Titanium Molybdenum Alloy Powders
Table of Contents
titanium molybdenum alloy powders enhance high-temperature strength and creep resistance for lightweight aerospace designs. This guide reviews TiMo alloy powder compositions, key characteristics, production methods, suitable applications, specifications, purchasing considerations, supplier comparisons, and pros/cons.
titanium molybdenum alloy powders Typical Composition
Alloy Grade | Titanium (%) | Molybdenum (%) |
---|---|---|
Ti-6Al-7Nb (IMI 550) | Balance | 7% |
Ti-15Mo-3Nb-3Al-0.2Si | Balance | 15% |
Ti-11.5Mo-6Zr-4.5Sn (Ti-11) | Balance | 11.5% |
Ti-15Mo-5Zr-3Al | Balance | 15% |
Molybdenum levels between 7% and 15% effective for high-temperature strengthening. Other elements like niobium, zirconium, and tin further boost creep properties.
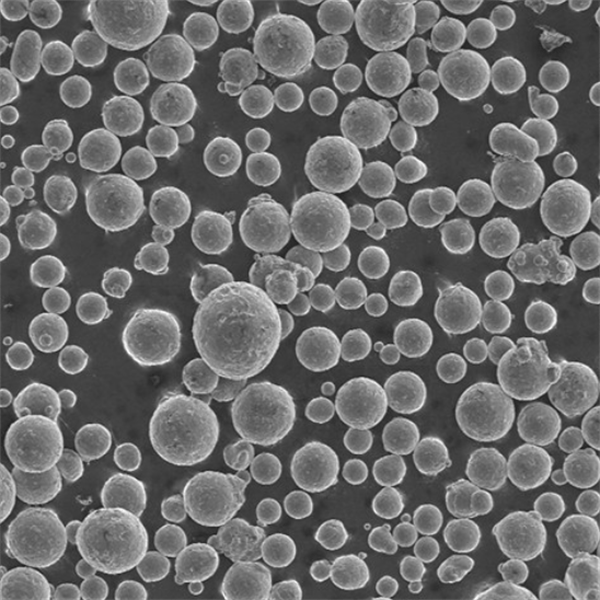
Characteristics and Properties
Attribute | Details |
---|---|
Particle shape | Spherical from inert gas atomization |
Oxygen ppm | Below 500 ppm |
Typical density | 4.5 g/cc |
Thermal conductivity | 4-6 W/mK |
High temperature strength | 100 MPa at 500°C |
Corrosion resistance | Forms protective TiO2 film |
Particulate nature, low oxygen content and tailored compositions suit alloy powder for additive manufacturing or sintering high performance components.
Production Methods
Method | Process Description |
---|---|
Gas atomization | Inert gas disintegrates molten alloy stream into powder |
Plasma atomization | Very clean but lower powder output vs gas atomization |
PREP | Spheroidization of existing powders by remelting |
Hydride-dehydride | Brittle TiH2 intermediate for comminution |
Plasma and gas atomization offer the best quality while being more expensive vs secondary routes like PREP and HDH.
Applications of TiMo Alloy Powder
Industry | Component Examples |
---|---|
Aerospace | Turbine blades, casings, landing gears |
Power generation | Heat exchangers, steam piping |
Chemical processing | Bioreactors, reaction vessels |
Marine | Propeller shafts, sonar domes |
Oil and gas drilling | Geothermal well tools and shafts |
Combination of high strength, low weight and corrosion resistance suits TiMo alloys with demanding environments like aircraft engines or offshore drilling.
Specifications
Standard | Grades Covered |
---|---|
ASTM B862 | Ti-6Al-2Sn-4Zr-6Mo, Ti-8Al-1Mo-1V, Ti-6Al-2Nb-1Ta-0.8Mo |
ASTM B348 | Titanium and titanium alloy bars and billets |
AIMS 04-18 | Standard for AM titanium parts |
AMPM (American Powder Metallurgy) Institute, IPS (International Powder Metallurgy Standards Organization) also cover various Ti grades.
Global Suppliers and Price Range
Company | Lead Time | Pricing |
---|---|---|
TLS Technik | 16 weeks | $300 – $900/kg |
Sandvik | 12 weeks | $350 – $1000/kg |
Atlantic Equipment | 14 weeks | $320 – $850/kg |
Pricing for 100+ kg batch. Premium for low oxygen and spherical powder. Larger quantities above 500 kg offer 20%+ discounts.
