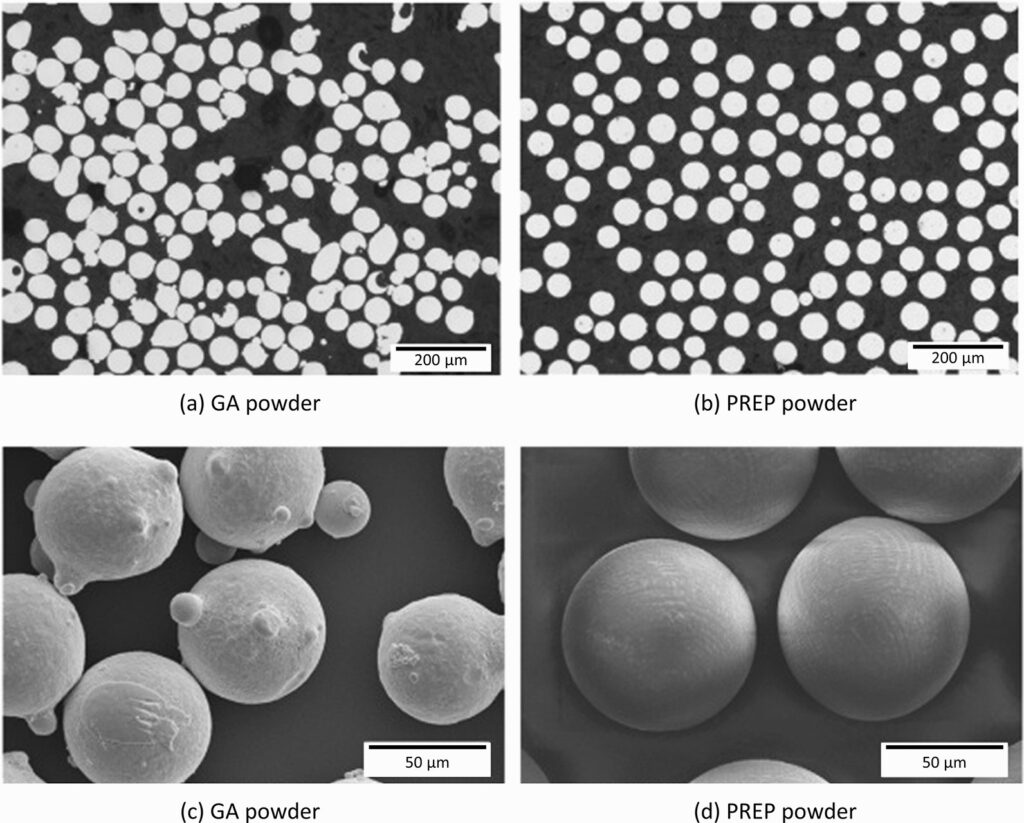
Why Stellite 12 Powder is the Best Choice for Tough Conditions
Low MOQ
Provide low minimum order quantity to meet different needs.
OEM & ODM
Provide customized products and design services to meet unique customer needs.
Adequate Stock
Ensure fast order processing and provide reliable and efficient service.
Customer Satisfaction
Provide high quality products with customer satisfaction at the core.
share this article
Table of Contents
When it comes to high-performance materials that can withstand extreme wear and tear, Stellite 12 powder is a top contender. This cobalt-based alloy is renowned for its exceptional wear resistance, even under high-temperature environments. It’s one of those rare materials that can take a beating in the most demanding conditions—whether it’s in aerospace, oil and gas, or power generation. But what exactly is it about Stellite 12 powder that makes it so special?
In this comprehensive guide, we will explore everything you need to know about Stellite 12 powder—its composition, properties, applications, and much more. Whether you’re an engineer, manufacturer, or simply someone interested in high-performance alloys, this guide will provide you with all the essential details.
Overview: What is Stellite 12 Powder?
Stellite 12 powder is a cobalt-chromium alloy that offers outstanding wear resistance and high-temperature performance. It is designed to perform in highly abrasive environments where other materials would fail. The alloy’s unique composition of cobalt, chromium, tungsten, and carbon results in an extremely hard material that retains its hardness even at elevated temperatures.
Unlike softer alloys, Stellite 12 is used in applications where wear, corrosion, and high temperature are critical factors. From cutting tools to valve seats and bearings, Stellite 12 powder is the go-to material for industries that demand the best in performance and reliability.
Key Features
- Superior wear resistance in both metal-to-metal and abrasive wear environments.
- High hardness and retained strength even at elevated temperatures, up to 650°C.
- Corrosion resistance in harsh environments, including both oxidizing and reducing atmospheres.
- Galling resistance, making it ideal for applications involving sliding contact between metals.
Composition and Properties
The performance of Stellite 12 powder comes down to its carefully balanced composition. Each element in the alloy plays a crucial role in enhancing specific properties, from wear resistance to corrosion protection.
