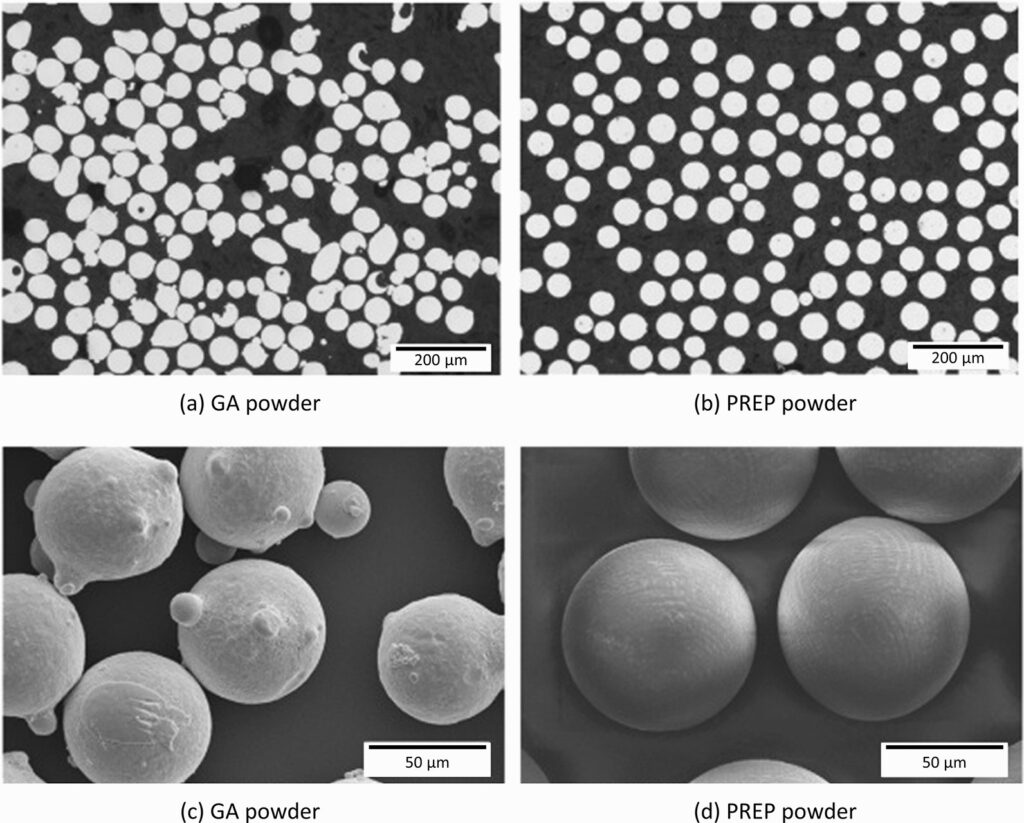
Spherical Tungsten Carbide-Cobalt Powder Explained: Enhance Your Manufacturing Efficiency
Low MOQ
Provide low minimum order quantity to meet different needs.
OEM & ODM
Provide customized products and design services to meet unique customer needs.
Adequate Stock
Ensure fast order processing and provide reliable and efficient service.
Customer Satisfaction
Provide high quality products with customer satisfaction at the core.
share this article
Table of Contents
In the world of advanced materials, spherical tungsten carbide-cobalt powder (WC-Co) stands out as a high-performance material with exceptional hardness, wear resistance, and thermal stability. This material is indispensable in industries like aerospace, automotive, mining, and oil and gas due to its ability to withstand extreme conditions while maintaining its structural integrity. But what exactly is spherical tungsten carbide-cobalt powder? How does it compare to other powders, and what makes it such a crucial material in modern manufacturing?
In this comprehensive guide, we will dive deep into the properties, applications, pricing, pros and cons, and much more about spherical tungsten carbide-cobalt powder. Whether you are a materials engineer, a product designer, or simply a curious reader, this article will provide you with all the information you need.