Pros vs Cons
Advantages | Challenges |
---|---|
Excellent high temperature strength | High raw material costs |
Corrosion resistant in many environments | Longer lead times for custom alloys |
Custom alloy design flexibility | Limited global supply chain presently |
Compatible with powder AM methods | Post-processing often needed after AM |
Excellent creep resistance | Stringent requirements on oxygen/nitrogen |
TiMo powders enable new component designs and lightweight construction but using titanium alloys poses unique powder manufacturing and handling challenges.
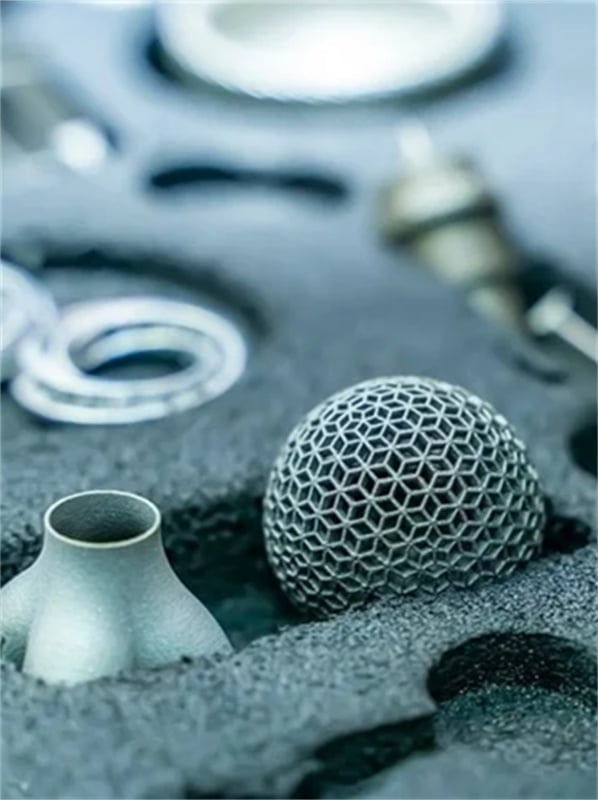
FAQ
What particle size range is optimal for binder jet 3D printing?
Around 30 to 50 microns facilitates higher powder bed density and efficient liquid saturation needed to bind layers properly. Too fine powders hurt performance.
What causes contamination during Ti alloy gas atomization?
Oxygen pickup from any air leaks degrades powder purity hence the need for stringent process controls. Furnace parting agents and melt crucibles are other contamination sources requiring high purity consumables.
Why is high Mo content difficult to achieve in Ti based alloys?
Excessive evaporation losses of molybdenum occur above 25% levels during vacuum induction melting and subsequent remelting steps. Mitigation measures include covering melt pools or using cold crucible techniques.
How should titanium powder be stored?
Inside sealed containers under inert cover gas or vacuum. Handled and stored to exclude moisture absorption which causes decrepitation and high osyggen or nitrogen impurity.
What are common defects when AM printing titanium alloys?
Porosity from trapped gas atoms, lack of fusion defects, residual stress cracking, unfused powder trapped inside enclosed volumes. Require integrated parameters optimisation accounting for scan strategy, energy input etc.
Conclusion
In summary, titanium molybdenum alloy powders provide customized high temperature properties and corrosion resistance vital for producing next generation components across aerospace, energy and other demanding industries via powder metallurgy or additive manufacturing.
Share On
MET3DP Technology Co., LTD is a leading provider of additive manufacturing solutions headquartered in Qingdao, China. Our company specializes in 3D printing equipment and high-performance metal powders for industrial applications.
Inquiry to get best price and customized Solution for your business!
Related Articles
About Met3DP
Recent Update
Our Product
CONTACT US
Any questions? Send us message now! We’ll serve your request with a whole team after receiving your message.
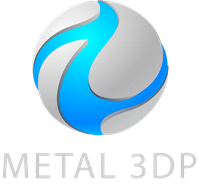
Metal Powders for 3D Printing and Additive Manufacturing