Composition
Element | Percentage (%) | Role in the Alloy |
---|---|---|
Cobalt (Co) | 50-60% | The primary base of the alloy, providing strength, wear resistance, and temperature stability. |
Chromium (Cr) | 28-32% | Enhances corrosion resistance and hardness, particularly in high-temperature environments. |
Tungsten (W) | 7-10% | Increases wear resistance, particularly at elevated temperatures, and contributes to the formation of hard carbides. |
Carbon (C) | 1.8-2.5% | Forms carbides that significantly enhance hardness and wear resistance. |
Nickel (Ni) | ≤ 3% | Sometimes included to improve toughness and ductility. |
Silicon (Si) | ≤ 2% | Improves oxidation resistance at high temperatures. |
Key Properties
Property | Value/Description |
---|---|
Density | ~8.7 g/cm³ |
Melting Point | ~1,260°C |
Hardness | 45-50 HRC (Rockwell Hardness) |
Wear Resistance | Extremely high in abrasive and metal-to-metal wear conditions, especially at high temperatures. |
Corrosion Resistance | Excellent, particularly in oxidizing and reducing environments. |
Thermal Stability | Retains hardness and wear resistance up to 650°C, making it ideal for high-temperature applications. |
Oxidation Resistance | High resistance to oxidation, making it suitable for components exposed to air at high temperatures. |
Why Choose Stellite 12 Powder? Key Characteristics
So, why is Stellite 12 powder such a popular choice for industrial applications? Let’s take a deeper dive into its unique characteristics and why it outperforms many other options on the market.
1. Extreme Wear Resistance
At the heart of Stellite 12 powder’s appeal is its wear resistance. It’s not just resistant to wear—it thrives on it. Thanks to the high carbon and tungsten content, the material forms hard carbides that enhance its ability to withstand abrasion and metal-to-metal wear. This makes it particularly useful in applications like cutting tools, valves, and bearings where constant wear is a concern.
2. High-Temperature Performance
Stellite 12 powder is designed for environments where heat is a constant factor. Whether you’re dealing with high-speed cutting or high-pressure valves, this alloy maintains its hardness and strength even at temperatures up to 650°C. This makes it an excellent choice for industries like aerospace and power generation, where components are subjected to extreme heat.
3. Corrosion Resistance
In addition to its wear resistance, Stellite 12 powder also offers impressive corrosion resistance. The high chromium content in the alloy provides protection against oxidation and corrosive environments. Whether you’re dealing with oil and gas or chemical processing, Stellite 12 can withstand exposure to harsh chemicals and extreme conditions.
4. Galling and Seizing Resistance
In applications where parts are in constant contact, galling and seizing can be a significant issue. Stellite 12 powder excels in these situations thanks to its natural resistance to galling. This makes it ideal for valve seats, bearings, and sliding wear components, where friction can cause problems.
5. Versatile Application
One of the great things about Stellite 12 powder is its versatility. It can be used in a variety of manufacturing processes, including thermal spraying, welding, and powder metallurgy. This versatility makes it easy to integrate into different industries and applications, from aerospace to medical devices.
Applications
Given its impressive properties, Stellite 12 powder is used in a wide range of high-performance applications. Below is a table that outlines the main industries and applications where Stellite 12 shines.
Industry | Application |
---|---|
Aerospace | Turbine blades, jet engine components, exhaust valves, and other high-temperature, high-wear parts. |
Oil & Gas | Valve seats, drilling tools, and other components exposed to high temperatures and corrosive environments. |
Automotive | High-performance engine components, exhaust valves, and parts that experience high friction and wear. |
Power Generation | Steam turbine blades, furnace linings, and other high-temperature components. |
Marine | Propellers, pumps, and other components exposed to saltwater and corrosive environments. |
Medical | Surgical tools and implants that require both wear and corrosion resistance. |
Industrial Tooling | Cutting tools, dies, punches, and other wear-resistant equipment used in manufacturing and machining processes. |
Chemical Processing | Pump impellers, valves, and other parts exposed to corrosive chemicals and abrasive particles in reactors and piping systems. |
As you can see, Stellite 12 powder is widely used in industries that demand durability, wear resistance, and high-temperature performance.
Specifications, Sizes, Grades, and Standards
When selecting Stellite 12 powder for your project, it’s essential to understand the different specifications, sizes, and grades available. These factors can influence the performance of the material in various applications.
Specification | Details |
---|---|
Particle Size | Typically ranges from 15 to 53 microns, making it ideal for powder metallurgy and thermal spraying. |
ASTM Standards | ASTM F75 for medical applications, ASTM B815 for wear-resistant coatings. |
ISO Standards | ISO 5832-4 for medical-grade cobalt-chromium alloys. |
UNS Number | UNS R30012 for Stellite 12. |
Hardness Range | 45-50 HRC, depending on heat treatment and specific application requirements. |
Powder Morphology | Spherical powder is most common and best suited for additive manufacturing and thermal spray processes. |
These specifications ensure that Stellite 12 powder meets the rigorous standards required for industries like medical devices, aerospace, and industrial tooling.
Suppliers and Pricing
The cost of Stellite 12 powder can vary based on factors such as order size, the supplier, and the specific formulation. Below is a list of some of the most well-known suppliers and their typical pricing ranges for Stellite 12 powder.