Overview of Spherical Tungsten Carbide-Cobalt Powder
Spherical tungsten carbide-cobalt powder is a composite material made up of tungsten carbide (WC) and a binder, typically cobalt (Co). The material is created through atomization processes, which result in spherical particles. This spherical shape is particularly important because it enhances the powder’s flowability, making it ideal for additive manufacturing, thermal spraying, and powder metallurgy.
Tungsten carbide is known for its hardness, while cobalt adds ductility and toughness, making the composite highly resistant to wear, corrosion, and high temperatures. This combination of properties makes spherical WC-Co powder a go-to material for cutting tools, wear-resistant coatings, and other high-stress applications.
Key Benefits of Spherical Tungsten Carbide-Cobalt Powder:
- Extreme hardness: Tungsten carbide is among the hardest materials known, ranking close to diamonds on the Mohs scale.
- Wear resistance: The material’s hardness translates to excellent wear resistance, increasing the longevity of components.
- Thermal stability: WC-Co can withstand high temperatures without losing its mechanical properties, making it ideal for extreme environments.
- Flowability: The spherical shape of the powder enhances its flow characteristics, crucial for 3D printing and other powder-based processes.
- Impact toughness: Cobalt adds toughness to the composite, preventing it from becoming brittle under impact or stress.
Types, Composition, and Properties of Spherical Tungsten Carbide-Cobalt Powder
There are several types of spherical tungsten carbide-cobalt powders, each tailored for specific applications. The ratio of tungsten carbide to cobalt can vary, and this ratio directly influences the properties of the powder, such as hardness, toughness, and wear resistance. The most common compositions are WC-6Co, WC-12Co, and WC-17Co, where the percentage indicates the amount of cobalt in the mix.
Here’s a breakdown of the most common types of spherical tungsten carbide-cobalt powders and their key properties:
Type | Composition (Wt%) | Hardness (HRA) | Toughness | Wear Resistance | Applications |
---|---|---|---|---|---|
WC-6Co | WC: 94%, Co: 6% | 91-92 | High | Excellent | Cutting tools, high-stress wear parts |
WC-12Co | WC: 88%, Co: 12% | 89-91 | Higher toughness | Very good | Thermal spray coatings, wear-resistant components |
WC-17Co | WC: 83%, Co: 17% | 87-89 | Excellent | Good | Mining tools, oil and gas drilling equipment |
WC-10Ni | WC: 90%, Ni: 10% | 88-90 | Good | Very good | Corrosion-resistant coatings, specialized tools |
Why Composition Matters:
The balance of tungsten carbide and cobalt significantly impacts the material’s performance. A higher cobalt content (such as in WC-17Co) increases the toughness but slightly reduces the hardness, making it more suitable for impact-prone environments like mining or oil drilling. On the other hand, a lower cobalt content (like WC-6Co) results in higher hardness, ideal for cutting tools where wear resistance is paramount.
Properties and Characteristics of Spherical Tungsten Carbide-Cobalt Powder
When selecting a material for high-performance applications, understanding its physical and mechanical properties is crucial. Below are the typical properties of spherical tungsten carbide-cobalt powder, which make it ideal for a wide range of industries:
Property | Description |
---|---|
Density | 14.5 – 15.1 g/cm³, depending on the cobalt content. |
Hardness | Ranges from 87 to 92 HRA, depending on the WC-Co ratio. |
Melting Temperature | Tungsten carbide has a melting point of approximately 2,870°C (5,198°F). |
Thermal Conductivity | High thermal conductivity, typically around 85-100 W/mK. |
Tensile Strength | Varies with composition, but commonly around 1,500-2,000 MPa. |
Fracture Toughness | Increases with a higher cobalt content, ranging from 8 to 12 MPa·m½. |
Wear Resistance | Exceptional wear resistance due to the hardness of tungsten carbide. |
Corrosion Resistance | Good, but can be enhanced by using nickel instead of cobalt in certain applications. |
Why Hardness and Wear Resistance are Key:
In industries where tools and components are exposed to extreme abrasion, friction, or high temperatures, the wear resistance of spherical tungsten carbide-cobalt powder becomes crucial. The tungsten carbide component provides the necessary hardness to resist wear, while the cobalt binder adds toughness, preventing the material from cracking under stress. This balance ensures longevity and reliability, even in the most challenging environments.
