titanium powder 3d printing Applications
Table of Contents
With its high strength-to-weight ratio, temperature performance, corrosion resistance and durability, titanium is an exceptional material for additive manufacturing across critical commercial and industrial applications. Paired with the complex design freedoms facilitated by modern powder bed fusion approaches, titanium powder 3d printing unlocks new potential.
This overview guide explores common titanium alloys leveraged, corresponding mechanical properties achieved, post-processing treatments to further enhance characteristics, available suppliers providing high purity print powders, and practical use case examples by end-use industry. Comparison tables highlight the relative strengths of different titanium materials and printing methods.
Overview of titanium powder 3d printing
Compared to conventional subtractive machining, additive printing using fine titanium metal powder feedstocks provides:
- Reduced Raw Material Waste – high buy-to-fly ratio over 90%
- Lower Component Mass – optimized lightweighting
- Design Freedom – complexity not limited by tool access
- Customization – site-specific feature tailoring
- Simplified Assemblies – integrated components
- Performance Improvements – stronger than cast and wrought
Both laser powder bed fusion and directed energy deposition (DED) techniques can successfully fabricate complex titanium parts. Quality assurance across the entire AM workflow – starting with high purity print powder – provides reliable, consistent high performance components.
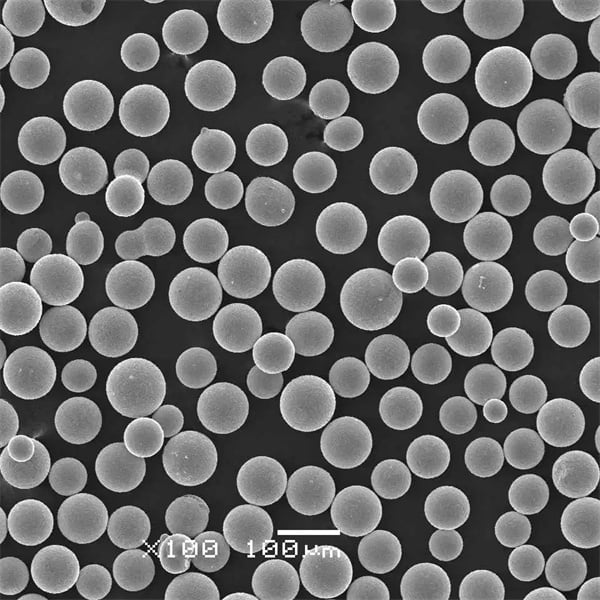
Titanium Alloy Options for 3D Printing
The most common titanium material variants leveraged for additive applications include commercially pure grades and titanium 6Al-4V (Ti64). Emerging alloys like Ti6462 provide enhanced capability.
Standard Titanium Print Alloys Matrix
Alloy | Composition | Properties | Common Uses |
---|---|---|---|
CP Grade 1 | Ti 99.2%, Fe/O/N/C limits | Excellent corrosion resistance, average mechanicals | Chemical plants, marine |
CP Grade 2 | Ti 99.4%, Fe/O/N/C limits | Better strength than Gr1, equally corrosion resistant | Aerospace airframes, implants |
Ti-6Al-4V | Ti 90%, Al 6%, V 4% | Harder, Excellent strength-to-weight ratio | Aerospace & motorsports |
Ti6462 | Ti Bal, Al 5.8-6.8%, Mo 3% | High fatigue resistance. Aerospace spec under development | Next-gen aerospace components |
Trace elements like Fe, C, N and O are heavily controlled to meet strict chemistry requirements for AM.
Specifications for titanium powder 3d printing
Spherical powders with controlled particle size distribution, minimal internal porosity and stringent chemistry purity levels are imperative for high quality printing using titanium.
Powder Feedstock Particle Standards
Measurement | Requirement |
---|---|
Size Range | 15 – 53 microns |
Mean Particle Size | 25-35 microns |
Particle Shape | Highly Spherical |
Apparent Density | 2.7 – 3.7 g/cm3 |
Tap Density | 3.2 – 4.2 g/cm3 |
Standards tighten morphological parameters to improve powder bed packing and spreading behavior during printing cycles.
Post-Processing Methods for Titanium AM Parts
Common post-processing techniques applied to improve material performance of printed titanium-based components feature:
Primary Post-Treatments Used
Stress Relieving
Low temperature aging to remove residual stresses. Prevents potential warpage or cracking.
Surface Finishing
Enhances precision dimensions, breaks sharp edges or smooths exterior aesthetic appearance.
HIP (Hot Isostatic Pressing)
Simultaneous elevated temperature and isostatic pressure densifies internal voids/porosity present from AM processes.
Heat Treatment
Alters microstructure of Ti-6Al-4V to optimize ductility, fracture toughness, and fatigue life.
