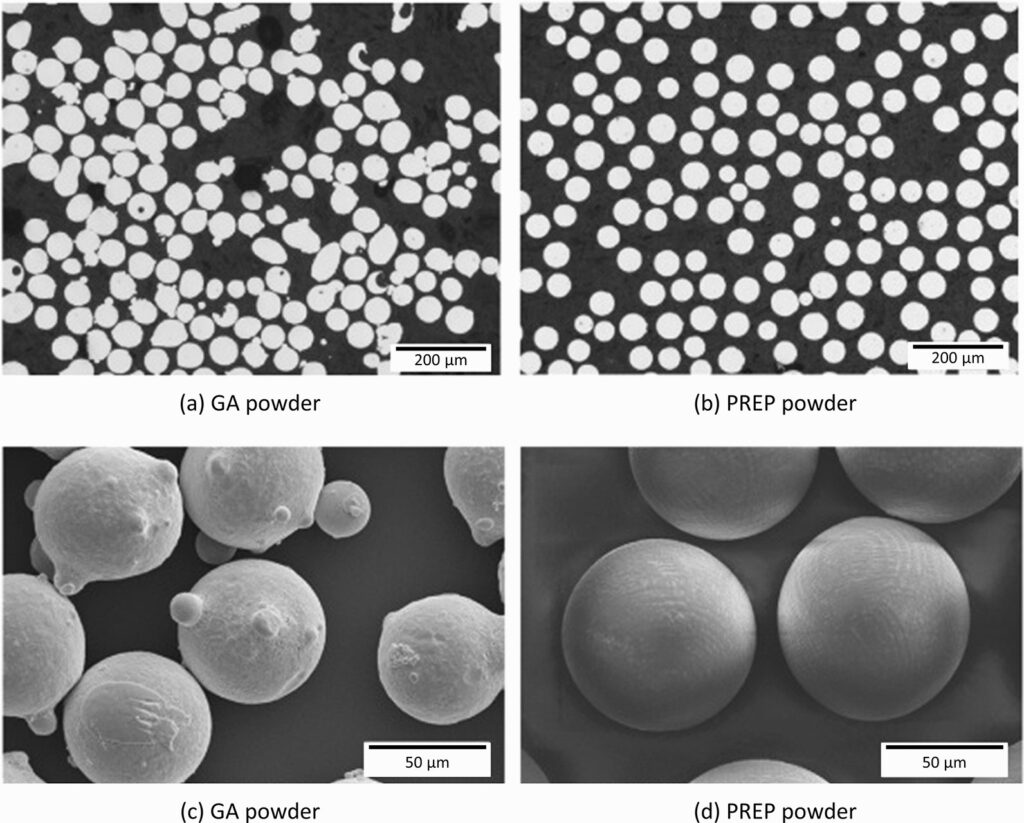
Tungsten Carbide Particles: The Toughest Material for High-Performance Tools
Low MOQ
Provide low minimum order quantity to meet different needs.
OEM & ODM
Provide customized products and design services to meet unique customer needs.
Adequate Stock
Ensure fast order processing and provide reliable and efficient service.
Customer Satisfaction
Provide high quality products with customer satisfaction at the core.
share this article
Table of Contents
Tungsten carbide particles may sound like a niche material, but they are quietly driving some of the most efficient, durable, and high-performance technologies across industries. If you’ve ever wondered how industries like mining, manufacturing, and aerospace can push their tools to the limit without them wearing down, tungsten carbide particles are often the unsung heroes behind that durability.
In this guide, we’re diving deep into tungsten carbide particles—what they are, why they’re valuable, how they’re used, and everything in between. Whether you’re a seasoned engineer looking for detailed specs, or someone new to industrial materials, this comprehensive guide will break down everything you need to know.
Overview of Tungsten Carbide Particles
What Are Tungsten Carbide Particles?
