Titanium Nitride Powder
Table of Contents
Titanium nitride (TiN) powder is an extremely hard ceramic material with unique properties that make it suitable for use across various industries. This article provides an overview of titanium nitride powder, including its composition, key characteristics, manufacturing process, and applications.
Overview of Titanium Nitride Powder
Titanium nitride or TiN is a golden-yellow ceramic compound made up of titanium and nitrogen atoms. Its chemical formula is TiN.
Some key features of titanium nitride powder include:
- Extreme hardness – nearly as hard as diamond
- Excellent wear and corrosion resistance
- High thermal stability
- Metallic gold color
- Electrically conductive
- Biocompatible and non-toxic
Its unique combination of properties has resulted in TiN powder being utilized for surface coating applications across tools, automotive components, turbines, and medical implants among others.
The following sections provide more details on the composition, characteristics, production, and uses of titanium nitride powder.
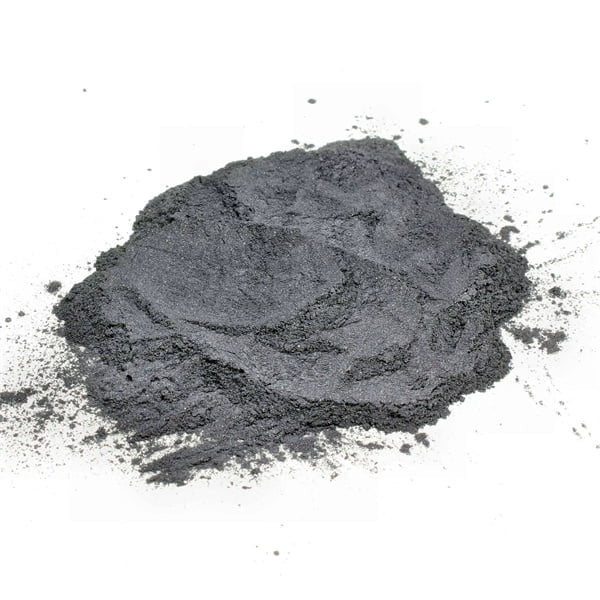
Composition and Characteristics of Titanium Nitride Powder
Property | Description | Units |
---|---|---|
Chemical Formula | TiN | |
Chemical Composition (Typical) | – Titanium (Ti): Min. 77.0 wt%<br> – Nitrogen (N): Min. 20.0 wt%<br> – Carbon (C): Max. 0.1 wt% | wt% |
Crystal Structure | NaCl-type face-centered cubic | |
Particle Size | Varies depending on application<br> – Micronized powders: < 10 microns<br> – Submicron powders: < 1 micron<br> – Nanopowders: < 100 nanometers | microns, nanometers |
Appearance | Gold-colored | |
Melting Point | ~2930°C | °C |
Density | 5.22 – 5.44 g/cm³ | g/cm³ |
Hardness | Vickers hardness: 1800-2100 HV<br> Mohs hardness: 8-9 | HV |
Modulus of Elasticity | 550 ± 50 GPa | GPa |
Thermal Expansion Coefficient | 9.35 × 10⁻⁶ K⁻¹ | K⁻¹ |
Electrical Conductivity | Metallic conductor (conductivity varies with stoichiometry and impurities) | S/m |
Thermal Conductivity | High (15-30 W/mK) | W/mK |
Superconducting Transition Temperature | Up to 6.0 K (single crystals) | K |
Chemical Stability | Excellent resistance to most chemicals at room temperature<br> Reacts with oxygen at high temperatures (> 800°C) | |
Biocompatibility | Generally considered biocompatible |
Manufacturing Process of Titanium Nitride Powder
Process | Description | Advantages | Disadvantages |
---|---|---|---|
Nitridation | This is the most widely used method for producing titanium nitride powder. It involves reacting titanium feedstock with nitrogen gas or ammonia at high temperatures (typically above 900°C). The reaction can be carried out in various reactor configurations, including fluidized beds, rotating reactors, and plasma reactors. | – Established and reliable technology – Produces high-purity TiN powder – Offers good control over powder morphology | – Requires high temperatures, leading to increased energy consumption – Particle size and size distribution can be difficult to control at high temperatures – Potential for oxygen contamination if not carefully controlled |
Carbothermal Reduction | This method involves heating a mixture of titanium dioxide (TiO2), carbon (graphite or charcoal), and nitrogen gas to high temperatures (around 1300°C). The carbon acts as a reducing agent, converting the titanium dioxide to titanium nitride. | – Offers a potentially lower cost alternative to nitridation – Can be used to produce titanium nitride with specific carbonitride compositions | – More complex reaction chemistry compared to nitridation – Strict control over the starting material ratio and reaction conditions is crucial to achieve desired product purity – May require additional post-processing steps to remove impurities |