Machining
Brings extremely tight dimensional accuracy and surface finishes best addressed by CNC machining near-net shape parts.
Comparing Metal 3D Printing Techniques for Titanium
Modern techniques facilitate micro welding of fine titanium powder using precision laser melting or electron beams in tight inert environments:
Titanium Printing Process Options Matrix
Method | Description | Benefits | Limitations |
---|---|---|---|
Laser Powder Bed Fusion | Laser selectively fuses regions of powder bed based on CAD model input | Highest commercial adoption; best fitness for final use material properties | Comparatively slower build speeds |
Electron Beam Melting | Electron beam fuses powder spread across build plate in high vacuum | Exceptional consistency part-to-part; large potential build volumes | Challenging to process reactive elemental titanium without rigourous atmosphere controls |
Direct Energy Deposition | Focused laser melts metal powder spray impacting the print area | Larger components feasible; repairs enabled | Significant porosity challenges titanium mechanical performance |
Laser-based powder bed approaches see predominant adoption for printing demanding titanium components thanks to precision dimensional accuracy and material purity.
Titanium Metal AM Part Applications
The tailorable mechanical properties, light-weightiness, corrosion and bio-inertness titanium provides over a wide temperature range suits nicely for:
Diverse Industries Adopting Titanium 3D Printing
Aerospace – Engine brackets, drone parts, satellite equipment Motorsports – Connecting rods, intake manifolds, turbochargers Medical & Dental – Custom orthopedic implants, prosthetics Oil & Gas – Pipeline fittings, deepwater valves/pumps Power Generation – Lightweight impellors and turbine blades
Ability to manufacture complex low-volume components with advanced engineered metallurgy accelerates titanium adoption. Partnerships across the supply chain ensure material traceability and process repeatability.
Industrial Suppliers Providing titanium powder 3d printing
Leaders providing high purity spherical titanium powders specifically for additive manufacturing processes feature:
Titanium Powder Producers Matrix
Company | Common Grades | Typical Pricing, $/Kg |
---|---|---|
AP&C | Ti-6Al-4V, Gr2, Gr5, Ti6462 | $100 – $500 |
LPW Technology | Ti-6Al-4V, Gr23, Ti64 | $150 – $600 |
Tekna | Ti-6Al-4V | $250 – $400 |
Sandvik | Ti-6Al-4V | $200 – $350 |
Range on $/Kg basis depends significantly on purity, powder size distribution tightness, sampling, certifications required and purchase volumes. Local supply chain helps reduce lead times.
FAQ
Which titanium alloy powder is considered optimal for medical devices & implants?
Due to its excellent biocompatibility paired with outstanding high cycle fatigue performance, medical grade 5 titanium per ASTM F67 meets stringent chemistry controls ideal for patient-facing devices and loadbearing implant applications.
How many times can titanium AM powder feedstocks be reused?
Titanium print powders may be effectively reused 5-10 times typically before refreshed, assuming strict monitoring protocols over acceptable oxygen pickup levels from repeated thermal cycling are maintained below maximum thresholds through blending and sieving.
What density should be expected for laser-melted titanium parts without any post-processing?
Directly after removal from a powder bed system with optimized processing parameters, near-full densities over 98% should be expected for as-built titanium components, rivaling and exceeding cast or wrought products requiring extensive downstream operations to achieve similar performance.
What post-processing technique boosts fatigue life the most?
For prominent Ti-6Al-4V alloy parts seeing cyclic stresses, Hot Isostatic Pressing (HIP) provides up to ~30% longer fatigue lifespans by minimizing internal voids and residual porosity typically present after metal AM processes from unavoidable localized micro shrinkage effects between fused powder particles.
Outside directed energy deposition techniques what other surface enhancement methods successfully modify titanium AM parts?
Thermal spray technologies like plasma transferred arc (PTA), high velocity air fuel (HVAF), and high velocity oxygen fuel (HVOF) welding techniques allow thick protective exterior coatings including ceramics; cold spray impacts powders onto surfaces providing thickened sections and wear protections; laser cladding or laser metal deposition overlay additional metal alloys enhancing corrosion, friction and impact resistance through superior metallurgical bonding.
Share On
MET3DP Technology Co., LTD is a leading provider of additive manufacturing solutions headquartered in Qingdao, China. Our company specializes in 3D printing equipment and high-performance metal powders for industrial applications.
Inquiry to get best price and customized Solution for your business!
Related Articles
About Met3DP
Recent Update
Our Product
CONTACT US
Any questions? Send us message now! We’ll serve your request with a whole team after receiving your message.
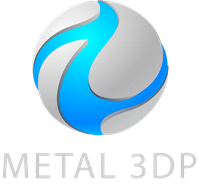
Metal Powders for 3D Printing and Additive Manufacturing