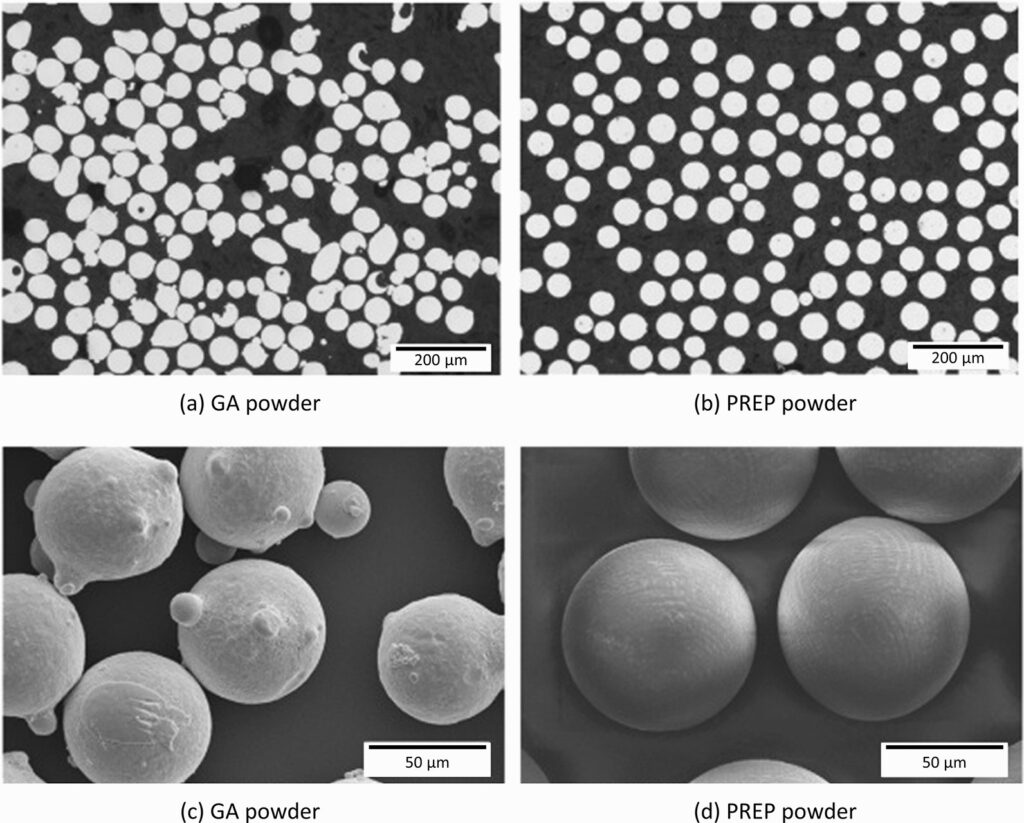
Ultimate Strength with Spherical Cobalt-Based Alloy Powder for Critical Industries
Low MOQ
Provide low minimum order quantity to meet different needs.
OEM & ODM
Provide customized products and design services to meet unique customer needs.
Adequate Stock
Ensure fast order processing and provide reliable and efficient service.
Customer Satisfaction
Provide high quality products with customer satisfaction at the core.
share this article
Table of Contents
Cobalt-based alloy powders are at the forefront of materials innovation, particularly for industries requiring exceptional strength, corrosion resistance, and thermal stability. Whether you’re involved in aerospace, medical device manufacturing, or additive manufacturing (AM), you’ve likely heard of spherical cobalt-based alloy powder. This powder is renowned for its superior mechanical properties, excellent wear resistance, and ability to withstand high temperatures. But how does it work? What makes it so special? And how can you use it to enhance your manufacturing processes?
In this guide, we’ll break down everything you need to know about spherical cobalt-based alloy powder—from its composition and properties to its applications, specifications, and pricing. By the end, you’ll understand why this material is a game-changer for advanced manufacturing and how it can help you stay ahead of the competition.
Overview: What is Spherical Cobalt-Based Alloy Powder?
Let’s start with the basics. Cobalt-based alloys are a group of metal alloys that use cobalt as their main component. These alloys are known for their high wear resistance, superior strength, and resistance to corrosion and oxidation, especially in high-temperature environments. They also maintain their mechanical properties over a wide range of conditions, making them a popular choice for critical applications, such as turbine engines, cutting tools, and medical implants.