Reactive Ball Milling | This is a high-energy mechanochemical process where titanium powder and a nitrogen source (often urea) are milled together in a high-energy ball mill. The mechanical force from the milling balls fractures the particles and promotes the solid-state reaction between titanium and nitrogen, forming titanium nitride at relatively low temperatures (around room temperature). | – Suitable for producing nano-sized titanium nitride powder – Lower energy consumption compared to high-temperature methods – Can be a scalable process | – Relatively new technology with ongoing research and development – May introduce contamination from the milling media – Achieving uniform particle size distribution can be challenging |
Chemical Vapor Deposition (CVD) | This method involves introducing precursor gases containing titanium and nitrogen into a heated reaction chamber. The precursor gases decompose and react to form titanium nitride particles, which are then deposited on a substrate or collected as powder. | – Highly versatile method capable of producing powders with tailored properties – Enables precise control over particle size and morphology | – Complex and expensive process equipment required – Limited production capacity compared to other methods – Safety considerations due to the use of potentially hazardous precursor gases |
Physical Vapor Deposition (PVD) | Similar to CVD, PVD involves vaporizing titanium in a vacuum environment and reacting it with nitrogen gas. The vaporized titanium can be generated using various techniques such as sputtering, cathodic arc deposition, or electron beam evaporation. | – Suitable for producing high-purity and well-defined titanium nitride thin films or powders – Offers good control over film thickness and composition | – Highly specialized and expensive equipment – Limited production rate for powder production – Line-of-sight deposition, making it unsuitable for complex geometries |
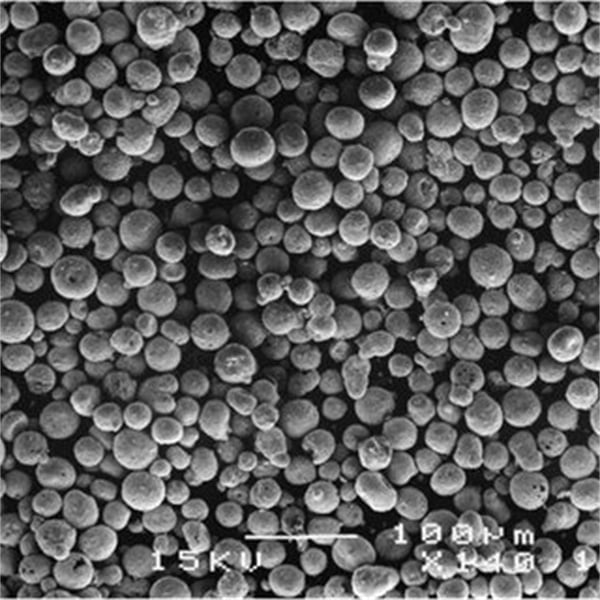
Applications and Uses of Titanium Nitride Powder
Category | Application | Properties Leveraged | Details |
---|---|---|---|
Cutting Tools | Drill bits, milling cutters, end mills | High hardness, wear resistance, low friction coefficient | Titanium nitride (TiN) powder is a popular choice for coating cutting tools due to its exceptional hardness, which extends tool life by up to three times compared to uncoated tools. The low friction coefficient of TiN coatings reduces friction between the tool and workpiece, minimizing heat generation and improving cutting efficiency. Additionally, TiN’s wear resistance prevents chipping and degradation of the cutting edge, maintaining sharp cuts for longer. |
Medical Devices | Scalpel blades, bone saws, orthopedic implants | Biocompatibility, wear resistance, sharpness | In the medical field, TiN powder finds application in coating surgical instruments like scalpels and bone saws. Its biocompatible nature makes it safe for implantation within the body. Furthermore, the wear resistance of TiN coatings ensures that these instruments retain their sharpness during procedures, leading to cleaner cuts and improved patient outcomes. TiN is also used to coat some orthopedic implants, such as hip replacements, due to its ability to enhance wear resistance and reduce friction at the implant-bone interface, promoting long-term implant stability. |
Decorative Coatings | Costume jewelry, automotive trim | Attractive golden color, high durability | Beyond its functional applications, TiN powder is valued for its aesthetic properties. The metallic gold color of TiN coatings makes them ideal for decorative purposes in costume jewelry and automotive trim. Unlike real gold plating, TiN offers superior durability and scratch resistance, maintaining its shine for extended periods. This combination of aesthetics and functionality makes TiN powder an attractive choice for manufacturers seeking a balance between style and longevity. |