Tungsten carbide particles are small grains or powders made from a compound of tungsten and carbon. The combination of these two elements results in a material that is almost as hard as diamond and incredibly resistant to wear, abrasion, and corrosion. Unlike some materials that are only strong in one dimension, tungsten carbide offers a unique blend of hardness, toughness, and thermal stability that makes it suitable for some of the most demanding applications on the planet.
To put it simply: if you’re building something that needs to withstand extreme wear, high temperatures, or intense pressure, tungsten carbide particles are probably on your radar.
Why Use Tungsten Carbide Particles?
Why do so many industries rely on tungsten carbide particles? Because they’re like the Swiss Army knife of industrial materials. They can be used in everything from cutting tools to wear-resistant coatings, and they outperform many other materials in terms of longevity and strength.
Imagine you’re working in mining. The drill bits you’re using are constantly exposed to hard rock, heat, and friction. Without a material like tungsten carbide, those drill bits would wear down pretty quickly. But with tungsten carbide particles, those bits last longer, require less frequent replacement, and can keep pushing through tough materials without breaking down.
Composition and Properties of Tungsten Carbide Particles
The incredible properties of tungsten carbide particles come from their unique composition. They are typically composed of 70-97% tungsten carbide (WC) combined with a metal binder (like cobalt or nickel), which helps to improve toughness and flexibility.
Property | Description |
---|---|
Composition | Typically 70-97% tungsten carbide (WC) and 3-30% metal binder (cobalt or nickel). |
Hardness (Vickers Scale) | Ranges from 1,500 to 2,200 HV, depending on WC content and particle size. |
Density | Around 15.6 g/cm³, making it one of the densest materials used in industrial applications. |
Fracture Toughness | Values range from 10 to 15 MPa·m^1/2, providing a good balance between hardness and toughness. |
Compressive Strength | Can withstand pressures up to 6,000 MPa, making it ideal for high-stress environments. |
Thermal Conductivity | High thermal conductivity, allowing it to disperse heat effectively in high-temperature settings. |
Melting Point | Tungsten carbide has a melting point of around 2,870°C (5,198°F). |
Corrosion Resistance | Excellent resistance to corrosion, especially in acidic or chemically aggressive environments. |
The hardness of tungsten carbide particles makes them exceptional for abrasive wear applications, while the metal binder improves their toughness, preventing them from becoming too brittle under stress. This combination makes tungsten carbide particles suitable for applications in cutting tools, drilling, powder metallurgy, and surface coatings.
Key Characteristics of Tungsten Carbide Particles
- Extremely Hard: Tungsten carbide is one of the hardest materials known to man, second only to diamond.
- High Wear Resistance: It resists wear and tear in abrasive environments, making it perfect for cutting and drilling tools.
- Thermal Stability: Tungsten carbide can withstand high temperatures without losing its strength or integrity.
- Corrosion Resistance: It holds up well in chemically aggressive environments, extending the lifespan of tools and components.
Types of Tungsten Carbide Particles Based on Composition and Properties
Not all tungsten carbide particles are created equal. Depending on their composition and how they are manufactured, they can have different properties that make them more suitable for specific applications.
Type | Description |
---|---|
Cobalt-Bonded Tungsten Carbide | Uses cobalt as a binder, offering a good balance of hardness and toughness. Ideal for cutting tools. |
Nickel-Bonded Tungsten Carbide | Nickel binder improves corrosion resistance, making it suitable for oil and gas industries. |
Mixed Binder Tungsten Carbide | Combines cobalt and nickel binders for applications requiring both toughness and chemical resistance. |
Fine-Grain Tungsten Carbide | Small particle sizes (0.5-2 µm) provide higher hardness and are used in precision tools. |
Coarse-Grain Tungsten Carbide | Larger particles (5-10 µm) offer better toughness and are used in impact-resistant tools. |
Spherical Tungsten Carbide Particles | Rounded particles for thermal spraying and surface coatings applications. |
Crushed Tungsten Carbide Particles | Irregularly shaped particles often used in abrasive blasting or composite materials. |
Each of these types has its own specific uses, depending on the balance between hardness, toughness, and chemical resistance that a particular application requires.