But why spherical powder? In advanced manufacturing processes—particularly additive manufacturing—the shape of the powder particles matters. Spherical powders offer better flowability, packing density, and layer uniformity, which are critical for precision manufacturing methods like laser powder bed fusion (LPBF) or direct energy deposition (DED).
Key Features of Spherical Cobalt-Based Alloy Powder
- High strength and wear resistance: Ideal for high-stress environments.
- Corrosion and oxidation resistance: Performs well in harsh and high-temperature environments.
- Spherical shape: Ensures excellent flowability and packing density for additive manufacturing.
- Versatility: Used in aerospace, medical devices, energy, and more.
- Thermal stability: Maintains mechanical properties at high temperatures.
Types, Composition, and Properties of Spherical Cobalt-Based Alloy Powder
Cobalt-based alloys come in different compositions, each optimized for specific applications. These alloys typically contain cobalt as the base element, along with other elements like chromium, tungsten, nickel, and molybdenum that enhance their properties.
Common Types and Composition of Spherical Cobalt-Based Alloy Powder
Type | Typical Composition | Primary Applications |
---|---|---|
Stellite 6 | Co, Cr, W, C | Cutting tools, turbine blades, valves |
Stellite 21 | Co, Cr, Mo, Ni | Medical implants, aerospace parts, high-temperature valves |
Haynes 188 | Co, Ni, Cr, W | Gas turbine components, aerospace engine parts |
Tribaloy T-400 | Co, Mo, Cr, Si | Wear-resistant coatings, high-stress environments |
Cobalt-Chromium-Molybdenum (CoCrMo) | Co, Cr, Mo | Orthopedic implants, dental prosthetics |
Each of these alloys offers a unique combination of mechanical properties, allowing them to perform exceptionally well in high-stress, high-temperature, and corrosive environments. For instance, Stellite 6 is widely used in cutting tools because of its excellent wear resistance, while CoCrMo is preferred for biomedical applications due to its biocompatibility.
Key Properties of Spherical Cobalt-Based Alloy Powder
Property | Typical Value |
---|---|
Density | 8.4 to 9.2 g/cm³ (depending on composition) |
Melting Point | 1,400°C to 1,500°C |
Hardness (Vickers) | 400 to 700 HV |
Tensile Strength | 700 to 1,200 MPa |
Thermal Conductivity | 10 to 25 W/m·K |
Modulus of Elasticity | 200 to 240 GPa |
Corrosion Resistance | Excellent in both acidic and alkaline environments |
Oxidation Resistance | High, especially in elevated temperatures |
Wear Resistance | Superior due to the alloying elements like chromium and tungsten |
These properties make spherical cobalt-based alloy powders ideal for demanding applications, such as turbine blades, high-performance tools, and biomedical implants. Their hardness and wear resistance ensure a long service life, even in the most abrasive environments.
Applications of Spherical Cobalt-Based Alloy Powder
The versatility of spherical cobalt-based alloy powder enables its use across a wide range of industries. From aerospace to medical devices, these powders play a critical role in high-performance applications where strength, corrosion resistance, and thermal stability are paramount.
Key Applications of Spherical Cobalt-Based Alloy Powder
Industry | Application | Why Use Cobalt-Based Alloy Powder? |
---|---|---|
Aerospace | Turbine blades, engine components, exhaust systems | High strength-to-weight ratio, excellent thermal stability |
Medical | Orthopedic implants, dental prosthetics | Biocompatibility, corrosion resistance, long-term durability |
Energy | Gas turbines, power generation components | High-temperature stability, oxidation resistance |
Additive Manufacturing | 3D printing of complex geometries | Superior flowability, excellent packing density, and layer uniformity |
Automotive | High-performance engine parts, exhaust systems | Corrosion resistance, heat tolerance, wear resistance |
Tooling | Cutting tools, wear-resistant coatings | High hardness, wear resistance, and prolonged tool life |
Oil & Gas | Valves, pumps, drilling components | Corrosion resistance, mechanical strength in harsh environments |
Example: Cobalt-Based Alloys in Medical Implants
In the medical industry, cobalt-based alloys—particularly CoCrMo—are widely used for orthopedic implants and dental prosthetics. Their biocompatibility and ability to withstand the body’s harsh conditions make them an excellent choice for hip replacements, knee implants, and dental frameworks. Additionally, their wear resistance ensures that implants last longer, reducing the need for revision surgeries.