Consumer Goods | Plumbing fixtures, doorknobs | Corrosion resistance, wear resistance, aesthetic appeal | The beneficial properties of TiN extend to everyday consumer goods. A common application is in the coating of plumbing fixtures and doorknobs. The corrosion resistance of TiN protects these items from tarnishing and wear, particularly in areas exposed to moisture. Additionally, the wear resistance of TiN coatings prevents scratches and maintains the smooth operation of faucets and door handles. In some cases, a top layer of TiN is used over a nickel or chromium base coat, providing a combination of durability, corrosion resistance, and a touch of golden elegance. |
Semiconductors | Diffusion barriers, electrical conductors | High thermal stability, good electrical conductivity | Within the realm of semiconductors, TiN powder plays a crucial role in the fabrication process. Thin films of TiN are deposited onto silicon wafers to act as diffusion barriers, preventing unwanted elements from migrating through the layers and disrupting the electrical properties of the device. TiN also exhibits good electrical conductivity, making it suitable for use as electrical contacts within integrated circuits. |
Emerging Applications | Solar cells, architectural coatings | Broad spectrum of properties | Research and development efforts are exploring new applications for TiN powder. In the field of solar energy, TiN coatings are being investigated for their potential to improve the efficiency of solar cells. The ability of TiN to absorb certain wavelengths of light while reflecting others could lead to the development of more efficient light-harvesting devices. Additionally, TiN’s combination of properties, including hardness, corrosion resistance, and a self-lubricating effect, makes it a promising candidate for architectural coatings on buildings. These coatings could offer protection against harsh weather conditions, improve self-cleaning properties, and potentially enhance the aesthetic appeal of structures. |
Specifications of Titanium Nitride Powder
Titanium nitride powder products are available in different purity levels, particle size distribution, morphologies, and can be customized as per application requirements.
Some important TiN powder specifications:
Specification | Details |
---|---|
Purity | 99% titanium nitride content minimum for most applications. Also lower purities ~92%-95% for non-critical uses. |
Particle shape morphology | Varied from spherical, agglomerated to angular |
Particle size (d50) distribution | Range from nano-scale 30-50 nm to micron grade 2-5 μm for tools/components coatings. Sub-micron grade ~0.5 μm also common. |
Specific surface area (SSA) | From low 5 m2/g for micron grades to 15-30 m2/g for nano powder |
Color | Metallic bright gold |
Melting point | 2950°C |
Mohs hardness | 8.5 |
Crystal structure | Cubic – NaCl type |
Density | 5.22 g/cm3 |
Oxygen/carbon content | Under 1% oxygen content is important for high purity |
Table 1: Titanium nitride specifications summary
These powder specifications can be varied as per target industry applications during custom manufacturing.
Global Suppliers and Pricing
Region | Major Suppliers | Product | Price (USD/kg) | Key Considerations |
---|---|---|---|---|
North America | American Elements, US Titanium Mills, Nanoventure | Micronized TiN (>1 micron) | 100-200 | Offers good balance between cost and performance for wear-resistant coatings |
Alfa Aesar, ATI Specialty Materials | Nanometerized TiN (<100 nm) | 400-800 | High surface area ideal for electronics and catalysis applications | |
Praxair Surface Technologies | Feedstock for CVD (Chemical Vapor Deposition) | Price upon request | Consistent quality and particle size crucial for thin film coatings | |
Europe | H.C. Starck, Sandvik Hyperion, Plansee | General purpose TiN | 80-150 | Wide availability from reputable European producers |
Evonik Industries, Arkema | High purity TiN (99.9%+) | 250-500 | Demanded by aerospace and medical device industries | |
NanoMaterials | Ultrafine TiN (<50 nm) | 800-1200 | Leading supplier for research and development purposes | |
Asia Pacific | China National Bluestar (CNB), Fangda Carbon New Material, Ningbo Tianxiang | Commercial grade TiN | 50-80 | Cost-effective option for bulk applications |
