Vacuum Induction Melting
Table of Contents
Overview
Vacuum Induction Melting (VIM) is a sophisticated and highly precise process used to produce high-quality metal alloys and powders. This method is crucial for applications requiring exceptional purity and precise composition, making it essential in industries like aerospace, medical devices, and high-performance engineering. Let’s delve into the intricacies of VIM, exploring its processes, applications, advantages, disadvantages, and detailed information on various metal powder models produced through this technique.
What is Vacuum Induction Melting?
Vacuum Induction Melting involves melting metals in a vacuum environment using electromagnetic induction. This technique minimizes contamination from gases and impurities, ensuring the production of metals with superior purity and homogeneity. By melting metals under vacuum, VIM prevents oxidation and enables precise control over the composition of the final product.
Key Details of VIM:
- Process: Melting metals using electromagnetic induction in a vacuum.
- Purpose: Producing high-purity metal alloys and powders.
- Applications: Aerospace, medical devices, high-performance engineering.
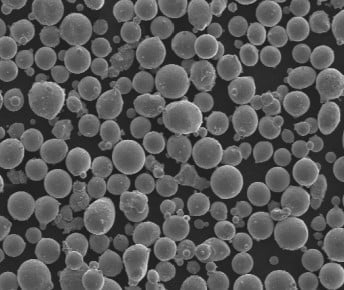
How Vacuum Induction Melting Works
Imagine a high-tech kitchen where you cook your favorite dish in a perfectly controlled environment, free from any unwanted odors or contaminants. That’s VIM in a nutshell, but for metals! The process begins with placing raw materials into a crucible within the vacuum chamber. An induction coil surrounds the crucible, generating a magnetic field when an electric current passes through it. This magnetic field induces eddy currents in the metal, causing it to heat up and eventually melt.
Once the metal reaches the desired temperature, alloying elements can be added to achieve the specific composition required. The vacuum environment ensures that no gases are trapped in the melt, resulting in a cleaner and more homogeneous alloy.
Types of Metals and Alloys Produced
VIM is versatile, capable of producing a wide range of metals and alloys. Here are some specific metal powder models:
- Nickel-Based Superalloys (e.g., INCONEL 718)
- Composition: Nickel, Chromium, Iron, and other elements.
- Properties: High strength, corrosion resistance, and excellent high-temperature performance.
- Applications: Turbine blades, aerospace components.
- Titanium Alloys (e.g., Ti-6Al-4V)
- Composition: Titanium, Aluminum, Vanadium.
- Properties: High strength-to-weight ratio, excellent corrosion resistance.
- Applications: Aerospace, medical implants.
- Cobalt-Chromium Alloys (e.g., CoCrMo)
- Composition: Cobalt, Chromium, Molybdenum.
- Properties: High wear resistance, biocompatibility.
- Applications: Medical implants, dental devices.
- Stainless Steels (e.g., 316L)
- Composition: Iron, Chromium, Nickel, Molybdenum.
- Properties: Corrosion resistance, mechanical strength.
- Applications: Surgical instruments, marine applications.
- Aluminum Alloys (e.g., AlSi10Mg)
- Composition: Aluminum, Silicon, Magnesium.
- Properties: Lightweight, good thermal properties.
- Applications: Automotive parts, aerospace components.
- Magnesium Alloys (e.g., AZ91D)
- Composition: Magnesium, Aluminum, Zinc.
- Properties: Lightweight, high strength.
- Applications: Automotive, electronics.
- Copper Alloys (e.g., CuCrZr)
- Composition: Copper, Chromium, Zirconium.
- Properties: High electrical conductivity, good mechanical properties.
- Applications: Electrical components, heat exchangers.
- Tool Steels (e.g., M2 High-Speed Steel)
- Composition: Iron, Tungsten, Molybdenum, Chromium.
- Properties: High hardness, wear resistance.
- Applications: Cutting tools, molds.
- Precious Metal Alloys (e.g., PtIr)
- Composition: Platinum, Iridium.
- Properties: High corrosion resistance, good mechanical properties.
- Applications: Jewelry, medical devices.
- High-Entropy Alloys (e.g., CoCrFeNiMn)
- Composition: Cobalt, Chromium, Iron, Nickel, Manganese.
- Properties: Excellent mechanical properties, high corrosion resistance.
- Applications: Advanced engineering applications.
Advantages of Vacuum Induction Melting
Why is VIM so highly regarded in the metallurgy world? Here are some key benefits:
- High Purity: The vacuum environment eliminates gas contamination, resulting in metals with exceptional purity.
- Precise Composition: Allows for exact control over alloying elements, producing materials with tailored properties.
- Improved Mechanical Properties: Metals produced through VIM exhibit superior mechanical characteristics.
- Homogeneity: Ensures uniform distribution of alloying elements throughout the metal.