Specifications, Sizes, Standards, and Grades for Spherical Cobalt-Based Alloy Powder
When choosing spherical cobalt-based alloy powders for your project, you need to consider the specifications, sizes, and standards that fit your application. These factors can influence the material’s performance, especially in industries like aerospace and medical devices, where precision is crucial.
Specifications and Grades of Spherical Cobalt-Based Alloy Powder
Specification | Value |
---|---|
Purity | 99.0% – 99.9% (depending on alloy type) |
Particle Size | 10 µm to 100 µm (varies depending on application) |
Flowability | Excellent for use in powder bed fusion and laser powder bed fusion |
Packing Density | High, ensuring consistent layer formation in additive manufacturing |
Standards | ASTM F75 (Cobalt-Chrome Alloys), ASTM F1537 (CoCrMo), ASTM B212 (Metal Powders) |
Grade | Different grades based on elemental composition (e.g., Stellite 6, CoCrMo) |
Available Sizes and Forms
The particle size of spherical powders plays a significant role in determining their suitability for specific manufacturing processes. For example, smaller particles are ideal for use in additive manufacturing, while larger particles may be better suited for powder metallurgy applications.
Size Range | Application |
---|---|
10–20 µm | Thin films, coatings, electronics, and microstructures |
20–45 µm | Additive manufacturing, laser powder bed fusion, fine powder metallurgy |
45–100 µm | Aerospace components, large-scale 3D printing, powder metallurgy |
Standards for Spherical Cobalt-Based Alloy Powder
Compliance with industry standards is critical, especially for applications in aerospace and medical devices. Here are some of the most common standards for cobalt-based alloys:
- ASTM F75: Standard Specification for Cobalt-Chrome Alloy Castings for Surgical Implants.
- ASTM F1537: Standard Specification for Wrought Cobalt-28-Chromium-6-Molybdenum Alloys for Surgical Implants.
- ASTM B212: Standard Test Method for Density of Metal Powders.
These standards ensure that the powders meet the mechanical, chemical, and biocompatibility requirements needed for critical use cases.
Pricing and Suppliers of Spherical Cobalt-Based Alloy Powder
While spherical cobalt-based alloy powders offer superior performance, they tend to be more expensive than traditional materials due to their complex production process and high demand in industries like aerospace and medical devices. However, the performance benefits often outweigh the costs in high-value applications.
Suppliers and Pricing of Spherical Cobalt-Based Alloy Powder
Supplier | Location | Available Grades | Price per Kg (Approx.) |
---|---|---|---|
American Elements | USA | Stellite, CoCrMo, Haynes 188 | $500 – $2,500 |
TLS Technik | Germany | High-purity cobalt-based powders for additive manufacturing | $600 – $3,000 |
Goodfellow | UK | Stellite 6, CoCrMo, Haynes 188 | $700 – $2,800 |
Advanced Refractory Metals | USA | CoCrMo, Stellite, Tribaloy | $550 – $2,700 |
Stanford Advanced Materials | USA | Stellite, CoCrMo | $600 – $3,200 |
Factors Affecting Pricing
Several factors can influence the price of spherical cobalt-based alloy powder:
- Purity: Higher purity powders are more expensive due to the increased cost of refining.
- Particle Size: Finer powders require more advanced production techniques, driving up costs.
- Alloy Composition: Alloys that contain tungsten, molybdenum, or other high-value elements cost more.
- Production Method: Methods like gas atomization or plasma spheroidization ensure high-quality powders but add to production costs.
- Order Size: Bulk purchases often come with discounts, reducing the cost per kilogram.
Advantages and Limitations of Spherical Cobalt-Based Alloy Powder
While cobalt-based alloys offer many benefits, it’s important to consider both the advantages and limitations before deciding if this material is right for your project.
Advantages and Limitations of Spherical Cobalt-Based Alloy Powder
Advantages | Limitations |
---|---|
High Strength and Wear Resistance: Ideal for high-stress environments | Cost: Cobalt-based alloys are generally more expensive than traditional materials |
Thermal Stability: Performs well in high-temperature environments | Production Complexity: Requires advanced manufacturing techniques |
Corrosion Resistance: Excellent in harsh environments | Limited Availability: High-quality cobalt powders may be harder to source |
Biocompatibility: Suitable for medical implants | Processing Difficulty: Requires specialized equipment for additive manufacturing |
Versatility: Suitable for a wide range of industries and applications | Research Stage: Some cobalt-based alloys are still being optimized for commercial use |
For instance, while spherical cobalt-based alloy powder is ideal for aerospace and medical implants due to its high strength and corrosion resistance, its higher cost makes it less suitable for cost-sensitive projects where cheaper materials like steel or aluminum could suffice.
