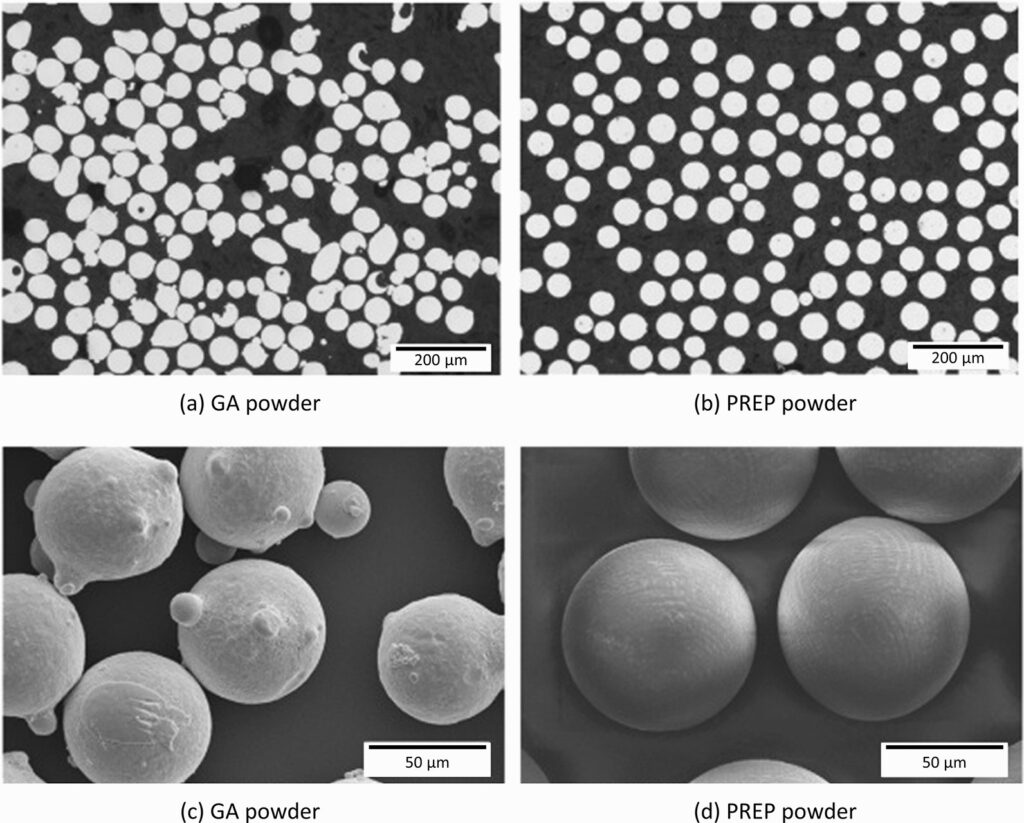
How Spherical Molybdenum Powder is Transforming Advanced Manufacturing
Low MOQ
Provide low minimum order quantity to meet different needs.
OEM & ODM
Provide customized products and design services to meet unique customer needs.
Adequate Stock
Ensure fast order processing and provide reliable and efficient service.
Customer Satisfaction
Provide high quality products with customer satisfaction at the core.
share this article
Table of Contents
Molybdenum is one of those “unsung heroes” in the world of advanced materials. It’s durable, has a high melting point, and performs beautifully under extreme conditions. When molybdenum is processed into spherical powder, it becomes a vital component for a range of high-tech industries. Whether it’s additive manufacturing, thermal spraying, or powder metallurgy, spherical molybdenum (Mo) powder is a game-changing material.
In this comprehensive guide, we’re going to explore everything you need to know about spherical molybdenum powder—from its composition, properties, and applications, to its specifications, pricing, and market trends. We’ll break down the technical aspects in a simple, conversational style, so even if you’re new to the world of molybdenum powder, you’ll walk away with a clear understanding of its potential.
Overview: What is Spherical Molybdenum (Mo) Powder?