Applications of Spherical Tungsten Carbide-Cobalt Powder
Spherical tungsten carbide-cobalt powder is highly versatile and finds applications in various industries that demand materials with exceptional hardness, wear resistance, and toughness. Let’s explore where this material is most commonly used:
Industry | Applications |
---|---|
Aerospace | High-performance turbine blades, wear-resistant components |
Automotive | Cutting tools, wear-resistant coatings for engine parts |
Mining | Drill bits, cutting tools, and wear-resistant components for mining equipment |
Oil and Gas | Valves, seals, and drilling tools exposed to extreme wear |
Thermal Spraying | Coatings for high-temperature and wear-resistant applications |
Additive Manufacturing | 3D-printed components requiring high hardness and toughness |
Why the Mining Industry Relies on WC-Co:
In the mining industry, tools and components are constantly exposed to harsh conditions, including abrasive materials and high-impact environments. Spherical tungsten carbide-cobalt powder is commonly used to manufacture drill bits and cutting tools that can withstand this level of stress without frequent replacement, reducing downtime and increasing operational efficiency.
Specifications, Sizes, and Standards for Spherical Tungsten Carbide-Cobalt Powder
When selecting spherical tungsten carbide-cobalt powder, it’s important to consider the specifications related to particle size, purity, and standards. Here’s a table outlining some of the most important specifications to keep in mind when sourcing this material:
Specification | Details |
---|---|
Particle Size Range | Common sizes range from 5-45 μm for additive manufacturing and 15-75 μm for thermal spraying. |
Purity | Typically, powders have a tungsten carbide purity of 99.5% or higher. |
Grades | Common grades include WC-6Co, WC-12Co, and WC-17Co. |
Standards | ISO 4499-2 (standards for tungsten carbide materials), ASTM B777 (density standards), and ISO 9001 (quality management for manufacturing). |
Packaging | Available in 1kg, 5kg, 10kg, and 25kg containers, with bulk orders available upon request. |
Why Particle Size Matters:
The particle size of spherical tungsten carbide-cobalt powder is particularly important in applications like additive manufacturing and thermal spraying. Finer particles (5-45 μm) are ideal for 3D printing, where they provide a smooth surface finish and high resolution. Coarser particles (15-75 μm) are better suited for thermal spray coatings, where thicker and more durable layers are required.
Suppliers and Pricing Details for Spherical Tungsten Carbide-Cobalt Powder
Pricing for spherical tungsten carbide-cobalt powders can vary significantly depending on the composition, particle size, and supplier. Below is a table listing some of the leading suppliers and their pricing for different types of WC-Co powder:
Supplier | Product Description | Price (USD) | Comments |
---|---|---|---|
Kennametal | WC-12Co, 15-45 μm, spherical powder | $150 – $200 per kg | High-performance powder for thermal spray applications. |
HC Starck | WC-6Co, 5-45 μm, spherical powder | $180 – $220 per kg | Ideal for additive manufacturing and wear-resistant parts. |
Oerlikon Metco | WC-17Co, 15-75 μm, spherical powder | $160 – $210 per kg | Suitable for wear-resistant coatings in mining and oil drilling tools. |
Global Tungsten & Powders | WC-10Ni, 5-45 μm, spherical powder | $190 – $230 per kg | Nickel-bonded powder for corrosion-resistant coatings. |
Tekna | WC-12Co, 5-45 μm, spherical powder | $170 – $220 per kg | High-purity powder for advanced additive manufacturing. |
Why Pricing Varies:
Several factors influence the pricing of spherical tungsten carbide-cobalt powder:
- Composition: Powders with higher tungsten carbide content or specialty alloys (like WC-Ni) tend to be more expensive due to the cost of raw materials.