Supplier | Price Range (per kg) | Notes |
---|---|---|
Kennametal | $200 – $300 | A leading supplier of Stellite alloys, including Stellite 12 powder for wear-resistant applications. |
Oerlikon Metco | $220 – $320 | Offers high-quality Stellite powders for thermal spraying and additive manufacturing. |
Carpenter Technology | $210 – $310 | Known for producing cobalt-based alloys, including Stellite 12 for aerospace and industrial applications. |
Höganäs AB | $230 – $340 | Specializes in powder metallurgy and offers Stellite 12 powder for various industries. |
Powder Alloy Corporation | $240 – $330 | Supplies a wide range of metal powders, including Stellite 12 for high-temperature and wear applications. |
The price of Stellite 12 powder can fluctuate depending on market conditions and the specific requirements of your project. Custom formulations or specialized specifications may also result in higher costs.
Advantages and Limitations
While Stellite 12 powder offers numerous advantages, there are also some limitations to consider. Let’s take a closer look at the pros and cons of using Stellite 12 powder in various applications.
Advantages
Advantage | Why It Matters |
---|---|
Superior Wear Resistance: High tungsten and carbon content provide excellent wear resistance. | Ideal for applications like cutting tools, turbine blades, and valve seats that experience extreme wear. |
High-Temperature Performance: Stellite 12 maintains its hardness and strength at elevated temperatures. | Perfect for use in high-heat environments such as jet engines, exhaust valves, and power generation turbines. |
Corrosion Resistance: Chromium provides excellent corrosion protection in harsh environments. | Suitable for marine, chemical processing, and oil & gas applications where corrosion is a concern. |
Galling Resistance: Designed to resist galling and seizing in metal-to-metal wear applications. | Great for parts like valve seats and bearings. |
Versatile Manufacturing: Can be used in various manufacturing processes, including 3D printing. | Offers flexibility in production, making it ideal for a wide range of industries. |
Limitations
Limitation | Why It’s a Challenge |
---|---|
Cost: Stellite 12 powder is more expensive than other wear-resistant materials. | May not be cost-effective for less demanding applications. |
Difficult Machinability: The hardness of Stellite 12 can make it challenging to machine or process. | Requires specialized tools and techniques, leading to increased production time and costs. |
Weight: Stellite 12 is heavier than lighter alloys like aluminum or titanium. | May not be suitable for applications where minimizing weight is critical, such as aerospace components. |
Limited Ductility: Stellite 12 is less ductile compared to other materials, making it harder to form or bend. | May not be the best choice for applications that require a lot of flexibility or deformation. |
FAQs About Stellite 12 Powder
Here are some frequently asked questions about Stellite 12 powder, along with detailed answers to help you better understand this remarkable material.
Question | Answer |
---|---|
What is Stellite 12 powder used for? | Stellite 12 powder is used in industries like aerospace, oil & gas, automotive, and power generation for high-temperature, wear-resistant, and corrosion-resistant components. |
How much does Stellite 12 powder cost? | Prices typically range from $200 to $340 per kilogram, depending on the supplier and specific application. |
Is Stellite 12 powder biocompatible? | Yes, Stellite 12 powder is biocompatible, making it suitable for medical implants and surgical tools. |
What makes Stellite 12 powder corrosion-resistant? | The high chromium content in Stellite 12 powder provides excellent resistance to corrosion in harsh environments, including oxidizing and reducing atmospheres. |
Can Stellite 12 powder be used in 3D printing? | Yes, Stellite 12 powder is commonly used in additive manufacturing processes like powder-bed fusion for creating complex, high-performance parts. |
What industries use Stellite 12 powder? | Stellite 12 powder is used in industries such as aerospace, oil & gas, automotive, power generation, marine, and chemical processing. |
How does Stellite 12 powder compare to other alloys? | Compared to other cobalt-based alloys like Stellite 6, Stellite 12 offers better wear resistance at the expense of slightly higher brittleness. |
Is Stellite 12 powder magnetic? | No, Stellite 12 powder is generally non-magnetic, making it suitable for sensitive environments like medical devices and electronic equipment. |
Conclusion: Is Stellite 12 Powder Right for Your Project?
Stellite 12 powder is a high-performance material that offers superior wear resistance, temperature stability, and corrosion resistance across a wide range of industries. Whether you’re working in aerospace, oil & gas, or medical devices, Stellite 12 powder delivers the durability and reliability required for the most demanding applications.
While it may come with some challenges—such as higher costs and difficult machinability—Stellite 12 powder remains a top choice for those who need a material that can withstand extreme conditions. Its versatility in manufacturing processes like thermal spraying, welding, and 3D printing makes it suitable for a wide range of high-performance applications.
In the end, if you’re looking for a material that can take on the toughest environments and come out on top, Stellite 12 powder might just be the perfect fit for your next project!
Get Latest Price
About Met3DP
Product Category
HOT SALE
CONTACT US
Any questions? Send us message now! We’ll serve your request with a whole team after receiving your message.
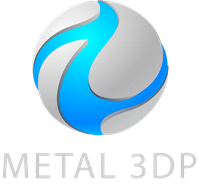
Metal Powders for 3D Printing and Additive Manufacturing