Spherical molybdenum powder is finely ground molybdenum metal shaped into spherical particles, often through processes like gas atomization or plasma spheroidization. This spherical shape offers a range of benefits, from improved flowability to better packing density, making it ideal for applications in 3D printing and thermal spraying.
The spherical form of the powder allows for more consistent layer deposition, improving the efficiency and quality of manufactured parts. Along with molybdenum’s inherent properties—like its high melting point (2,623°C), low thermal expansion, and resistance to corrosion—spherical molybdenum powder is a crucial material in high-temperature and high-performance environments.
Key Benefits of Spherical Molybdenum Powder
- High Melting Point: Molybdenum can withstand extreme heat without melting, making it indispensable in high-temperature applications.
- Low Coefficient of Thermal Expansion: It doesn’t expand much with heat, which is perfect for precision parts that must maintain their dimensions.
- Excellent Flowability: The spherical shape ensures that the powder flows smoothly in additive manufacturing processes like 3D printing.
- Corrosion Resistance: Molybdenum stands up well against corrosion, especially in saltwater and chemical environments.
- High Strength and Toughness: Molybdenum retains its strength even at high temperatures, making it ideal for extreme environments.
Composition, Types, and Properties of Spherical Molybdenum (Mo) Powder
When it comes to spherical molybdenum powder, understanding its composition and properties is essential for selecting the right material for your specific application. Molybdenum powders can vary in their purity, particle size, and alloying elements, all of which influence their performance.
Types and Composition of Spherical Molybdenum Powder
Type of Molybdenum Powder | Composition | Purity Level | Key Properties |
---|---|---|---|
High-Purity Molybdenum Powder | ≥ 99.95% Molybdenum | Ultra-high purity | Ideal for high-temperature applications and electronics |
Alloyed Molybdenum Powder | Molybdenum + Nickel/Copper | 90-95% Molybdenum | Enhanced mechanical properties for structural uses |
Submicron Molybdenum Powder | Molybdenum in submicron sizes | ≥ 99.95% Molybdenum | High surface area, excellent for catalysts and chemical industries |
Each type of spherical molybdenum powder brings its own advantages, making it suitable for specific industrial applications.
Physical and Mechanical Properties of Spherical Molybdenum (Mo) Powder
Property | Value |
---|---|
Density | 10.28 g/cm³ |
Melting Point | 2,623°C (4,753°F) |
Thermal Conductivity | 138 W/m·K (at 20°C) |
Electrical Resistivity | 53 nΩ·m |
Hardness | 5.5 Mohs |
Tensile Strength | 690 MPa |
Coefficient of Thermal Expansion | 4.8 µm/m·K (at 20°C) |
Corrosion Resistance | Excellent in most environments, particularly in chemical and saltwater conditions |
Molybdenum’s unique combination of high melting point, thermal conductivity, and corrosion resistance makes it a standout material for high-performance applications.
Applications of Spherical Molybdenum (Mo) Powder
Spherical molybdenum powder has found its way into a wide range of high-tech applications, from aerospace to medical devices. Its ability to withstand extreme temperatures and tough environments makes it indispensable in industries that demand durability and precision.
Key Applications of Spherical Molybdenum Powder
Industry | Application | Why Molybdenum? |
---|---|---|
Aerospace | High-temperature turbine blades, rocket nozzles | High melting point, resistance to thermal expansion |
Medical | X-ray tubes, high-temperature surgical instruments | Low thermal expansion, biocompatibility |
Defense | Armor plating, missile components | High strength, durability in extreme conditions |
Electronics | Electrical contacts, heat sinks | High conductivity, excellent thermal properties |
Additive Manufacturing | 3D printing of precision metal parts | Excellent flowability, high packing density |
Thermal Spraying | Coatings for wear-resistant surfaces | Resistance to wear, corrosion, and high temperatures |
Example: Molybdenum in Additive Manufacturing
In the world of additive manufacturing, spherical molybdenum powder is a top choice for printing high-performance components. Its high flowability ensures smooth deposition of layers, while its high melting point makes it ideal for parts that need to withstand extreme heat. Think of it like building a house—if you want it to last through hurricanes, storms, and earthquakes, you’d choose the sturdiest materials possible. That’s what molybdenum brings to the table for high-stress 3D printing applications.
