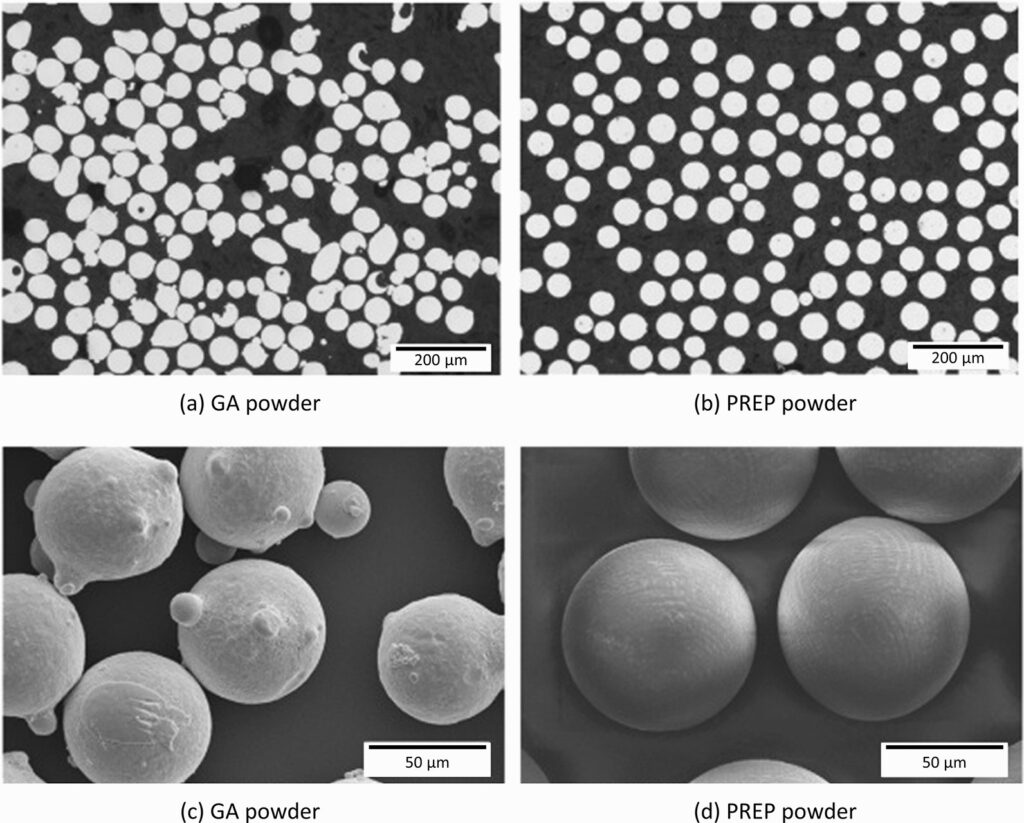
Triballoy T800 Powder: Proven Excellence in Wear-Resistant Applications
Low MOQ
Provide low minimum order quantity to meet different needs.
OEM & ODM
Provide customized products and design services to meet unique customer needs.
Adequate Stock
Ensure fast order processing and provide reliable and efficient service.
Customer Satisfaction
Provide high quality products with customer satisfaction at the core.
share this article
Table of Contents
Looking for a material that can handle extreme wear, high temperatures, and corrosive environments? Look no further than Triballoy T800 powder. This high-performance alloy is designed to excel in the most demanding industrial conditions, offering a unique balance of hardness, toughness, and corrosion resistance. Whether you’re working in aerospace, oil & gas, or heavy machinery, Triballoy T800 powder has the properties to improve efficiency and extend the life of your equipment.
In this guide, we’ll dive deep into the composition, properties, applications, and much more, giving you a complete picture of why Triballoy T800 powder is a top choice for critical applications. Whether you’re an engineer, a manufacturer, or someone just looking to learn more about high-performance alloys, we’ve got you covered.
Overview: What is Triballoy T800 Powder?
Triballoy T800 powder is a cobalt-based alloy known for its superior wear resistance, high hardness, and corrosion resistance even at elevated temperatures. It belongs to the Triballoy family, which is specifically designed to perform in environments where traditional materials fail due to friction, abrasion, and chemical attack.
What sets Triballoy T800 apart is its ability to maintain its mechanical properties in extreme conditions, making it ideal for applications in industries like aerospace, power generation, and mining. As a powdered material, it’s commonly used in thermal spraying, laser cladding, and additive manufacturing, providing a layer of protection to components subjected to wear and corrosion.
Composition and Properties of Triballoy T800 Powder
The composition of Triballoy T800 powder is carefully crafted to deliver exceptional performance in the harshest environments. Each element in the alloy plays a specific role in enhancing its resistance to wear, corrosion, and oxidation.