- Versatility: Capable of melting a wide range of metals and alloys.
Disadvantages of Vacuum Induction Melting
Like any process, VIM has its drawbacks. Here are a few:
- Cost: The equipment and operational costs for VIM are relatively high.
- Complexity: The process requires sophisticated technology and expertise.
- Scale: Typically suitable for smaller batch sizes compared to other melting methods.
Applications of Vacuum Induction Melting
VIM is a game-changer in many industries. Let’s explore its key applications:
Aerospace:
- Components: Turbine blades, engine parts.
- Benefits: High-temperature performance, durability.
Medical Devices:
- Components: Implants, surgical instruments.
- Benefits: Biocompatibility, corrosion resistance.
High-Performance Engineering:
- Components: High-stress components, specialized tools.
- Benefits: Strength, wear resistance.
Types of Metals and Alloys Produced by VIM
Metal/Alloy | Composition | Properties | Applications |
---|---|---|---|
INCONEL 718 | Nickel, Chromium, Iron | High strength, corrosion resistance | Turbine blades, aerospace components |
Ti-6Al-4V | Titanium, Aluminum, Vanadium | High strength-to-weight ratio, corrosion resistance | Aerospace, medical implants |
CoCrMo | Cobalt, Chromium, Molybdenum | High wear resistance, biocompatibility | Medical implants, dental devices |
316L Stainless Steel | Iron, Chromium, Nickel, Molybdenum | Corrosion resistance, mechanical strength | Surgical instruments, marine applications |
AlSi10Mg | Aluminum, Silicon, Magnesium | Lightweight, good thermal properties | Automotive parts, aerospace components |
AZ91D | Magnesium, Aluminum, Zinc | Lightweight, high strength | Automotive, electronics |
CuCrZr | Copper, Chromium, Zirconium | High electrical conductivity, good mechanical properties | Electrical components, heat exchangers |
M2 High-Speed Steel | Iron, Tungsten, Molybdenum, Chromium | High hardness, wear resistance | Cutting tools, molds |
PtIr | Platinum, Iridium | High corrosion resistance, good mechanical properties | Jewelry, medical devices |
CoCrFeNiMn | Cobalt, Chromium, Iron, Nickel, Manganese | Excellent mechanical properties, high corrosion resistance | Advanced engineering applications |
Applications of VIM-Produced Metals
Industry | Components | Benefits |
---|---|---|
Aerospace | Turbine blades, engine parts | High-temperature performance, durability |
Medical Devices | Implants, surgical instruments | Biocompatibility, corrosion resistance |
High-Performance Engineering | High-stress components, specialized tools | Strength, wear resistance |
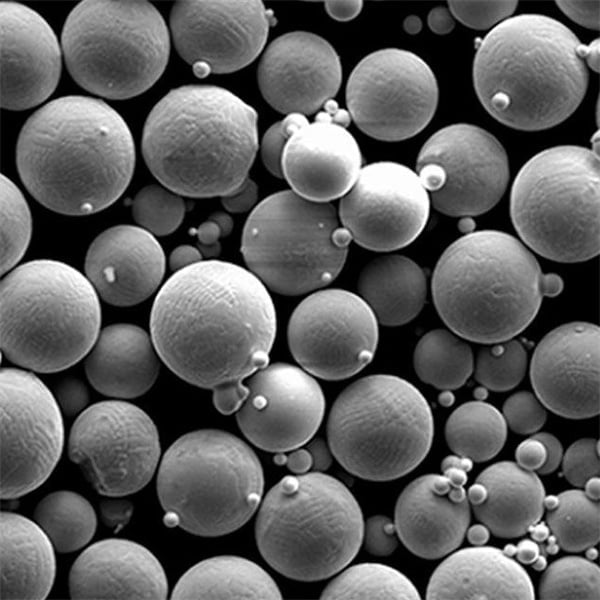
Specifications and Standards
Metal/Alloy | Standard | Grade | Specification |
---|---|---|---|
INCONEL 718 | ASTM B637 | Grade 1 | High strength at elevated temperatures |
Ti-6Al-4V | ASTM B348 | Grade 5 | High strength-to-weight ratio |
CoCrMo | ASTM F1537 | Grade 1 | High wear resistance |
316L Stainless Steel | ASTM A240 | Grade 316L | Corrosion resistance |
AlSi10Mg | ASTM B928 | Grade 1 | Lightweight, good thermal properties |
AZ91D | ASTM B93 | Grade AZ91D | Lightweight, high strength |
CuCrZr | ASTM B224 | Grade 1 | High electrical conductivity |
M2 High-Speed Steel | ASTM A600 | Grade M2 | High hardness, wear resistance |
PtIr | ASTM B563 | Grade 1 | High corrosion resistance |
CoCrFeNiMn | ASTM E2209 | Grade 1 | Excellent mechanical properties |
Pros and Cons of Vacuum Induction Melting
Advantages
Advantage | Description |
---|---|
High Purity | Eliminates gas contamination for superior purity. |