Specifications, Sizes, Grades, and Standards for Spherical Molybdenum (Mo) Powder
Choosing the right specifications and grades for spherical molybdenum powder is essential to meet the demands of your application, whether it’s for additive manufacturing, powder metallurgy, or thermal spraying.
Common Specifications and Grades of Spherical Molybdenum Powder
Specification | Value |
---|---|
Purity | 99.95% – 99.99% |
Particle Size | 1 µm – 150 µm |
Flowability | Excellent for additive manufacturing and powder metallurgy |
Packing Density | High due to spherical shape, ideal for high-density applications |
Standards | ASTM B386 (Standard Specification for Molybdenum)**, ISO 9001 (Quality Management Standard) |
Grade | Molybdenum Grade Mo-1, Mo-2 (High-purity molybdenum for aerospace and electronics) |
Available Sizes and Forms
The particle size of spherical molybdenum powder varies based on its intended use. Smaller particle sizes (e.g., submicron powders) are typically used in catalysts and chemical reactions, while larger sizes (e.g., 50–150 µm) are preferred for additive manufacturing and thermal spraying.
Size Range | Application |
---|---|
Submicron (<1 µm) | Catalysts, electronics, chemical applications |
1-10 µm | Powder metallurgy, sintering |
10–50 µm | 3D printing, coatings, thermal spraying |
50–150 µm | Additive manufacturing for larger components |
Standards for Spherical Molybdenum (Mo) Powder
Several standards ensure that spherical molybdenum powder meets the necessary quality requirements for high-performance applications:
- ASTM B386: Specifies requirements for molybdenum used in electronics, aerospace, and other industries.
- ISO 9001: Quality management standard ensuring consistency across manufacturing processes.
- AMS 7847: Aerospace Material Specification for molybdenum used in high-temperature environments.
These standards guarantee that the spherical molybdenum powder you’re getting is up to the challenge, whether you’re building a jet engine or 3D printing precision parts.
Suppliers and Pricing of Spherical Molybdenum (Mo) Powder
Now let’s talk about where you can get spherical molybdenum powder and what it might cost you. Pricing depends on factors such as purity levels, particle size, and processing methods.
Suppliers of Spherical Molybdenum Powder
Supplier | Location | Available Grades | Price per Kg (Approx.) |
---|---|---|---|
Global Tungsten & Powders | USA | High-purity molybdenum powders, submicron powders | $300 – $1,000 |
H.C. Starck Molybdenum | Germany | Aerospace-grade, electronics-grade molybdenum | $350 – $1,200 |
Advanced Refractory Metals | USA | Molybdenum alloys, high-purity powders | $400 – $1,100 |
Stanford Advanced Materials | USA | High-purity molybdenum, molybdenum alloys | $350 – $1,300 |
American Elements | USA | Submicron molybdenum powders | $450 – $1,500 |
Factors Influencing the Price of Spherical Molybdenum Powder
Several factors come into play when determining the price of spherical molybdenum powder:
- Purity: Higher-purity powders (99.95% and above) are more expensive due to the additional refining processes required.
- Particle Size: Submicron powders are typically more costly because of the specialized production techniques involved.
- Processing Method: Techniques like gas atomization or plasma spheroidization can also increase the cost.
- Volume: Bulk purchases often come with discounts, reducing the cost per kilogram.
For example, high-purity molybdenum powders used in electronics and aerospace are often more expensive than powders designed for thermal spraying or powder metallurgy.
Pros and Cons of Spherical Molybdenum (Mo) Powder
As with any material, spherical molybdenum powder has its advantages and limitations. Knowing these will help you decide whether it’s the right material for your specific needs.