Applications of Tungsten Carbide Particles
Where are tungsten carbide particles used? The better question might be: where aren’t they used? Their versatility and performance make them essential across a wide range of industries. Let’s dive into some of the key areas where tungsten carbide particles shine.
Industry | Applications |
---|---|
Mining and Drilling | Tungsten carbide particles are used in drill bits, rock-cutting tools, and wear parts that need to withstand extreme abrasion. |
Oil and Gas | Found in downhole tools, valve seats, and bearings that face corrosive environments and high pressure. |
Metalworking | Used in cutting tools, grinding wheels, and dies for machining tough metals like steel and titanium. |
Aerospace | Applied in jet engines, turbine blades, and rocket components that require materials resistant to high temperatures and wear. |
Automotive | Found in engine components, brake systems, and gear tools that need to resist wear and stay strong under intense heat. |
Construction | Used in concrete cutting tools, road milling machines, and demolition equipment that face heavy impact and abrasion. |
Defense and Military | Tungsten carbide particles are used in armor-piercing ammunition and coatings to enhance the durability of military equipment. |
Surface Coatings | Tungsten carbide particles are used in thermal spraying to create protective coatings for industrial machinery and tools. |
Tungsten Carbide Particles in Mining and Drilling
In the mining and drilling industry, tungsten carbide drill bits are used to cut through hard rock formations. The extreme hardness of tungsten carbide makes these bits last longer and resist wear better than other materials, reducing downtime and increasing productivity.
Tungsten Carbide Particles in Metalworking
In metalworking, tungsten carbide particles are a staple in the production of cutting tools such as end mills, drill bits, and lathe tools. Their ability to retain sharpness for extended periods reduces the need for frequent tool changes, saving both time and money.
Tungsten Carbide Particles in Surface Coatings
One of the more specialized uses of tungsten carbide particles is in coatings. By applying tungsten carbide to a surface using thermal spraying or other methods, industries can create extremely durable coatings that resist wear, corrosion, and heat. These coatings can extend the life of machinery and tools by providing an additional layer of protection.
Specifications, Sizes, Grades, and Standards for Tungsten Carbide Particles
When selecting tungsten carbide particles for a particular application, it’s essential to understand the specifications, sizes, and grades available. These factors can significantly impact performance depending on the environment and stresses the material will face.
Specification | Details |
---|---|
Particle Sizes | Available in sizes ranging from 0.5 µm (fine) to 10 µm (coarse) depending on the application. |
Grain Sizes | Grain sizes typically range from 0.5 µm (fine-grain) to 10 µm (coarse-grain) for different performance needs. |
Grades | Common grades are defined by ISO standards, with grades like K10, K20, and K30 being widely used based on hardness and toughness. |
Hardness | Hardness values range from 1,500 to 2,200 HV depending on the tungsten carbide content and grain size. |
Density | Typically around 15.6 g/cm³, depending on the metal binder and tungsten carbide content. |
Compressive Strength | Can withstand pressures up to 6,000 MPa, making it ideal for high-pressure and high-wear environments. |
Standards | Tungsten carbide particles are often certified to meet ISO 9001, ASTM B777 for tungsten products, and ISO 513 for cutting tool materials. |
These specifications ensure that you’re getting the right material for the job, whether you’re working in aerospace, mining, or metalworking.
Suppliers and Pricing
When choosing a supplier for tungsten carbide particles, it’s essential to consider factors like material quality, reputation, and of course, pricing. Below is a breakdown of some leading suppliers and their pricing ranges.
