here’s a general breakdown of typical compositions for Spherical Mold Steel Alloy Powders, though exact formulations can vary by manufacturer and application:
Element | Percentage (%) | Role in the Alloy |
---|---|---|
Carbon (C) | 0.2% – 1.2% | Improves hardness and wear resistance |
Chromium (Cr) | 12% – 18% | Enhances corrosion resistance and toughness |
Molybdenum (Mo) | 0.3% – 5.0% | Increases strength and heat resistance |
Nickel (Ni) | 0.5% – 5.0% | Adds toughness and improves corrosion resistance |
Vanadium (V) | 0.1% – 1.0% | Increases hardness and wear resistance |
Silicon (Si) | 0.3% – 1.0% | Enhances material strength and hardness |
Manganese (Mn) | 0.5% – 2.0% | Improves strength and toughness |
Key Properties of Spherical Mold Steel Alloy Powder
Property | Typical Range |
---|---|
Hardness (HRC) | 50 – 62 (depending on heat treatment) |
Density | 7.7 – 8.0 g/cm³ |
Tensile Strength | 1,000 – 2,500 MPa |
Thermal Conductivity | 20 – 25 W/m·K |
Melting Point | 1,400 – 1,500°C |
Flowability | Excellent due to spherical shape |
Wear Resistance | High, especially with chromium and vanadium |
Corrosion Resistance | Moderate to high (depending on chromium content) |
Machinability | Good, especially when post-processed |
Why Choose Spherical Mold Steel Alloy Powder?
The properties of Spherical Mold Steel Alloy Powder are tailored to meet the specific demands of tooling, molding, and additive manufacturing. For example, its hardness and wear resistance make it ideal for tools that will undergo significant mechanical stress, while its corrosion resistance ensures longevity even in harsh environments.
But it’s not just about strength. The flowability of the powder—thanks to its spherical shape—ensures smoother, more consistent layers during 3D printing and metal injection molding processes. This leads to fewer defects, better part quality, and increased production efficiency.
Applications of Spherical Mold Steel Alloy Powder
The versatility of Spherical Mold Steel Alloy Powder means it can be used in a wide range of industries and applications. Whether you’re creating injection molds for plastic parts or 3D printing complex metal components, this material offers the performance you need.
Common Applications of Spherical Mold Steel Alloy Powder
Industry | Typical Applications |
---|---|
Automotive | High-strength molds for plastic and metal parts, 3D-printed components |
Aerospace | Complex geometries for engine components, structural parts |
Tooling and Molding | Injection molds, die-casting molds, and wear-resistant tools |
Medical Devices | Surgical tools, biocompatible implants, and precision components |
Additive Manufacturing | 3D-printed metal parts, custom tooling, and prototypes |
Energy | Heat-resistant parts for turbines, oil rigs, and power plants |
Why Is Spherical Mold Steel Alloy Powder Ideal for Injection Molding?
In injection molding, the molds themselves are subjected to high levels of thermal and mechanical stress. Spherical Mold Steel Alloy Powder provides the necessary hardness and wear resistance, ensuring that the molds last longer and maintain their shape under repeated use. Additionally, its high thermal conductivity helps dissipate heat quickly, improving cycle times and overall production efficiency.
Additive Manufacturing: A New Frontier for Mold Steel Alloy Powder
Additive manufacturing (AM), or 3D printing, has opened up new possibilities for mold steel alloy powders. In traditional manufacturing, creating complex geometries can be time-consuming and expensive. With AM, manufacturers can now produce intricate parts directly from digital designs, reducing lead times and enabling the creation of custom tools and molds that would be impossible with conventional methods.
Specifications, Sizes, and Standards for Spherical Mold Steel Alloy Powder
When selecting Spherical Mold Steel Alloy Powder for your project, it’s crucial to understand the various specifications, sizes, and standards available. These factors will influence the performance, compatibility, and processing requirements of the material.
Common Specifications for Spherical Mold Steel Alloy Powder
Specification | Details |
---|---|
Particle Size Range | 15 – 63 μm (common for additive manufacturing) |
Purity | ≥ 99.5% |
Bulk Density | 4.5 – 5.5 g/cm³ (varies by particle size) |
Flow Rate (Hall Flow) | 20 – 35 s/50g |
Oxygen Content | ≤ 0.03% (critical for high-strength applications) |
Packaging | Available in 1 kg, 5 kg, 10 kg, and bulk quantities |
Certification | ISO 9001, ASTM F3302 (Additive Manufacturing) |
Common Sizes of Spherical Mold Steel Alloy Powder
Particle size plays a key role in determining the performance of the powder in additive manufacturing and molding applications. Smaller particles tend to provide better surface finish and higher detail resolution, while larger particles may offer quicker build times but with less precision.
Particle Size | Application |
---|---|
15 – 30 μm | High-precision 3D printing, fine details |
30 – 45 μm | General 3D printing, metal injection molding |
45 – 63 μm | Faster build speeds, larger parts with less detail |
Industry Standards for Spherical Mold Steel Alloy Powder
Ensuring that the material meets industry standards is crucial for maintaining quality and performance. Here are the most common standards you should look for when selecting Spherical Mold Steel Alloy Powder:
- ISO 9001: Certification for quality management systems.