Advantages and Limitations of Spherical Molybdenum Powder
Advantages | Limitations |
---|---|
High Melting Point: Ideal for high-temperature applications | Cost: Molybdenum is more expensive than some alternative metals |
Low Thermal Expansion: Great for precision parts | Brittleness: Molybdenum can be brittle compared to ductile metals like copper |
Excellent Flowability: Perfect for 3D printing and powder metallurgy | Processing Complexity: Specialized equipment needed for optimal performance |
Corrosion Resistance: Performs well in harsh environments | Weight: Molybdenum’s density can be a drawback in lightweight applications |
For example, while spherical molybdenum powder is unmatched in high-temperature environments, its cost and brittleness may limit its use in more structural applications.
Spherical Molybdenum (Mo) Powder vs. Other Materials
When choosing a material for your project, it’s important to compare spherical molybdenum powder to other metals and alloys that serve similar purposes, such as tungsten, tantalum, or titanium. Let’s take a look at how molybdenum stacks up against these competitors.
Comparison of Spherical Molybdenum Powder with Other Materials
Material | Key Properties | Cost Comparison | Common Applications |
---|---|---|---|
Molybdenum (Mo) | High melting point, low thermal expansion | Moderate to expensive | Aerospace, electronics, thermal spraying |
Tungsten (W) | Higher density, higher melting point | More expensive than molybdenum | Aerospace, defense, electronics |
Tantalum (Ta) | Superior corrosion resistance, biocompatibility | More expensive than molybdenum | Medical devices, chemical processing, electronics |
Titanium (Ti) | Lightweight, strong, corrosion resistant | Cheaper than molybdenum | Aerospace, medical implants, automotive |
Compared to tungsten, molybdenum is often chosen for applications where weight is a concern, while tungsten is preferred for high-density applications like armor or radiation shielding.
Frequently Asked Questions (FAQ) About Spherical Molybdenum (Mo) Powder
Common Questions About Spherical Molybdenum Powder
Question | Answer |
---|---|
What is spherical molybdenum powder used for? | Spherical molybdenum powder is used in aerospace, medical devices, electronics, and additive manufacturing due to its high-temperature resistance, strength, and low thermal expansion. |
Why is molybdenum good for high-temperature applications? | Molybdenum has a very high melting point of 2,623°C, making it ideal for extreme heat environments like jet engines and thermal coatings. |
Is molybdenum powder expensive? | Molybdenum is more expensive than some common metals, but generally cheaper than tungsten or tantalum. |
Can molybdenum be recycled? | Yes, molybdenum can be recycled, particularly in industries like electronics and manufacturing. |
Is molybdenum safe for medical devices? | Yes, molybdenum is used in various medical applications, including X-ray equipment and surgical instruments, due to its biocompatibility and corrosion resistance. |
How does molybdenum compare to tungsten? | Molybdenum is lighter and has a lower density than tungsten, making it a better choice for applications where weight matters. Tungsten, on the other hand, is better for high-density uses. |
What is the typical particle size for spherical molybdenum powder? | The typical particle size ranges from submicron to 150 µm, depending on the application. |
Conclusion: Is Spherical Molybdenum (Mo) Powder Right for Your Project?
In conclusion, spherical molybdenum powder is a versatile and high-performance material that offers significant advantages for a wide range of applications. Whether you’re working in aerospace, medical devices, electronics, or additive manufacturing, molybdenum’s high melting point, low thermal expansion, and corrosion resistance make it a top contender for high-performance environments.
That said, molybdenum does have its limitations—primarily its cost and brittleness. While it’s excellent for high-temperature and precision applications, it might not be the right choice for applications where ductility or lightweight materials are more critical.
Ultimately, the decision comes down to your specific needs. If your project demands strength, durability, and resistance to extreme conditions, spherical molybdenum powder might just be the material you’ve been looking for.
Get Latest Price
About Met3DP
Product Category
HOT SALE
CONTACT US
Any questions? Send us message now! We’ll serve your request with a whole team after receiving your message.
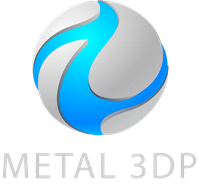
Metal Powders for 3D Printing and Additive Manufacturing