Supplier | Country | Price Per Kg (USD) | Grade Options | Special Features |
---|---|---|---|---|
Kennametal | United States | $80 – $150 | K10, K20, K30 | Leading supplier of high-quality tungsten carbide for various industrial applications. |
Sandvik | Sweden | $90 – $160 | K10, K20, P10 | Known for precision carbide products for mining, metalworking, and cutting tools. |
Zhuzhou Cemented Carbide Group | China | $50 – $100 | K10, K20, K30 | Lower-cost supplier with a focus on carbide for mining and drilling industries. |
CERATIZIT | Luxembourg | $100 – $180 | K10, K20, P15 | Specializes in carbide materials for aerospace and high-performance applications. |
Sumitomo Electric Hardmetal | Japan | $110 – $170 | K10, K20 | Premium quality carbide for cutting tools and wear-resistant parts. |
Factors Influencing Tungsten Carbide Particle Pricing
Several factors can impact the price of tungsten carbide particles, including:
- Tungsten carbide content: Higher WC content usually leads to higher prices due to the cost of raw materials.
- Binder type: Cobalt as a binder is typically more expensive than nickel, impacting the overall price.
- Grain size: Fine-grain tungsten carbide tends to be more expensive due to the additional processing required.
- Supplier location: Suppliers from regions with lower production costs, such as China, may offer more competitive pricing.
Advantages and Disadvantages
Like any material, tungsten carbide particles come with their own set of advantages and disadvantages. Understanding these can help you determine whether they are the right choice for your particular application.
Advantages | Disadvantages |
---|---|
Extreme Hardness: Provides superior wear resistance in abrasive environments. | Brittleness: Can be brittle under high impact, potentially leading to cracks. |
Longer Tool Life: Reduces the need for frequent tool changes and maintenance. | High Cost: Tungsten carbide particles are more expensive than many alternatives. |
Thermal Stability: Maintains strength and hardness even at high temperatures. | Difficult to Machine: Requires specialized equipment for shaping or forming. |
Corrosion Resistance: Holds up well in chemically aggressive environments. | Weight: Tungsten carbide’s density may be a disadvantage in applications where lightweight materials are preferred. |
Overall, tungsten carbide particles are ideal for applications where hardness, wear resistance, and durability are essential. However, they may not be the best fit for applications requiring flexibility or lightweight materials.
Frequently Asked Questions (FAQ)
To help clarify some common questions about tungsten carbide particles, we’ve compiled a list of frequently asked questions below.
Question | Answer |
---|---|
What are tungsten carbide particles used for? | They are used in a wide range of industries, including mining, metalworking, aerospace, and oil and gas for wear resistance. |
How are tungsten carbide particles made? | They are produced using powder metallurgy, where tungsten carbide powder is mixed with a binder, pressed, and sintered at high temperatures. |
How hard are tungsten carbide particles? | Tungsten carbide particles typically have a hardness of 1,500 to 2,200 HV, depending on their composition. |
Why are tungsten carbide particles so expensive? | Their cost is due to the high price of tungsten and the complex manufacturing process involved in their production. |
What’s the difference between cobalt-bonded and nickel-bonded tungsten carbide? | Cobalt-bonded particles offer better toughness, while nickel-bonded particles provide greater corrosion resistance. |
Can tungsten carbide particles be recycled? | Yes, tungsten carbide particles can often be recycled to reduce costs and environmental impact. |
How do I choose the right grade of tungsten carbide particles? | The right grade depends on the application. For wear resistance, choose a higher WC content; for toughness, opt for higher binder content. |
Conclusion
Tungsten carbide particles are an indispensable material in industries where wear resistance, hardness, and durability are paramount. Whether you’re drilling through rock, cutting through metal, or coating industrial machinery, tungsten carbide particles provide a perfect solution to extend tool life, reduce downtime, and improve overall efficiency.
While they can carry a higher upfront cost than other materials, their performance and longevity make them a worthwhile investment in the long run. By understanding the composition, types, applications, and specifications, you can make an informed decision about incorporating tungsten carbide particles into your next project.
So, are tungsten carbide particles the right fit for your needs? If you’re working in demanding environments where tools and machinery are pushed to their limits, they just might be your best ally.
Get Latest Price
About Met3DP
Product Category
HOT SALE
CONTACT US
Any questions? Send us message now! We’ll serve your request with a whole team after receiving your message.