Chemical Composition of Triballoy T800 Powder
Element | Percentage (%) | Role in the Alloy |
---|---|---|
Cobalt (Co) | Balance | The base element, providing high-temperature stability and wear resistance. |
Chromium (Cr) | 16-18% | Increases corrosion resistance and contributes to hardness. |
Molybdenum (Mo) | 28-32% | Enhances wear resistance, especially in abrasive environments. |
Nickel (Ni) | ≤ 3% | Adds toughness and corrosion resistance, particularly in reducing environments. |
Silicon (Si) | ≤ 2% | Improves oxidation resistance and the overall manufacturability of the alloy. |
Triballoy T800 Powder Key Properties
Property | Value/Description |
---|---|
Density | 8.6 g/cm³ |
Melting Point | 1,300°C – 1,350°C |
Hardness | 60-65 HRC (Rockwell Hardness) |
Wear Resistance | Exceptional, especially in abrasive and high-friction environments. |
Corrosion Resistance | Superior, particularly in saline, acidic, or chemically aggressive environments. |
Thermal Stability | Retains hardness and strength up to temperatures of 900°C. |
Tensile Strength | 1,000 MPa |
Oxidation Resistance | Excellent, making it suitable for high-temperature applications where oxygen exposure is a concern. |
Toughness | Moderate, though optimized for wear resistance rather than impact toughness. |
Why Triballoy T800 Powder is the Superior Alloy for Extreme Conditions
1. Unmatched Wear Resistance
If you’re dealing with high-friction environments, Triballoy T800 powder should be at the top of your list. Thanks to its high molybdenum and chromium content, this alloy offers incredible wear resistance, especially in abrasive and erosive conditions. Whether it’s metal-on-metal contact or exposure to hard particles, Triballoy T800 excels where other materials fail.
Imagine an industrial pump that constantly handles abrasive slurry. Over time, components made from traditional materials would wear down, leading to costly maintenance and downtime. But with Triballoy T800, you get a material that significantly extends the life of your equipment, reducing both costs and headaches.
2. Excellent High-Temperature Performance
Triballoy T800 powder is specifically designed to maintain its hardness and mechanical properties at elevated temperatures, making it ideal for environments where heat is a constant factor. With the ability to withstand temperatures up to 900°C, this alloy is a perfect fit for industries like power generation and aerospace, where components are often subjected to extreme heat.
3. Superior Corrosion Resistance
In environments where exposure to corrosive chemicals, saline water, or acidic substances is a concern, Triballoy T800 powder offers excellent corrosion resistance. Its high chromium and molybdenum content allows it to perform well in environments that would quickly degrade other materials, making it a reliable choice for oil & gas, marine, and chemical processing industries.
4. Good Machinability in Powder Form
Although Triballoy T800 is extremely hard, as a powder, it’s relatively easy to work with in thermal spraying and laser cladding processes. Its spherical particles ensure good flowability, which is essential for achieving a uniform coating or build in additive manufacturing applications.
Triballoy T800 Powder Applications
So, where does Triballoy T800 powder truly shine? Its versatility and high-performance properties make it a favored material across a wide range of industries with demanding operational requirements.
Common Applications of Triballoy T800 Powder
Industry | Application |
---|---|
Aerospace | Turbine blades, engine components, and bearings that operate at high temperatures and under constant friction. |
Oil & Gas | Valve seats, pump parts, drilling components, and other equipment exposed to corrosive fluids and abrasive environments. |
Marine | Propellers, shafts, and other components exposed to the corrosive effects of saltwater. |
Power Generation | Steam turbine components, heat exchangers, and other high-temperature parts used in power plants. |
Chemical Processing | Valves, seals, and pump components that handle corrosive chemicals and abrasive fluids. |
Mining | Drill bits, crusher components, and other tools subjected to extreme wear in harsh mining environments. |
General Manufacturing | Cutting tools, extrusion dies, and other wear-resistant tools in high-friction manufacturing processes. |
Triballoy T800 Powder Specifications, Sizes, Grades, and Standards
When selecting Triballoy T800 powder for your project, it’s essential to understand the specifications, sizes, and grades available. These factors can significantly influence the material’s performance based on your specific application needs.
Triballoy T800 Powder Specifications
Specification | Details |
---|---|
Particle Size | Typically ranges from 15 to 53 microns, depending on the application (e.g., thermal spray, additive manufacturing). |
Powder Morphology | Spherical particles for optimal flowability in thermal spraying and additive manufacturing processes. |
ASTM Standards | ASTM F75 for cobalt-based alloys used in medical and industrial applications. |
ISO Standards | ISO 5832-12 for cobalt-chromium-molybdenum alloys used in medical implants. |
UNS Number | UNS R40080 |
Hardness Range | 60-65 HRC, depending on the application and heat treatment. |
These specifications ensure that Triballoy T800 powder meets the rigorous demands of industries like aerospace, oil & gas, and power generation.
Suppliers and Pricing of Triballoy T800 Powder
As with any high-performance material, sourcing Triballoy T800 powder from reliable suppliers is crucial to ensure you get the quality and consistency needed for your application. Below, we’ve listed some of the top suppliers and typical pricing information.