Toda Metal, Mitsui Mining & Smelting | High performance TiN | 120-200 | Known for quality and consistency in Asia | |
Kojundo Chemical Laboratory | Specialized TiN grades (e.g., doped) | Price upon request | Expertise in custom-engineered powders for specific needs |
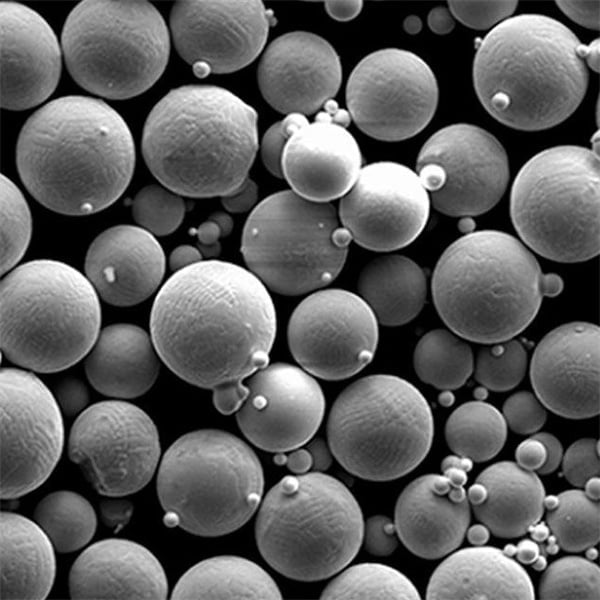
Comparison between Titanium Nitride and Other Hard Coatings
Properties Comparison
Properties | Titanium Nitride | Chromium Nitride | Aluminum Titanium Nitride | Diamond-Like Carbon | Titanium Carbide |
---|---|---|---|---|---|
Hardness (HV) | 2000 – 2400 | 1400 – 1800 | 3200 – 3400 | 1000 – 1500 | 2800 – 3400 |
Strength | Excellent | Good | Superior | Very Good | Extremely High |
Wear Resistance | Extremely High | Moderate | Exceptionally High | Moderate | Exceptionally High |
Corrosion Resistance | High | Moderate | Very High | Low | High |
Oxidation Resistance | Moderate | Good | Excellent | Good | Good |
Coefficient of Friction | 0.5 | 0.35 – 0.6 | 0.4 | 0.1 – 0.2 | 0.25 – 0.35 |
Color | Bright gold | Gray | Dark Purple | Graphite gray | Blue-gray |
Max. Operating Temp. (°C) | 500 | 750 | 800 | 250 | 600 |
Cost | Moderate | Low | High | High | High |
Toxicity | Non-toxic | Contains Cr, Co | Non-toxic | Non-toxic | Non-toxic |
Advantages of Titanium Nitride
Some benefits and advantages of choosing titanium nitride coatings over other alternatives:
- Extreme hardness for wear protection with rating comparable to TiC
- Corrosion resistance suitable for most production environments
- High temperature stability retaining hardness up to ~500°C
- Low toxicity – safe for medical devices/implants unlike CrN
- Excellent adhesion to titanium alloy and stainless steel substrate
- Bio-inert making biocompatibility approval easier
- Neutral friction coefficient prevents galling of parts
- Higher oxidation resistance versus TiC coatings
Limitations of Titanium Nitride
Despite having very well-rounded performance, titanium nitride does have some limitations:
- Lower temperature stability than AlTiN which is stable over 800°C
- Relatively lower toughness and shock resistance versus DLC
- Higher coating stresses can result in cracking/flaking over time
- Not recommended for acidic environments due to spontaneous oxidation
- More expensive compared to simple Cr or WC coatings
- Metal-working processes can smear metallic debris over TiN finish
When to Choose Alternatives over Titanium Nitride
Other coatings may be better suited than TiN if:
- Operating temperatures exceed 500°C (use AlTiN or chromium nitride)
- Superior toughness against impact loads needed (consider DLC)
- Passthrough of RF signals required e.g. aerospace/telecom (DLC better option)
- Exposed to halogen acids or other very corrosive media (choose DLC)
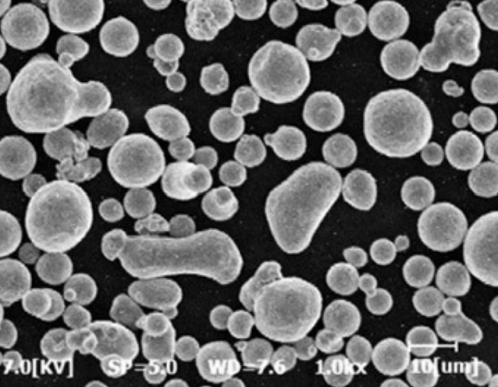
Pros and Cons of Titanium Nitride Coating
Feature | Pros | Cons |
---|---|---|
Wear Resistance | * Significantly extends tool life by reducing friction and wear. Cutting tools, drill bits, and other implements last longer, reducing replacement costs and downtime. * Offers superior protection against abrasive materials, making it ideal for machining composites, wood, and certain metals. | * Brittleness: While hard, TiN can chip or flake if subjected to high impact or excessive force. May not be suitable for heavy-duty percussion applications. * Thickness |
Friction Reduction | * Lowers friction coefficient, leading to smoother cutting operations. This reduces heat generation, which can damage tools and degrade workpiece quality. * Minimizes energy consumption during machining, resulting in cost savings and a more environmentally friendly process. | * Performance may vary depending on the material being machined. Lubrication might still be necessary for some applications. |