Spherical Cobalt-Based Alloy Powder vs. Other Materials
When deciding whether to use spherical cobalt-based alloy powder, it’s essential to compare it to other common materials like titanium alloys, aluminum, and stainless steel. Here’s how it stacks up against these materials in terms of performance, cost, and applications.
Comparison of Spherical Cobalt-Based Alloy Powder with Other Materials
Material | Key Properties | Cost Comparison | Common Applications |
---|---|---|---|
Cobalt-Based Alloys | High strength, wear resistance, corrosion resistance | More expensive than most metals | Aerospace, medical implants, additive manufacturing |
Titanium Alloys | Lightweight, high strength, biocompatible | Similar or slightly cheaper than cobalt alloys | Aerospace, medical implants, automotive |
Aluminum | Lightweight, good corrosion resistance | Cheaper than cobalt alloys | Automotive, aerospace, construction |
Stainless Steel | High strength, good wear resistance | Much cheaper than cobalt alloys | Construction, tools, industrial machinery |
Compared to titanium alloys, cobalt-based alloys offer superior wear resistance and corrosion resistance, making them ideal for high-stress applications. However, titanium alloys may be preferred for lightweight and biocompatible applications. Aluminum and stainless steel are cheaper alternatives but lack the high-temperature stability and wear resistance that cobalt-based alloys provide.
Frequently Asked Questions (FAQ) About Spherical Cobalt-Based Alloy Powder
Common Questions About Spherical Cobalt-Based Alloy Powder
Question | Answer |
---|---|
What makes cobalt-based alloys different from other alloys? | Cobalt-based alloys offer superior wear resistance, corrosion resistance, and thermal stability, making them ideal for high-stress environments. |
Why are cobalt-based powders spherical? | The spherical shape improves flowability, packing density, and layer uniformity, which are essential for additive manufacturing. |
What industries use spherical cobalt-based alloy powder? | Common industries include aerospace, medical devices, energy, and additive manufacturing due to the material’s high strength and resistance to wear and corrosion. |
How does the price of cobalt-based powder compare to traditional materials? | Cobalt-based powders are generally more expensive than traditional materials like aluminum or stainless steel due to their complex production process and superior properties. |
Can spherical cobalt-based alloy powder be used for 3D printing? | Yes, spherical cobalt-based powders are often used in additive manufacturing applications, especially for laser powder bed fusion and direct energy deposition. |
How does cobalt-based powder compare to titanium alloys? | Cobalt-based powders offer better corrosion resistance and wear resistance but are generally heavier and more expensive than titanium alloys. |
Are cobalt-based alloys safe for medical implants? | Yes, CoCrMo alloys are widely used for medical implants due to their biocompatibility and corrosion resistance. |
What particle size is best for additive manufacturing? | Particle sizes between 20 µm and 45 µm are typically ideal for additive manufacturing applications. |
Conclusion: Is Spherical Cobalt-Based Alloy Powder Right for Your Project?
In conclusion, spherical cobalt-based alloy powder is a revolutionary material that offers high strength, wear resistance, corrosion resistance, and thermal stability—qualities that make it ideal for aerospace, medical, and energy applications. While the material comes at a higher cost compared to traditional metals, its performance advantages often justify the investment in high-tech industries.
If you’re looking to produce components that require exceptional mechanical properties, resistance to harsh environments, and the ability to maintain structural integrity at elevated temperatures, spherical cobalt-based alloy powder is likely the right choice for you. However, if your project is cost-sensitive and doesn’t require the advanced properties of cobalt-based alloys, more affordable materials like aluminum or stainless steel may be more suitable.
Ultimately, spherical cobalt-based alloy powders are helping to push the boundaries of what’s possible in advanced manufacturing, offering unmatched performance in critical applications. If you’re ready to take your engineering projects to the next level, it’s time to seriously consider incorporating this cutting-edge material into your processes.
Get Latest Price
About Met3DP
Product Category
HOT SALE
CONTACT US
Any questions? Send us message now! We’ll serve your request with a whole team after receiving your message.
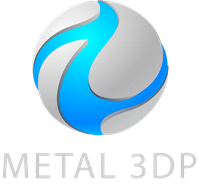
Metal Powders for 3D Printing and Additive Manufacturing