Triballoy T800 Powder Suppliers and Pricing
Supplier | Price Range (per kg) | Notes |
---|---|---|
Kennametal | $400 – $500 | A leading supplier of cobalt-based alloys, known for high-quality Triballoy powders. |
Oerlikon Metco | $420 – $540 | Specializes in advanced materials for thermal spraying and additive manufacturing. |
Carpenter Technology | $430 – $550 | Supplies high-performance alloys for aerospace, energy, and industrial sectors. |
Höganäs AB | $430 – $550 | Offers a wide range of metal powders, including Triballoy T800 for wear resistance applications. |
Powder Alloy Corporation | $420 – $530 | Provides high-quality Triballoy powders specifically for thermal spraying and laser cladding. |
Given the specialized nature of Triballoy T800 powder, it tends to be more expensive than traditional materials. However, its durability and extended service life often result in lower long-term costs, especially in critical applications where maintenance and downtime are costly.
Comparing the Pros and Cons of Triballoy T800 Powder
Before deciding whether Triballoy T800 powder is right for your application, it’s important to weigh its benefits and limitations. Below, we’ve outlined the advantages and disadvantages of this high-performance material.
Advantages of Triballoy T800 Powder
Advantage | Why It’s Important |
---|---|
Exceptional Wear Resistance: Withstands abrasion and erosion better than many alloys. | Ideal for high-wear applications such as cutting tools, turbine blades, and valve seats. |
High-Temperature Stability: Retains hardness and strength at temperatures up to 900°C. | Perfect for components in engines, turbines, and other high-temperature environments. |
Corrosion Resistance: Performs well in saline, acidic, and chemically aggressive environments. | Suitable for applications in the oil & gas, marine, and chemical processing industries. |
Flowability in Powder Form: Spherical particles ensure smooth application in thermal spray. | Ensures consistent results in coating and cladding processes. |
Extended Service Life: Reduces the need for frequent replacements, lowering maintenance costs. | Especially beneficial in industries where downtime is expensive, like aerospace and power generation. |
Limitations of Triballoy T800 Powder
Limitation | Why It’s a Challenge |
---|---|
Expensive: Higher cost compared to more common wear-resistant materials. | May not be suitable for lower-demand applications or budget-conscious projects. |
Moderate Toughness: Not ideal for applications requiring high impact resistance. | Other alloys may be more suitable for applications with significant impact loads. |
Difficult to Machine: High hardness can make machining challenging. | Requires specialized tools and processes, which can increase manufacturing costs and lead times. |
Limited Availability: Not always readily available in all regions or in large quantities. | May result in longer lead times depending on supplier and demand. |
FAQs About Triballoy T800 Powder
To help you better understand Triballoy T800 powder, we’ve compiled a list of frequently asked questions and their answers.
Question | Answer |
---|---|
What is Triballoy T800 powder used for? | It is used in industries like aerospace, oil & gas, and power generation for high-wear, high-temperature applications. |
How much does Triballoy T800 powder cost? | Pricing typically ranges from $400 to $550 per kilogram, depending on the supplier and order size. |
Can Triballoy T800 powder be used in additive manufacturing? | Yes, it is commonly used in additive manufacturing processes, such as laser cladding and powder-bed fusion. |
What industries commonly use Triballoy T800 powder? | Aerospace, oil & gas, marine, automotive, and power generation industries frequently use Triballoy T800 powder for components exposed to wear and high heat. |
What makes Triballoy T800 powder resistant to wear? | The high molybdenum content gives it excellent wear resistance, especially in abrasive environments with significant friction. |
Is Triballoy T800 powder magnetic? | No, Triballoy T800 powder is generally non-magnetic, making it suitable for applications requiring non-magnetic properties. |
How does Triballoy T800 powder compare to other cobalt alloys? | Compared to other cobalt-based alloys, Triballoy T800 excels in wear resistance and high-temperature performance but may be more challenging to machine. |
What are the main advantages of using Triballoy T800 powder? | The main advantages include exceptional wear resistance, high-temperature stability, and excellent corrosion resistance in harsh environments. |
Conclusion: Is Triballoy T800 Powder Right for Your Next Project?
When it comes to selecting a material that offers superior wear resistance, high-temperature stability, and corrosion resistance, few alloys compare to Triballoy T800 powder. While it may come with a higher price tag, its long-term durability and performance in the toughest environments make it a cost-effective solution for industries like aerospace, oil & gas, and power generation.
If your project involves components exposed to constant friction, abrasion, or corrosive environments, investing in Triballoy T800 powder can lead to longer service life, reduced maintenance, and greater operational efficiency.
So, is Triballoy T800 powder the right material for your next project? If you’re dealing with extreme conditions, the answer is most likely a resounding yes!
Get Latest Price
About Met3DP
Product Category
HOT SALE
CONTACT US
Any questions? Send us message now! We’ll serve your request with a whole team after receiving your message.
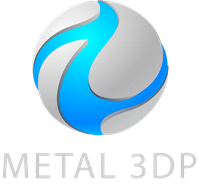
Metal Powders for 3D Printing and Additive Manufacturing