- Particle Size: Finer powders are generally more expensive because they require more precise manufacturing processes.
- Supplier: Established suppliers with advanced quality control systems may charge a premium for guaranteed consistency and performance.
Advantages and Limitations of Spherical Tungsten Carbide-Cobalt Powder
While spherical tungsten carbide-cobalt powder offers numerous benefits, it’s essential to understand both its advantages and limitations to determine if it’s the right material for your application. Here’s a comparison of the pros and cons:
Advantages | Limitations |
---|---|
Exceptional hardness: Provides excellent wear resistance for long-lasting parts | High cost: WC-Co powders are generally more expensive than other metal powders due to the cost of raw materials |
Thermal stability: Maintains mechanical properties at high temperatures | Limited corrosion resistance: Cobalt can be prone to corrosion in certain environments, though nickel-bonded alternatives exist |
Toughness: Cobalt binder prevents brittleness under stress | Difficult to machine: Tungsten carbide is extremely hard, making post-processing more challenging |
Versatile applications: Suitable for a wide range of industries, from aerospace to mining | Heavy material: Despite being extremely strong, WC-Co is also quite dense, which may not be suitable for all lightweight applications |
Is WC-Co Worth the Investment?:
For industries where wear resistance and toughness are critical, the higher cost of spherical tungsten carbide-cobalt powder is often justified by its long-term durability and performance. However, for applications where cost is a major constraint, alternatives like steel or ceramics might be more appropriate, though they won’t offer the same level of durability.
FAQs About Spherical Tungsten Carbide-Cobalt Powder
Question | Answer |
---|---|
What industries benefit the most from WC-Co powder? | Aerospace, automotive, mining, oil and gas, and additive manufacturing industries benefit the most due to the material’s hardness, toughness, and wear resistance. |
Why is the spherical shape important in tungsten carbide-cobalt powders? | Spherical particles offer better flowability, higher packing density, and enhanced performance in powder-based manufacturing processes like 3D printing. |
What is the difference between WC-6Co and WC-17Co powders? | WC-6Co has higher hardness and is better suited for cutting tools, while WC-17Co offers higher toughness and is ideal for impact-resistant applications like mining tools. |
Can spherical tungsten carbide-cobalt powder be used in high-temperature environments? | Yes, WC-Co powders can withstand high temperatures without losing their mechanical properties, making them suitable for thermal spraying and high-temperature coatings. |
How does WC-Co powder compare to steel or ceramic powders? | WC-Co powders offer superior hardness and wear resistance compared to steel, but at a higher cost. Ceramics may offer similar hardness but lack the toughness of WC-Co, making them more brittle. |
Conclusion: Why Spherical Tungsten Carbide-Cobalt Powder is Critical for High-Performance Applications
In conclusion, spherical tungsten carbide-cobalt powder is a high-performance material that excels in applications requiring hardness, wear resistance, and toughness. Its widespread use across industries like mining, aerospace, and automotive is a testament to its durability, especially in extreme environments where lesser materials would fail.
While the cost of WC-Co powder may be higher than other materials, its long-term durability often makes it a more cost-effective option in the long run. If you’re working in a field where performance, longevity, and reliability are non-negotiable, spherical tungsten carbide-cobalt powder is a material worth considering.
Are you ready to explore how spherical tungsten carbide-cobalt powder can enhance your manufacturing process? Reach out to suppliers, compare compositions, and find the right grade to meet your specific needs.
Get Latest Price
About Met3DP
Product Category
HOT SALE
CONTACT US
Any questions? Send us message now! We’ll serve your request with a whole team after receiving your message.
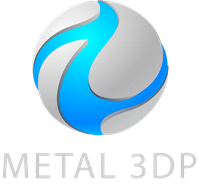
Metal Powders for 3D Printing and Additive Manufacturing