Precise Composition | Exact control over alloying elements for tailored properties. |
Improved Mechanical Properties | Superior mechanical characteristics in final products. |
Homogeneity | Uniform distribution of alloying elements. |
Versatility | Suitable for a wide range of metals and alloys. |
Disadvantages
Disadvantage | Description |
---|---|
Cost | High equipment and operational costs. |
Complexity | Requires sophisticated technology and expertise. |
Scale | Typically limited to smaller batch sizes compared to other methods. |
Suppliers and Pricing Details
Leading Suppliers of VIM Equipment
Supplier | Product Range | Pricing | Region |
---|---|---|---|
Inductotherm Group | VIM furnaces, accessories | $100,000 – $1,000,000 | Global |
ALD Vacuum Technologies | VIM systems, custom solutions | $150,000 – $2,000,000 | Global |
Seco/Warwick | VIM furnaces, after-sales services | $120,000 – $900,000 | North America, Europe |
Consarc | VIM and VAR furnaces | $200,000 – $1,500,000 | Global |
ECM Technologies | VIM systems | $100,000 – $850,000 | Europe, Asia |
Comparison of VIM vs. Other Melting Methods
Aspect | Vacuum Induction Melting (VIM) | Arc Melting | Electroslag Remelting (ESR) |
---|---|---|---|
Purity | High due to vacuum environment | Moderate | High |
Cost | High | Lower | High |
Complexity | High | Moderate | High |
Batch Size | Small to medium | Medium to large | Medium |
Application | High-performance alloys | General purpose | High-purity applications |
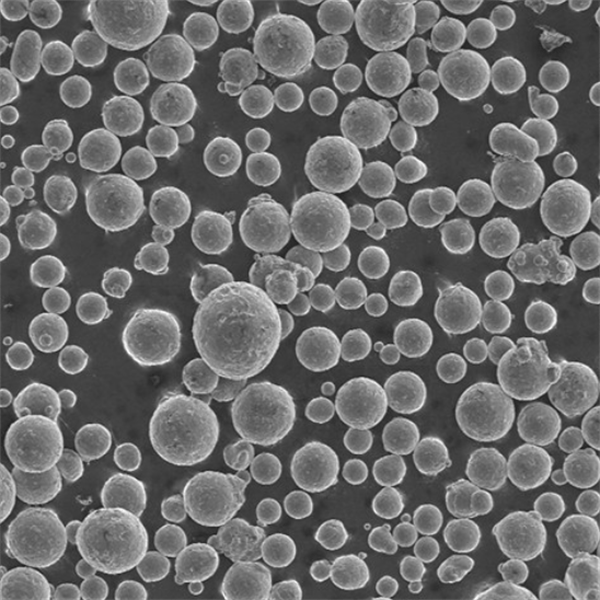
FAQs
Question | Answer |
---|---|
What is Vacuum Induction Melting (VIM)? | VIM is a process that melts metals using electromagnetic induction in a vacuum to produce high-purity alloys. |
Why use VIM over other melting methods? | VIM offers superior purity, precise composition control, and improved mechanical properties. |
What metals can be produced using VIM? | VIM can produce a wide range of metals, including nickel-based superalloys, titanium alloys, and more. |
What are the key applications of VIM? | Key applications include aerospace components, medical devices, and high-performance engineering parts. |
What are the disadvantages of VIM? | Disadvantages include high cost, complexity, and typically smaller batch sizes. |
Who are the leading suppliers of VIM equipment? | Leading suppliers include Inductotherm Group, ALD Vacuum Technologies, and Seco/Warwick. |
How does VIM compare to Arc Melting? | VIM provides higher purity but at a higher cost and complexity compared to Arc Melting. |
Conclusion
Vacuum Induction Melting is a pinnacle of modern metallurgy, providing unmatched purity and precision in metal production. Its applications span critical industries where performance and reliability are non-negotiable. While it comes with higher costs and complexity, the benefits often outweigh these challenges, making VIM an invaluable process in advanced material manufacturing.
Share On
MET3DP Technology Co., LTD is a leading provider of additive manufacturing solutions headquartered in Qingdao, China. Our company specializes in 3D printing equipment and high-performance metal powders for industrial applications.
Inquiry to get best price and customized Solution for your business!
Related Articles
About Met3DP
Recent Update
Our Product
CONTACT US
Any questions? Send us message now! We’ll serve your request with a whole team after receiving your message.
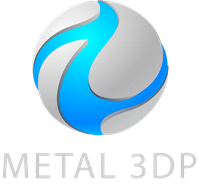
Metal Powders for 3D Printing and Additive Manufacturing