Corrosion Resistance | * TiN acts as a barrier against corrosion, protecting the underlying metal from rust and other environmental factors. * Maintains the integrity and functionality of tools and components in harsh environments. | * Not as effective against certain chemicals or highly corrosive substances. * Other coatings might be better suited for extreme corrosion resistance needs. |
Thermal Stability | * Performs well at elevated temperatures, making it suitable for high-speed machining applications. * Reduces heat-related tool wear and maintains dimensional accuracy of machined parts. | * May not be the best choice for extremely high-temperature environments where other advanced coatings excel. |
Aesthetics | * Distinctive golden or yellowish hue often associated with high-performance tools. * Enhances the visual appeal of certain products. | * Cosmetic benefit is secondary to the functional advantages. * Color can vary slightly depending on the deposition process. |
Cost | * Relatively affordable compared to some other advanced coating technologies. * Provides significant performance improvement at a reasonable cost point. | * Initial coating cost needs to be weighed against the benefits of extended tool life and improved machining efficiency. |
Environmental Impact | * Reduces waste by extending tool lifespan, requiring fewer replacements. * Contributes to a more sustainable machining process. | * The coating process itself might involve the use of specific chemicals, requiring proper disposal procedures. |
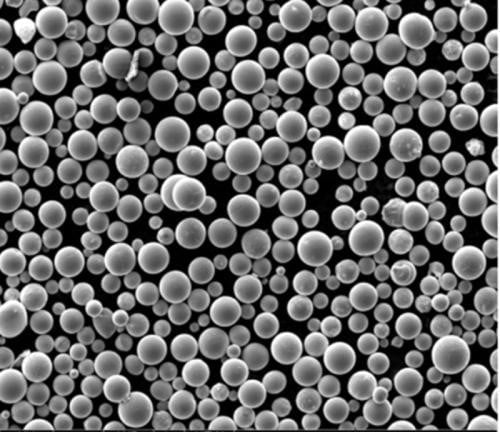
FAQ
Q: Why is titanium nitride gold in color?
A: The golden color results from light absorption/reflection properties of titanium nitride crystalline structure which gives plasma or vapor deposited TiN coatings their distinctive gold finish.
Q: Is titanium nitride toxic?
A: No, titanium nitride ceramic is considered completely non-toxic and bio-inert making it safe for use in biomedical implants per ISO 10993 biocompatibility standards.
Q: What thickness of TiN coating should be used?
A: Typical thickness range is 1-5 microns. Thinner 0.5-1 micron coatings provide wear protection. 2-5 micron films offer corrosion and erosion resistance for longer service.
Q: Does TiN coating increase or decrease friction?
A: TiN reduces coefficient of friction significantly versus steel. Exact values range from 0.4 to 0.9 depending on counterpart material thus decreasing overall friction but preventing galling seizure.
Q: What is the typical hardness of titanium nitride films?
A: Hardness values range from 2000-2500 Vickers when deposited as thin films using PVD or CVD techniques, among the highest values achievable for commercial coatings.
Q: What is aqua titanium nitride?
A: Aqua TiN refers to a titanium carbonitride coating alloyed with 8-20% silicon giving an aqua-blue color finish besides excellent tribological performance upto 700 deg. C temperatures.
Q: Does TiN coating prevent galling and adhesion wear?
A: Yes, titanium nitride is widely used in applications like forming/punching/drawing where it serves as an excellent anti-galling and anti-seizure coating even under boundary lubrication conditions.
Q: What industries use titanium nitride coatings?
A: All major manufacturing sectors including automotive, aerospace, textile, packaging, electronics, steel, petrochemical, medical etc. use TiN films to enhance performance and reliability of critical parts and tooling.
Share On
MET3DP Technology Co., LTD is a leading provider of additive manufacturing solutions headquartered in Qingdao, China. Our company specializes in 3D printing equipment and high-performance metal powders for industrial applications.
Inquiry to get best price and customized Solution for your business!
Related Articles
About Met3DP
Recent Update
Our Product
CONTACT US
Any questions? Send us message now! We’ll serve your request with a whole team after receiving your message.
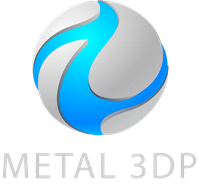
Metal Powders for 3D Printing and Additive Manufacturing
COMPANY
PRODUCT
cONTACT INFO
- Qingdao City, Shandong, China
- [email protected]
- [email protected]
- +86 19116340731