- ASTM F3302: Standard for additive manufacturing feedstock materials.
- AMS 4998: Aerospace material specification for high-strength alloys.
Adhering to these standards ensures that the powder is produced to the highest quality, making it suitable for critical applications in industries like aerospace and medical devices.
Suppliers and Pricing for Spherical Mold Steel Alloy Powder
Pricing for Spherical Mold Steel Alloy Powder can vary depending on factors like particle size, purity, and order quantity. While it may be more expensive than traditional steel powders, its superior performance in high-stress and high-precision applications often justifies the investment.
Top Suppliers and Pricing for Spherical Mold Steel Alloy Powder
Supplier | Product Description | Price per kg (USD) | Comments |
---|---|---|---|
Höganäs AB | Spherical mold steel alloy, 15-45 μm | $300 – $500 | High-purity powder for tooling and molding |
GKN Additive | Spherical tool steel powder, 20-63 μm | $400 – $600 | Premium quality for additive manufacturing |
Carpenter Additive | Alloy steel powder, spherical, 25-50 μm | $350 – $550 | Suitable for metal injection molding and 3D printing |
Sandvik Osprey | Spherical mold steel, 30-45 μm | $380 – $600 | High-performance powder for industrial applications |
Tekna Advanced Materials | Tool steel powder, spherical, 20-63 μm | $400 – $700 | Ideal for high-strength, wear-resistant tools |
Factors Affecting Pricing
Several factors influence the price of Spherical Mold Steel Alloy Powder, including:
- Particle Size: Smaller particles (e.g., 15-30 μm) are typically more expensive due to the precision required in production.
- Purity: Higher purity levels (≥ 99.5%) are more costly but essential for critical applications like medical devices and aerospace.
- Order Quantity: Bulk purchases often come with discounts, so buying in larger quantities can reduce the price per kilogram.
- Special Treatments: Some powders may be treated or coated to enhance specific properties, which can also affect the cost.
Advantages and Limitations of Spherical Mold Steel Alloy Powder
Like any material, Spherical Mold Steel Alloy Powder has its share of strengths and weaknesses. Understanding these can help you determine whether it’s the right fit for your project—and how to maximize its benefits while minimizing any drawbacks.
Advantages of Spherical Mold Steel Alloy Powder
Advantages | Details |
---|---|
High Strength and Hardness | Excellent mechanical properties, especially after heat treatment. |
Wear Resistance | High resistance to wear and deformation, ideal for tooling applications. |
Good Flowability | Spherical shape ensures smooth flow during 3D printing and molding processes. |
Corrosion Resistance | Chromium and molybdenum content provide moderate to high corrosion resistance. |
Thermal Stability | Can withstand high temperatures without losing structural integrity. |
Versatility | Suitable for a wide range of industries, from automotive to medical devices. |
Limitations of Spherical Mold Steel Alloy Powder
Limitations | Details |
---|---|
Cost | Generally more expensive than traditional steel powders due to higher purity and precision. |
Processing Complexity | May require specialized equipment for optimal results in additive manufacturing. |
Limited Availability | Spherical powders may have longer lead times compared to irregular powders. |
Post-Processing Requirements | Heat treatment and finishing may be necessary to achieve desired properties. |
FAQs About Spherical Mold Steel Alloy Powder
Common Questions and Answers
Question | Answer |
---|---|
What is Spherical Mold Steel Alloy Powder used for? | It’s used in tooling, molding, and additive manufacturing for high-strength and wear-resistant applications. |
Is Spherical Mold Steel Alloy Powder suitable for 3D printing? | Yes, its flowability and spherical shape make it ideal for additive manufacturing processes. |
How does Spherical Mold Steel Alloy Powder compare to traditional steel powders? | It offers better flowability, uniformity, and precision, especially in 3D printing and molding applications. |
What size of Spherical Mold Steel Alloy Powder should I use for injection molding? | A particle size range of 30-45 μm is typically ideal for metal injection molding. |
What industries benefit most from Spherical Mold Steel Alloy Powder? | Industries like automotive, aerospace, and medical devices benefit from its durability, wear resistance, and precision. |
Conclusion: Why Spherical Mold Steel Alloy Powder Is a Game-Changer for Modern Manufacturing
Spherical Mold Steel Alloy Powder is a cutting-edge material that offers a unique blend of strength, hardness, and precision. Its properties make it indispensable for industries where performance and durability are paramount, such as automotive, aerospace, and tooling.
While it may come with a higher price tag compared to traditional materials, the long-term benefits—from longer tool life to faster production cycles—make it a worthwhile investment for any manufacturer looking to push the boundaries of what’s possible. Whether you’re creating complex molds or 3D printing intricate parts, Spherical Mold Steel Alloy Powder offers the performance and reliability you need to stay ahead in today’s competitive market.
Get Latest Price
About Met3DP
Product Category
HOT SALE
CONTACT US
Any questions? Send us message now! We’ll serve your request with a whole team after receiving your message.
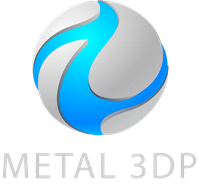
Metal Powders for 3D Printing and Additive Manufacturing